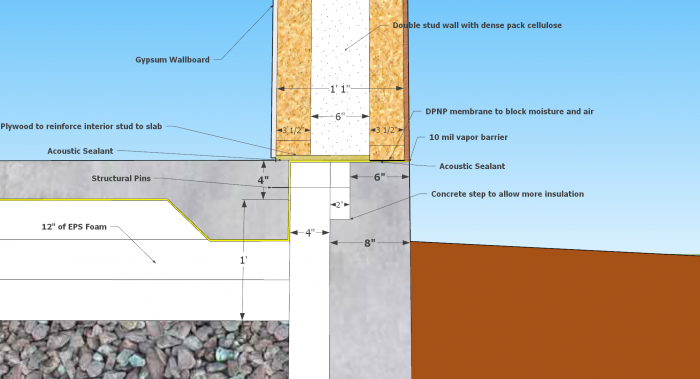
In New Hampshire, Chris Roche is pulling together plans for a new energy-efficient home. The slab-on-grade design calls for double-stud walls insulated with dense-packed cellulose, what Roche believes is the most economical and practical approach for getting the walls to R-40, or beyond.
Roche has paused at an important detail: the layer of rigid foam insulation that separates the concrete foundation wall on the outside from the slab on the inside.
Roche writes in a recent Q&A post that just about every foundation design for a slab that he’s seen either puts all of the rigid insulation on the outside of the foundation, or splits it half-and-half between inside and outside. In either case, Roche sees a problem.
The aim is to insulate the foundation wall with a total of 4 inches of expanded polystyrene (EPS) insulation. If the foam goes on the outside of the wall, it creates a difficult flashing detail, plus he’ll have to protect the outer surface of the foam from damage. If he puts 2 inches of foam on the outside and 2 inches on the inside, the concrete may stay to cold, and transmit that to the interior slab.
Roche saw a solution to this dilemma in a recent GBA article on double-stud walls by Dan Kolbert in which the entire perimeter of the slab was insulated with EPS to the interior.
“This would effectively create a cold foundation wall but warm interior slab,” Roche says. A potential weakness with this approach is that the interior stud wall would be partially resting on foam, so Kolbert had suggested placing plywood under the bottom plates to provide some additional support.
Roche has followed that up with a design detail of his own, shown in the illustration at the top of this article. A video…
Weekly Newsletter
Get building science and energy efficiency advice, plus special offers, in your inbox.
This article is only available to GBA Prime Members
Sign up for a free trial and get instant access to this article as well as GBA’s complete library of premium articles and construction details.
Start Free TrialAlready a member? Log in
13 Comments
Sometimes, more is easier when it comes to sub-slab insulation. When the excavator has prepped the area you can do some fine tuning. I recommend seeing what you can get for used rigid insulation. There are a few places in Mass that sell used insulation. Below slabs is an excellent place for this.
Great article. Re the bug issue. We have a lot of those down south, so I used borate infused EPS under the slab of my last house. In planning for my next build, I came across Glavel foam glass gravel. Has anyone tried this product? Combining gravel and insulation seems to simplify things, and I don't imagine the bugs will want to set up home in the stuff.
Seems like a great idea for the termite kingdom AKA the SE US.
For those of us who don't live in the frigid north, it is instructive to recognize that R40 walls and 6" of XPS slab insulation does not provide enough benefit for the investment. 1-2" of slab insulation around the perimeter (none needed under the entire slab if not using radiant heat) and R-25-30 exterior walls is all you need for a very comfortable, cost effective structure.
Good to know, Carl. I assume you are okay with placing the foam around the inside of the footer.
https://www.greenbuildingadvisor.com/article/movin-on-up
Looks like he is (See Gallery Photos)
"I installed Owens Corning 1-inch XPS board around the perimeter of the slab and below the slab, 24 inches wide around the perimeter. This should give me all the insulation I need in Climate Zone 3, where it rarely gets very cold.".
Carl, I assume you are referring to projects not built in the north? I can assure you that in heating-dominated climates we want more than 1-2" of insulation at the slab perimeter and we definitely want insulation in the floor. Walls are another matter--R-30 CAN make sense, but it depends on the heating system.
12" of foam seems way too much . What's the point? I can't imagine that 4" isn't adequate .
Illustrations 4-4 in the ORNL link are quite odd. They show a stem-wall reduced to about 3" at the top. I don't know how y0u would pour it, and the result would be very unstable.
Great Article. I just built a slab edge scenario like this. Worked like a charm. I considered doing a plywood connector, but I just used a 2x6 PT bottom plate for the interior wall and put the 2x4 wall to the inside face of it. I held the 2x6 off the exterior wall plate, and used ccSPF as a flash coat over the bottom plates and bottom of wall. Exterior door thresholds are also tricky with this detail.
I would also add that when working with thicker EPS - take extra care to make sure your compacted stone layer is dead flat. I had some areas that weren't as perfectly flat as they could have been, which magnified into EPS sheets not sitting dead flat.
Why not just skip the strip foundation and go with a thickened edge slab? This results in zero thermal bridging because you can insulate the entire outside and have far fewer complicated details in forming your foundations. Frost protection comes from horizontal wing insulation so you save having to dig and backfill. You also can do it with one concrete pour.
User ... 375,
I agree that the detail would benefit from being simpler, but I'm not sure a thickened slab is always a suitable solution. A few of reasons I can think of which might militate against using one:
- Many engineers are reluctant to allow foam under load-bearing elements like footings.
- You are back to the problem of providing and protecting thick exterior insulation at the perimeter.
- The depth of excavation is often not determined by the depth of frost penetration, but by the depth necessary to reach a good load-bearing substrate, and can be a lot deeper than that typically done for a slab 0n grade. Foundation walls help deal with that.
- Sloping sites can still be suitable for slabs, but not without perimeter walls.
Log in or become a member to post a comment.
Sign up Log in