Questioning my logic…GSHP, ASHP, radiant?

I’m in the planning/almost ready to break ground stage of a new home and I’m beginning to question my sanity when it comes to figuring out the right approach for heating & cooling.
The home is:
North end of Climate Zone 5
Main Floor: 1700 sq ft + 1000 sq ft garage, vaulted ceilings through much of it
2nd Floor: 1100 sq ft (2 bedrooms, 2 baths, living room) primarily over the garage
Basement: 1700 sq ft, partial walkout + 1000 sq ft shop under the garage (separated from the rest of the basement)
Walls: R30+ (2×6, 2″ XPS outside, 2lb SPF for sealing + 1/2lb SPF for cavity fill)
Roof: R50 (similar construction to walls. thermal envelope at roof. vent-over roof deck)
Windows: Double-pane, energy star rated
Garage is insulated to the same R30 walls, plus a deceptively-rated “insulated” garage door with typically mediocre air sealing.
Basement Walls: R10 for the time being. Will be finished eventually to R20-30. Really won’t be used much until it’s finished. Shop under garage will be insulated to R10-20.
Natural gas is a $30k proposition to have the main extended to my property, but electric is readily available
Garage and shop space under garage need to be heated, but only to 60 deg max
Main floor will have a Tulikivi soapstone fireplace for ambiance/backup heating (or primary heating on some days)
The master bedroom is on the main floor and we prefer to sleep in a cold room. As in our bedroom windows are open if the temp is over 20F outside. Typical morning bedroom temps are in the upper 50s in the winter. Yes, the master bedroom will be insulated from the rest of the house. Yes, this drives some sort of zoning. Radiant floor heat in the master bath is thus mandatory, hydronic or electric.
My previous thoughts:
Radiant floor heating on the main floor because of the comfort level it brings (warm under foot). We’ll have “Wood” flooring throughout the main floor. Carpet upstairs.
Seems natural to go with a Ground Source Heat Pump/Horizontal Loop Geothermal since I’m 100% electric, looking for efficiency, and there’s a rebate that could be appealing.
Hot water at least in part from the GSHP (almost free at that point, right?)
BUT….
Of course, after reading several threads, I’m second-guessing that.
Radiant drives 2 delivery systems, which drives $$
Geothermal, especially the one quote I have is OMG expensive
Radiant might not be THAT warm underfoot if the house is that well sealed.
As I said, I have one lone quote right now. He said he did a Manual J and came back with over 60k for the house, plus about 20k for the garage and 20k for the shop for heat, and almost 50k for cooling. 11 tons total in the equipment , split between 2 units, and a 12 ton loop. At roughly $1 per heating btu, there’s absolutely no way that’s happening.
So now I’m reading and wondering. Seems like my project is paralleling Kent’s project from a couple of years ago, except in comparison I’m thinking the Manual J numbers for mine are way past being in left field: https://www.greenbuildingadvisor.com/community/forum/mechanicals/33963/why-must-hvac-decisions-be-so-complex-or-geothermal-worth-it
Thoughts?
Ground Source? Air Source? Mini Split?
Mix of the 3?
Ditch the radiant entirely except for the bathrooms?
Could a mini-split unit heat & cool the garage and shop? (shop won’t need cooling being in the basement)
Thanks in advance for any advice!
Dave
GBA Detail Library
A collection of one thousand construction details organized by climate and house part
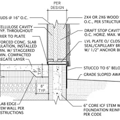
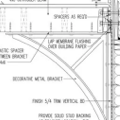
Replies
Dave,
In general, GBA usually recommends that residential designers focus on the thermal envelope. Once the heating and cooling loads are reduced by envelope improvements, you can design a very simple, relatively low-cost heating and cooling system.
I'm not a fan of hydronic systems with in-floor tubing. To learn why, read All About Radiant Floors.
I'm not a fan of ground-source heat pumps (mostly because they are, as you put it, "OMG expensive"). For more information, see Are Affordable Ground-Source Heat Pumps On the Horizon?
Once you've whittled down your heating and cooling loads by investing in a good envelope, you should be able to heat and cool your home with a simple forced-air system (using a furnace or an air-source heat pump), a few ductless minisplit units, or one or more ducted minisplits.
By the way, your basement wall insulation doesn't meet minimum code requirements. In you climate zone, you need at least R-15 wall insulation for your basement.
Your description of your roof insulation was vague. You should be aware that if you plan to install rigid foam above your roof sheathing, your rigid foam needs to have a minimum R-value of R-20. More information here: How to Build an Insulated Cathedral Ceiling.
My house is also on the northern edge of Zone 5 (Linden, MI). It has comparable insulation levels (a little less in the walls, a little better windows). It is a little smaller than yours but is not a particularly efficient shape. My manual J heat load came out about half of what your contractor is saying. The cooling loads were about a third. Even then, Dana D. said he thought they over-estimated and I believe him. It is still under construction so I don't have operational data yet.
Is the contractor willing to share a manual J report that shows what inputs they used? If so, check them. If not, I wouldn't believe them that they actually did one.
I made a spreadsheet to estimate heating loads using area x delta T x 1/R for conduction losses and formulas from Marc Rosenbaum for basement losses and infiltration/ventilation losses. It agreed within 10% with the manual J. It also helped me understand the relative contribution of various sources to indicate what areas to improve. Without that insight there is a tendency to spend too much in one areas such as making really good walls while you lose a lot of heat through the basement, the windows, or infiltration.
Thanks Martin.
The roof is being done with R20 over the sheathing as you mentioned.
Our building department is enforcing basements to R10/13 right now. i.e. 10 total in exterior/interior, or 13 if in a 2x cavity.
I've read the Radiant Floor article you mentioned. Hadn't previously thought of the comparatively small delta-t required, floor-to-air, in a well-sealed and insulated house. Hard to beat it on a tile bathroom floor on a cold morning though.
Reid,
We're neighbors! I've got a Fenton, MI mailing address, though we're not near the city. I'm off Center road (Tyrone Hills Golf Course exit).
What are you going with for windows, Reid? I've looked into triple-pane, but I'm not seeing a positive tradeoff between a very slightly improved U & SHGC for the additional $$.
The contractor I referenced above gave me the btu values from his Manual J, but not the specific details, though I didn't ask for them either. The heating load simply seems impossibly high.
I'm waiting on some more quotes right now. I'll ask them to quote non-hydronic as well.
I'll have to look into various methods for spreadsheet Manual J's. I have all of the walls and fenestrations jotted down in a spreadsheet somewhere. Should just need to number crunch a bit.
Dave,
It looks like we are within 10 miles of one another. My house is on Linden airport. I have a blog documenting the construction process at http://lindenairporthouse.blogspot.com. If you would like to see the place and talk in person, feel free to contact me by email at reid.a.baldwin at gmail.com.
Regarding the windows, I ordered triple pane Inline fiberglass windows. They were shipped from Canada. Due to the exchange rate, they were cheaper than purchasing double pane Andersen, Pella, or the like locally.
Dave, I'm in zone 6 (central NH), in a superinsulated house with two levels, the lower one set into a hill so that back wall is totally concrete foundation, front is totally framed. Total conditioned space (gross) is about 4,000 sqft. Framing is doubled (2x6 outer, 2x4 inner), with 12" cellulose in the cavity (R40). Windows are triple pane, attic floor is R60, foundation insulation is R20, under slab is R20.
My spreadsheet for heat loss showed 22 KBTU/hr, but actual is more like 19 at zero outside temp. Heat is by GSHP, two-ton, and it keeps the house warm in just first stage. Cooling load is less than one ton; the system loafs in the worst summer weather.
Even at just R30 walls, I'd say the heating load estimate you had done is high by a factor of two. Doing a realistic heat load calc for a high-performance house requires a lot of time using a lot of detailed information, something many contractors won't do in the limited time they can afford to spend on it. So they typically use unwarranted assumptions in picking things in the software's dropdown lists and "play it safe" to avoid undersizing equipment, usually grossly oversizing things. Three different calcs done for my house this way called for a five-ton GSHP, when ultimately the two-ton works fine in just first stage.
The economic justification of GSHP is indeed controversial, although I still feel it was correct for my situation. But as others have said, the first thing to do is to focus on building a really high-performance shell, and part of the modest extra cost will be offset by lower cost of a smaller, correctly sized HVAC system. As for windows, I'd advocate triple panes, partly to reduce heat load, but also for much improved comfort.
Dave - A heated floor IS nice on a cold winter morning. The problem is that your's will rarely turn on. When it does turn on, it won't be on long enough to really heat up the slab. A similar problem will arise with the Tulikivi. By the time it's warm enough to feel heat out of it, the house will be uncomfortable - you'll end up not using it most of the winter. A small, efficient wood stove would be used more, and cost a lot less. Tulikivis are good for really big houses that are not so well insulated/air sealed. They hold the heat for a long time, and are aesthetically pleasing, but….
Dick, many thanks for the comparison figures. The rep at the place I have a quote from boasted about building a model of the house in order to get an accurate estimate of the needs. For the life of me, I can't figure out how a workshop under my garage (30x36) with 1 wall open to outside, 2 walls against earth, and 1 wall against the basement would need almost 20k by itself, even when fudging low on the insulation and high on Temp delta. I guess I'll wait for the other companies to come back with quotes.
Kevinb, The Tulikivi is certainly going to come with a bit of a learning curve, Kevin. My wife is the "turn the knob a lot because I'm hot/cold right now" type, rather than the "nudge the setting just a little because it'll take some time to heat up" type :) That said, I think we'll get a lot of use out of it once we learn to plan ahead and make a fire hours before wanting it warm. Planning on a bench around it, which i suspect will get well-used. I totally understand the "but..." though.
I'm really second-guessing the heated floor though.
Dave,
Another reason to omit the Tulikivi: doing so would free up $14,000 to $20,000 for envelope improvements or a massive PV system. Just saying.
Kevin Z stated
" Dave - A heated floor IS nice on a cold winter morning. The problem is that your's will rarely turn on. When it does turn on, it won't be on long enough to really heat up the slab. A similar problem will arise with the Tulikivi. By the time it's warm enough to feel heat out of it, the house will be uncomfortable - you'll end up not using it most of the winter. A small, efficient wood stove would be used more, and cost a lot less. Tulikivis are good for really big houses that are not so well insulated/air sealed. They hold the heat for a long time, and are aesthetically pleasing, but…. "
Regarding the portion of your comment about radiant . This is factually incorrect . Radiant systems transfer heat only when the wavelengths contact surfaces in the room . Unless the slab or panel in this case is heated there will be less heat transfer , less heat transfer than required WILL NOT satisfy the thermostat and thus it will keep heating . Properly designed radiant systems require low water temps which vary based on required load at a given time . Only water offers the capacity to vary temp and flow in a way that allows optimum use of heat that has been stored .
The Tulikivi argument about it being uncomfortable is also without merit , maybe . If Dave was to use a Tulikivi W10 model heat would be moved away from the mass and could be stored in a tank to be used to produce hot water and heat . That same tank could have multiple heat exchangers to receive heat from multiple sources and feed a water to water heat pump and allow for a 2 digit system COP while the Tulikivi is on and until the heat has been degraded to the point that it is equal to ground loop temp .
This also allows through proper design the use of only the amount of stored heat throughout the largest portion of a heating season . The Tulikivi in this instance does not store heat in the mass at a like rate and therefore is not likely to make the home uncomfortable . This can be verified by looking at how the Hoover Dam was constructed . Concrete produces an extraordinary amount of heat , they wanted to get it done as fast as possible . The contractors embedded tubing throughout the pours and ran water through them to remove heat and allow faster cure .
Martin ,
Is an extra 14,000-20,000 dollars saved and put into the envelope really worthwhile ? A heating source that can be used during times of outage or emergency in my opinion has a much higher overall value than deeper insulation which at some point will have you uncomfortable . Take into account please that this Tulikivi also offers great benefit whether or not there is any level of emergency . Payback is greater . We should also ask Dave about his lot and whether PV is even something to be considered . I have performed several designs in Michigan and most of them have not been candidates for PV or Solar thermal due to lot limitations .
Dave ,
I have a suspicion that you are right about your contractor and his loads . I would certainly contact others , possibly not even in the area . These contractors or consultants / designers may not even be required to be area specific as long as they know how to design for a specific area and make best recommendations based on your wants and needs . GSHP is not always worthwhile , for instance , in your case . Not sure it ever pencils out . I would like to hear more about the lot exposure and such and am sure others would also . I will add that a water based system offers so many worthwhile benefits that it is worth exploring . There are now hydro based fan coils that do both heating and cooling that allow for individual room zoning so you are only using what you need when you need it . This can be set up also to put the return water through the tiled floors and provide floor warming also . While I have the utmost respect for the Pros here , sometimes the discussions evolve to one direction and one type of system using one type of fuel as source . My belief is that many different approaches are more likely to be a sustainable answer . I know a few contractors in your area that are capable of top notch installs , I do not know any consultants / designers however . Whatever you decide to do it will require much more detailed analysis than can be offered here . I would look at the RPA website or heatinghelp.com to locate someone who is capable of design and use the contractor location portions for installers . I can be reached to assist you through either of these sites . I have jobs in your area that are very successful , these projects were performed in cooperation with some of the best building science names in this country . Teamwork and cooperation are key to any success . You are on the right track with water , just don't fall for gimmicks and false claims .
Richard. It sounds like you are saying that Dave possibly can use a very complicated system to meet his heating and cooling needs. I take some of the posts to mean that Dave should consider building a tighter envelope so he can use a simpler approach to meet his heating and cooling needs. At the same time, I agree that more information about Dave's property and sunlight exposures would be helpful.
Richard,
Q. "Is an extra $14,000-$20,000 saved and put into the envelope really worthwhile?"
A. The answer depends on the thermal envelope under discussion and the investment plan. Of course some envelope investments are foolish. Other investments have a quick payback.
Q. "A heating source that can be used during times of outage or emergency in my opinion has a much higher overall value than deeper insulation which at some point will have you uncomfortable."
A. I agree that an emergency heater may make sense -- but a simple wood stove will provide emergency heat for a lot less than a Tulikivi.
And I have no idea why you think the "deep insulation ... at some point will have you uncomfortable."
Here's the site-plan: https://postimg.org/image/hbp4g43sx/ North is up.
It's in the middle of a 40+ acre farm and is wide open to the West and South
The house is positioned relative to the trees such that the morning sun in the summer is blocked, but the morning sun in the winder is allowed to shine on the back of the house.
I appreciate the input from everyone.
Steve , There is nothing complicated about what I suggest . Because the level of mechanical competence in this and other countries has declined should not mean that something simple is complicated . In fact , this type of system is less complicated than many envelope assemblies that are presently being installed . That does not mean they do not need to be that way for a good reason . What is complicated about heating water with a stove or any source , closing and opening switches and using circs or pumps . Nothin complicated .
I would also point out that mini splits would not be considered passive while ecm technology would meet the criteria .
I simply noted that while he can possibly have what he desires while also having it not cost too much ( only he can determine what that is ) and still be comfortable even without the availability of modern conveniences such as equipment . He can also eliminate the need for Environmentally friendly refrigerants within the envelope . What good is a healthy , well built house which then gets something possibly harmful introduced within it ?
The things I suggest have worked for thousands of years and use less energy than gimmicks and fads . I guess sea temps have nothing to do with GCC since water has no practical use in any of this communities regular suggestions . The sun is capable of generating electric but not making hot water that can be stored and extracting heat from cold air is more easily done than extracting heat from 80* + water . I get it , the hydronic industry that has worked on using nature to truly conserve energy should just disappear because some industries have convinced everyone that they have a better solution that relies heavily on dangerous things with a markedly higher GWP . Thermal comfort is not determined by T air my friends and electric is not that reliable .
Martin said ,
" 2.
Richard,
Q. "Is an extra $14,000-$20,000 saved and put into the envelope really worthwhile?"
A. The answer depends on the thermal envelope under discussion and the investment plan. Of course some envelope investments are foolish. Other investments have a quick payback.
Rebuttal . He already has a very good thermal envelope planned . I contend that firther upgrades would not lower the BTUh requirement to pay off quickly .
Q. "A heating source that can be used during times of outage or emergency in my opinion has a much higher overall value than deeper insulation which at some point will have you uncomfortable."
A. I agree that an emergency heater may make sense -- but a simple wood stove will provide emergency heat for a lot less than a Tulikivi.
Rebuttal . A simple woodstove would be a poorer choice than the Tulikivi since the Tulikivi has the abilities that it does . It can store heat which can be used to make hot water also . It can also use that stored heat to keep the pl;ace heated while Dave and the Mrs sleep instead of staying awake stoking a fire . Generators are a normal accompaniment nowadays and circs to accomplish basic heating from stored water use much less power than mini splits . Dave also wants a Tulikivi for his own reasons and I think it is an insult to his intelligence not to discuss ways for him to smartly use what he has researched , especially since it actually does make economic sense .
And I have no idea why you think the "deep insulation ... at some point will have you uncomfortable."
I ahve an idea that a home in an area that has a potential for very cold outdoor temps and storms that could potentially shut down services for an extended period without then appropriate amount of people within it tyo offset BTUh requirements could get uncomfortable after a few days without services. Dvae could however have a generator that uses almost no fuel and live like a human being for the duration or forever .
What type material will be used for the driveway Dave ?
It's a gravel drive with a TBD size concrete pad in front of both the house garage and outbuilding.
FWIW it looks like Greenstone makes a soapstone masonry heater with heat exchanger (http://www.greenstoneheat.com/water-jacket-heat-exchangers/). Dave, I can appreciate how aesthetics are an important part of the decision making process. So maybe Richard's approach would check more boxes.
Richard, how would radiant cooling work since Dave wants a solution he can use year round?
I don't believe I mentioned radiant cooling as opposed to a heating / cooling fan coil unit . Cooling degree days in Dave's area are extremely small though . Radiant cooling can certainly be done but I am of the opinion that in residences it more often than not is too costly on a square foot / benefit basis .
These will work very nicely , similar to Chiltrix units but using other than Chiltrix ODU . Water based cooling and heating , ability to vary flow and temp , optimizing conservation of stored heat and the ability to remove more heat using less energy . Not complicated at all . Water heater used for heating and domestic , basic chiller used for cooling . House of this size uses one tank to store heated or chilled water to load shift and hold out equipment while using what is stored . Manifolds or 2 pipe reverse return piping are both as simple as it gets .
http://www.htproducts.com/fan-coil.html
Then again he could have hydronic heating which is used 7 months a year and do something else for the few days he would need A/C , but why , when you can install one system that uses much less electricity and any refrigerant is outside the envelope .
Interesting units, Richard. Essentially a mini-split system with hydronic, eh?
As far as cooling goes, for the record, i complain when the first digit is >7. I like my air conditioning. :)
Thanks for the Greenstone link, Steve. I've already sent them an email. Tulikivi, as you know, also has a water jacket insert available. That's part of my thoughts with having such a fireplace and in-floor hydronic, is that I could transfer heat from the main room to the nether regions of the house (assuming they're hydronic as well).
I'm really not concerned about the tradeoff of having a Tulikivi vs spending that money on the envelope. This is a house I'm planning on living in for a long time, and I'm putting plenty $$ into the envelope to make it pretty darn good in comparison to most. Could it be better? Always. Is it a good balance of cost to performance? I think so. Even with a perfect envelope, I would still want the wood burner simply because there's no substitute for the ambiance and extra-warm radiant heat of something like that. Being able to build a fire in the morning and have it heating at the end of the day, or having it burn overnight and be warm in the morning (while using no electricity) is appealing. It's not always about the math, financial tradeoff, and payback.... sometimes it's about what the significant other wants, too ;)
A little more detail on my house, the main floor great room area is a single room with a high vaulted ceiling where the kitchen, dining, and great room areas are all combined. The fireplace will be more or less centrally located in this area. Master suite (insulated) off to one side, pantry, laundry, mudroom, etc... off the other side.
On the electrical service/outage side of things, it's anyone guess where I'm building. From my front porch, I cannot see another house except in the winter when I can see one. I do have a generator if the need arises, and it's enough to keep the lights on, well pumping, and hopefully the HVAC going as well.
It seems like the consensus is that the contractor who gave me the first estimate is off in the weeds with his Manual J estimates.
I'm really wondering if a mini-split is the way to go with my garage and underneath workshop. Heating only needs to be to 60 deg max, and not necessarily on the coldest day of the year. A/C really isn't needed in the basement, but in the garage it will be nice for comfort, and to remove the heat-load from the floor of the bedrooms above it. It's on the Northwest end of the house, so the sun-load won't be too terrible.
At that point, do I start looking at this house as multiple projects?
The garage is really another building that's attached to the house. The bedrooms over the garage are only attached to the house via a stairway.
Do I address those rooms on their own, rather than try to run ducting up there from a basement HVAC? ("ducting" being generic for whatever connection happens from the basement HVAC room to up there). I could well put a mini-split up there as well. I have attic space where a Mitsubishi ducted system could live. http://www.mitsubishicomfort.com/products/multi-room/product-listing/multi-position-ducted
The goal is, when (if?) the kids leave in a few years, we'll be able to all but close off that section of the house.
Hmmm.....
Some truly insane heat load numbers, especially for a better-than code house.
I doubt your ACTUAL heat load is high enough to warrant a Tulikivi with a hydronic insert. But the peak load may be above the low-temp capacity of a 2-ton Chilltrix, if that's the way you want to go. You might be able to pull that off with sufficient thermal buffering though. The risk with a reversible chiller (as with GSHP) is the competence of the system designer, and the amount of local support. Spending the Tulikivi money on the building envelope would likely bring the heating load within the capacity of a 2 ton Chilltrix though, and would provide a higher comfort level.
Regarding the building envelope plan, a couple of comments:
1: 2" XPS eventually ends up at the same R-value as 2" EPS of equal density as it loses it's blowing agents, and is substantially more expensive. The blowing agents also have a heavy environmental footprint. EPS uses relatively low-impact pentane for the blowing agent and has a stable performance over many decades.
2: A flash-inch of 2lb foam for air sealing buys you no better air tightness than a full cavity fill of half-pound foam. It also buys you nearly nothing in whole-wall R, and only impedes the drying capacity of the sheathing. Most 2lb foam also uses high impact blowing agents, and ~2x the polymer per R of half-pound foam.
1 + 2 = (usually)...
3: Spend the closed cell foam money on an other inch or two of exterior (EPS) foam, which will give you higher net performance and higher resilience for the money. Putting 3" of EPS on the exterior would run about $1.25 per square foot in my area, which is barely more than the cost of a flash-inch of 2lb foam inside the cavities. At 4" the exterior EPS would be maybe $1.75 per square foot, and still cheaper than a flash-inch of 2lb SPF + 2" XPS. And that's a virgin stock pricing. Using reclaimed foam (EPS or XPS) the installed cost should run less than half that.
With 4" of exterior EPS and half-pound cavity fill you'd have a whole-wall R (with all thermal bridging factored in) in the mid R30s, which is about what it takes to hit Net Zero Energy with a rooftop PV array that still fits on the house in your location using a reasonably implemented air source hydronic chiller (or well considered mini-split) approach. At 3" of exterior EPS you might still be able to pull that off if you design both the building envelope and chiller system extremely carefully. Pay attention to roof orientation and roof penetrations with an eye toward rooftop solar- you can really get there from here (for less than the $30K it takes to bring in natural gas) if you play your cards right.
Thanks Dana,
Over what period of time does XPS lose that much insulation value, and how does the eventual product differ in terms of R-value variance with temperature? I haven't been able to find anything that suggest EPS ever approaches the performance of XPS at low temperatures.
While a lift or two of 2lb SPF might not be any better than 1/2lb SPF for air infiltration, it's certainly better for vapour infiltration. I don't see how it impedes drying of the sheathing. If the sheathing can't dry towards the inside, that's a very good thing. I don't want it to. I want there to be a total seal in the wall for air and vapour. Drying of the sheathing thus happens to the outside, which is quite intentional. That's one of the reasons to put an air barrier between the outside of the wall and the inside of the siding.
I'm looking into a PV array, but with the way the house sits, the roofline isn't favourable for rooftop solar. The house is positioned as it is for other reasons, and that aspect isn't going to improve. With tons of acreage, a ground-array would be more possible and more efficient. I've requested quotes for systems, though I have no responses as of yet.
Dave,
Q. "Over what period of time does XPS lose that much insulation value, and how does the eventual product differ in terms of R-value variance with temperature?"
A. Start by reading this article: Thermal Drift of Polyiso and XPS.
"If the sheathing can't dry towards the inside, that's a very good thing. I don't want it to."
You sure DO want it to!
In your stackup the sheathing can't dry toward the exterior at reasonable pace through a couple inches of exterior foam- any bulk water that gets by the flashing soaks into the wood and takes a long time to leave through ~1-perm (or less) closed cell foam, a lot longer than through 3-5 perm standard latex paint and 10+ perms of open cell foam.
In a zone 5 location with better than R8 on the exterior you want MORE not less vapor diffusion capacity between the interior and the sheathing, which allows the sheathing to dry toward the interior at a reasonable rate. The exterior R ensures that the peak moisture content from wintertime moisture drives never reaches mold-inducing levels. The more exterior R there is, the warmer (=drier) the sheathing is. By giving the sheathing a drying path it gives the assembly MUCH more resilience against moisture from all sources.
So, again, spending the ccSPF money on even thicker exterior foam moves the sheathing to an even warmer-drier layer of the stackup for better resilience, and gives the assembly higher thermal performance to boot, a win on all fronts.
Even the name-brand XPS vendors' warranties assume an R-value to be more 90% of the labeled R at 50 years, but even 20 years is unduly optimistic. They get away with it since in most situations it's never sampled & re-tested, and they have all of the other legal weasel-wording exclusions & conditions in the warranty, eg:
http://msdssearch.dow.com/PublishedLiteratureDOWCOM/dh_05e8/0901b803805e898e.pdf?filepath=styrofoam/pdfs/noreg/179-04573.pdf&fromPage=GetDoc
Lots of luck trying to collect on that when your R10 foam re-tests at R9 at only 10 years (which it might). Are you really going to re-test in 10 years, or 20 years, or ever?
Fully depleted it's thermal performance is 84% or R8.4 @ 2", and I suspect that's pretty close to where almost all XPS will be performing at age 50, weasel-warranty-wording notwithstanding. The 50 year warranty (which is only guaranteeing R9 for 2") appears to be solely for marketing purposes, not a reflection of reality.
https://www.greenbuildingadvisor.com/articles/dept/musings/thermal-drift-polyiso-and-xps
https://www.greenbuildingadvisor.com/articles/dept/musings/comparing-properties-insulation-materials
[edited to add:]
Not to be outdone, Dow's competitor has now move their worthless warranty up to "lifetime limited warranty" at 90% of labeled R-value:
http://www.owenscorning.com/networkshare/eis/10015916-foamular-lifetime-limited-warranty.pdf
It's all BS. From a design robustness point of view, don't count on anything more than R8.4 @ 2" even though you probably will beat that for a decade or two.
Dave,
Dana is correct, of course, when he advises you that walls with exterior rigid foam are designed to dry to the interior. For more information on this type of wall, see these two articles:
Calculating the Minimum Thickness of Rigid Foam Sheathing
How to Design a Wall
Thanks for the links, which lead to reading, and more links, and more reading… Certainly a wealth of information to be had here, and I’m sure I’ve merely scratched the surface. :)
It seems that the notion of vapour permeability to the inside of the wall is more of a “just in case” bit of speculation, than hard science:
*Vapour permeability to the inside is good IF the sheathing gets wet
*An air barrier between the siding and WRB is good since it helps prevent the sheathing from getting wet
*Air leaks are bad in general
*Proper flashing is important since it helps prevent the sheathing from getting wet
*Foam outside the sheathing is good since it’s vapour impermeable and it helps prevent the sheathing from getting wet
*Etc…
The take-aways for me are:
1) The risk is sufficiently low, and the science lacking to the point where sealing the heck out of the wall inside the sheathing is a good thing
2) OSB is a generally poor material to use for construction
3) The proposed strategy is to make the wall construction inferior for the purpose of compensating for an inferior building material
Why degrade good wall construction because one of the elements is insufficient for the task at hand?
Dave,
You wrote, "The proposed strategy is to make the wall construction inferior for the purpose of compensating for an inferior building material."
I'm not sure what you mean. Installing vapor-permeable materials that allow the OSB or plywood sheathing to dry to the interior is not an "inferior" approach to construction. It is preferable to sandwiching wood fibers (OSB or plywood) between two vapor-impermeable layers.
Dave. Before you move on, please check out his article by Building Science Corporation's Joe Lstiburek (http://buildingscience.com/documents/digests/bsd-106-understanding-vapor-barriers). No one at Green Building Advisor is trying to give you bad advice, but it may be helpful for you to check out another source of information.
Planning for imperfection in flashing is not speculative. Actual field failures, not theoretical analyses, are what motivate people's concern about that. The strongest advocate for careful flashing I've met is a consultant who investigates field failures. You might think OK, you'll specify proper flashing and you'll be all set. But getting it implemented as designed is not easy. We had to have six newly installed windows removed and re-flashed after it was not just done wrong, but actively leaked. This week's project is to have the chimney flashing re-done because it wasn't done to spec, even though it was done by an "expert" recommended by an excellent experienced carpenter. It too leaked. Inspection revealed not only the active leak but half a dozen other things that were done wrong. And across the street, the house that got a new roof last year has tarps up around the chimney because of the same problem.
Does not matter what industry we are talking about , there are lots of experts and few that actually are . The guys that examine failures and address and correct them are usually the right guys . The phenomenon is however that these are the very same guys who did not get the job because they were not economical enough when it came to first cost .
An accurate twist to an old cliche would be , " You didn't get what you didn't pay for and it will never be what you thought you were getting ." Unfortunate reality .
For more information on flashing failures, see All About Wall Rot.
1: AIR sealing the heck out of the interior is a good thing, but when the sheathing is sufficiently warm, VAPOR sealing increases risk rather than reducing it.
2: CDX or plank sheathing will grow mold and rot under the same conditions as OSB, but may take longer to become a structural problem. Asphalted fiberboard can take it though, as long as the damp fiberboard isn't subjected to regular freeze/thaw conditions above some moisture content level.
3: The strategy had nothing to do with inferior materials, (unless you are defining all wood products are inferior materials for use as sheathing.) By putting any foam on the exterior you are limiting the ability of the wood to dry toward the exterior, but if you put enough exterior-R (as a fraction of the total) the wood stays warm enough that it won't take on enough moisture from interior moisture drives to grow mold. This is an extremely moisture safe way to build, and it's well within your budget.
Martin,
Would wall construction not be better if OSB were replaced with a sheathing material that was both air and water impermeable and rot-proof? If that were the case, your recommendation would be to make the insulation as air and vapour impermeable as possible to seal the cavity, so that anything that could get past joints in the sheathing can't make it inside, correct? Without wood sheathing, sheathing wouldn't rot.
If that's the case, the physical properties of OSB are making you build a wall that is inferior to one that had something better in its place. Plus, a rot-proof sheathing would be more tolerant of mistakes in other areas.
Thus OSB is a compromise of convenient/cost effectiveness vs robustness. We essentially use wood in home construction for properties other than its ability to sit outside and resist the weather.
Dana, yes, that means I'm categorizing all wood sheathing as inferior. If I'm making a decision not because it's desirable in and of itself, but because I'm trying to prevent an undesirable situation that results from a non-critical property of the materials being used, that material isn't as good as it could be.
Certainly rot proof sheathing would be an improvement for any wall. But for many climates and wall constructions, the ideal sheathing material would be highly permeable. In a simple wall, 2x6 studs with fiberglass insulation, in cold weather, moisture would accumulate against the inside surface of the sheathing if it was impermeable. You might think that wouldn't matter if it was rot proof, but it could still get the studs wet, get the insulation wet, drip down and get the bottom plate wet, etc.
A rot-proof highly permeable sheathing material is gypsum board with fiberglass facers, such as the "Densglass" brand.
If you want a fully rot-proof wall, you might consider ICF (insulated concrete forms).
Dave,
Charlie is right: if you want a wall that is invulnerable to moisture, build an ICF wall.
You are choosing to build with 2x6 studs, made of wood. These studs are not invulnerable to moisture, so you need to design a wall that can dry out if it ever gets wet.
There is nothing wrong with a wall that is able to dry to the interior. It's not an inferior method of construction. It's durable and resilient -- and potentially airtight, if you pay attention to air sealing.
I certainly agree that OSB is not a perfect sheathing material. If you don't like OSB, there are other sheathing choices worth considering. Here is a link to an article you may wish to read: Wall Sheathing Options.
Dave,
I find it hard to understand why green builders have such strong opinions on vapor permeance.
Most people in the U.S. don't have a good instinct for vapor permeance. We all understand air leakage -- an insect screen leaks more air than a fixed glass window -- but when it comes to vapor permeance, most people don't have a clue. Which material is more vapor-permeable, plywood or drywall? The average American would say, "I dunno."
When green builders express strong opinions on vapor permeance, they are usually on the opposite side of the fence from you, Dave. They usually write, "My wall has to breathe." (I'm thinking, "Really? Why?")
You're unusual. You write, "Do I want a permeable wall? Heck no."
Why the strong opinion? If your wall is airtight, who cares what the vapor permeance of the layers is? It's not as if you're going to be able to tell what the vapor permeance of these layers is when you are sitting in your armchair reading a newspaper.
The reason that some layers of a wall assembly need to be vapor-permeable is to protect the materials that you use to build your house from rot. That's a good thing. It makes your house last a long time. It makes the assembly less risky.
If you decide on your own that you don't like conventional advice on vapor permeance, and choose a wall that may trap water, that's a risky choice. But hey -- it's your house.
Dave,
Q. "With XPS as an exterior vapour barrier, and closed-cell on the inside to permit vapour to travel inward, why is the situation different for a roof?"
A. I don't recommend that builders assemble a wall with exterior XPS and closed-cell spray foam between the studs -- unless they are building a wall without any OSB or plywood sheathing. (That's possible, by the way, as long as you have a wall-bracing plan.) You don't want to sandwich the wood fibers of the wall sheathing between two vapor-impermeable layers. For more on this issue, see How to Design a Wall.
Q. "Is a roof not merely a wall on an angle?"
A. Actually -- no, it's not. For more on this issue, see A Researcher Looks at Insulated Roof Assemblies.
Dave,
Q. "What should I do with the roof which I'm planning on building similarly, except with 4 inches of exterior foam instead of 2? Is open-cell good or bad in this case when the sheathing has a fully-adhered membrane applied to put the water-resistive barrier at the sheathing and thus under the foam?"
A. If you are planning to install rigid foam above the roof sheathing (in your climate zone, you'll need rigid foam with a minimum R-value of R-20 if you go this route), and if you are also planning to install spray foam on the interior side of the roof sheathing, then open-cell spray foam is definitely preferable to closed-cell spray foam (because open-cell spray foam is vapor-permeable, allowing the roof sheathing to dry inward).
Other types of insulation would also work well under the roof sheathing for this type of roof: cellulose, mineral wool, or dense fiberglass batts.
Dave, I think you might have a typo in comment 36: "With XPS as an exterior vapour barrier, and closed cell on the inside to permit vapour to travel inward." Closed cell doesn't permit that; open cell does.
Is there anything you haven't written an article about, Martin? :)
Don't get me wrong, I appreciate the advice and have been continuing with research and reading article after article. But we absolutely make compromises in construction to compensate for materials that are less than ideal. I mean, we build houses out of fuel fercrissakes and they burn down. Wood is cheap, convenient, renewable, has adequate material strength, and all that good stuff, but if it wasn't for cost (and tradition I suppose) we wouldn't be building houses out of it. Do I want a permeable wall? Heck no. Does it seem appropriate in this case? Quite possibly, though the risk still seems quite low if other things are done correctly.
btw, I currently live in an ICF house. Built it 15 years ago when the local building department pretty much had no clue what the heck I was doing. Used PEX too, all of which confused both the electrical and plumbing inspectors. The electrical inspector even left a confused note on putting a ground wire on the supply line. Ummm... ok chief...but I'm not sure that'll work.
Having lived in an ICF house, I'll say one thing. It's a pain. For the normal homeowner, probably not. For the homeowner who does stuff and remodels, it's a pain. Partly because mine is waffle-blocks. Want to attach a 1/2 wall to the concrete for the shower in the basement? No way it'll land on the flat, making it a major pain to bolt a 2x to the wall. You need to taper the 2x to the curve in the wall. Ugh. Also decided to put a pellet stove in the basement. Cutting a hole in the rebared wall was fun. Plus plastic studs that are generally adequate until you want to hang shelves in the garage. etc... Glad I did it once. Won't do it again.
Back to the wall construction...
I understand, though struggle with the imperfection of "if/when it gets wet" scenario, since water should be managed away from the OSB such that the sheathing simply doesn't get wet (make it perfect, right?)
With XPS as an exterior vapour barrier, and open cell on the inside to permit vapour to travel inward, why is the situation different for a roof? Open Cell Spray Foam and Damp Roof Sheathing Is a roof not merely a wall on an angle?
If I bump up the thickness of my exterior wall foam to gain a little more R-value, and go with an open-cell foam, what then should I do with the roof which I'm planning on building similarly, except with 4" of exterior foam instead of 2. Is open cell good or bad in this case when the sheathing has a fully-adhered membrane applied to put the water resistive barrier at the sheathing and thus under the foam?
Thanks Charlie. Indeed a typo. Fixed it.
And this is where things conflict and get confusing, Martin.
The Perfect Wall
"A Wall is a Roof is a Slab—The physics of walls, roofs and slabs are conceptually the same."
I'm planning on a vent-over roof, similar in construction to what Joseph Lstiburek presents in his BSC "BSI-068: Rocks Don't Burn" article. Separating the shingle-layer from the insulated roof sandwich minimises the conduction part of the heat transfer equation, which is a good thing in general. Essentially, this ends up being a site-built SIP.
If I go with open cell under that, the only concern I have is really fire-resistance, and perhaps making the inspector happy with a vapour barrier, which the painted drywall should technically still do, even though it's separated from the roof (in some places) by the conditioned attic.
http://homeenergypros.lbl.gov/video/building-science-insights-to-vent-or-not-to-vent?xg_source=msg_mes_network
Doubling back to where I started, I have another quote and another Manual-J figure for the house. Still not sure that I trust all of the numbers, but it's better than the other figures by a bit.
Main floor of the house: 1700 sq ft 28000 btu
Upper floor (bedrooms over garage, not a full story, just dormers into the roofline: 1100 sq ft 16000 btu
Partial Walkout/Daylight Basement: 1700 sq ft 19000 btu
Garage: 1100 sq ft 13000 btu
Shop under garage: 1100 sq ft 17000 btu (walkout one end, connects to basement on one side)
I rounded off, so the numbers might not add up, but the conditioned total (minus garage and shop beneath it) is about 68,000 btu heating load. Still close to 100k when those two are factored in.
I think the over-garage living area is high, since he figured R30 for all of the wall, when it's closer to R50 for everything covered by roof.
I'm struggling a bit with the loss from the space under the garage being almost as much as the rest of the basement.
I think the garage and shop below are crying for a mini-split. The basement shop will need minimal heat & minimal conditioning for what I need that space to do (wood shop). The garage won't be heated to 70F either. The mini-split seems like an efficient way to handle those areas without worrying about ducting.
Dave ,
Are these heat load calcs being performed by compensated professionals with a building science background or are they being done by local wholesalers for contractors or the contractors themselves ? I designed a system in cooperation with a gentleman from Az who is well known that is in Linden (Ann Arbor) which is 3,800+ sq ft , 400+ of that being heated garage that only has a load of 31,000 at design . ACH would probably be similar whereas R ratings for assemblies are far short of your projected values .
I have to say that with a load such as this and such a concern about delivering what you need when you need it cries out not for mini splits but in fact screams out for mass storage and a water based system . When you have the ability to vary water temp , vary flow there is basically nowhere high or low that you cannot go . You will also cut first cost , guarantee all equipment never short cycles allowing for longer life . You really should contact me or someone like me .
Richard,
These are figures from the contractor that is providing an estimate for the installed. I've been wondering if I really need to seek out an independent contractor for the purpose of doing the Manual-J properly.
Dave, I highly recommend getting an independent load calculation done. Your savings on the installation could pay for the service many times over, plus you'll get better comfort and efficiency.
Contractors that can perform a good load calc are more rare than one that can do a proper install . My usual reviews show that most contractors install too many loops based upon manufacture recs(more material) as opposed to the overall better design of giving your system more efficiency by looking at what circ will cover max demand but not drop below the low end operating curve and overpumping for 50% or more of the season . When you don't know anything except what you've been shown by reps and salesmen you don't know what you don't know . When those performing your calcs have no idea about wall assemblies and air changes and how they actually perform you end up with systems that will heat your home but underperform for a great portion of the year and have less than best life cycles . They also cost more that way .
Thanks guys. Now how does one find a reputable, qualified service?
Ask Martin . I am positive he knows a few folks . Just in case , that was not sarcasm Martin . I might be inclined to contact Optimal Building Services , if the gentleman that is the principle is not interested maybe he could steer you .
Richard,
Most home energy raters who have been certified by RESNET or BPI can probably perform an accurate heat loss and cooling load calculation. Readers can visit the RESNET and BPI web sites and search for certified energy rates in their geographical area.
Richard, I appreciate your many contributions to conversations on GBA. But I will balance your advice to Dave -- namely, that Dave's situation "screams out for mass storage and a water based system" -- by noting that you give exactly the same advice to every GBA reader with a problem. (In other words, Dave, Richard believes strongly in hydronic systems.)
I can safelt state that certified Resnet and BPI raters as a group suffer from the same anomalies that every other trade do Martin . Probably why so many jobs still go awry . I still operate in the field and see it first hand . Most of them are terrioble and only know enough to game the numbers for program approval .
Dave ,
Martin is correct that I advocate hydronic systems . The reason I do this is not a personal preference as much as due to the fact that water is far and away the very best heat transfer medium available . Water heaters , heat pumps , electric equipment all can heat water . Water is not an environmental concern and never will be , boilers need not be used .
Martin ,
I would remind you that Dave asked specifically about a hydronic system . I would also point out that you seemingly point always advocate using a small Asian box high on the wall that after being monitored by NREL , ORNL seem to not perform as folks would believe . I guess I am saying that we are much alike in our advisory capacity . I do however question your loyalty since it really cannot do as good a job as water based systems .
Water can continue to condition any home while using only the circ is on , not the equipment . Water can completely fill an evaporator or heat exchanger while refrigerant cannot since some is fluid and some changes to vapor / gas . I did not choose water as a perfect transportation device for heat , the planet did that . You and your ilk may continue to believe you can do better than or fool Mother Nature , me I'll keep listening and being in tune with her and giving the advice that some ask for .
Dave probably did not need you to tell him I like water .
Richard,
I accept your first point -- that some certified energy raters aren't very good at performing heating load and cooling load calculations. This is a real problem in the HVAC industry, as we've pointed out on GBA many times. (See, for example, Saving Energy With Manual J and Manual D.)
I think that a certified energy rater may be more likely to perform an accurate load calculation than an HVAC contractor aiming to make a sale -- but I may be wrong.
Concerning the issue of forced-air systems vs. hydronic systems: It's always good to have more than one voice on a web forum. Most North Americans end up installing air-based systems because of the need for air conditioning, but hydronic systems still have loyal advocates like you. It's good that you keep making your suggestions here -- hydronic systems have their applications. I'll continue to provide balance, though.
I am happy to have people that are biased toward different types of systems participating in this forum. The exchanges among these people are thoughtful, rational, and respectful. The tone of the debates allow a reader like me that came to the site never having heard of mini-splits and having limited knowledge (and a few misconceptions) about other options to become educated. Thank you.
I wish I could find a site where people with differing political preferences had respectful debates.
The balance is certainly good when someone seeking advice is looking for that .
The idea that people install air based systems because they need A/C is now factually antiquated , I would point out that it always was . Many folks pushed real hard for solutions to this imbalance . The industry has finally responded with solutions for the residential market . The excuse that hydronic systems cannot provide A/C also at a cost that makes sense from a performance and life cycle cost is no longer valid .
I only respond when someone asks for assistance in mt area of knowledge . I do understand many of your points Martin but again must point out that many of your conclusions about water based systems are flawed . Many of them are based on failed systems designed by those who may not understand that some types of systems are better performing than others and in their attempts to intelligent and frugal just plain screwed them up and did not get good results . I think , presuming you want to know the truth you would also be interested . Take into account that many of the labs and research centers that perform testing of products are given certain parameters for those tests to come to a pre determined conclusion . That may be why most of their facilities have water based systems in them when they in fact consider what works best and operating costs .
Some examples are as follows :
Solar thermal ; drainback systems are best and can be done without glycol . They last quite a long time , easily 25 years without compromise . Heat can be stored and used later without running equipment save for a couple ecm circs . By spending a few extra dollars and including a proper amount of panels the end user can use stored water to deliver 70* + water to a WSHP and get system COPs well over 10 .
Pressurized systems , in my opinion , going forward are not the best bet and should be avoided .
GSHP systems cost much more to install , use much more energy and COPs are hard to achieve without the tightest guidelines , best designers , best installers , best commissioning . In my opinion they are best left to A/C dominant areas .
In cold climates , thermal battery systems are a great way to use multiple heat sources and KNOW your COP to within a gnats butt .
Air source stuff in general must use more energy since one needs to move more air through the equipment because it is a terrible heat transfer medium . 1 cu ft of water can hold roughly 3500 xs the heat as 1 cu ft of air . Not my rules , I just play the game and follow the rules .
I don't think it can be argued that a water heater can deliver all the heat needed in most well built modern homes , you need one anyway . It also makes sense that a similar ODU used with a minisplit can remove heat from water that has removed latent and sensible heat from a home without short cycling and not requiring all sort of control in an attempt to avoid this . It also offers the luxury of only changing the ODU when refrigerants become unavailable or illegal because the indoor units are not compatible .
I would also mention that given the proper design consideration all can be achieved using solar PV technology , it'll be good as long as the sun is out .
These systems are not as crazy as everyone thinks and the offer much more value when the goals are taken into consideration , those goals are shared by both sides of the industry . One side however is truly greener in mind . I would rather see more educated , qualified designers and installers than less . The outcome will not be good .
We have the same goals at the end of the day . Education is key unless we are willing to accept a society that resembles the cult classic , Idiocracy . Although frustrating at times Martin , I do enjoy our debates and differences and am glad you continue to provide a forum for them . Many people learn alot from them I am sure .
Richard,
I'll agree that hydronic is a very nice way to go. However, I'm also learning that it's a ridiculously expensive way to go when coupled to a GSHP, nearly doubling the cost of installing a forced-air GSHP system.
If I understand correctly, you're advocating for a hydronic system where the water is heated through either solar or PV, not through a GSHP, is that correct?
GSHP is the most costly and has the lowest cost to benefit ratio , that is correct . I am also saying there are several other ways to spend less up front than GSHP , get much better performance using less energy and less equipment .
If GSHP is something you were seriously considering I suggest a thermal battery instead . I am also stating that you can build the home without ducts save for DOAS which should be a separate operation anyway . Heat removed from the house during A/C operation can be used to pre heat DHW before a water heater thus using less energy . A water heater can be used to heat the home using a priority operation , a water heater that heats the house has no stand by losses or at a minimum they are greatly lessened . This can all be done when designed properly and outperform MOST systems .
Although many say solar thermal is a losing proposition I say they are wrong or mistaken . For those who look at GSHP systems I say that solar thermal is far less expensive by far and will outperform GS in a heating dominate climate zone by 2 xs . These types of systems can also be adapted easily later on to include other sources to combat any number of problems one may want to deal with .
"With XPS as an exterior vapour barrier, and open cell on the inside to permit vapour to travel inward, why is the situation different for a roof? Open Cell Spray Foam and Damp Roof Sheathing Is a roof not merely a wall on an angle?"
I cringe whenever I read that common misconception. A few differences between roofs & walls:
*The cladding of roofs are of-necessity extremely water proof and (with few exceptions) fairly vapor-impermeable. There is no such requirement for walls, which are usually semi-permeable or at least somewhat permeable (even 2" of XPS is somewhat permeable to water vapor.)
*This is because roofs (particularly in a zone 5 climate) can dwell for days/weeks/ months in direct contact with liquid water / snow / ice, conditions that walls do not withstand. There is no such thing as a roof deck drying outward into snow or water, but wall claddings do not experience persistent surface wetness.
*The average winter (and summer) temperature of roofs are quite different from those of walls, due to the average incident radiant temperatures. Walls face the landscape, which has an average radiant temperature comparable to the ambient air temperature. Roofs face the sky. In winter the average roof temperature of roof are WELL below those of walls. Nighttime radiational cooling out to a clear sky brings roof temperatures to below the ambient air temperature, often reaching the dew point of the outdoor air. The daytime direct solar radiation in winter brings the sun exposed walls & roofs to above the ambient, but not the shaded walls or north facing pitches of the roof. The average wintertime differences are large enough that the ratio of exterior R needed to protect from interior moisture drives in is larger for an unvented roof than for walls. In zone 5 locations that's about 40% for the roof, compared to only 25-30% for walls.
The ~15-16 BTU/hr per square foot of conditioned space ratios from the Manual-J mentioned in response #44 are still pretty high- likely due to high air infiltration/ventilation assumptions (?), combined with unrealisticly low 99% outside design temperatures (https://www.extension.org/sites/default/files/7.%20Outdoor_Design_Conditions_508.pdf ), but not so insanely high as to be completely useless. If you sized the heating system EXACTLY to those numbers it'll likely still be considerably oversized for the true loads, but probably not more than 2x oversized. (As a point of reference: My sub-code but reasonably tight ~2400' 2x4 framed house comes in at about 15-16 BTU/hr per square foot at an interior to outdoor temperature difference of 35C, but l~12-13 BTU/ft if I count the ~1600' of mostly-below grade insulated basement. This has been verified by fuel use against heating degree-day data, as well as an aggressive-assumption Manual-J. ) The shape of the house makes a difference, as does the total amount of glazed area, (and window performance) etc, but at your U-factors I'd expect the ratio to work out to something in the range of 9-10 BTU/hr at a delta-T of 40C. (+20C, indoors, -20C outdoors), assuming your 99th percentile temperature bin is that cold (about as cold as it gets for a 99% bin in zone 5.)
That "coldest day ever" in the heating load concept does have me somewhat concerned as far as practicality goes. It seems like a "just in case" measure in a sense. Plus I'm putting in a soapstone fireplace. It'll add quite a bit of heat to the house on that coldest-ever day. Plus, that coldest-ever is also at night where there is no sun load whatsoever, AND the time when the indoor temperature doesn't need to be 20C. I think the heating calcs really should include a "total-available heat" consideration.
I follow you on the wall vs roof distinction, but everything you want a roof to do, you also want a wall to do. Structure, insulation, and air/water resistance. A good roof would certainly make a good wall as well, no? Sure, they have different heat-loss figures due to their orientation, but that's why code calls for more R in a ceiling/roof. Perhaps a decent wall would be insufficient as a roof, and a roof would merely be overkill in a wall.
Now, if I follow you correctly, you're suggesting that because a roof is extra-protected against moisture from the outside, it's different from a wall. Can I extend that to also mean that closed-cell foam is appropriate on the underside of roof sheathing that is entirely covered with a fully-adhered membrane (with R20 foam on top of that)?
As I go around and around on this stuff in my mind, I'm wondering now if, on the walls, the 1/2 OSB sheathing is simply an unnecessary expense. I'm not in a seismic zone, and don't have ridiculous wind loads. I could remove the OSB, add an additional 1/2" of rigid foam without affecting my wall cross section, use steel-straping for shear strength, wrap it in Tyvek, and then flash & batt the wall cavities with closed cell & cellulose. The studs, if wetted, could still dry to the inside. R-value goes up, the closed cell adds a minor amount of wall rigidity, I've got the cementious siding as a projectile barrier, but let's face it, if a tornado is throwing stuff through the side of my house when I live in the middle of a farm, I probably have bigger problems. Plus I'll be sheltered in the basement vault (or on the front porch streaming to youtube).
Dave,
Yes, it's certainly possible to omit the OSB or plywood, and simply sheathe the outside of your studs with rigid foam -- as long as you have a good wall bracing plan.
For more information, see Four Options for Shear Bracing Foam-Sheathed Walls.
The differences between roofs & walls have nothing to do with how "...a roof is extra-protected against moisture from the outside..." . Perhaps I need to reprhase it more simply
A roof is in direct contact with liquid water for days or weeks on end, whereas direct wetting of walls is extremely abreviated both in time and saturation. (A driving hurricane rain is typically only a few hours at a time, whereas a foot of snow on the roof can take weeks to go away). Thus, wall assemblies can be expected to dry toward the exterior, and roofs can never be expected to dry toward unless the roof deck is vented to the outdoors from below, or the roof is on a house in the Atacama, where it rains maybe once every 20 years or so.
A roof runs significantly colder temperatures than walls in winter. If treated like a wall those colder temperatures lead to higher moisture content related to interior moisture drives unless the roof deck vented, interrupting the interior moisture drive with a layer of drier outdoor air. The wall (rainscreen-vented or not) benefits from both less direct wetting & the ability to dry toward the exterior AND from higher average wintertime temperatures.
Code requirements for higher R in roofs than walls have next to nothing to do with "...they have different heat-loss figures due to their orientation, but that's why code calls for more R in a ceiling/roof..."
It's more about the cost/benefit ratio. R50 of open blown goods in a vented attic is dirt cheap compared to an R50 wall so doubling the R value has comparatively low cost compared to doubling a wall assembly. But the favorable cost/benefit ratio goes to hell when going with a high-R unvented roof assembly, which is far more expensive to construct than 15-18" of fluff on an attic floor, and becomes comparable to the cost to a high-R wall, though the framing is often simpler, since there are fewer interruptions to deal with such as windows & doors. In a cost per square foot basis and a fixed cost/benefit ratio you can still go higher-R on an unvented roof than on walls, but not by quite as much as code minimums might imply.
And yes, if you wanted to build your walls with R20 on the exterior and R30-ish fluff in the framing, that would be a very good wall!
Closed cell foam on the underside of an roof with an adhered membrane + R20 above the roof isn't particularly risky, but it's completely not necessary in a zone 5 location with R30-ish cavity fill between the rafters. The adhered membrane is an air barrier, and the average temp at the roof deck is sufficiently warm that it won't accumulate problematic amounts of moisture. Closed cell foam under the roof deck underperforms thermally due to the thermal bridging, and only limits the drying capacity toward the interior. If there is enough R above the roof deck, forget about it- the closed cell foam buys you pretty much nothing.
If there is NO insulation above the roof deck, 2" of closed cell is sufficiently low permeance to protect the roof deck (without blocking drying completely), and an interior side smart vapor retarder would be enough to keep the rest of the insulation dry. See: http://buildingscience.com/sites/default/files/migrate/pdf/BA-1001_Moisture_Safe_Unvented_Roofs.pdf
Dana, I am talking about a vented roof. Vented below the roofing, over the insulation which is over the bottom layer of sheathing. De-couple the roof from the deck. Why thermally bridge them when venting is almost free?
Likewise, a wall should be vented as well imho. No point in putting siding in contact with the WRB