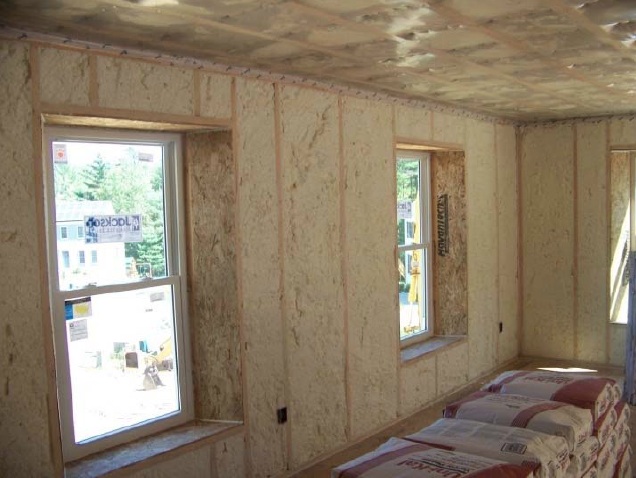
Image Credit: Building Science Corporation The house in this study is wired up with a lot of sensors to measure temperature, moisture content, and relative humidity in various places (indoors, outdoors, and within the walls).
Image Credit: Building Science Corporation After three years, the research team took the walls apart. In this photo, you can see the three different wall sections studied.
Image Credit: Building Science Corporation The sheathing on the south wall showed no damage after three years.
Image Credit: Building Science Corporation The sheathing on the north side, which had experienced moisture contents indicating failure, also showed no damage.
Image Credit: Building Science Corporation
Insulation is good. More insulation is better (although at some point, more may not be cost-effective). It reduces the amount of heat a home loses in winter or gains in summer.
You can get there by building thicker walls and putting more insulation in the cavities, or you can put insulation on the outside of the structure, as in the Perfect Wall. The photo here shows thick insulation in the cavities of a home with double-stud wall construction.
When you do it by making the walls thicker, you also change the ability of an assembly to deal with moisture because the sheathing stays colder in winter, an issue that painters discovered back in the early days of insulating homes when walls stayed wet and paint peeled off. With a 2×4 or 2×6 wall, dealing with the rain on the outside of the wall is usually enough to prevent problems (unless you’re in an extremely cold climate).
Going to thicker walls, though, especially double-stud wall construction with cavities that are 12 inches thick, makes vapor diffusion of interior moisture a bigger threat. Building Science Corporation (BSC) recently published the latest results from its study of a home in Massachusetts with double-stud walls and found a somewhat surprising result about cold sheathing getting wet.
The BSC study
BSC has been working with home builder Carter Scott of Transformations, Inc. on this Building America research project. Scott builds superinsulated homes in Massachusetts (climate zone 5A) using double-stud wall construction. The house in this study is wired up with a lot of sensors to measure temperature, moisture content, and relative humidity in various places (indoors, outdoors, and within the walls). The photo below shows the sensors in one of the walls. You can look at the full BSC report to get all the details about them.
The BSC study used both cellulose insulation and open-cell spray polyurethane foam (ocSPF) insulation, and they monitored what happened to the OSB sheathing (Huber’s Zip System sheathing) over a three-year period on the south and north walls of the home. Further, they looked at two different thicknesses of ocSPF: 5.5 inches and 12 inches. The cellulose was 12 inches thick. (GBA reported on this research project in a November 2013 article called Monitoring Moisture Levels in Double-Stud Walls.)
In this article, I’m going to focus on a few key questions:
- How wet does the exterior sheathing get?
- Where does the water come from?
- Does the wetting cause any problems?
How wet does the sheathing get?
The BSC report shows three years of data. The set of graphs below shows the moisture content (MC) in the three wall sections (12-inch-thick open-cell spray foam insulation, 12-inch-thick cellulose, and 5.5-inch-thick open-cell spray polyurethane foam) as well as the outdoor temperature. Keeping the moisture content of wood below 20% is considered to be safe. If the moisture content goes above 20%, there’s enough water to start growing mold and rot fungi.
Notice that the two spray foam sections stay below 20% moisture content for all but a few months in the second winter. The sheathing next to the cellulose insulation goes above 20% in all three winters, at least in some places.
Clearly, though, the second winter showed the most potential for moisture problems. The moisture content of the OSB sheathing went above 20% for all three wall types. The good news is that by mid-summer, the moisture content was back down to about 10%.
The graphs above are for the north wall. The data from the south wall show the same basic pattern, but the moisture contents are all lower. The 12-inch-thick ocSPF, in fact, stayed below 20% all three winters. The 5.5-inch-thick ocSPF went slightly above 20%, and the cellulose section went up almost to 30%.
So, how did the walls get wet? And did the moisture cause problems?
Where does the water come from?
Water that gets into building assemblies can come from a variety of sources. It could be rain getting through bad window flashing or a roof leak. It could be ground water wicking up through the foundation and into the framing. It could also be from water vapor in the air. In this case, it’s the last of those.
The graph below shows the interior relative humidity (RH) in the basement and in the north and south rooms where the test walls were located. In the first and third winters, the RH spent a good amount of time between 10% and 20%. In the second winter, the RH spent a good amount of time above 40%.
The first winter was dry because no one was living in the home yet. By the second winter, there were occupants but the ventilation system wasn’t operating until mid-February. After they started ventilating (exhaust-only, two 30 cfm fans), the air dried out and by the third winter, the indoor air was dry again.
Those numbers correlate with well with the changes in moisture content in the OSB sheathing. And that raises an interesting question: Do you need to keep the indoor RH below 30% to keep the sheathing in double-stud wall construction from getting wet? That’s a bit on the low side.
When I asked Kohta Ueno, the author of the BSC report, about this, he said low relative humidities are typical in New England. “I have very seldom seen houses running 40% RH through the entire winter around here.” Most homes, he said, run at about 20-30% RH through the winter, and he considers 40-50% RH to be “crazy-dangerous levels in a New England/Zone 5 type of climate.”
Does the wetting cause any problems?
Another really cool part of this study was what they did after three years of collecting temperature and moisture data: They took the walls apart and inspected them for signs of rot, mold growth, or other problems.
The last three photos below show the disassembly. The first of them shows the north wall with siding and sheathing removed. You can see the three sections with different insulation. The second photo shows the sheathing from the south wall. They found no damage here and no evidence of mold or rot. The final photo shows the north wall sheathing. They found no indication of mold or rot here either, although they did see some rust on the nails.
The results were surprising because the moisture content of the sheathing had gone so high in the second winter. In Martin Holladay’s 2013 article on this double-stud wall research, Ueno is quoted as saying, “I don’t think it’s an issue. As Mark Bomberg says, ‘We measure the moisture content of wood during the winter but it rots during the summer.'”
When I spoke with him last week, though, he was a bit less sanguine about it. He told me the walls stayed wet long enough into spring that it was warm enough to grow mold. In the report’s conclusion, he wrote, “Based on the monitored data, calculations, and analysis, all three walls should have been at high risk of failure; the analytic tools used indicate that these walls should have failed.”
But taking the walls apart at the end of three years showed that they not only did not fail but were “essentially undamaged.” Ueno thinks it may be the borate added to cellulose that helped protect the sheathing in that wall. He proposes several hypotheses for the success of the spray foam walls, which had lower moisture content but still should have failed, but wrote in the report, “The protective mechanism of the ocSPF wall was not clear.”
In a Journal of Light Construction article on this study, Ueno told author Ted Cushman that Joe Lstiburek appears to be right. “Joe has said for years that building assemblies are more robust than we give them credit for. This is a solid demonstration of that fact.”
Addendum
4/22/15 This just in: I spoke with Joe Lstiburek today, and he wants to make sure it’s clear to readers that he does not recommend this wall assembly. “I would never build that wall because I consider it too risky,” he said. This was a research project for BSC, not a building that incorporated their design. Details in next week’s blog.
Allison Bailes of Decatur, Georgia, is a speaker, writer, energy consultant, RESNET-certified trainer, and the author of the Energy Vanguard Blog. Check out his in-depth course, Mastering Building Science at Heatspring Learning Institute, and follow him on Twitter at @EnergyVanguard.
Weekly Newsletter
Get building science and energy efficiency advice, plus special offers, in your inbox.
50 Comments
Allison
Have you seen the results of their testing in other climates? I understand they were doing similar work in a Vancouver test house.
I'd be interested to hear other's views on where they feel this leaves us. Building assemblies may indeed be more robust than we generally give them credit for, but not the other hand, at least here in the PNW, they do frequently experience moisture related damage - especially to sheathing.
Poly and MC in outside sheathing...
I know the progressives on the continent have moved away from "6mil poly", but here in Ontario it is enshrined in the building code and consequently its used often. The paper tested only "..walls [with].. a relatively vapor open Class III vapor retarder (latex paint on gypsum board) as the interior vapor control layer." and I wonder had they used "6mil poly", would it have significantly reduced the winter peaks in MC?
Curious data
The fact that the ocSPF walls hit the same moisture peaks independent of the wall thickness implies that the wetting of the exterior OSB was not predominantly from interior side moisture diffusion. The 12" thick cavity had something like half the vapor diffusion of the 5.5" thick cavity, yet the moisture in the OSB was essentially the same.
This implies that direct wetting of the exterior may have been a factor.
The wall stackup diagram in Figure 1, p2 (p13 in PDF pagination) does not specify the siding type, but the photographs elsewhere appear to be vinyl, which is inherently back-ventilated. There is no separate WRB- they're relying entirely on the Huber ZIP coating, and there is no rainscreen gap. Any liquid moisture that gets by the vinyl siding ends up on the ZIP, and they're apparently relying on the back ventilated vinyl siding to provide sufficiently fast drying (usually does.) But unlike a stackup with a housewrap WRB, there is not even a hint of capillary break between the WRB & OSB. It may be useful to compare a housewrap stackup to ZIP to see how it compares.
I'm not surprised that the cellulose hung onto the moisture much longer than the ocSPF, but was surprised at the height of the peaks. Fat cellulose double-studwalls have a fairly good track record in New England, but if it requires sub-30% RH interior air to survive it's not necessarily a great way to build. A smart vapor retarder on the interior are likely to improve the situation more than rainscreened siding (assuming that really WAS vinyl), but using a crinkle-type housewrap to provide some amount of capillary break between the WRB & OSB wouldn't hurt either. A smart vapor retarder would reduce the vapor retardency to the interior to that of the OSB or lower in winter (even with 40% RH conditioned space air), which would give the OSB a much better shot of dry-through, but would not appreciably slow the springtime drying rate.
Dana
I notice Allison says:
"Going to thicker walls, though, especially double-stud wall construction with cavities that are 12 inches thick, makes vapor diffusion of interior moisture a bigger threat."
He appears to be drawing different conclusions. First that it is the wall thickness that causes the problems, and that the source isn't exterior wetting or poor air sealing, but diffusion from the interior. Both seem to be at odds with what you have pointed out in the data.
Response to Malcom Taylor (#1)
I don't know about the Vancouver project, but I spoke with Joe today, and I'll be publishing an update on this article. Despite what I wrote at the end of the article about his belief in the robustness of buildings, he said wouldn't recommend this assembly because he considers it too risky. More later.
Response to Greg Labbe
I think the answer to your question is yes, a layer of 6 mil polyethylene would have reduced the moisture flow from the indoor air to the sheathing.
By the way, are you saying that Ontario is not "on the continent"?
Response to Dana Dorsett
Hmmmm. I hadn't noticed that, and I can't find anywhere in the paper where Kohta discussed it either. Another possibility besides wetting from the exterior is lateral migration of water in the OSB. On the north wall, the 12" ocSPF was next to the cellulose, but the 5.5" ocSPF was on the other side of the window. (See figure above.) Lateral moisture transport in OSB would be easier than water coming from outside.
The cladding was indeed vinyl, which is vented. See page 8 of the report, just below Table 3.
Thanks for verifying the siding type. (response to Allison, #7)
Wind driven water can and does make it by vinyl siding during a typical New England Nor'Easter, and the ventilation rates behind vinyl siding aren't as assured as with rainscreen cavities specifically designed to convect.
I agree that lateral movement within the OSB will skew the numbers a bit on a foamed cavity right next to a soggy-cellulose cavity, but the sensors are well apart from one another, (as seen in the pictures- see figure 11, p.12) with quite a bit of drying area between them. A high drying rate into the vent space behind the siding should null most of that out. I'm skeptical that diffusion wetting of the cellulose would be so high that the OSB three feet on either side of the cellulose portion would make the moisture content in the 12" ocSPF and 5.5" ocSPF sections the same just from lateral wicking. That would imply that the diffusion wetting through the foam was so low that it's contribution was a secondary factor at best.
I've often wondered about whether the WRB coating on ZIP was adequate for all situations, given the lack of capillary break. Under a full rainscreen it's probably background noise, but with unvented siding of different types tight to the sheathing it seems like it might be marginal, and not quite as good as a housewrap solution.
For what it's worth
Bill Rose has repeatedly said that wintertime moisture accumulation in sheathing is driven by temperature, not diffusion from the interior. According to Bill, in most cases the source of the moisture is the exterior air.
Martin
If Bill is right ,would that mean that an uninsulated shed would see the same moisture levels in its sheathing, but have a greater capacity to dry when seasons changed?
Allison
Here is a link to the ongoing Vancouver tests:
http://www.buildingscience.com/documents/special/vancouver-test-hut
Thank you to
Thank you to Allison,BSC,Martin, Dana,Malcolm,and all contributors. This is important info. for designers and builders, and the discussion and comments are equally useful. I know OSB is cheap and therefore prevalent, but it seems like such a bad idea in these buildings. Plywood is twice the price but it seems like cheap insurance. Of course, rain screens and good detailing of flashings are important. I'd love to see a comparison of these walls with a rain-screened, plywood sheathed wall.
Response to Malcolm Taylor
Malcolm,
I don't want to put words into Bill Rose's mouth, but based on several conversations I've had with him over the years, I think that he would agree with your analysis. On a barn, the siding and sheathing get wet in winter, but dry very quickly in the spring.
Of course, in a house with insulated walls, outward diffusion still happens during the winter -- the question is, how much of a factor is it compared to sheathing temperature? Is it a significant or minor factor?
The answer can be found by WUFI modeling -- and of course whether you accept the validity of the WUFI calculations depends on your faith in WUFI (and the inputs) -- but not by field measurements. All field measurements can tell you is how damp the sheathing is.
We can draw inferences from field measurements, however -- as when the MC of the sheathing is correlated with changes in indoor RH. Needless to say, this is a complicated issue.
Run the numbers
My first response is--run the numbers. Calculate the diffusion flow. Compare that to the change in moisture content due to cold weather outside--actually due to high RH during cold weather. The cold weather effect dominates in almost all cases.
Then I realize that people don't run numbers any more. The steady-state ASHRAE profile method (Glaser method) is poohpoohed, especially by people who do not use it correctly. Once the lines are seen to cross it is critical to calculate flows to and from the critical plane and make judgments based on the accumulation number. ASHRAE fails to give good guidance on how to interpret that accumulation number. (That's my fault, incidentally.) People run to WUFI, a black box that does not welcome customization, necessary for any good analysis.
So I'm trying to get a book written on Spreadsheet Hygrothermal Analysis. To fill the void between Glaser and WUFI. Use, say, monthly average input values in Glaser, since ASHRAE Standard 160 recommends monthly average outputs for decision-making. What do you do with the Glaser method accumulation number for January? Dump it on February. Link the months, and now you have a semi-transient model, fully transparent, and everybody who cares to can run the numbers. You can customize the perm values using tables already in the ASHRAE Handbook. You can cobble together ways to account for radiant effects, even convective effects. You can apply the "mold index" criteria to determine if an assembly is satisfactory or not.
It's correct to say that the exteriors of well-insulated buildings have colder and therefore wetter exterior materials. Diffusion from indoors could, I suppose, graduate in importance from being negligible, under some conditions. I've never seen a wetness problem in the field that can be attributed solely to lack of diffusion control. Years ago I checked with big-name colleagues and they hadn't either. I got mold from diffusion only in a fiberglass-insulated wall cavity in my lab one year.
Why is vapor entering the wall cavity?
The article lists many ways that water can get into a wall cavity, but concludes that, in this case, the water entered the wall as vapor from the interior living space. We know that this cannot have been caused by diffusion because the role of diffusion is said to be negligible. We also know that vapor migration from the conditioned space can be prevented with an air barrier. Yet, I find no mention of the air barrier details, or mention of a failure of the air barrier or a reason for the failure.
I would not want to live with the seasonal buildup of wall cavity moisture and then rely on the change of seasons to dry that moisture back out before it can cause mold or rot. Why rely on that threading of the needle rather than just keeping the vapor out of the wall in the first place?
Response to Ron Keagle
Ron,
I've spoken to Kohta Ueno and Carter Scott about these walls, and I think it's safe to say that they were assembled with close attention to airtightness, and that air leakage has been well controlled.
I think that the amount of moisture that moves from the interior to the sheathing in winter is small, as Bill Rose hypothesizes ("The cold weather effect dominates in almost all cases.") That doesn't mean it is zero. Diffusion occurs; calculations can be performed to quantify it. Air leakage in this case is probably minimal. I believe that the main reason that this sheathing gets damp in February is because the sheathing is cold. That doesn't mean, however, that diffusion should be ignored.
Response to Martin Holladay
Martin,
You said: “I believe that the main reason that this sheathing gets damp in February is because the sheathing is cold.”
Just to clarify, what do you believe to be the source of the moisture that is encountering that cold sheathing?
Response to Ron Keagle
Ron,
Q. "What do you believe to be the source of the moisture that is encountering that cold sheathing?"
A. Of course, I will defer to any answers provided by the building scientists conducting this research.
In the meantime, my guess is that the main source of the moisture was exterior air, with some possible contribution from interior moisture that migrated to the sheathing by diffusion.
"What do you believe to be the source of the moisture"
We are still speculating because we haven't measured air leakage from inside or from outside. Diffusion is ALWAYS negligible, with or without poly (as I explain below) There is a fourth source of moisture that I call condensation pumping, which is related to condensation vacuums:
Condensation Vacuums and Why Poly Vapor Barriers Cannot Work in some Wall Assemblies
Please watch this video about “steam vacuums”, to understand an important side effect that occurs when water vapor condenses: https://www.youtube.com/watch?v=Tm3f1MfrWdM
The volume of a gram of water vapor is 1700 times larger than a gram of water*. That means when a gram of water (one cc) condenses, 1700 ccs of air must rush in to take its place. This phenomenon is the reason steam heating systems from the 1800s can throw heat into a room a half a block away from the boiler without a pump.
That 1700 cc of new air may contain more water vapor, and now this new vapor can hit the condensing surface and condense, and so on. Since this vacuum effect can cause a local pressure difference of 12-14.7 psi, a stapled 6mil polyethylene vapor barrier is useless. In fact, anything short of a pressure vessel will fail under that much force.
Note this isn’t “vapor drive” which is caused by a concentration gradient and obeys Fick's law, which is linear. Smart membranes are also useless.
In the leaky wall assemblies of the past, or in walls with interior air barriers (like airtight drywall), this effect shouldn't cause problems because the condensing surface is close to the outside of the wall where it’s colder. When the water vapor collapses, it would be replaced with outside air. The outdoor air is even colder than the wall cavity, which means it would be too dry to cause any condensation. Hence no chain reaction, and the wall cavity just gets filled with outside air.
Now that tight walls often have exterior air barriers (such as taped sheathing), however, the condensation vacuum can pull warm, moist interior air into the wall cavity, and start a chain reaction of condensation pumping.
Joe Lstiburek is quite aware of this phenomenon, and believes it caused the space shuttle crash of 2003 http://www.buildingscience.com/documents/insights/bsi-021-thermodynamics-its-not-rocket-science/?searchterm=space%20shuttle
He must have a reason for not connecting the dots here.
The good news is that the Shirley wall is proving that these assemblies are in fact NOT risky.
https://www.greenbuildingadvisor.com/blogs/dept/musings/dense-packed-cellulose-and-wrong-side-vapor-barrier
Response to Kevin Dickson
Kevin,
You wrote, "We are still speculating because we haven't measured air leakage from inside or from outside."
From the BSC report: "Airtightness = 1.0–1.5 ACH50 range, typical."
water comes from where
Wood products, and any sorptive materials, have an equilibrium moisture content that is a function of surrounding air relative humidity. Here in the midwest, that means that the cold air tends to have high RH, so MC of exterior materials tends to be high. The "vapor vacuum" image is somewhat correct in a sense. The material will get its water from wherever it can--inside, outside, wherever--along paths of least resistance. Just as when it heats up it will discharge its water wherever it can.
Kevin Dickson's observation that the phase change of water vapor leads to a lowered air pressure is correct (higher air pressure when the material warms up), but its impact may be limited in a wall. TenWolde's group at FPL measured air pressures in cavities that were sometimes higher sometimes lower than either the indoor or outdoor air pressure. That's probably just tortuosity or instrument noise, but may have a phase change component. The air vacuum gets makeup air from wherever it can, but that vacuum need is pretty easily satisfied, with usually only a small change in the humidity of the air surrounding the "thirsty" material. Joe might be right about the space shuttle. We are looking into that effect possibly occurring in soil gas.
Response to Martin
A blower door test measures the relative tightness of the overall wall assembly. It does not measure the actual amount of air moving through the wall during the moisture tests. The air carries water vapor. The amount of vapor transported by the air has always been shown to be much higher than the amount that diffuses.
I can't even imagine how it could be measured in the lab unless you controlled it first. But you can't control it in the field, so then it wouldn't be a realistic test.
What's worse, is that unless the condensation pumping effect is accounted for, the mass balance of the air movement will be out of whack.
That is, the mass of air entering the wall should equal the mass of air leaving. But if the water vapor in the air is condensing or being adsorbed by the sheathing, then the mass of air leaving could be significantly less than what is entering.
BSC research, not design
I added a note to the end of the article yesterday because I spoke with Joe Lstiburek and he wanted to make sure it's clear that this was a BSC research project, not a home they did the building enclosure design for. "I would never build that wall because I consider it too risky," he told me. I'll write more about that next week.
I'm speaking at a conference in Oregon this afternoon, but I'll try to jump back into the discussion tomorrow.
Cold Sheathing Doesn't Rot
In this testing, when the MC of the OSB gets above 20%, the temperature is cold. For rot to occur, the MC and temperature both have to be high at the same time and for a long enough time.
These results show that it didn't happen for a long enough time to start rot.
I think all this is pointing us toward thick walls with (inside to outside) gypsum, cellulose, plywood sheathing, vapor permeable air/WRB, drainage plane, and siding.
It is robust, simple, cheap, and I like what it doesn't have or need:
1. Poly vapor barrier
2. Any vapor barrier
3. Spray foam
4. Rigid foam
5. Expensive long screws
6. Airtight drywall
7. Larson or Riversong trusses
8. Separate water and air barriers
We also know that if air leakage is high, the wall will fail. So there should be a maximum allowable blower door test number to go with the wall assembly.
The phase change here isn't vapor to water...(response to Kevin)
... its vapor to adsorb in the wood fiber. There is no condensation taking place. But the air pressure effects of subtraction/addition of water vapor from adsorb aren't really different from condensation.
If it's strictly a sheathing temperature and air-tightness issue, is are leakage the ONLY operating theory why the dense packed cellulose cavity hit higher peaks than the more air-tight ocSPF?
Also, without continuous monitoring & data logging the Shirley house example falls well short of "proof". A randomly timed mid-winter one-off moisture content sample doesn't cut it the way continuously logged data logged over three years does.
Response to Dana
I agree that one measurement isn't proof.
But all the building scientists have cautioned against the Shirley wall for years because of modeling results. All the models are highly flawed as Martin pointed out in 2013: https://www.greenbuildingadvisor.com/blogs/dept/musings/monitoring-moisture-levels-double-stud-walls
Already the building codes require exterior foam based on these models. That's bad because it raises the cost and complexity of walls.
National Fiber says "The ability of cellulose to disperse moisture to the interior, combined with its high installed density of over 3.5 lbs/cuft, makes vapor barriers and airtight drywall unnecessary and, in fact, counterproductive, with dense pack cellulose insulation. This has been borne out by the more than thirty years of experience we have with the first generation of superinsulated cellulose buildings that were constructed in the early 1980’s."
This BSC report indicates the Shirley wall could be close to a failure point. I'm suggesting that conventional plywood instead of OSB will make it reliably safe.
Response to Kevin Dickson
Kevin,
You wrote, "The building codes require exterior foam based on these models."
You are mistaken. The most convincing evidence of the robustness of foam-sheathed walls comes from field studies, not modeling exercises. We now have at least two decades of very convincing data from field studies in many climates, and they all point to the fact that the type of wall with the most consistently dry sheathing is a wall with an adequate thickness of exterior rigid foam.
That said, all building codes in the U.S. allow the construction of double-stud walls, as they should. Building codes have always been extremely permissive when it comes to wall construction details. Building codes not only permit the construction of double-stud walls -- walls which appear to be fairly robust -- but they permit all manner of extremely stupid walls, many of which fail very quickly.
Smart vapor retarders in worst cases ( for Kevin)
Compare the moisture content of the sheathing in the unvented stucco walls with/without vapor retarders in this not-so-cold climate (not too different from Vancouver), when the interior RH was maintained at 55%:
http://www.energy.wsu.edu/documents/AHT_ComparingTheMoisturePerformance%20Of%20Wood%20Framed%20Wall%20Systems.pdf
Wall # 8 has an inch of foam and a smart vapor retarder, Wall #2 just the smart vapor retarder, Wall #1 had a polyethylene vapor barrier.
Unfortunately they didn't test a vented assembly with only latex paint as the interior side vapor retarder.
But if you look at the graphs (starting on page 15) of the MC 3 & MC 4 moisture content sensors for the sheathing you'll clearly see the benefits of both the exterior foam AND the vapor retarders.
Wall #8 has both the foam & smart vapor retarder and is clear winner by a good margin, where the moisture content of the sheathing barely changes with seasons. It was comparable to wall #4, which was vented stucco siding with a poly vapor barrier.
Wall #7 is the clear disaster, with only a latex paint on the interior.
This test has is a higher interior side diffusion drive than a real-world typical in that climate, but not necessarily worse than a house in New England location with no exterior foam and an impermeable membrane on the exterior of the sheathing such as the Shirley house, if kept above 30% RH, given the much colder sheathing. (Average mid-winter temp in Puyallup WA is about +40F, compared to about +23F in Shirley MA.)
The WSU test indicates that vapor diffusion is still an important factor when there is little or drying toward the exterior. If the moisture in the sheathing was coming from the outdoors the vapor retarders & exterior foam would have made little difference, but they clearly DO make a difference.
You can always ventilate the Shirley house to keep the interior RH under 30% in winter to keep the sheathing dry (which is what it would take in the Carter Scott ocSPF walls) but 30% is the low limit of what's considered the healthy range for humans. I'd be surprised if a smart vapor retarder didn't move the needle considerably on Carter Scott's cellulose insulated wall.
Kevin
I agree this is fascinating stuff and I am indebted both to the present contributors and those who did the heavy lifting to bring the building science to this point. This does feel like one of the a last big areas of uncertainty in building envelope design and it seems like some consensus isn't far off.
As someone who went through architecture school in the mid-'80s and starting practicing after that, you have idea how refreshing all this is. We simply had no idea what we were doing.
Indoor Air vs. Outdoor Air
The article says that the water entering the wall cavity is water vapor in air. But it stops short of stating whether the air is outdoor air, or air in the conditioned space. It seems to me that there is a big difference in the wall cavity moisture rise, depending on whether the vapor is coming from indoor air or outdoor air. This is my evaluation of that difference:
PROCESS OF OUTDOOR AIR VAPOR:
As the average outdoor temperature falls during the winter season, it lowers the average temperature of the sheathing, which causes an average corresponding rise in the moisture content of the sheathing. So once the average temperature of the sheathing reaches its lowest point, there is no more accumulation of moisture content.
PROCESS OF INDOOR AIR VAPOR:
As the average outdoor temperature falls during the winter season, it lowers the average temperature of the sheathing, which causes an average corresponding rise in the moisture content of the sheathing.
However, unlike the outdoor air process, the indoor air process provides a continuous outward flow of higher vapor pressure as it seeks to equalize with regions of lower vapor pressure. So with this process, there is no end to it, even when the sheathing reaches its coldest average temperature.
Unlike the outdoor air process, this indoor air process continues to feed moisture into the sheathing as the sheathing temperature drops below the condensing temperature of the vapor; until the sheathing is 100% saturated. Then, once the outdoor average temperature falls below freezing, it freezes the water in the saturated sheathing.
But the indoor process continues feeding vapor into the wall cavity where it condenses and freezes on the inside surface of the frozen sheathing. The ice layer will continue to thicken as the indoor air vapor feeds into the wall cavity. It seems to me that the process could fill the entire wall cavity with solid ice if the outdoor temperature remained below freezing.
Response to Ron Keagle
Ron,
You wrote, "But the indoor process continues feeding vapor into the wall cavity where it condenses and freezes on the inside surface of the frozen sheathing. The ice layer will continue to thicken as the indoor air vapor feeds into the wall cavity. It seems to me that the process could fill the entire wall cavity with solid ice if the outdoor temperature remained below freezing."
The scenario you describe could happen -- but only at an indoor swimming pool facility in Antarctica. The rate of diffusion is too slow, and the the sheathing is too warm, and winter is too short, for your scenario to occur in Vermont, Minnesota, or Manitoba.
Response to Martin Holladay
Martin,
I understand your point, but my point was not to warn about the scenario. It was only to show the fundamental difference between the two processes; that being that the outdoor process is a one-time, wintertime adjustment that accumulates only during that adjustment, whereas the indoor process is continuously accumulative during the wintertime. Of course both processes are subject to short term warming and cooling cycles and intermittent drying of the wall cavity.
But on average, the indoor process has much more potential to wet the wall cavity than does the outdoor process. Also entering into this is the fact that the indoor process can be 100% mitigated by stopping diffusion and airflow out of the conditioned space, whereas the outdoor process can only be mitigated by insulation outside of the sheathing.
Response to Dana
Dana,
We are learning some things from tests like you have cited.
My position is that all the testing including BSC's latest, is flawed.
The flaw is that no test has controlled for infiltration flowrate. During all those tests, the amount of air moving through the wall is unknown.
Diffusion & a comment from John Semmelhack
I think the graphs above make it pretty clear that the source of the moisture is indoor water vapor diffusing through the wall. I know correlation doesn't prove causation, but there's excellent correlation between the indoor RH and the moisture content in the sheathing. When the indoor RH was low in winters 1 and 3, the sheathing moisture content was fine. When the RH was 40-50% in winter 2, the moisture content went too high.
Also, John Semmelhack sent me his thoughts on this in an email this morning. Here's what he wrote:
I've been following the discussion and I think there are some big things that people are missing, so I thought I'd send them straight to you for possible inclusion in your discussion. Curious to hear what Kohta and Joe think as well.
1) Where is the moisture coming from (part 1)? Bill Rose's comments indicates he thinks the bulk of the moisture in the sheathing must come from the outside, due to elevated RH% during colder weather….however, I don't think he's looked at the data….average outdoor RH% during Dec. 1 to March 31 in each of the three winters ('11-12, '12-13 and '13-14) at the Fitchburg, MA weather station ~10-15 miles away from Devens was 63%, 67% and 65%….all of which translate to an equilibrium moisture content in wood of something like 12-13% (based on the charts I have access to)…..certainly nothing that's going to create wet sheathing!
2) Where is the moisture coming from (part 2)? Other's have wondered about air leakage….as I mentioned on your site, the house is tight and has an exhaust ventilation system. If the house tested at 1.1ACH50 and has a 60cfm exhaust ventilation system (starting mid-season in winter #2), the ventilation system will depressurize the house to roughly 4Pa (without accounting for stack or wind). Constant 4Pa fan depressurization should be just enough to overcome stack and wind (on average) throughout the Devens, MA winter….which should effectively negate air exfiltration as a possible cause of major moisture accumulation in the sheathing. On top of that (and possibly even more relevant), any significant air leakage in this house is not likely happening in the walls with taped Zip sheathing and a combination of open cell spray foam and cellulose! The leaks are likely elsewhere...
3) Where is the moisture coming from (part 3)? Folks seem to be missing that the surface rust on the fasteners is on the inside of the wall and that the sheathing shows "raised grain" (in the cellulose section) on the inside of the sheathing. It certainly seems to me that the moisture is coming from the inside, and since we've already ruled out air exfiltration, we're left with diffusion from inside.
Response to Kevin Dickson
Kevin,
Field studies are extremely valuable, even if some factors are very difficult to quantify in the field.
I think you are underestimating the difficulty of quantifying air flows through building assemblies. BSC researchers know a bit about this issue, because the company almost went bankrupt underestimating how hard it would be to measure air flows through building assemblies in a lab -- which they attempted to do (and finally succeeded in doing) in a research project that took many years longer to accomplish than originally planned. For more information on this issue, see:
A Bold Attempt to Slay R-Value
Air Leakage Degrades the Thermal Performance of Walls
Walls without exterior sheathing
We did a couple of houses last year in Montana with a Riversong/Clupp type wall section. 2x4 sheathed interior wall as air barrier, then 8.5" curtain wall with cellulose to the outside. No exterior sheathing, just building wrap, 1x furring (rainscreen) and siding. I wonder what happens on that building wrap surface? We obviously get the cold temps so moisture from the exterior air may accumulate in the outer layers, but would be readily vented away.
Response to Martin
I absolutely understand how difficult it is to quantify air flows through walls.
Joe L. says, "The only true measure of air changes is tracer gas." I agree. (From http://www.energyvanguard.com/blog-building-science-HERS-BPI/bid/66004/Interview-with-Dr-Joe-Lstiburek-The-Ventilation-Debate-Continues)
He has also said something to the effect of: A blower door test doesn't tell us the natural infiltration rate. We don't know the geometry of the holes in the envelope, and there is no accurate way to convert an ACH50 to an actual ACHnat. (Sorry I can't find that quote)
I'm saying that unless the actual ACHnat is measured or controlled for, all the previous tests are helpful only empirically.
And you don't actually have to measure it, just control for it. To control for it means that you make sure that it is the same in all the testing. In the latest BSC test it is "minimal" (1.0 ACH50) but not zero, not measured, and certainly not consistent.
Response to John Semmelhack via Allison
You said,
"3) Where is the moisture coming from (part 3)? Folks seem to be missing that the surface rust on the fasteners is on the inside of the wall and that the sheathing shows "raised grain" (in the cellulose section) on the inside of the sheathing. It certainly seems to me that the moisture is coming from the inside, and since we've already ruled out air exfiltration, we're left with diffusion from inside."
You are also left with the adsorption/condensation pumping effect that I've described above. I take no offense if you wish to ignore it. All the researchers have.
But stick with me through this thought experiment before your forget it completely.
Consider one-pipe steam heating systems. They routinely deliver large amounts of heat to registers up to 500 feet away from the boiler through a 2" pipe without any mechanical delivery work. How do they do it?
One thing we know for sure is that water vapor is created in the boiler and the vapor is condensing inside the register.
So what causes the vapor to travel from the boiler to the condenser?
1. Is it convection? After all, the registers are usually higher than the boiler.
2. is it diffusion? After all, the vapor concentration is higher at the boiler than it is in the condenser.
3. Is the water vapor transported by the air in the pipes? After all, there is an air vent at each condenser.
4. Conduction?
All 4 of these are negligible compared to the mass transfer due to the condensation pumping effect. I don't see how walls are different. There is a water vapor source and a condensing surface in both cases. In steam systems, condensation pumping is the well-known transport mechanism.
Why did we forget it in building science?
Summing up
I'll act as referee on the question of the origin of the moisture. I'm already on the record on this one -- in spite of my hunches, I wrote that "I will defer to any answers provided by the building scientists conducting this research."
As we await the researchers' statements, here's what we have:
1. In his article Allison Bailes reported that the source of the moisture is "water vapor in the air," thereby eliminating (apparently) wind-driven rain as an important source of the moisture. He hinted that he's talking about interior air, but didn't seem to exclude exterior air. He later clarified his position, commenting, "I think the graphs above make it pretty clear that the source of the moisture is indoor water vapor diffusing through the wall."
2. William Rose reported that "the cold weather effect [rather than interior RH] dominates in almost all cases," but also noted that the question can't be answered until you do the calculations.
3. Kevin Dickson says the moisture is due to "condensation pumping," which creates a difference in pressure that pulls interior air to the sheathing through cracks in the drywall.
4. Ron Keagle appears to be arguing that this wall has an imperfect interior air barrier, allowing leaking interior air to contact the cold sheathing. He may also be arguing that diffusion of interior moisture is to blame. [P.S. Ron Keagle has responded to this summary by commenting, "All I have done here is hypothesize that outdoor transfer seems to have a limited potential for delivering moisture to the sheathing, whereas the indoor transfer has unlimited potential. However, I cannot come to any conclusion about what happened in the case under discussion here because I do not know if the moisture content measured can be completely accounted for by the outside transfer."]
5. William Rose chimed in, appearing to cast doubt on the importance of Kevin Dickson's "condensation pumping" mechanism. Rose wrote, "The air vacuum gets makeup air from wherever it can, but that vacuum need is pretty easily satisfied, with usually only a small change in the humidity of the air surrounding the "thirsty" material."
7. Dana Dorsett believes that the sheathing moisture is coming from the inside of the house: "If the moisture in the sheathing was coming from the outdoors the vapor retarders & exterior foam would have made little difference, but they clearly DO make a difference."
8. John Semmelhack concludes that air leakage is not a factor, and writes, "It certainly seems to me that the moisture is coming from the inside, and since we've already ruled out air exfiltration, we're left with diffusion from inside."
Response to Martin Holladay
Martin,
Regarding your summary: Actually I have taken no position on the question of where the vapor is coming from. I am not arguing that point at all. We have had extensive discussion in the past about the so-called “cold sheathing problem” and whether it involves vapor moving outward from the conditioned space and condensing-adsorbing on the cold sheathing in cold weather; or whether it involves vapor adsorbing into the sheathing from outdoor air as a result of seasonal cooling. I have seen the potential of the indoor transfer, but I have many lingering questions about the outdoor transfer.
I like the concept of insulating inside of the sheathing versus outside of it. So it concerns me that this cold sheathing problem is always posed as a “risk” associated with insulating inside of the sheathing. Where exactly is the risk? Is it sloppy workmanship, or is it fundamentally related to natural causes that good workmanship cannot overcome?
I would like to see this issue finally resolved rather than hanging there as a nebulous “risk.” So that is why I find this blog so intriguing. It places that central question right on the table, but does not answer it. And yet, if the answer to the question is that the risk is moisture from the outside transfer, then it fundamentally discredits the concept double stud walls, regardless of perfect workmanship.
All I have done here is hypothesize that outdoor transfer seems to have a limited potential for delivering moisture to the sheathing, whereas the indoor transfer has unlimited potential. However, I cannot come to any conclusion about what happened in the case under discussion here because I do not know if the moisture content measured can be completely accounted for by the outside transfer.
The effectiveness of the air barrier is central to the question posed by this blog, and that is why I asked about it. The answer seems to be that the air barrier is sufficient based on the blower door test results. There is a fundamental assumption that diffusion is incapable of causing any moisture problem unless there is unusually high indoor humidity, and that is not the case with this tested house. Therefore, we can rule out the vapor being transferred outward as the cause for the wet sheathing. And yet, Allison Bailes says that “the graphs above make it pretty clear that the source of the moisture is indoor water vapor diffusing through the wall."
So, I would like to pose this question: If the source of moisture is indoor vapor diffusing outward though the walls, how can this be reconciled against the fundamental premise that diffusion is not sufficient to cause moisture in the wall cavity?
Ron
You wrote:
"And yet, if the answer to the question is that the risk is moisture from the outside transfer, then it fundamentally discredits the concept double stud walls, regardless of perfect workmanship."
Perhaps, but if the only material to contain moisture high enough to cause damage is the sheathing, then the strategies that either move it further into the wall, use alternate materials or no sheathing still yield a safe double wall.
Summary: Apparent Conclusions in the State of the Art
1. We can put condensation/adsorption pumping completely aside at least until there are some test results to suggest that it is significant. (More work for the researchers)
2. Bill Rose and others have concluded for at least ten years that the vapor transport from diffusion is negligible compared to the vapor transported by air leakage. ("I've never seen a wetness problem in the field that can be attributed solely to lack of diffusion control. ") As we build better walls and the air leakage rates get lower, we may find diffusion is significant.
3. If you agree with John Semmelhack's logic above (which I do), the walls in this study didn't see any exfiltration. That means the moisture in the sheathing wasn't transported from interior space out to the sheathing via air leakage.
4. We can always conclude that water vapor in the exterior air can't be transported into the sheathing because the sheathing is almost always slightly warmer than the outside air. As soon as the outside air touches the sheathing, saturated air rises above the dewpoint and condensation is impossible. Any wood sheathing will adsorb moisture from outside air, but in this assembly, the MC & temperature can never reach dangerous levels through adsorption of outside air vapor. (Wood can be stored in unheated, vented sheds, or under tarps, and will never rot if bulk water never touches it.)
5. Interior poly vapor barrier is still a bad idea even if diffusion is the largest transport mechanism.
6. Some rigid foam on the exterior of the sheathing could be considered cheap insurance, especially in humid locations. (It's still unclear how much)
Advice for BSC: the present report concludes: "(in the cellulose walls), a Class II vapor retarder (1–0.1 perm; e.g., variable permeability membrane or vapor retarder paint) will reduce moisture risks to more reasonable levels." If you ever try to prove this to be true but find no reduction in MC, start investigating condensation pumping.
Response to Kevin Dickson
Kevin,
You wrote, "Some rigid foam on the exterior of the sheathing could be considered cheap insurance, especially in humid locations. (It's still unclear how much.)"
I think the "how much" issue has been settled. Since exterior rigid foam prevents drying to the exterior, you can't go halfway with this measure. You have to go all the way -- so that the foam is thick enough to keep the sheathing above the dew point during the winter.
Foam that is too thin is a worst-case scenario. The foam is too thin to prevent moisture accumulation in the sheathing in February, but is thick enough to prevent the damp sheathing from drying in April.
Can't go halfway
Martin, your last comment makes a really important point, and as usual, the devil is in the details. Outdoor temperatures go up and down all the time, and clearly you don't need to put enough foamboard on the exterior to keep the sheathing from going below dew point during extreme conditions. I'd think that designing the enclosure to keep the sheathing above dew point when you hit the 99% design temperature would get you enough. The 1% of the time it goes below that temperature shouldn't cause a problem. Do you know of field studies that have looked at this?
Of course, we're sidetracking the discussion with this topic, but I think it's a really interesting one and definitely related.
Foam thickness and condensation
Well, according to Joe Lstiburek, you use the average outside temperature for December through February to calculate the minimum foam thickness to prevent condensation on the sheathing. This doesn't prevent condensation - just condensation on average. I don't know of the studies behind it, but he goes into some detail about this in his Builder's Guide to Cold Climates. In that book Mr. Lstiburek alludes to "detailed dynamic Hugo-thermal modeling" and "extensive field testing and field experience". There is a relevant discussion in that book that applies here, a discussion of the vapor permeability of the sheathing and why that's important to consider when designing your wall, but that discussion stops short of this topic - very thick walls. In that book, Mr. Lstiburek seemingly stops at 2x6 walls with no external foam.
Response to Allison Bailes
Allison,
When I wrote that "the 'how much' issue has been settled," I meant:
Joe Lstiburek's recommendations on the issue have been widely reported -- for example, in Ted Cushman's November 2006 article in Coastal Contractor, and my September 2010 article on GBA, and my October 2010 article in GBA.
Joe Lstiburek's recommendations on the issue have been incorporated into the International building codes.
When I wrote that it is desirable "to keep the sheathing above the dew point during the winter," that was a shorthand reference to the recommendations made by Joe Lstiburek. If you follow those recommendations, the temperature of your wall sheathing won't be above the dew point on the coldest day of the year -- but your wall sheathing will be warm enough to keep you out of trouble, and your sheathing will be much dryer than it would be on a double-stud wall.
Allison and Joe to the Rescue
Allison reminds us that BSC has already designed a safe, high R double wall with cellulose: Lstiburek’s Ideal Double-Stud Wall Design.
What I like - it keeps the structural sheathing near the middle of the wall so it's always too warm to adsorb water vapor, and if condensation pumping should ever happen at the exterior sheathing layer, the replacement air comes from outside, not inside. Outside air is always too dry to cause trouble.
What I don't like - Two layers of sheathing, a separate WRB and air control layer. But this is not a very high price to pay for complete peace of mind.
Clearly you can't count entirely on the hygric buffering.
For those who seem to think dense-packed cellulose in double studwalls works without interior vapor retarders in a VT climate, here's a good example of a 1980s vintage version of just such a wall that failed:
http://www.jlconline.com/moisture-barriers/major-surgery-for-a-failing-fat-wall_o.aspx?utm_source=newsletter&utm_content=jump&utm_medium=email&utm_campaign=JLCNL_070515
The solution using Intello on the exterior side of the interior studs isn't that different from Lstiburek's OSB vapor retarder approach. With the Intello ~1/3 of the way within the stackup it'll be colder, and therefor higher RH, with a 1-ish vapor permeance in winter, but a much higher vapor permeance than OSB when the moisture content rises. The gypsum sheathing and high-perm housewrap under rainscreened fiber cement gives it huge drying capacity toward the exterior, and the moisture in the cellulose should pretty much track the outdoor humidity levels, without huge influence from interior side moisture drives.
Unfortunately we don't know exactly what the original density of the cellulose was, which plays a huge factor in settling, especially when subjected to the high moisture cycling when there is no interior-side vapor retarder.
It wasn't dense-packed
Dana,
Your opening sentence refers to "dense-packed cellulose." But it seems clear to me that the failure discussed in the JLC article wasn't dense-packed: "The cellulose had settled badly, leaving the upper portion of most walls entirely uninsulated."
Your last sentence -- "we don't know exactly what the original density of the cellulose was" -- is disingenuous. If the cellulose settled as badly as described, then this wasn't a dense-pack job.
If you soak the cellulose it'll settle.
I don't think it's at all obvious that they didn't at least TRY to dense pack it.. After ~30 years of fairly extreme moisture cycling it'll settle, even when dense packed. (Per Rasmussen, et al) I'd agree that the starting density was probably less than 3lbs in the worst-case corner that they imaged:
http://www.jlconline.com/Images/1472378703_BradleyRehab-A_tcm96-2201545.jpg?width=600&404=404.png
But SFAIK even 30 years ago nobody was silly enough to blow it into studwalls as if it were just another attic (in which case it probably would have settled by more than 2/3 instead of 1/3-1/2).
I've seen 30 year old ~2.5lb cellulose that stayed dry and didn't settle even an inch in a balloon framed house, but that was 2x4 construction with oil based paint on plaster as the interior vapor retarder. I've also seen ~2.5lb cellulose that was in worse shape than in the picture after 15 years, where the exterior was caulked tight clapboards with multiple layers of leaded oil paint, no back ventilation. There's lots of moving parts to it, but it's primarily a moisture + density thing.
In the case of the failed wall they state:
"Moisture testing showed that the wall cavities were 15% damper than the occupied rooms."
But they don't mention the calendar date of the testing (as if it matters? :-) ), nor did they state the moisture levels in absolute terms.
Even if blown at 2-2.5lbs the density after settling by 1/3-1/2 would be at least 3-3.5lbs, which has the same hygric buffering capacity as typical modern dense pack, yet it appears it was the sheathing & framing where the insulation still remained that had the rot issues- the upper parts of the OSB sheathing looked comparatively clean in the post-mortem. The sheathing in the upper part of the wall sections l that was no longer insulated was a lot warmer, which likely protected it.
There may have been bulk water intrusion problems too- they simply don't go into sufficient detail, but none of the 20 pictures in their slide show obvious bulk water intrusion.
I'm not sure if 1980s vintage OSB is any more vapor-tight than current OSB, but they clearly needed something more vapor-tight on the interior- counting on the hygric buffering isn't enough.
They speculate in the article on the basis of the heavy insect infestation that the original material probably had no borates, which is possible. If it requires borates to keep the rot from getting started it's not going to be a century-long solution in a high moisture cycling environment. Their solution of adding the Intello layer and using vapor-open gypsum sheathing instead of OSB seems like a much more reliable approach, since the cellulose & framing will stay much drier (at any density) and the gypsum itself isn't very susceptible to moisture.
.
Log in or create an account to post a comment.
Sign up Log in