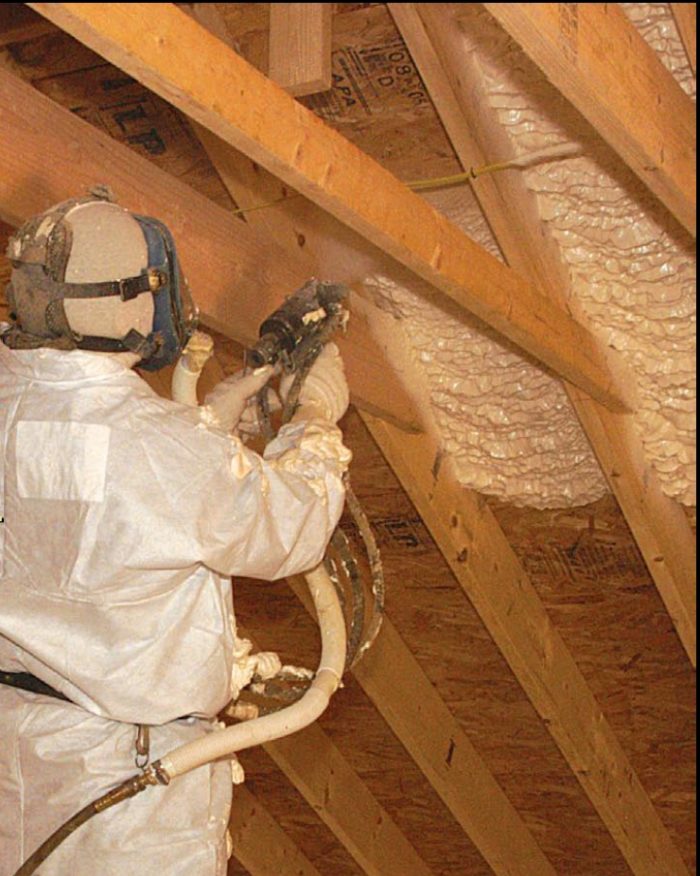
Image Credit: Fine Homebuilding
UPDATED on August 13, 2017 with new concluding paragraphs
Millions of Americans live in states where residential HVAC contractors routinely install ductwork in unconditioned attics. In many cases, these attics also contain a variety of appliances, including air handlers, furnaces, or water heaters.
Because the disadvantages of this arrangement are fairly well known, I’ll mention them only briefly:
- During the summer, attic temperatures often exceed outdoor temperatures.
- Attic ducts almost always have thinner insulation than ceilings, in spite of the fact that the delta-T (that is, the temperature difference) between the air in the ducts and the air in the attic is even greater than the delta-T between the inside of the home and the exterior.
- Most duct seams leak; as a result, supply ducts lose conditioned air to the attic, while return ducts suck in attic air — air which is hot in summer and cold in winter — and bring it to the air handler.
- If access to the attic is through a hatch, servicing any HVAC equipment in the attic is awkward at best.
The bottom line: running ducts through an attic saves money for the builder, but costs the homeowners dearly in increased energy costs.
Ductwork belongs inside a home’s thermal envelope
Ideally, HVAC appliances and ductwork should be located inside a home’s conditioned envelope. In the northern half of the country, appliances and ductwork are routinely located in basements or crawl spaces. If your house has a slab foundation, HVAC appliances can be located in an equipment room and ductwork can be located in interior soffits.
Another solution is to move the insulation from the attic floor to the sloped roof, thereby creating a conditioned attic.
Assuming you want to create a conditioned attic — either during new construction or as a retrofit project — how…
Weekly Newsletter
Get building science and energy efficiency advice, plus special offers, in your inbox.
This article is only available to GBA Prime Members
Sign up for a free trial and get instant access to this article as well as GBA’s complete library of premium articles and construction details.
Start Free TrialAlready a member? Log in
138 Comments
Great article!
Great article, Martin! Maybe you could link this article to the one you wrote a while back about contractors putting in lower R-values when they insulate the roofline. That's an important issue that you kind of glossed over in this article but that generates a lot of discussion, especially from the SPF installers who insist on diminishing their installed thickness because of the diminishing returns of extra R-value.
I agree with you that we need to pay more attention to thermal bridging. Here in the Southeast, SPF installers generally go in and spray about 6" of open cell foam between the rafters for an R-value of ~20. Sometimes they spray over the rafters to reduce that thermal bridging, and sometimes they don't. Rigid foam above or below is almost never installed here. The closed cell installers generally put in the same R-value (~20), but I've seen as little as 2" for R-14.
One thing you didn't mention is whether or not you should remove the existing insulation in the flat ceiling if you insulate the roofline in an existing home. I haven't seen data on this, but I've heard that you should remove that insulation to keep the attic close to the temperature in the house, which helps prevent condensation on the underside of the roof insulation. Any thoughts?
Finally, I think you used the wrong word in the last paragraph of your answer to Question 2:
Remember: insulated rafter bays are incompatible with rigid foam insulation installed on top of the roof sheathing.
Didn't you mean to say 'ventilated' instead of 'insulated' there at the beginning of the sentence?
Response to Allison Bailes
Allison,
Thanks very much for catching my typo, which I have corrected in the text.
Thanks also for all of the points you brought up:
1. As I made clear in my earlier blog, It’s OK to Skimp On Insulation, Icynene Says, I believe that it is essential to comply with minimum code requirements for insulation R-value, even when using spray polyurethane foam. The main reason that spray foam contractors try to circumvent minimum code requirements for insulation R-value is because spray foam is so expensive that it has a hard time competing with other insulation products. I have taken your suggestion to heart and added a reference to this point in my blog.
2. I agree that the Achilles' heel of many spray-foam jobs is that thermal bridging through the rafters is not addressed.
3. In most cases, the existing insulation on an attic floor should be removed when an unconditioned attic is converted to a conditioned attic. However, this recommendation should be addressed on a case-by-case basis. Depending on the climate and the thickness of the existing insulation, it may make sense to leave the old insulation in place.
Follow Up on Removing Existing Insulation
How do you recommend removing the existing insulation? Are there other services out there with truck mounted vacs that could do this? Is is more of a hand and time job?
What about removing extremely deteriorated R-2 Rockwool batts, before blowing cellulose?
Martin: You mentioned that
Martin,
You mentioned that for "many spray-foam jobs thermal bridging through the rafters is not addressed." Can you point me to any other articles by you or anyone else in the Building Science community on thermal bridging at the rafters? By the way, thanks for another great article.
Response to John Nicholas
John Nicholas,
1. Contact cellulose insulation contractors for information on removing existing insulation with a vacuum. Many of these contractors offer this service.
2. If you have severely deteriorated old batts, it's probably a good idea to remove them, if only to get rid of the rodent feces. That's probably an old-fashioned job requiring a dust mask, gloves, and many garbage bags.
Response to Allan Edwards
Allan,
Thermal bridging links -- (by the way, the "search" function on our GBA site can help you track down the answer to questions like this):
Thermal Bridging
Thermal bridging with spray foam insulation
Insulation Overview
Pitfalls of different climates
I appreciate your coverage of this very interesting topic. In the hot-humid South where I live, it is my understanding there are a number of lawsuits from insulated attics and I believe the #1 problem is rotting roof decking connected with undiscovered water leaks. Research is still ongoing but I do not see a consensus yet as to the wisdom, nor guidelines to avoid trouble.
The methods you describe work well in some climates, but around the country there are several zones with special needs. The simple factor of outdoor dew point being chronically very high or low is important in many situations. Hot-humid climates make it normal to consume a lot of energy, and I would like to hear more from the perspective of a builder in such climates.
Thank you for bringing up the attic subject, it is very interesting.
Why Does "Green" Require Hazmat Suits
I love the picture at the top of this article. It always amazes me that people would consider "green" any material or method that is IDLH (a NIOSH acronym for Immediately Dangerous to Life and Health) and requires a complete isolation suit for safe installation.
And M. Johnson, you're quite right that studies have demonstrated the danger to the roof sheathing when roofs can't breathe in either direction and take literally months to dry after a leak event. Anything wooden needs to breathe.
Response to M. Johnson
M. Johnson,
1. You are quite right that installing spray polyurethane foam directly against roof sheathing is controversial, because of the possibility that the foam can disguise roof leaks. That's why I wrote, "Even if you insulate between your rafters with an air-impermeable insulation like spray polyurethane foam, you may want to provide a ventilation channel under your roof sheathing. The main function of such a ventilation channel is to separate the roof sheathing from the foam; this facilitates future repairs of sheathing rot."
2. You wrote, "The simple factor of outdoor dew point being chronically very high or low is important in many situations." If you follow the recommendations provided in this article, however, your roof sheathing will never be cold enough to allow for moisture accumulation in the sheathing due to a dew-point issue -- even (especially) in a southern climate.
3. I disagree with our statement, "Hot-humid climates make it normal to consume a lot of energy." If you design your house well, you will have low energy bills, even in the south. For more information on energy-saving tips for hot climates, see Hot-Climate Design .
Comment from Joe W
[Joe W. was having trouble with the GBA spam filter, so he sent me the following comment by e-mail:]
Martin,
I've heard a couple of proposed solutions to increasing the accuracy of screwing SIPs and thick exterior insulation to rafters.
One was to order truss rafters with a screwable flange -- this was advanced as an easily available option.
Another was to double up truss rafters every four feet to provide a wider surface.
Of course, with a timber frame set up, either rafters or purlins would be expected to be wider to begin with.
Are these legitimate suggestions?
Thanks in advance, and happy new year
Joe W
Response to Joe W
Joe,
If trusses can be ordered with wide top flanges, that seems like an easy solution -- although some truss-spacing jigs probably won't work with wide flanges.
Doubling up trusses every 4 feet doesn't make sense to me, for two reasons: it's an expensive solution, and you'll want to space your screws closer than every 4 feet.
A home that uses half the energy of a code built home
Seal up a home well somehow and stop the flow of heat thru the insulation and a home instantly will use half the energy of yesterdays leaky homes.
Icynene does that and I can take anyone to a home and show you.
The home will have less than R 38 above in complete defiance of Martin's rant that Icynene is selling nonsense. I say Martin who I agree with most of the time is barking up the wrong "R vs. air leaks" tree.
Talk is cheap. I have Icynene installed and it is performing amazingly.
Martin, come visit, I will give you a tour. Then come back to this thread and post your thoughts. I have never seen you post actual hands on experience with Icynene. Stop railing against it till you do have some personal knowledge of the success many of us are having with it.
I am all for going green and entirely cellulose as to insulation. But I am not going to say Icynene does not do a great job. It does. It does for me. It does for my customers. It does for my spray company.
Every good assembly has its' use. What Icynene did for us is cut the size of our HVAC system size in half. It reduced the number of AC run hours to 1/4.
Robert will rant back as to myself and foam and Icynene and using less than "code" R. Rant away. The homes work, I am in them all the time and the HVAC is off most of the time. I have never been in a home that an HVAC system runs so little an amount of time. And they are sized smaller than the installers wanted to size them at my insistence. I will not counter-post Robert. You all do not need an extended warming from that.
peace out. I suggest anyone that if you are trying any assembly that you learn about online to go to sites and learn in person. Talk to satisfied customers. Go to sites that are in the process of being built.
Cellulose is by far the greenest insulation. Icynene is a less green product but it is better at reducing energy demands then Martin is willing to admit.
unvented attic spaces
I am looking at a home in Santa Cruz, CA that is to be built. It has a rather cut up 4 in 12 truss roof with many areas of California framing. It is fairly complicated with fake rafter tails and a lot of odd framing details. The architect wants closed cell foam (R30) blown in under the roof sheathing with no ventilation. The roof is to be corrugated metal screwed directly down to the plywood sheeting. I am worried about condensation in areas where the foam may not be able to reach (California sections) among other things. Any helpful advice? Thanks, Alex Rockas
Response to AJ Builder
AJ,
Did you accidentally post your comment on the wrong page? I don't know what you're talking about. Why are responding to "Martin's rant that Icynene is selling nonsense. ... Icynene is a less green product but it is better at reducing energy demands then Martin is willing to admit."
I didn't attack Icynene insulation. For the record, Icynene spray foam is excellent at filling framing bays completely and does an excellent job of air sealing. For those reasons it always performs much better than fiberglass batts.
Response to Alex Rockas
Alex Rockas,
1. Please define "California framing."
2. Your architect's plan should perform very well, and shouldn't lead to any condensation problems, as long as the spray foam contractor can reach all areas of the roof sheathing. If some areas of the roof sheathing are not accessible to the spray foam contractor, you need to come up with a plan to insulate those areas.
Ice damming with OC foam
Good topic I will attempt below paste my post from a different thread.
I am constructing town homes
I am constructing town homes in Iowa where the zone is 6. The homes are slab on grade so it requires that all the HVAC to be place in the attic. The entire envelope of the home is done with OC foam. The underside of the roof has anywhere from 6" to 8" of foam and putting my HVAC in conditioned space. I am experiencing major snow melt and ice damming on these roofs when the are completely covered with snow with an outside air temp. at as low as 0 degrees.
I'm feeling I missed a major element in the equation by not sealing the underside of the foam.
I am still able too apply the sealer and am thinking about spraying it with Suppertherm or a good latex paint. But I do not want to trap the moisture at the roof sheathing or worse yet have it raining in the attic.
Sorry to be long winded
Thanks in advance for you comments
Why Does "Green" Require Hazmat Suits
The hazmat suit is for the over spray it sticks to anything and everything and is in the vapor until it is dry.
Response to Iowa Builder
Iowa Builder,
Your roof has at least three problems.
1. The biggest problem is that you installed less than the minimum code requirement for roof insulation in your climate zone. In Zone 6 (according to the 2006 IRC) you need to install a minimum of R-49 of ceiling or roof insulation. If you choose to install open-cell spray polyurethane foam, that means you need a little more than 13 inches of insulation.
You write that you have between 6 inches (R-22) and 8 inches (R-30) of insulation in your roof. That's not enough, as your ice damming problems indicate.
2. Your roof also has thermal bridging problems, since your rafters are uninsulated.
3. Finally, unless you sprayed the cured foam with vapor-retarder paint, your roof sheathing is at risk of accumulating moisture during the winter.
To learn more about solving ice dams, see Prevent Ice Dams With Air Sealing and Insulation.
It's not impossible that your home has an air leak -- for example, at the perimeter of the attic, where the roof foam should join up with your wall's air barrier. Any air leak would certainly contribute to an ice damming problem.
The solution is to beef up your roof insulation by adding rigid foam on top of the existing roof sheathing (and installing a new roof) or by adding insulation on the interior.
Thanks Martin
Thanks for the reply. The 6" would be cutting myself short but I included it in my range of thickness.
I do feel that the thermal bridging is on the trusses you can see that on the frost pattern. I feel comfortable about air leakage for I am getting better blower door test on the total envelope than other homes of the same size. I do have foam over the trusses just not enough I guess primarily where the webs meet the top cord. I will need to correct the problem from the under side they are 4 homes tied together and thats 128 squares of roof. One more thing. It only seems to be bad where there is a large volume of space below the roof and it all freezes at night. I feel I am right at the threshold and sealing will do the trick but don't want two wrongs. I have 86 more homes two do.
California Framing
Martin,
California framing (also called blind valley framing) is when you frame a portion of a roof over a roof that has already been sheeted. Here is a link to a page with a rough sketch. http://www.easyrafters.com/blindvalley.htm It will be hard to spray foam in those areas. Is it feasible to try and seal those spaces with spray? There will be nooks and crannies that easily could be missed. Also, roofers usually seal the top of the sheeting with Grace fire and ice shield before screwing down the metal roof. It is a very effective vapor barrier. Thanks for your help. Alex
Second response to Alex Rockas
Alex,
Determining whether a spray foam contractor can reach a space in order to install foam isn't rocket science; it's common sense. If a guy in a moon suit has enough room to get in there with his spray wand and move his spray wand in a smooth motion without bumping into anything, the work should be possible. When in doubt, talk to your spray foam contractor.
However, I think you already know the answer to your question. Spray foam is not a good solution when you want to spray the underside of roof sheathing in tight crawl-space areas of attics.
In your case, rigid foam on top of the roof sheathing makes more sense.
Iowa Builder
Do the roof trusses you are using have an "energy heel", are you getting full insulation out over the plate line? My experience in using energy heel trusses, insulation to code or above and venting the attic space at both the eave and ridge, prevents ice dams. My projects have been in locations with 8,000 to 9,500 heating degree days.
Iowa builder experiences differ from mine
Scratching my head as to his melting snow. I have had snow melt problems in the past mostly from their being very deep snow on a roof for more than a short period of time. The insulating effect of the deep snow is the issue along with it being on a building that is heated. We have plenty of "unheated" structures here that suffer not from melting snow but do collapse once in awhile due to weight. Lots of snow, rain and ice can take down any building in this area.
If I ask what is different between our two experiences, the number one difference I see is that I do not have the HVAC or any ducts in my attic spaces. That makes me think they may just be pushing a lot of BTUs into his roof that my homes aren't doing, especially since he is insulated much more than my 5-6 inches.
Martin?
Solutions for Iowa Builder type assemblies
Given that snow is on the roof and is melting and that the HVAC and ducts are in the attic space, vent. Your insulation contractor should have a method that works. If he does not, get another or contact Building Science Corporation and pay for solution that is backed by an insurance policy and contract.
Your project is certainly large enough to afford more expense to solve a possibly horrendous future liability.
Response to AJ Builder
AJ,
Iowa Builder has a conditioned attic with insulation installed between the roof rafters. Your suggested solution is: "vent."
Obviously, you can't vent a conditioned attic, so I assume you are suggesting that Iowa Builder install 2x4s on top of his existing roof sheathing and vent on top of the roof sheathing. That may help, but it's an expensive solution. If Iowa Builder ends up doing that, I hope he puts down some rigid foam under the 2x4s.
Different solutions for 4 of the 90 homes he is building
My suggestions above are mainly to do with his next 86 units. As for the existing units, since I have no issues with snow melt and he does, I think his safest fix for the 4 built units is to add venting above. He could try spraying foam on all the HVAC system too to try to stop the heat flow that I do not have at my homes. I sprayed my ducts in the cellars and love the outcome.
As to expense, yes... but if the melting is a real issue it must be dealt with. No way would I add foam and make a sandwich of any OSB board. Nope. Never ever ever ever. OSB waits for no one to rot. Junk. Has to be dry. Never sandwiched.
For the same price as adding foam sheeting he can spray more foam in the attics which like I said should encapsulate all his ducting and even blank sides of his HVAC. Open cell comes off easy if ever a unit needs to be pulled and replaced. Just leave appropriate areas insulated with wrap style insulation.
How to vent on top
To vent the first 4 units for the least cost I would go right over the shingles. Add 2x4s then Advantech Zip sheathing taped, then shingle it as per standard methods. The fascia would be lapped and doubled like we do now for thick roof assemblies. Vent added between fascias or choose one of many other set ups.
Done... problem gone, start building the next 86. Worry not.
Great feedback thanks
1st. Doug yes I have energy trusses and the exterior sheathing runs right too the deck and notched around the tails and foamed full.
2nd. Aj Yes snow is an insulator but does not melt itself so I feel Martin is on track with the thermal bridging it don't take much water on a roof to make a lot of ice.
A roof over a roof will not happen on a job of mine, the insulating contractor will correct it or remove his product.
This is my first experience in using foam. My last project of 26 duplexes and same style build only vented,R-8 on the HVAC and blown fiberglass. Drove thru there the other day and had a consistent 16 to 20 inches of snow on the roofs and not one icicle.
I wanna be green but I'm not slip sliding on a carbon footprint. ( Just scratching my head here)
Sorry was my previous post
Sorry was my previous post not anonymous
More on minimum R-values
Iowa Builder,
You wrote, "The insulating contractor will correct it or remove his product."
I think it's a good idea for you to hold the insulation contractor responsible for his work. In preparation for meeting with your contractor, I would suggest that you research your local code requirements for minimum ceiling R-values. It's probable that your contractor's spray-foam job doesn't meet minimum code requirements. If the installation doesn't meet code, this is a negotiating point in your favor.
Duct leakage to outside in homes with ducts in conditioned space
I thought it worthwhile to mention that moving duct work into conditioned space does not eliminate all duct leakage to outside. We have measured duct leakage to outside in numerous homes that have brought their ducts inside, and they still register a fair bit of leakage to outside. The reason for this is that the "conditioned" areas that the ducts now leak into are also connected to the outside. It is not difficult to imagine this happening in a drop ceiling chase that is imperfectly sealed. Now, this is certainly not as bad as having that air leak directly into an attic or crawlspace, because heat/cool is imparted to the indoor air before the leakage to outside occurs. But there is still an energy and air delivery problem. I'm sure it goes without saying on this website, that envelope tightness is essential in homes with duct work within the conditioned space. A tight envelope will ensure that duct leakage within conditioned space stays within that space. I add this comment because it is often thought that once ducts are in conditioned space, there is no longer any need to seal the ducts with tape/mastic. So, if you move duct work into conditioned space, be sure that the conditioned space and your ducts are well-sealed, otherwise you've accomplished little. Cheers.
Creating a conditioned attic without a HVAC unit in the attic?
Seems to me, the only reason to create a conditioned attic is to bring the HVAC system and ductwork into the thermal envelope of the home. If there is no HVAC in the attic - why not just air seal and insulate at the attic level - much easier and less expensive. I am not a HERS rater but I would think adding all of that volume and extra surface area to the thermal envelope would actually decrease the efficiency of the home. Even if you are a foam lover - can't you spray your foam at the ceiling level? Any HERS raters have an opinion on how this would affect the rating?
Bingo Danny
keeping the thermal envelope at the attic floor level does keep the exterior surface area lower...
and it will use less energy.
It will not change the HERS index because the HERS index will compare the house envelope to it's own geometric twin.
I think the best solution is to keep the envelope at the attic floor with airtight drywall and use more thickness of less expensive insulation.
Increasing the thickness and r-value will improve the HERS index
Response to Danny Kelly
Danny,
If you don't have any HVAC equipment or ductwork up there, and you don't intend to use your attic for living space, then it is clearly best to leave the insulation level on the attic floor. I agree with you and John Brooks: that makes air sealing easier and insulating cheaper.
It also makes it easier to spot and repair roof leaks, which is a big plus.
I've added a few sentences at the end of the blog to address these issues.
Thanks again for your comments.
Thanks Martin
Thanks for the clairifcation. I thought your article was clear by the way - was mainly responding/questioning AJ's post/practice and wondering if would afect HERS. John - thanks for the reply.
Thanks.
Construction details you alluded to
Martin you said "Even if you insulate between your rafters with an air-impermeable insulation like spray polyurethane foam, you may want to provide a ventilation channel under your roof sheathing. The main function of such a ventilation channel is to separate the roof sheathing from the foam; this facilitates future repairs of sheathing rot."
Do you have any articles with more discussion of that? Something with pictures is most welcome. I have been looking for a comprehensive discussion of how this might be done with low probability of trouble in a hot-humid climate.
Thank you -- Mark Johnson
Response to Mark Johnson
Mark Johnson,
No, I can't think of a specific article that discusses the concept.
However, people have been building site-built ventilation chutes in rafter bays for many years, so we aren't discussing a new technology or technique.
Although these ventilation chutes are usually used with fiberglass or cellulose insulation, there is no technical reason they can't also be used with spray polyurethane foam, as long as the panels are rigid enough not to collapse under the pressure of the expanding foam.
My spray company will do vented roof decks
My spray company, as I remember said they would spray right over the store bought foam vent chutes. For odd sized spacing one would have to make these fit well or make your own like has been posted many times on this site. He had no issues with venting by the way, though I really want to try an unvented non heated attic assembly and it is working beyond my expectations. Much better than detractors state it should. Open cell if a tiny bit of water gets to sheathing will let the sheathing dry. That is a fact. Much less chance of rot verses closed cell. If I went closed cell I would purchase pressure treated sheathing. It would be worth every penny.
Spray foam on the roof deck
I wrote an article that appeared in the JLC on Repairing a Rotting Roof June 2010 that dealt with a few shortcomings of the Icynene, when not installed considering all of the parameters. While this was not just an insulation problem but an indoor humidity problem as well, some things could have been done to alleviate this problem at the time of original construction.
Iowa Builder feel free to get in touch with me for additional perspective.
http://www.thebuildingconsultant.com
Making the Attic a Conditioned Space
Taking the building envelope to the roof is a good approach and will save energy - another approach is to use radiant coated deck sheathing, seal all ceiling attic penetrations and blow in R-60 insulation as it will cost less than spray foam and should give at least the same energy efficiency to the home.
What about thermal bridging in the ceiling joist
If I used 2x10s would I spray cellulose to the top of the joist and add an extra 2 inches? Would the 2 inches be enough to eliminate thermal bridging? What is the best barrier to use between the ceiling joists and the plywood for cellulose?
Response to A.K. Harrison
A.K.,
Q. "If I used 2x10s would I spray cellulose to the top of the joist and add an extra 2 inches? Would the 2 inches be enough to eliminate thermal bridging?"
A. If you are using spray cellulose, you would need to install framing members perpendicular to the rafters to address thermal bridging. Two inches would go a long ways toward addressing thermal bridging.
Q. "What is the best barrier to use between the ceiling joists and the plywood for cellulose?"
A. I'm not sure what you mean. If by "joist" you mean "rafter," and if by "barrier" you mean "ventilation chute material," the answer is "plywood, fiberboard, or rigid foam." If you mean something else entirely, please explain.
You need to cite your sources
Sorry for long post. I find this article a bit more informative than previous ones but the opening premise is flawed (IMHO) and hence doesn't seem worthy of much discussion. I find it curious that I asked a question touching on some of the topics in this article a few months back. The advice you guys gave seems to contradict what this article is saying today.
I have a problem with opening premise is that it costs "homeowners dearly". I'd like that quantified since I'm pretty sure that implementing the recommended upgrades would cost homeowners dearly.
I tend to rely on my experience so forgive me if I can't quote DOE or IRC. I have a house in the mid Atlantic with the very scourge of energy efficiency you refer to (leaky air handler in the dreaded uninsulated attic/crawlspace). Your definition of costing "dearly" is about $1000 extra to run the AC in the summer. I can't see how I can effectively insulate the attic (as you suggest) with an ROI of less than 7 years. So even though it's costing me dearly, I have better places to put my resources.
I have another house in New England the same energy scourge and I paid big bucks to spray foam the rafters. I calculate that I save about $0 (that's Zero) in AC costs. Maybe it's a hundred bucks a year, but with rising energy costs my ROI should be sometime before I expire (I'm in my late 40's).
Your delta T argument goes down the right path but is meaningless without duty cycle; ie. it may only be for short duration. This is why a frugal New Englander (or one good at math) would not insulate his attic to save cooling costs. Even my house near the Nation's Capital peaks at about 50% during the hottest 6 hours of the hottest days. Thank goodness it's oversized by today's standards because it's a much cheaper solution to solve the issues raised in your opening argument than the ones you proposed.
I hate to pick; but your thermal bridging argument only makes sense in the context of an opportunity cost or comparative analysis. Diminishing returns are valid issues that real people have to struggle with. Instead of glittering generalities you need to quantify how much energy you'll save jumping from R1.5 to R20 in contrast to R20 to R50? Then quantify the perceived comfort, up front and recurring costs, and ROI to substantiate your claim.
Thank you
Good points Gerard
Gerard,
I have to agree with the idea behind you points on the cost effectiveness of retroactively adding insulation to existing houses and also looking at the incremental savings of additional energy saving strategies in new construction (such as 2" of under slab insulation vs 16"). Regarding existing houses, a cost/benefit analysis definitely should to be performed, and unfortunately, the benefit is frequently not realized within the desired time frame (before an owner wants to sell the house for example).
The two "devil's advocate" points that I would like to mention are
1) The externalized costs of heating/cooling your house (the ambiguous environmental impacts of remote power generation and transmission) are not reflected in the price you pay for gas and electric. Therefore the cost benefit analysis may work out in more situations than we think.
2) In new construction the incremental costs of increased energy efficiency seem to intuitively be cost effective because the labor costs will have little change. I can't name a study off the top of my head, but I bet there is one out there from LBNL or Building America that backs this up. There is of course a tipping point where they are cost in-effective, but I don't know of any energy modeling software that can accurately help determine this point.
Response to Gerard Celentano
Gerard,
Thanks for your post; you bring up many important issues.
First of all, the point of my article is to provide advice to anyone who wants to create a conditioned attic, with the aim of making sure they do a good job. I never intended to encourage people to install insulation between the rafters of an existing home. That's why I wrote, "Creating a conditioned attic is a solution to a fundamental design flaw (locating ductwork or HVAC equipment outside of a home’s thermal envelope). But conditioned attics are not unalloyed blessings; they come with their own set of drawbacks."
According to your own estimates, this fundamental design flaw is costing you $1,000 a year. For you, the investment in insulation to create a conditioned attic isn't worth it, because the payback period is 7 years. That's your decision. Some other homeowners are very happy to make investments in their homes with a 7-year payback.
I am happy to stipulate that many energy-efficiency measures don't make much sense when analyzed in terms of payback. The main reason for these long payback periods is the fact that fossil fuels are quite cheap, and are sold at prices that don't include external costs like damage to the planet's climate.
rigid foam under rafters - fire protection required?
Thanks for the article. If you install the rigid foam under the rafters in an unoccupied/non living space attic, does the foam need to be covered with drywall?
Response to Troy Conover
Troy,
The answer to your question can be found in section R316.5.3 of the 2006 IRC. If the attic space is "entered only for purposes of repairs or maintenance," you can dispense with the requirement for a thermal barrier and instead install an ignition barrier (a less stringent option than a thermal barrier). But ignition barriers aren't nothing -- many people choose drywall, which must be at least 3/8 inch thick to qualify as an ignition barrier.
If you install Thermax foil-faced polyiso, some building inspectors will allow you to dispense with the requirement for an ignition barrier.
rigid between rafters
Thanks for thinking so much about insulation, i'm still new to thinking about this so please bear with me.
I live in the Northwest, am planning to gradually finish a 600 sq foot attic space with cathedral ceilings, new roof put on about 5 years ago, before we moved in. my rafters are only 2x4 and i don't want to lose much living space. My tentative plan has been to put 2-2.5 in. polyiso between and 2 in. under rafters for now. This won't get us to code but would be better than what we have now. now i've been thinking that someday the roof will need to be replaced and i could add rigid on top.
Which brings me to my questions:
if "ventilated rafter bays are incompatible with rigid foam insulation installed on top of the roof sheathing" does this approach make sense?
and since poly-iso is faced, can i use 2 layers on top of each other and if so do i create a sandwich with the faced surfaces or layer them with facing to the interior? thanks
Response to Joell Solan
Joell,
Don't bother to include ventilation. Instead, fill the 3.5 inch rafter bays with 3.5 inches of polysio (one 2-inch layer, and one 1.5-inch layer). Seal all gaps with canned spray foam. Then install a continuous layer of 2-inch polyiso under the rafters to stop thermal bridging.
Using several layers of foil-faced foam is fine -- there is no problem with making a sandwich like this, except that it is slow, fussy work.
Foil Faced Foam for Venting Channels
In a 2x12 rafter attic, can I use foil faced foam (Dow Thermax) to create the 2" air channels in the rafter bays and then use fiberglass batt in the bays followed by sheetrock with latex paint. Will the low perm of the thermax cause any problems at this location. Also, shoud I add some rigid foam such as dow blue board below the rafters for a thermal break against bridging: say 1" foam?
Response to Gary Steinfeld
Gary,
Yes, you can use rigid foam (for example, Thermax) to create a ventilation channel.
If you have 2x12s with a 2-inch ventilation channel, 1 inch of Thermax will give you an R-value of R-6.5, and the remaining 8 1/4 inches of fiberglass will give you about R-30.5. So you end up with R-37. I don't know if that is enough to meet minimum code requirements; it depends on your climate zone and the local code.
Yes, you can cut down on thermal bridging through the studs by adding a continuous layer of rigid foam insulation under the rafters. I don't think this type of assembly will have moisture problems.
Kraft Free Insulation
Martin
My intention was to use batt insulation with out kraft paper. Is that the correct detail?
Response to Gary Steinfeld
Gary,
I don't know your climate, your geographical location, or your local code requirements, so I can't answer your question.
Your detail has to satisfy your local code official, so you can call your local building office for an answer. It rarely matters from a building science perspective whether your fiberglass batts have kraft facing or no kraft facing, as long as you pay attention to air sealing.
Here's more information on vapor retarders: Vapor Retarders and Vapor Barriers.
Venting Cathedral Ceiling
Like the previous poster I am thinking of using foil faced 1 inch polyiso for a site built ventilation baffle for 12 inch deep rafters, creating a 2 inch gap. Then spray foam underneath. Should I be worried about vapor condensing on interior foil so that the foam absorbs moisture like a sponge? Is one type of foam better than a another? The house is in climate zone 4c in Northern Ca. Thanks for you time.
Response to David Head
David,
Q. "Should I be worried about vapor condensing on interior foil so that the foam absorbs moisture like a sponge?"
A. No, for three reasons: (a) The foil layer, even if it is wet, prevents the water from reaching the rigid foam; (b) The foil will be warm (since it is on the interior side of the foam) and will therefore never be cold enough to become a condensing surface; (c) In most cases, the spray foam will stop moisture transfer from the interior to the foil.
Q. "Is one type of foam better than a another?"
A. Closed-cell spray foam has a higher R-value per inch and is less vapor-permeable than open-cell spray foam; for those two reasons, I would say that closed-cell foam is better than open-cell foam in this application. But either one will work.
For more information on this topic, see How to Build an Insulated Cathedral Ceiling.
Cathedral Ceiling Venting
Thank You very much for you quick reply, you have relieved some of my anxiety of this project. I take that "No, for three reasons: (a) The foil layer, even if it is wet, prevents the water from reaching the rigid foam" also means that water vapor can not entrap itself inside the spray foam and lead to rotting or mold growth on the rafter? Does the vapor just move to dissipate back into the conditioned space?
Sorry for the basic questions, I just do not want to make any mistakes and understand the building science.
Response to David Head
David,
During the winter, the indoor air is warm and humid. The outdoor air is cold and dry.
The moisture held in the air indoors isn't supposed to go anywhere. It is supposed to stay put. You don't want to have any air or water vapor migrating through your building assemblies. That's why you have an air barrier -- to keep the indoor air in, and the outdoor air out.
Q. "Can water vapor entrap itself inside the spray foam?"
A. No. Closed-cell spray foam is vapor-impermeable. While open-cell foam is vapor-permeable, any water vapor inside the foam isn't trapped. It's free to come and go. Water vapor doesn't hurt spray foam.
Q. "Does the vapor just move to dissipate back into the conditioned space?"
A. Are you talking about outdoor water vapor during hot, humid weather in the summer? If you are, the water vapor should stay outdoors. You can make sure that happens by including an air barrier in your ceiling assembly -- in your case, that would be the foil-faced polyiso. The foil is also a vapor barrier.
If you are talking about water vapor that is inside the house during the winter, the idea is to keep it inside, not allow it to flow through your walls and ceilings.
Creating a Conditioned Attic
Mr. Holladay,
I am writing to you in hopes you that you may possibly add some clarity to a confusing situation for me. While renovating my house a couple of years back I used this sight for a lot of the recommendations in regard to insulating my house. I am in Westchester NY about a mile from the coast zone 5. The house is a wood frame ranch with a pitch of 6/12 with 2x8 rafters and new ¾ in sheathing. My main concern is the attic and roof insulation. Unfortunately, I have Hvac equipment in the attic and I might finish the attic in the future too. There is floor decking in the attic with R-30 bat between the ceiling of the first floor and the attic floor. The sheet rock ceilings were made air tight or as close as possible. I have a sealed door to the attic. My question is this, as per a number of articles and readings (one of which was “Five questions to consider before insulating a sloped roof”) I decided that I would have the contractor create an on-sight baffle to vent the underside of the roof sheathing by using 1x1 and 1” xps foam board to create a continuous channel from soffit vent to ridge pole vent. I then intended to either flash foam with closed-cell and then another type of insulation after that or fill the rest of the 2x8 with closed-cell. Either way I believe I would be short the required code value for insulation (R-38 zone 5?), but thought I would be close and the tighter envelope would still be better over all situation. The problem I have is that all of the South/East facing side of the roof has the 1x1 baffles installed, the other side was never finished, but looking to complete everything now. The info in the last 2 or 3 years has seemed to change (Dr. Joseph Lstiburek article about roof venting). My concern now is that the 1x1 channel with foam board is not large enough even though the IRC says 1” is the minimum. I believed from what I read that 1” would be fine especially since I wanted to give up the least amount of R-value as possible while doing it. The idea was minimum amount of R- value lost, no foam against the deck, and the attic included in the envelope. Now I’m reading all these negative things about potential for mold and other bad things if the channel under the sheathing is less than 2”. So do I spray over the existing baffles and cross my fingers or rip out the baffles and spray against the sheathing? I could try to take the foam board down and increase the channel size up to 1.5 “or 2” , but I would lose some more R-value? What would you do at this point. Any information would be greatly appreciated. Forgot to mention that I am having that side of the roof spec’d out for PV array, if that makes any difference?
Thank you,
Response to Eric Schroeder
Eric,
1. I wouldn't worry about whether or not your 1-inch deep air channel is adequate. It is. A great many attics have smaller air gaps than the one you have provided (for example, those that use Styrofoam Proper-Vents). You have done an above-average job.
2. The most important way to ensure that there are no moisture problems in your ceiling assembly is to pay attention to airtightness. Because you plan to use closed-cell spray foam, you are unlikely to have problems on this score, as long as the spray foam installer pays attention to maintaining air barrier continuity near the soffits, where the air barrier in the sloped roof assembly meets the air barrier in the wall assembly. Since you are worried on this issue, you can always hire a contractor with a blower door to depressurize your attic when the work is done; that way you can check for air leaks and fix them.
3. If you fill the rafter bays with closed-cell foam, you'll end up close to R-38. However, most closed-cell spray foam contractors don't fill framing bays (because the foam is dense and hard to trim when it bubbles past the plane of the framing) -- the framing bays end up "almost full." You might want to consider adding a layer of rigid foam on the interior side of your rafters, to address thermal bridging and to beef up the assembly's R-value.
Roof Assembly without sheathing
This seems to be a common theme with my home - I asked a question in the 'Cut and Cobble' article. I need to create a conditioned attic due to the location of the air handler and ductwork. It would also be a great help to use it as storage as it's an old home with limited closets, etc. I'm located in Climate Zone 4. The home has a metal roof on perlins. I cannot insulate from the exterior. The roof has no ventilation (no soffit vents/ridge vent) except from holes from those pesky squirrels.
My hope was to use fiberglass between the rafters and foil-faced foam on the underside. I don't think I would need to worry about wind-washing in the roof assembly.
Any suggestions on how to properly condition this type of attic would be greatly appreciated.
Thanks!
Response to Chris Thomas
Chris,
Everything you need to know is explained in this article: How to Build an Insulated Cathedral Ceiling.
Here are the steps for the type of roof you describe:
1. The air between the purlins (under the metal roofing) provide enough ventilation.
2. The first step is to create an air barrier at the top of each rafter bay. You can either install rectangles of plywood, OSB, or thin XPS or EPS foam. No matter which product you choose, the rectangles have to be air sealed at the perimeter with caulk, canned spray foam, or a high-quality construction tape.
3. You can insulate the rafter bays with fiberglass batts, blown-in cellulose, mineral wool, or spray foam. If the rafter bays aren't deep enough for you to get the minimum R-value of insulation required for your climate zone, you may have to extend the rafters inward (make them deeper) with scabbed framing members.
4. It's important to install an air barrier on the interior of your roof assembly. The simplest air barrier at this location is gypsum drywall.
New Roof & Venting Options
I'm currently in the process of working with a roofing contractor for a new roof and thus looking into the ventilation options. Here are the details:
- We would like to use stone coated steel shingles - for a variety of reasons
- We currently only have 2 gable vents for attic ventilation and a large open attic that we would eventually like to convert to living space
- We have no soffit or ridge vents and the eaves are stucco
- We have cathedral ceilings in about 1/3 of the house, and while the roof is not extremely complex, it does have some hips and valleys, and 2 eyebrows.
- We have recessed can lights everywhere - and in the cathedral ceilings
- I'm pretty sure there's some sort of insulation in between the cathedral ceiling and the roof - most likely fiberglass
- Los Angeles area
- Built in 1975 - we just bought the house last year
Since the metal roof would need adequate ventilation, and venting the attic would not easily allow us to convert it later, in addition to the area above the cathedral ceilings needing to be vented (for the metal), we are looking at alternate options to vent the roof. I am aware that adding recessed lighting in an insulated ceiling is completely backwards. The previous owner added the cans and we'd like to keep them - especially if using one of the two options below negates need for the cathedral ceilings to be insulated.
So it seems we have two options:
1. We can use the flat metal shingle we like best (they are only a direct to deck install) and add a second roof deck over the existing deck with battens in between to create an air space that we vent. The existing roof sheathing would have a layer of SharkSkin underlayment and radiant barrier. The new sheathing (2nd layer) would just have an underlayment.
2. Create a counter batten system with a raised metal shingle and radiant barrier / SharkSkin.
Both options would allow us to convert the attic and should cut down on a considerable amount of heat transfer into the attic. There are a few ways we can vent the roof near the eaves with venting options from cor-a-vent. We will also be adding 3 ridge vents. The shape of the house / roof is basically a U, though upside down and with hard corners. There's 3 parts to the roof, the largest which goes left to right and is the horizontal section of the U shape. The other 2 parts are the vertical extensions off the U shape and intersect the longer section. There's a space in between the vertical sections (our front walk). Then there are 2 small eyebrows, one on each of the extensions that faces out toward the street. I realize even with the above sheathing venting it will be difficult to completely vent the roof.
Since we would much prefer to use the flat shingle, we'd be looking to add the second roof deck. The issue then becomes the added weight of the second roof deck (and the solar system we plan on adding ~820 lbs), and this being earthquake country, the lighter the roof the better. This is beyond the scope of your article but I mention it only to illustrate that we are having difficulty deciding which route to take and maybe you can offer an opinion unrelated to the weight issue that will steer us in one direction over another.
I apologize for such a long comment - but I'm finding it very difficult to find anyone who really seems to understand all this, and would very much appreciate any insights and advice you might have.
Thanks for the great article.
Response to Joe G
Joe,
It seems to me that you are too concerned about venting, and not concerned enough about R-value.
For more on venting, and why it isn't that important, see All About Attic Venting.
I have never heard that metal roofing needs a ventilation channel. Is this a requirement of the roofing manufacturer? Here in Vermont, many builders install metal roofing over unvented roof assemblies.
It sounds like your roof assembly is underinsulated, especially in the cathedral ceilings with recessed cans. The obvious solution (if you are reroofing) is to install a thick layer of rigid foam above your existing roof sheathing. For more information on this option, see How to Build an Insulated Cathedral Ceiling.
If you want to install added insulation and a new vent channel, one possible solution is to install vented nailbase panels like the Cool-Vent product from Hunter Panel.
New Roof & Venting Options
Martin,
Thanks for the response.
I should add by the way that - you guessed it - our ducting is all in our attic.
Yes, the metal manufacturer specifies that there should be adequate ventilation - not necessary directly below the metal shingles but at least in the attic from soffit to ridge. The company is Metro Roof Products. I'm assuming this is to prevent condensation issues.
As much as I would love to use a rigid foam like Polyiso, I have many reservations due the inclusion of known carcinogenic flame retardants like TCPP and the fact that Pima.org has a newly published / revised paper from January 2014 - updated in March (http://www.polyiso.org/resource/resmgr/Technical_Bulletins/PIMA_StewardPapr_updateMar20.pdf) which essentially states that TCPP is completely and utterly safe all around, based on a 2008 study. It goes on to quote the agency study saying there is no need for further testing as a result of the 2008 tests. There have been numerous studies as of late classifying TCPP as carcinogenic and it is listed on CA's Prop 65. The fact that Pima recently published this brief and the way the information is laid out sounds like propaganda and I just can't get behind such a product or organization.
If we vent the roof deck or added insulation above the deck -- 1. Would it also be necessary or recommended to remove the existing insulation (if there is any) from the cathedral ceilings? We have plenty of insulation in the rest of the attic floor and walls between the cathedral ceilings and attic - which would most likely be moved to the ceiling if we converted the attic.
I read your article on mineral insulation. Owens Corning Thermafiber is a mineral wool / rock wool product I just found that seems fairly safe. Like the Roxul product it seems to use a formaldehyde binder, according to their FAQ ... 12 ppb (http://www.thermafiber.com/TechnicalLibrary/FAQs#g3)
I've been looking for the study Owens Corning was supposedly doing on Thermafiber UltraBatt, mentioned here: https://www.greenbuildingadvisor.com/blogs/dept/energy-solutions/better-national-distribution-mineral-wool-batts, and the formaldehyde levels but it doesn't seem like it's been released yet. Thermafiber has many different products and some of the MSDS list Phenolic Resin with no mention of formaldehyde, while others list mineral oil where the Phenolic Resin was listed, and then the MSDS for the SoundZero product lists Formaldehyde. I can't even find an MSDS for UltraBatt: http://www.thermafiber.com/TechnicalLibrary/MSDSCompliance
It says Thermafiber can be formed into boards. 2. Would you recommended something like Thermafiber or Roxul for roof insulation? It looks like you can even get the Thermafiber with a vapor retarding foil facing.
I should add that when we convert the attic we would of course insulate the ceilings and remove the attic floor insulation. Thus, we'd have a vented roof and insulated ceilings. Of course the Cathedral Ceilings would still be an issue. I wonder if it might make more sense to address the Cathedral Ceilings instead of adding insulation above the roof sheathing for the entire roof, when we have rafters in which we can insulate below - and they cover more of the house. I'm assuming there's no real way to insulated the cathedral ceilings under the roof sheathing, but above the drywall, WITH the recessed lighting. And from your article on that, it seems like the air gaps around the cans could cause some moisture issues on the insulation in there etc., especially since there's no venting.
Response to Joe G
Joe,
Q. "[If rigid foam or mineral wool were installed above the roof sheathing,] would it also be necessary or recommended to remove the existing insulation (if there is any) from the cathedral ceilings?"
A. No.
Q. "Would you recommended something like Thermafiber or Roxul for roof insulation?"
A. According to my understanding, mineral wool panels are only installed above roof sheathing on low-slope or flat roofs. Use of this product on a steep-slope roof would be considered experimental.
Conditioned Attic Needs a Little Air
Hello, posted on here before about my 1800 sqft attic in Nebraska that was transitioned from a blown cellouse vented attic, to an icynene open-cell unvented space. Initially humidity was very high during sunny afternoons. After posting on here for advise, and speaking with the insulation company, the company came back filled gaps, made the insulation thicker, and used a spray on vapor barrier. They even paid for a local energy inspector to check it afterward. The energy inspector thought the work was really well done. Since then in the spring and fall in the late afternoon when the HVAC is off and the windows of the house are closed it can reach 80% RH at the very peak point of the attic which is 8ft to central peak from atttic floor. However as the sun sets the humidity goes back down to about 55% RH at night. If the windows are open in the house or the HVAC is on its lower, and in the winter it stays at 51% all day. The energy adviser recommended two options for the afternoon humidity and to provide a bit of air to the space. Option one was just a small ventilation feed from the house into the attic. Option two was placing a bathroom exhaust fan in the space that vents outside, and has a humidstat switch that turns it on when needed. The feed from the house would be difficult since the duct work is in the basement. What are your thoughts on the bathroom exhaust fan? Should I look for HRV or CRV system?
Response to Nick Schuler
Nick,
The phenomenon you are describing -- high RH in an unvented conditioned attic after open-cell spray foam was installed on the underside of the roof sheathing -- is common. That's why my article notes, "Recent research suggests that open-cell spray foam may be risky in all climate zones, so the safest spray foam insulation to use is closed-cell spray foam. For more information, see Open-Cell Spray Foam and Damp Roof Sheathing."
In that article, I noted, "If you have an unvented conditioned attic with high humidity problems, the best solution is to install a supply-air register connected to your forced-air HVAC system in the attic (and in some cases, a return air grille as well). If the attic is heated in the winter and air conditioned during the summer, humidity problems should disappear."
I hope this solution works for you. Good luck.
Try a tiny ventilation fan running continuously.
A Panasonic FV-05-11VK1 set to 50cfm draws 3.2 watts. If you set one up to draw from the attic and exhaust into the conditioned space, with a return grill to the attic from some other place the peaks in attic humidity will be managed by the air conditioning.
If 50cfm doesn't quite do it during the summer it can be cranked up a bit. At 80cfm it draws 5.4 watts, at 110 cfm it draws 9.8 watts.
It's available at some box stores for about $135. You'll have to buy a small exhaust grille/diffuser, a tiny amount of 4" round duct, and a return path grill too, but for under $200 in hardware plus some electrician work you'd be there.
Rigid Foam Board Under the Rafter
I am in a HOT climate near the Gulf Coast in Texas with the air conditioning unit is in the attic. My thought is to add 2 inch foil wrapped foam board under the rafters. The space between the rafter would be left open to allow air to flow from the soffit vent to the top roof vent. I would seal the air space between the rafter from the airspace in the attic. I have NO combustion in the attic from appliances (all electric). Also plan to leave the existing insulation on the ceiling below. This will create a space that is less than the current 150 F and over in the summer to something cooler but not as cool as the conditioned space under the insulated sheet rock ceiling. My question if you get comfortable with these plans is which ridged board material is best for this application. Keep in mind freezing weather is not a major factor in this climate. Part of the driver here is comfort, when the AC starts the first air out is hot, not cooler than the existing house. And to be clear i have installed the newest insulated duct work available however the broad side of the roof faces west and catches the major afternoon heat from the sun. And suggestions are welcome to improve the heat.
Response to Ben Reese
Ben,
The best type of rigid foam to use for your project would be foil-faced polyisocyanurate. Make sure that you seal the polyiso seams with a quality tape (for example, housewrap tape).
The approach you describe can't hurt -- R-12 insulation is better than nothing. But clearly, R-12 insulation is a far cry from code-minimum insulation.
How deep are the rafters? (@ Ben Reese)
If you have 2x6 rafters you can install R13-15 batts between them, and add the 2" polyiso below to improve the performance. (Don't go with lower-density R11s, since at low density the translucency of fiberglass to infra red radiation renders it pretty useless during the cooling season.) If you have deeper rafters than that you can go even higher. If the roof pitch is ~3:12 or lower you'll want at least 2" of air space between the fiber and the roof deck, but at higher pitches it can be the code-min 1" gap.
Foil faced polyiso is fairly fire-safe relative to polystyrene foams, but you may be required to use a fire-rated polyiso (eg Dow Thermax) if leaving it uncovered on the interior. Local codes vary.
If you're going to skip the batts, you get a modest performance boost out of low-E "radiant barrier" paint with an IR emittance less than 0.25 on the underside of the roof deck. (see: http://www.rimainternational.org/index.php/technical/ircc/ ) If you're installing the batts that benefit is pretty small, but if it's facing a shiny foil facer it's real enough. Not all low-E paint is the same- be sure to look up the specifications for both emittance and coverage. Mop-on exterior coatings are typically higher emittance and only cover a few hundred square feet per 5 gallon bucket, and they're pricey. A 5 gallon bucket of the better class low-E under-deck paint starts at about $300 and covers ~2000 square feet, which is 15 cents per square foot. But if you don't have 2000 square feet of roof deck to paint it's higher on a per-square foot basis, and you're stuck with the leftover paint to dispose of.
Bang per buck, R13 batts run 35-35 cents per square foot at box store pricing, but you don't need to buy 2000 square feet at a time, and the performance boost is higher.
Conditioned Attic - Hot Climate
Thanks for the responses, first the rafters are 2x6. I will look for foil faced polyisocyanurate board. And while this will this is less than code the insulation on top of the ceiling is 21 inches and meet code for the enclosed space. Again i am really just trying to make the AC system more comfortable due to all the long runs of ducting in a space that is over 160F today. My concern on adding insulation between the rafters is the potential to block adequate air flow under the roof deck. My shingles are fairly old and would prefer to no do anything to reduce the life of the shingles. Again I could be all wrong on my assumption so any help would be most appreciated.
Mini split system for conditioned attic renovation?
Thank you for the great articles, Martin. I'm working on an attic renovation project in Chicago where we are converting a previously unfinished and uninsulated attic into a living space with 2 bedrooms and 1 bathroom. The existing space has 8 passive roof vents installed between rafters close to the ridge and the roof does not have any eaves. After reading this and several other of your articles I have a couple questions that I'm hoping you can help me with. For context, the existing rafters are 2x6's and the gable ends are double wythe brick walls that have been inspected, are not good candidates to insulate, and are therefore being left exposed. Because there are no eaves and the roof has multiple valleys, we are spraying 3" of closed cell spray foam against the existing sheathing to control condensation, compressing a 3.5" batt into the rest of the rafter cavity, and then capping the interior of the rafters with a continuous 1" rigid insulation board. The final interior finish will be painted drywall. It would be difficult to extend the existing ductwork for the forced air furnace and AC into the attic (but we could do it if it made the most sense) and we are therefore considering a mini split system with 2 zones for dedicated heating and cooling for the attic. In total the attic is roughly 900 sq ft and the larger bedroom will be 400 sq ft when done.
My first questions / concerns with this plan are regarding humidity and fresh air:
I have not yet personally installed or lived with a mini split system but I have read that it should be able to alleviate any excess humidity that collects in the attic space during the summer. Is that accurate? Would another system be more appropriate? If we are not planning to extend the ducts or add additional ventilation, should we be concerned about a lack of fresh air in the bedrooms? The stairs will be completely open to below but one bedroom is 30' away and we don't have headroom to add a ceiling fan for additional air circulation. It's such a small space that perhaps it won't be an issue, but I'd hate to have the space feel stale when it's complete.
My second question is concerning the existing passive roof vents that we are planning to remove in order to turn the roof into an compact unvented assembly with the close cell foam as I describe above. Should we be concerned that this plan could lead to interior moisture problems that were not present before when the roof was so freely "breathing"? There aren't any signs of moisture in the basement or existing walls, but Chicago can be quite humid and we would need to remove all of the passive vents in order to make the space livable as an unvented roof is really our only option.
I really appreciate your insight.
Thank you.
Dan
Response to Dan H
Dan,
Your proposed insulation will total about R-31, which is probably less than minimum code requirements. That's not enough to invalidate your plans -- just something you should know.
Sealing the roof vents (as part of the work to convert a vented unconditioned attic into an unvented conditioned attic) will not put your roof sheathing at risk. As long as your roofing and roof flashing are in good shape, your roof sheathing will be fine. Eventually, your roof will leak -- but that happens to all roofs.
The indoor air in your attic shouldn't be any worse than the indoor air elsewhere in your house. During the summer, your minisplits will cool and dehumidify the indoor air.
The question on ventilation is hard to answer. Whether or not the top floor of your home feels stuffy depends on several factors, including (a) whether you have air leaks on your gable walls or near your windows, (b) whether you like to open your windows a crack when you sleep, (c) whether or not your house has a mechanical ventilation system for the lower floors, and (d) the quality of the indoor air on the lower floors.
If your house is tight and poorly ventilated, the solution is to install a ventilation system. If your top floor is stuffy, a good solution might be to install two Lunos fans. For more information, see Designing a Good Ventilation System.
R-value followup question
Thank you for the quick response, Martin.
I'm curious why the R-value would be 31? I was estimating 36.5 with the following:
3 x 6.5 for the closed cell = R19.5
A 3.5" R15 compressed to 2.5" = R11 (per owens corning)
1" polyiso board = R6
Am I making a mistake in that calculation?
We will most likely need to sit down with a code official on this issue in order to get our permits. The Chicago code has an exception where up to 500 sq ft can be less than the required R-49 (down to R-30) if existing conditions prohibit more insulation. And, the home owners really don't want to use more closed cell spray foam than we have to. We are maintaining as much of the original roof as possible which is why head room is at a premium and we don't have any space to furr down to add more insulation. The 1" board below the rafters is already cutting it close. The shingles are only a couple years old or else I would encourage them to insulate from the exterior but that would add a huge cost and destroy the budget.
Response to Dan H
Dan,
Your R-value estimate may be more accurate than mine. You wrote "rigid foam" in your original post, so I assumed R-5 for the (unspecified) material -- polyiso probably would be R-6.
I assumed R-6.25 per inch for the spray foam -- but R-6.5 is possible.
I assumed R-9.5 for the 2 1/2 inches of compressed fiberglass -- probably more pessimistic than necessary, but compressed fiberglass is rarely perfectly installed.
Then I made an addition error, reporting R-31 when I should have reported R-33. (Sorry.)
So the ultimate R-value will likely be somewhere in the range of R-33 (my low-end estimate) and R-36.5 (your high-end estimate). That's OK for a retrofit job. Just so your eyes are open -- it's not R-49, but it doesn't have to be.
Martin,
First off wanted to thank you for this wealth of information, it is great! Can you clarify a couple of the items you discussed?
1. “Remember: ventilated rafter bays are incompatible with rigid foam insulation installed on top of the roof sheathing. If you want to reduce thermal bridging through the rafters of a ventilated roof, you’ll have to install rigid foam insulation under your rafters.”
Question: I am in a hot-humid climate (Austin,TX) and want to use rigid foam insulation on top of the roof sheathing of an unvented attic and use a fibrous insulation like fiberglass or cellulose between the rafters. Do you mean there cannot be an air gap between the bottom of the roof sheathing and the fibrous insulation used inside the attic or do you mean that the attic itself cannot be ventilated (i.e. it is only recommended to install rigid foam insulation on top of the roof sheathing if you have a sealed or unvented attic)
2. “You’ve protected any exposed foam with a thermal barrier like drywall.”
Question: Does foam need to be protected when installed under the rafters? Can you leave 2-in. thick foil-faced polyisocyanurate exposed in the attic in a hot humid climate or does it require a thermal barrier?
3. “If you have insulated the roof assembly with open-cell foam and you live in a humid climate, however, there is increasing evidence that you probably need to install a supply register and a return grille in your attic in order to keep humidity levels low enough to avoid damp roof sheathing. For more information on this issue, see Open-Cell Spray Foam and Damp Roof Sheathing.”
Question: What about when you install a fibrous insulation like fiberglass or cellulose between your rafters? Do you still recommend installing a supply register and return grill in your attic?
4. “A radical approach: Abandoning attic ductwork. If your house has a vented unconditioned attic that includes ductwork, and you are thinking of converting the attic into a conditioned attic, you may be surprised at the high cost of the required work. Creating a conditioned attic is expensive. In light of the high cost of the work, it’s worth considering a radical option: abandoning the existing forced-air system. In some cases, the cost of installing one or two ductless minisplits is less than the cost of creating a conditioned attic. Moreover, the minisplits will perform at a much higher efficiency than a conventional forced-air system with attic ductwork”
Question: When you have an unconditioned attic how do you deal with mechanical ventilation and other vents that typically go through the roof? Do you route all vents including mechanical ones through the walls of the home?
Thanks,
Steve,
Q. " I ... want to use rigid foam insulation on top of the roof sheathing of an unvented attic and use a fibrous insulation like fiberglass or cellulose between the rafters. Do you mean there cannot be an air gap between the bottom of the roof sheathing and the fibrous insulation used inside the attic?"
A. Yes.
Q. "Or do you mean that the attic itself cannot be ventilated (i.e. it is only recommended to install rigid foam insulation on top of the roof sheathing if you have a sealed or unvented attic)?"
A. If you are installing insulation along the sloping roofline, then the attic must be inside the home's conditioned space (and therefore the attic must be unvented).
Q. "Does foam need to be protected when installed under the rafters? Can you leave 2-in. thick foil-faced polyisocyanurate exposed in the attic in a hot humid climate or does it require a thermal barrier?"
A. Different code officials have different interpretations on this issue. To get a relevant answer, you should contact your local code official.
Q. "What about when you install a fibrous insulation like fiberglass or cellulose between your rafters? Do you still recommend installing a supply register and return grill in your attic?"
A. If you are installing fiberglass or cellulose between your rafters, you will need either (a) a ventilation channel between the top of your insulation and the underside of the roof sheathing, or (b) an adequately thick layer of rigid foam on the exterior side of the roof sheathing, or (c) an adequately thick layer of closed-cell spray foam on the underside of the roof sheathing. Assuming that you have followed one of these methods, then you don't necessarily need a supply air register or a return-air grille in your attic.
Q. "When you have an unconditioned attic, how do you deal with mechanical ventilation and other vents that typically go through the roof?"
A. They can still be routed through the roof as before.
Q. "Do you route all vents including mechanical ones through the walls of the home?"
A. No, that's not usually necessary.
Hi Martin,
Thanks for this helpful article. After reading it and others on GBA and in Fine Homebuilding, we still have some questions and need some advice on the best approach to insulating the conditioned attic, basement, and some walls of our two and a half story 1944 brick and block colonial in zone 4a (see last picture).
We’re renovating the basement, garage, kitchen, master bedroom, and finished attic. The walls and ceilings are plaster over one-inch furring strips with air space between the backer board and the concrete block (see fourth picture for a view of the furring strips on the block wall with the plaster removed in our future kitchen). The attic had two very thin layers of mineral wool insulation between the two by eight rafters (see first picture) with a large air gap from the insulation to the roof decking. The decking is one by five boards laid diagonally with a quarter inch of space between each board. There is a thin layer of asphalt paper on top of the decking and beneath the original slate roof. The slate roof has been inspected by a slate expert and is in very good shape. There are no soffits, only very thin and inconsistent air gaps between the top plates of the walls and bottoms of the rafters. There are gable vents built into the brick side walls at each end of the room near the peak of the roof (currently plugged with rigid foam in second picture).
The master bedroom is directly above the garage and is typically colder than much of the rest of the house in the winter. The ceiling joists in the garage had two layers of mineral wool insulation, similar to the attic. The garage doors have foam core insulation, but the rest of the garage is not insulated. The basement block walls (third picture) had wood paneling over furring strips and have never been insulated.
We have a high-efficiency heat pump in the knee wall of the attic that conditions the attic and the bedrooms on the floor below. The ductwork runs in a horseshoe down one side of the knee wall, across one side wall, and then down the other side of the knee wall. We have a high-efficiency gas furnace in the basement that conditions the basement and main floor.
We have done as much research as we can and think our major constraints are the slate roof, lack of roof venting, and seven and a half inch rafter bays. The slate roof experts we have consulted have told us we need to preserve air space beneath the roof decking. Our understanding is that the city requires us to fill all of the available joist space to pass inspection. However, we want to get the best performance we can within these constraints and without obliterating our budget. Whenever possible, for cost savings and learning, we'd like to do the projects ourselves.
We think our options are closed cell spray foam, rigid foam, fiberglass batts, or rockwool batts. For the attic and garage ceiling, we think the best option might be to furr down the rafters an inch and install R-30 rockwool batts flush with the inside edge of the rafters. This would leave about an inch of airgap to the decking without requiring us to install baffles. We also like this option because we can do it ourselves and it does not involve some of the initial odor and cost concerns associated with spray foam, and rockwool resists moisture and wind. We could also layer additional rockwool below the rafters in the knee walls and beneath the ridge. Is this a good approach? If so, we could use advice on: 1) whether to leave open the gable vents and small gaps above the top plate to allow the decking to dry if it gets wet or to seal and insulate over the gaps; 2) whether to/what kind of air barrier/permeable membrane to use on the interior facing part of the insulation; and 3) whether we need to remove (and then later reinstall) the knee wall supports to run the membrane continuously on the rafters from the ridge/ceiling down to where they meet the top plates, or if there is another way to work around the knee wall framing.
For the basement and interior walls, we are not sure whether to use rigid foam alone, rigid foam with rockwool or fiberglass, or to go with closed cell spray foam. We also are not sure what sort of air barrier and/or moisture barrier to use, particularly since there will be a number of walls that will not get insulation since we are only taking down the plaster walls in the areas where we are doing major renovations. Since there will not be consistent insulation and air and/or moisture barrier across all of the walls, we want to make sure we don’t create problem areas behind the sections of new drywall. After reading your article on insulating old brick buildings, we're still a little confused about whether all of the conclusions and recommendations apply equally to walls that have a cement block interior wythe that has intermittent interlocking courses with the exterior brick wythe.
We would appreciate your expert advice. Thank you!
Kyle
Kyle,
In general, your questions belong elsewhere -- on our Q&A page. Here is the link: Q&A page.
An important hint: Ask one question at a time. That way, you're more likely to get an answer. You might also spend more time with GBA's "Search" function -- that way, you can read articles on most of the topics you're curious about.
I'll get you started by answering one of your questions.
Q. "For the attic and garage ceiling, we think the best option might be to furr down the rafters an inch and install R-30 rockwool batts flush with the inside edge of the rafters. This would leave about an inch of air gap to the decking without requiring us to install baffles. ... We could also layer additional rockwool below the rafters in the knee walls and beneath the ridge. Is this a good approach?"
A. The reason you want to install ventilation baffles is to create an air barrier above your fibrous insulation. This improves thermal performance and prevents wind-washing. For more information, read these two articles:
"How to Build an Insulated Cathedral Ceiling"
"Site-Built Ventilation Baffles for Roofs"
Martin,
Thanks for your quick reply, and sorry for the rookie mistakes. I appreciate you getting me started. I reread the articles you suggested and several others. I hope you'll indulge a more focused attempt on my part to clear up some issues. Here are my key remaining, generalizable questions that are relevant to the article above:
Q1: When you're dealing with an unvented (or with only gable vents) slate roof, are vent baffles necessary to allow the decking to dry to the interior and exterior, or is closed cell spray foam applied directly to the decking an acceptable and smart approach?
Q2: If you install site-built rigid foam vent baffles between rafters, then install rigid foam board under the rafters and blow cellulose into the void to reach the right total R or U value, does this comply with R806.5 of the 2012 IRC (foam must be "applied in direct contact with the underside of the structural roof sheathing" in a flash and batt type approach)?
Q3: Assuming the above is workable, is there a risk of trapping moisture in the fibrous insulation layer by having largely impermeable layers on either side?
Q4: What are the best practices for mitigating thermal bridging where structural knee wall framing members (vertical and horizontal) intersect with roof rafters?
Thank you again,
Kyle
Kyle,
Q. "When you're dealing with an unvented (or with only gable vents) slate roof, are vent baffles necessary to allow the decking to dry to the interior and exterior, or is closed cell spray foam applied directly to the decking an acceptable and smart approach?"
A. If it is a vented attic with gable vents, the board sheathing can dry to the interior and the exterior, and everything is fine. If you are finishing the attic and turning the space into a conditioned attic with insulation that follows the sloped roofline -- at which point the gable vents become irrelevant -- then you want to maintain a vented air space directly under the roof sheathing, to allow the board sheathing and the slate roofing to dry quickly. You could use spray foam, I suppose, as long as you install rigid ventilation baffles to create an air space under the roof sheathing before you install the spray foam.
Q. "If you install site-built rigid foam vent baffles between rafters, then install rigid foam board under the rafters and blow cellulose into the void to reach the right total R or U value, does this comply with R806.5 of the 2012 IRC (foam must be 'applied in direct contact with the underside of the structural roof sheathing' in a flash and batt type approach)?"
A. If you are installing cellulose on the interior side of a ventilation baffle, you are creating a vented roof assembly. This has nothing to do with flash-and-batt, which is a type of unvented roof assembly incorporating spray foam insulation.
Q: "Assuming the above is workable, is there a risk of trapping moisture in the fibrous insulation layer by having largely impermeable layers on either side?"
A. As long as you take reasonable precautions to ensure that the rafters are dry on the day you install the continuous layer of interior rigid foam, and as long as the cellulose blown into the rafter bays is dry, the assembly you describe is safe.
Q: "What are the best practices for mitigating thermal bridging where structural knee wall framing members (vertical and horizontal) intersect with roof rafters?"
A. Kneewall framing is vertical, unless you are talking about the bottom plates and top plates of the kneewall. If you want to limit thermal bridging through a kneewall, install a continuous layer of rigid foam on either the interior or exterior side of the kneewall. Of course, if you choose to install the rigid foam on the interior side of the kneewall, it must be protected by a layer of 1/2-inch drywall.
Note that not all kneewalls are insulated, though. It's usually best to extend the insulation installed along the roofline all the way down to the soffits rather than to try to insulate the kneewall. For more information, see “Two Ways to Insulate Attic Kneewalls.”
Martin,
Thanks again for your answers. A few quick follow-up questions:
Q: If one is insulating along the sloped roofline (and installing rigid ventilation baffles), and there is no soffit or ridge ventilation, is the channel above the ventilation baffles sufficient to label the roof assembly as "vented"?
Q: Recalling another GBA user's challenges with condensation in a related but different situation (see https://www.greenbuildingadvisor.com/question/insulation-for-vaulted-ceiling), is it a bad idea to install and air seal 1 or 1.5" depth rigid foam ventilation baffles and not immediately add the layers of fibrous insulation and additional rigid foam on the interior side to reach the prescribed R value and six-sided air seal? In other words, would a thin layer of rigid foam collect moisture on the inside and/or outside surface and risk causing problems for the decking, rafters, and/or exterior wall top plates if we have to wait to finish the assembly until after rough-in inspection in a couple months? Would that be worse than leaving the decking entirely exposed to the semi-conditioned inside as it is now (we have two HVAC registers in the area that are closed to minimize interior-exterior temperature differentials)?
Q: In my last question in the previous round, I was asking how to work around the kneewall top plate, which will interrupt a continuous layer of rigid foam installed below the rafters from the ridge to the eaves. I have read the article you cited, but other than caulking the joint where the foam hits the top plate, I don't see that issue specifically addressed. Is it advisable to use two 1" layers of rigid foam staggered to try to overlap the top plate with flush cutouts where you have to work around the kneewall studs?
Thanks,
Kyle
Kyle,
Q: "If one is insulating along the sloped roofline (and installing rigid ventilation baffles), and there is no soffit or ridge ventilation, is the channel above the ventilation baffles sufficient to label the roof assembly as 'vented'?"
A. No.
Q: "Is it a bad idea to install and air seal 1 inch or 1.5 inch depth rigid foam ventilation baffles and not immediately add the layers of fibrous insulation and additional rigid foam on the interior side to reach the prescribed R value and six-sided air seal?"
A. No.
Q. "In other words, would a thin layer of rigid foam collect moisture on the inside and/or outside surface and risk causing problems for the decking, rafters, and/or exterior wall top plates if we have to wait to finish the assembly until after rough-in inspection in a couple months?"
A. No.
Q: "In my last question in the previous round, I was asking how to work around the kneewall top plate, which will interrupt a continuous layer of rigid foam installed below the rafters from the ridge to the eaves. I have read the article you cited, but other than caulking the joint where the foam hits the top plate, I don't see that issue specifically addressed."
A. Caulking the joint is fine. You could also use a high-quality European tape.
Thanks Martin. Your first answer seems to take us back to an earlier question:
Q: If the assembly described above is unvented, then do we face the conundrum of either complying with R806.5 of the 2012 IRC that says for an unvented assembly foam must be "applied in direct contact with the underside of the structural roof sheathing" or following your and others' guidance that a slate roof like ours needs an air gap under the decking to allow for some interior drying?
Thank you,
Kyle
Kyle,
It's good to be conservative with a slate roof, which is a wonder and expensive asset that needs to be protected. Ideally, you'll have a vented air channel under the slate -- which requires soffit vents and a ridge vent.
That said, there's some wiggle room here -- wiggle room that requires judgment. Slate is vapor-permeable and air-leaky, so there is always some outward drying (through the roofing) with slate. Things get complicated, however, if the slate is installed over heavy asphalt roofing felt and solid sheathing. That's where the judgment comes in.
With slate installed on skip sheathing the sheathing is inherently vented and fiber insulation can be in contact with the underside of the skip sheathing planks.
Slate mounted on full plank (no gaps) or sheet goods it needs to be either vented from below, or done with the layer of closed cell foam on the underside of the roof deck. Your roof deck appears to be plank sheathing and needs to be either foamed or vented on the underside.
Dana,
Are you sure about that? Skip sheathing would leave the fibrous insulation in direct contact with the underside of the slate itself. i don't know much about this, but it seems instinctively to be potentially problematic.
Hello Martin,
I'm completely remodeling a historic home that is a mixture of 1, 1.5, and 2 stories in climate zone 5. Ductwork will be in 1.5 and 2 story attics. The 1.5 and 2 story attics we be just large enough for ductwork and room to crawl through. The 1 story attic is a little larger and will be used for storage and has no ductwork. I will be installing a metal roof.
My original plan was to build a conditioned attic and place 1.5” of foam XPS board (r7.5) installation on top of the roof deck and, fill the old true 2x4 rafters and rafter walls with closed cell insulation, and If able, attach 3” of foam XPS board (r15) to the rafters in the attic. This would total about r35 on the sloped walls and r 50 in the attic.
My contractor is concerned that a sealed conditioned attic with no airflow will become humid and stale and promote mold and rot. Is this a concern and should I do something to create airflow through the attic. Maybe I should intentionally install very leaky ducts. I think if I actually install a supply and return that I won’t meet fire code. What would you suggest?
At 1.5 XPS is labeled at R7.5, but only warranteed to R6.75, and at full depletion of it's climate damaging HFCs after several decades is more likely to hit it's fully depleted performance of R6.3. Using EPS instead of XPS it would be R6.3 today, and R6.3 in 50 years and beyond, and being blown with much more benign pentane, doens't have nearly the long term envrironmental impact. Better yet would be 1.5" of 2lb roofing polyisocyanurate, also blown with pentane, with a labeled R of R8.5, but performing more like R7.5 during mid winter, and uses a more environmentally polymer to boot.
In a zone 5 unvented roof assembly as long as at least 40% of the total-R is on the exterior side, 60% of the total R can be fiber insulation or open cell foam, either of which is a lot cheaper.
R7.5 on the exterior would be sufficient dew point control for only R11 of fiber insulation snugged up to the roof deck. Most closed cell spray polyurethane is blown with HFC245fa, and is nearly as bad for the environment as XPS, but products blown with HFO1234ze get slightly better R per lb of polymer, and about 1/1000 the damage due the blowing agents. Adding as little as 2" or R14 of HFO blown closed cell foam, there would be sufficient dew point control for up to R30 of fiber insulation, leaving 2" of nominal depth in the full dimension 2x4 cavities. If one installs milled 2x4s perpendicular to the existing rafters 24" on center the depth becomes 5.5" which is enough for about R23 of 1.8lb density blown fiberglass.
That stackup would give you ...
...R7.5 polyiso (derated for climate and temperature)
...R14 closed cell polyurethane (if HFO blown)
...R23 fiberglass
... for about R44-R45 total.
But with the reduced thermal bridging due to the exterior polyiso and interior side fiberglass it would be pretty close to the code minimum performance on a U-factor basis. With R20.5 on the exterior of the fiberglass it's at least ~47% of the total R outside the air and vapor permeable layer, which is sufficient for dew point control at the foam/fiber boundary. Using a rugged reinforced "smart" vapor retarder such as Intello Plus on the interior is recommended as the interior side air barrier, and would be cheaper than installing gypsum board and latex paint in areas that aren't being fully finished. Intello is rugged enough to be used as the blowing mesh for the dense packed fiberglass too.
>"Maybe I should intentionally install very leaky ducts."
And maybe you should have your head examined !?! :-)
Terrible idea!
A good duct design is balanced to limit the pressure differences between rooms when the air handler is operating. A leaky duct upsets that balance, and the resulting pressure differences drive outdoor air infiltration via uncontrolled unknown and not always healthy paths.
>" I think if I actually install a supply and return that I won’t meet fire code."
If it's supply-only registers I believe it will meet fire code even if using uncovered spray or rigid foam board. It may meet fire code with both supply & return registers in the 1.8 lb fiberglass scenario if the spray polyurethane is painted with intumescent paint before the fiberglass goes up. Check with the inspectors.
Hello again,
Here is the article form the Building Science corporation that I was reading suggesting that some sort of air circulation is needed in the unvented attic. It does make sense that needs to be some method for the more humid air to be circulated or removed.
https://www.buildingscience.com/documents/insights/bsi-077-cool-hand-luke-meets-attics
Chris,
The issue discussed by Joe Lstiburek in the article you cite ("Cool Hand Luke Meets Attics") is also discussed in several GBA articles, including "High Humidity in Unvented Conditioned Attics."
Hello,
Most of these articles such as "High Humidity in the Attic' deal with open and not closed cell insulation.
An article just published today cites problems with closed cell as well.
https://www.greenbuildingadvisor.com/article/high-humidity-attic
The concencious seems to be that in a conditioned attic, some sort of circulation system needs to be in place to (HVAC or other) to circulate the attic air with the rest of the house. It doens't seem that passive air movement is enough.
Regardless, after learning that a fire barrier is also needed to cover the spray foam code 2603.4.1.6, it's starting to seem that building a conditioned attic in my home will be more trouble than it worth.
I guess that was the whole purpose of this article right? To help us understand that this isn't a one-size fits all solution.
Chris,
If you bring a room into your conditioned space, it should be treated just like your living room or a bedroom. It is now indoors, not outdoors. Building scientists are now realizing that moving the air around is helpful to address potential humidity issues. Of course, for fire safety reasons, most indoor rooms cover the insulation with drywall. That's common sense, but it also adds expense.
If all this seems like a lot of work just to make your ducts comfortable, you're right. These hassles make ductless minisplits look better and better.
Chris,
First of all, it would be helpful to know your climate zone or geographical location.
Your suggested foam sandwich -- exterior XPS, closed-cell spray foam between the rafters, and XPS interior insulation -- isn't very environmentally friendly and differs from my usual recommendations for creating an insulated sloped roof assembly.
For one thing, green builders don't use XPS. For more information on this topic, see this article: "Choosing Rigid Foam."
For another thing, most brands of closed-cell spray foam aren't particularly environmentally friendly.
The usual approach -- if you want to combine continuous exterior insulation with insulation between the rafters -- is to install EPS or polyiso on the exterior side of the roof sheathing, and to install a fluffy insulation like fiberglass, mineral wool, or cellulose between the rafters. For more information, see this article: "How to Install Rigid Foam On Top of Roof Sheathing."
Martin,
I am in climate Zone 5.
This XPS board was reclaimed "used" board that was saved from a landfill.
My hope was to use Closed cell for it's sealing properties and high R value, while using the foam board as a way to minimize the amount of needed closed cell spray foam. The foam board would also help to minimize thermal bridging. Being that most of my rafters are actually upstairs walls and only 4" think, I'd need to put 5" or more of any kind of foam board on top of the roof deck added with an R13 fiberglass batt to get close to R40. That's a lot of above roof insulation.
My bigger question is not so much about the materials used, but more as to the health of my sealed/conditioned attic. What would be the best practice to keep my attics healthy?
>"This XPS board was reclaimed "used" board that was saved from a landfill."
That's greener than new foam board (any type), but derate to R6.3- R6.75 from a design point of view.
>"Being that most of my rafters are actually upstairs walls and only 4" think, I'd need to put 5" or more of any kind of foam board on top of the roof deck added with an R13 fiberglass batt to get close to R40. That's a lot of above roof insulation."
As little as 4" of ubiquitous and cheap reclaimed roofing polyiso (not XPS) above the roof deck you would have sufficient dew point control for up to R32 or so of fiber insulation. R13 batts don't fit in full dimension 2x4 cavities- they don't have enough loft. Compressing an R23 rock wool batt to 4.0" in those cavities would be about R17, compressing an R21 fiberglass batt to 4.0" would deliver R16.
Installing milled 2x4s perpendicular to the underside of the rafters 24" o.c. would allow you to install another layer of R15 rock wool or fiberglass (or R13s, if you like). That would put you in the R49-ish range, with substantial thermal breaks as well.
Chris,
Q. "My contractor is concerned that a sealed conditioned attic with no airflow will become humid and stale and promote mold and rot. Is this a concern? And should I do something to create airflow through the attic?"
A. Your contractor is wrong. In general terms, bringing your attic into the conditioned space of your house should mean that the attic shares the conditions of other rooms in your home's conditioned envelope -- so your attic should be no more humid or moldy than your bedrooms or living room.
That said, there is a specific subset of problems that can occur if you insulate the underside of your roof sheathing with open-cell spray foam. Assuming that you avoid this problematic approach to insulating, your attic should be fine.
Thank you,
I have read some of the articles about the dangers of using open cell foam under roof decks to created a conditioned attic. That is why I was choosing Closed cell, to stop the flow of water vapor into the roof.
The contractor is concerned because the attic is only passively conditioned. The rest of air is constantly mixed by the HVAC system, but the attic air will only passively migrate through gaps in the drywall or leaks in the ductwork and most ductwork nowadays is almost fully sealed.
I read an article a few days ago about leaky ducks helping to move air through the conditioned attic space but am unable to find it now.
Thank you for your expertise.
>"I read an article a few days ago about leaky ducks helping to move air through the conditioned attic space ..."
No matter which end of the duck was leaking it's nothing you want to have in your attic! :-)
See my comments in response #94 about leaky DUCTS.
Thank you both. Great information. I have some good ideas to work with now.
“Remember: ventilated rafter bays are incompatible with rigid foam insulation installed on top of the roof sheathing.”
Martin:
With nearly a hundred comments/replies I was not able to scrutinize all of them and perhaps the answer to my question lies within them. I don’t understand the concept of the incompatibility in the above statement. It seems more of a duplication or redundancy than an incompatibility.
My particular interest is that I could sooner insulate my rafter bays (and properly ventilate them) and later (years) renovate my roof to include rigid foam on top of the sheathing.
I really appreciate the abundance of wisdom that you and commenters bring here.
Mark Walter
Mark,
What Martin is getting at is that if you include ventilation bays under the sheathing, and rigid foam above it, the air introduced through the ventilation negates the insulating value of the foam above. It's like insulating your walls but leaving the doors open.
There is nothing wrong with what you are proposing. You would just have to remove the ventilation when you decided to add the rigid insulation in the future.
Oh, JEEZ!!!! Duh. 🤭😳
Mark,
Over the years Martin has several times had to p0int out to me the logic behind really basic things that in retrospect were obvious. I've certainly had my share of Oh JEEZ Duh moments too.
Martin,
Fantastic article. I am in middle of new construction. I am in California, in wildfire country: to prevent ember intrusion, building unvented attic, sealed w closed cell spray foam.
I have some basic question from a building novice on your article on bringing the attic into the conditioned space of the home:
1. Aside from opening windows for ventilation, do I need to design special ventilation for the conditioned space? Can I simply use the HVAC fan to circulate air- does that qualify as ventilation? Or do I need a special exhaust ventilation, supply ventilation through HVAC return or balanced ERV ventilation. Those all seem complicated. My hope was simply use the HVAC fan +/- windows.
2. My furnaces in attic are sealed combustion. But the fireplace will be b-vented, the kitchen fan has typical vent etc. Do I need to do anything special to avoid negative pressure/ backdraft? One of your colleagues wrote this article: https://www.greenbuildingadvisor.com/article/sealed-combustion-appliances-and-hot-tub-parties. I don't know if answer to question #2 is related to question #1.
3. As I am in southern California, usually hot and dry, does that change whether I need to ventilate within the conditioned space: i.e. between attic and living space. In your article I gathered it may not be necessary since you say "probably don’t need a supply register or return grille in your attic." Anything I need to consider to change that "probably" to "definitely"?
Thanks very much!
Jon,
Q. "Aside from opening windows for ventilation, do I need to design special ventilation for the conditioned space?"
A. You should check with local building code requirements in California -- but an increasing number of jurisdictions require that all new homes include an adequate mechanical ventilation system. Even if your local code doesn't require ventilation, the best building science advice is that every new home should be built tight and ventilated right. Here are links to two relevant articles:
"Designing a Good Ventilation System"
"Revisiting Ventilation"
Q. "Can I simply use the HVAC fan to circulate air -- does that qualify as ventilation?"
A. No. A forced air system is designed to circulate indoor air in a loop, while the air is either cooled or heated. Most forced air heating and cooling systems do not provide any outdoor air -- they aren't ventilation systems. They just keep circulating the same stale air, over and over again.
Q. "Or do I need a special exhaust ventilation, supply ventilation through HVAC return or balanced ERV ventilation? Those all seem complicated."
A. Yes, that's what you need. Read the articles.
If creating a conditioned attic in a hot, DRY, climate (ie. southwest) is an air space under the roof sheathing still necessary? I expect not, but thought it worth asking. It would certainly simply things if batt insulation could be installed between rafters directly against the roof sheathing.
Thanks!
Patrick,
If you are using fluffy (air-permeable) insulation -- something like fiberglass, mineral wool, or cellulose -- between your rafters, building codes require you to include a ventilation gap between the top of the insulation layer and the underside of the roof sheathing. This ventilation gap needs to be connected to soffit vents at the lower end of the roof, and needs to be connected to a ridge vent at the top of the roof. More information here: "Site-Built Ventilation Baffles for Roofs."
If you want to create an unvented roof assembly -- that is, an assembly that lacks the ventilation gap between the insulation and the roof sheathing -- you have only two choices: either (1) install an adequately thick layer of rigid foam on the exterior side of the roof sheathing, or (2) install an adequately thick layer of closed-cell spray foam on the interior side of the roof sheathing. More information here: "How to Build an Insulated Cathedral Ceiling."
Thanks Martin. My son has a house in the Las Vegas area which has HVAC equipment in the attic. It seems like a good candidate for creating a conditioned attic (it's a ranch style house with a fairly open attic), but all the insulation would need to be installed from the interior.
Although there are some soffit vents in the eaves, there are no ridge vents. So my thought was to make it an unvented space. As I understand it, the purpose of the closed-cell spay foam is to air seal the roof. Would polyiso rigid foam boards, cut to fit between rafters and caulked, accomplish this? The roof deck is composed of 1x6 boards that are spaced apart (shake shingles were originally nailed to those I believe). When the house was reroofed years ago OSB sheathing was nailed over the planks to give a continuous nailing surface for fiberglass shingles. But from the interior you can see the original spaced roof planks which might make closed-cell spray foam awkward to use. Anyway, just looking for ideas. I expected using batt insulation against the decking (spaced planks), although not code, would likely not cause any issues given how warm and dry the climate is.
Thanks again!
Patrick,
Q. "The purpose of the closed-cell spay foam is to air seal the roof."
A. Not exactly. The closed-cell spray foam works because of two properties: the fact that it has enough R-value to raise the temperature of the first condensing surface, and the fact that it is an air barrier.
Q. "Would polyiso rigid foam boards, cut to fit between rafters and caulked, accomplish this?"
A. No. You are describing the cut-and-cobble method. That approach is risky for cathedral ceilings. To learn why, see "Cut-and-Cobble Insulation."
Q. "I expected using batt insulation against the decking (spaced planks), although not code, would likely not cause any issues given how warm and dry the climate is."
A. That might be your expectation, but you are wrong. Joe Lstiburek experimented with your suggested approach in Las Vegas, and ended up with roofs with moisture problems. Don't do it.
I have a question related to this article and your recent reply to Patrick regarding Cut-and-Cobble.
In the "If you insulate between the rafters" section of the article, it seems to imply that either spray foam or rigid foam board could be installed directly against the underside of the roof:
- "...as long as the minimum R-value of the air-impermeable insulation that is 'applied in direct contact with the underside of the structural roof sheathing'..."
- "Although spray foam insulation and rigid foam insulation can meet this standard..."
Wouldn't it have to be Cut-and-Cobble if you're using rigid foam board between the rafters? Or is it just saying that foam board could meet that standard, but that doesn't necessarily mean it should be used in that setup?
Our 1880s farmhouse attic is unvented and has the HVAC unit in it (as well as several unused chimneys), so I was interested in making it a conditioned space. The roof sheathing is over old slats that were used for an older roof system, so I'm not sure if that means I'm stuck with spray foam.
I have a quote for closed cell spraying the whole roof and gable walls, but was curious to see if I could instead fill the space between the rafters with rigid foam board (sealing the edges with canned foam) and then also attach continuous rigid foam board below the rafters, basically creating a thick wall of foam board. If that's even a feasible option, I'm not sure if the slats that are in place help or hurt the situation. (I attached a pic, for reference.)
If that air gap presents a problem because the foam board can't be against the sheathing, could I instead use a thin layer of foam board between the rafters and against the slats (using the space between them as an air gap) and then fill in below them with mineral wool, and then additional layers of mineral wool below the rafters?
Sorry, I've read this article, the Cut-and-Cobble, the Insulated Cathedral Ceiling article, the Cape Cod Insulation article, and all the details can be overwhelming! If looking at this photo brings to mind an ideal solution (to compare costs with spray foam), that would be a tremendous help! I'm willing to put in the work. I just don't want to ruin the attic or roof!
Jasiu,
This article describes code requirements that seem to allow the cut-and-cobble approach for unvented cathedral ceilings. Although the code language appears to allow the cut-and-cobble technique, that doesn't mean it's a good idea.
Remember, (1) no insulation contractor ever uses the cut-and-cobble approach, which is incredibly time-consuming, and (2) building scientists warn against the cut-and-cobble method for unvented cathedral ceilings, as I explained in my article, "Cut-and-Cobble Insulation." (There is a risk of moisture accumulation.)
Don't do it. Instead, use closed-cell spray foam.
Thanks, Martin! Again, really appreciate your help! We're trying to fix up the home and save it, so the last thing I want to do is make anything worse.
I had a random idea that I haven't necessarily seen before, so there may be a very good reason for not doing it. If we ultimately decide that closed cell spray foam isn't affordable or cost effective, do you think there would be a benefit to just using insulation (likely mineral wool) on the attic floor, putting additional insulation over the ducts, and building a small insulated "room" around the HVAC unit itself? We're not using the attic for storage, so there would be plenty of space to frame a space around the unit and still have access for maintenance. Even if it's not airtight, I'm just wondering if going the traditional insulation route but keeping the HVAC unit away from the extreme attic temps might help its efficiency and longevity.
Hi, Martin!
We're getting quotes on roof replacement, so we're exploring the idea of installing foam board at the same time instead. As I've discerned from this site, that would mean sheathing, asphalt paper, foam board above (in coastal NC, it seems 1" of XPS would do it), and then any type of insulation below. That leads to two questions:
1) Does the foam board require another layer of sheathing above it, and then the shingles? Or, can the shingles be installed directly above the foam board (or perhaps with another layer of asphalt felt between)? I'm concerned about the added weight of a second layer of sheathing.
2) If we did mineral wool below, would the slats under the sheathing (please see pic in preceding post) create an issue, since the insulation wouldn't be directly against the underside of the sheathing?
Thank you in advance for any light you can shed on this!
Jasiu,
Q. "Does the foam board require another layer of sheathing above it, and then the shingles?"
A. Yes. More information here: "How to Install Rigid Foam On Top of Roof Sheathing." Double check your math on the minimum thickness of the rigid foam.
Q. "If we did mineral wool below, would the slats under the sheathing (please see pic in preceding post) create an issue, since the insulation wouldn't be directly against the underside of the sheathing?"
A. The "slats" are called skip sheathing. No, the skip sheathing won't cause a problem, as long as you install a good air barrier on the interior side of the mineral wool.
We are in climate zone 3, so I was basing the thickness on this article: https://www.greenbuildingadvisor.com/article/how-to-install-rigid-foam-on-top-of-roof-sheathing
"In Climate Zones 1 through 3, you’ll need at least R-5 of rigid foam (about 1.5 inch of EPS, 1 inch of XPS, or 1 inch of polyiso);"
So, I was thinking I could put R5 above and the rest in mineral wool below. I didn't realize it would also require an air barrier, though. Not sure it would be at all feasible to install drywall (or similar) throughout the attic and actually get a secure fit. And, if a second layer of sheathing is required, I'm not sure I want to go that route regardless.
I'm wondering if foam board could be used to reduce the spray foam cost. You mentioned, "Even if you insulate between your rafters with an air-impermeable insulation like spray polyurethane foam, you may want to provide a ventilation channel under your roof sheathing." Could I install foam board between the rafters and then spray foam over that, to air seal the entire enclosure? (Could it go up against the skip sheathing, or would it still need spacers?) I'm not sure if that really counts as Cut-and-Cobble anymore, if the whole thing gets sprayed over to seal. There are DIY closed cell sprays that would be much more affordable for an inch of coverage (or two, if need be), if I just coated it all over after.
Thanks again! This site and your guidance really are an invaluable resource as I explore options!
Jasiu,
You're right about the R-5 rigid foam -- that will work in Climate Zone 3. Note that most green builders avoid the use of XPS because it is manufactured with a blowing agent that has a high global warming potential. (More info here: "Choosing Rigid Foam.")
You can probably combine rigid foam and spray foam safely, as you propose -- but note that exposed spray foam is a fire hazard. Most code inspectors will require the spray foam to be protected on the interior with a so-called "thermal barrier" like drywall. More information here: "Thermal Barriers and Ignition Barriers for Spray Foam."
Thanks so much, Martin!
I had actually read that article, and (unless I'm misunderstanding) it seems the thermal barrier wouldn't apply to an attic space that was using only for HVAC equipment. The attic isn't used for storage or any living space, and would be separated from the living space by plywood, drywall, and beadboard. So, I believe that would create the thermal barrier for the living space.
I was, though, still interested in applying that paint that helps spray foam be more fire resistant, just as an added layer of safety.
Overall, I think the foam board and spray covering may be the most effective route. No additional weight from the extra layer of sheathing, and it seems significant cost savings by filling up most of the space with foam board instead of spray. And, considering future improvements, I think makes roof repairs easier (since the spray foam wouldn't be on the sheathing) and I could always add more spray foam to increase R value, if need be.
Now if this heat wave would end and the attic would stop being 300º... haha
Thanks again! Greatly appreciated!
Hi Martin,
Big fan, I would really appreciate some advice on a project I'm doing in my home.
I am renovating my house built in 1976 in south Florida climate zone 1 – Hot and humid
I currently have a vented roof with a floor insulated attic and HVAC ducts in the attic. I have been researching unvented conditioned attics and wanted to find the best solution
I’ve read the articles on Green Building Advisor “Creating a Conditioned Attic” and “Open-Cell Spray Foam and Damp Roof Sheathing”.
I would really appreciate some advice to make sure I’m going about this the right way
My plan is to use open-cell spray foam on roof rafters and condition the attic.
Will the following steps solve the risk of damp roof sheathing?
1) My roof was recently redone with asphalt shingles, so the roof is new and without leaks.
2) Add an HVAC supply to the attic (What R-value open-cell should I install in my climate zone? How many CFM should I supply to the attic space? Do I need to add a return?)
3) Add a whole-house dehumidifier and a supply to the attic (Do I need to install the air-handler and dehumidifier in the attic? Or can I just run supply and leave the air-handler in the house?) Will an Ultra-aire 120h be enough or should I use the SD12?
4) Add an ERV (Do I need to add a supply to the attic?) Which unit do you recommend?
Some more info about the project: My house is about 3500 sq ft and I want to change the HVAC to a VRF system. What is your opinion? I am also replacing all my windows to double-pane and low-e glass to get as tight as possible. Should I use a Mitsubishi VRF? Or another brand like Carrier Infinity?
Should I just use Mini splits all over the house? If so how do I dehumidify?
I have spoken with a couple of mechanical engineers and they both advised against everything I am doing. They both say to keep a vented attic and leave everything as-is saying it is dangerous.
Their claim is humidity issues and fresh air change. When I explained I was adding a dehumidifier and an ERV they said it won’t solve the problems without explanation why.
Can you recommend a mechanical engineer who agrees and can help design this project properly?
I appreciate your help
Thank You
I’m building a 2 story home in the Los Angeles area with the furnaces and ducts in the attic. From what I’ve seen almost every builder does this and ventilates the attics (and I’m guilty of having done this before as well). After subscribing to GBA and reading all the articles I could find on the topic, I’ve been convinced to condition the attic and keep it unventilated. It’s an unusually shaped lot/house resulting in a complicated roof design containing multiple hips, valleys, and gables which would be a logistical nightmare to properly ventilate anyway. I plan to use closed cell foam under the rafter bays. My title 24 calcs call for R-15 under the roof rafters and R-30 at the attic ceiling. A few questions in this regard:
1. Does this sound right? Why the lower R value at the roof rather than the other way around, since it’s all within the thermal envelope?
2. I could spray 2 inches of closed cell foam under the roof rafters. Would it be acceptable to just spray 1 inch of closed cell foam and fill the rafter bays below it with fiberglass batts? That way I get the air barrier of the foam and still reach the required overall R-value (the roof rafters are 2x10, so I have plenty of room). I would save a substantial amount of $$ this way.
3. This is a fairly mild climate zone (3B). Do I need to worry about thermal bridging through the rafters? From my understanding, the only way I could circumvent this is by using rigid foam above the rafters.
4. As an alternative to closed cell spray foam, could I install a single layer of rigid foam boards above the rafters, but below the roof sheathing, and complete the required R-value with fiberglass batts between the roof rafters? My insulation contractor seems to think this is a less reliable method/barrier than closed cell. And would it even be more cost-effective?
Any input/comment is greatly appreciated.
Thanks.
Oren,
Although California's Title 24 may allow it, I don't recommend splitting your insulation and installing it in two locations (some of it following the sloped roofline, and some of it on the attic floor). You want to establish your thermal boundary at the roofline--so that's where all your insulation belongs. In Climate Zone 3, you want to aim for R-38 at the roofline.
If you want to try a flash-and-batt approach, you need a minimum of 1 inch of closed-cell spray foam for the "flash" layer in your climate zone. More information here: "Flash-and-Batt Insulation."
You can't sandwich rigid foam between rafters and roof sheathing, because the rigid foam is too squishy. It will deform when the sheathing is nailed on. If you want to install a continuous layer of rigid foam above your rafters, the rigid foam belongs on the exterior side of the roof sheathing. More information here: "How to Install Rigid Foam On Top of Roof Sheathing."
Hi Martin,
Thanks so much for your quick response. I thought the split insulation seemed odd, so I will follow your advice and just insulate the roof rafters adequately with R38. Is there a benefit to still insulating the attic ceiling or can i leave it without any insulation?
Given our climate, would I be OK not supplying any registers for heating/cooling the attic? And doesn’t that mean my HVAC is working that much harder to cool/heat the attic as well? I should mention that part of the attic includes a few small gables, which will just have fiberglass batts.
I have a 2nd floor balcony in the home as well, with conditioned living space under it. I assume this should be treated the same way as a roof by sealing the underside of the “roof” with foam as well?
And for my last insulation question - my garage will be partially under a bedroom, and this part of the garage attic (as well as the interior garage walls) will obviously be insulated (with fiberglass batts). But about 100 sf of the garage is covered by another balcony. How would you recommend approaching this? If I insulate the whole garage ceiling, then I assume I would need to ventilate the garage attic. If I leave this part of the garage ceiling and the exterior garage walls uninsulated, then would I need to vent the attic? If so, what kind of vents? I would be limited to vents in the only 2 adjacent walls of the garage that are exterior walls. I also read your article on cutting and cobbling rigid foam, which sounds like a pain, but maybe would work since there isn’t that much square footage to cobble? I am attaching a photo of the space in case my description is unclear. The balcony portion of the garage is labeled at the bottom of the photo. Thanks again for your help and the website is an incredible trove of helpful information.
-Oren
"Damp roof sheathing will always dry faster in a home with an unconditioned attic than in a home with a conditioned attic."
Even though heat causes drying?
Qofmiwok,
In an unconditioned attic, the roof sheathing is fully exposed on one side to the attic air, and attic air is almost always dry (except in the Pacific Northwest). If the roof get some sun -- most roofs do -- the solar radiation helps keep roof sheathing dry.
In a conditioned attic, the underside of the roof sheathing is either covered by insulation, or is adjacent to a narrow ventilation channel. In either case, there is less opportunity for drying than in an unconditioned attic.
We are building a home in SE Kansas (Zone 4A) with a bonus room over the garage and a little bit of bonus space of the adjacent part of the attic over the house. About 1/2 the house attic has no bonus space. I've been reading a lot of articles and comments on how to insulated cathedral ceilings, all about attic venting, etc and am still faced with a few questions. I would consider putting foam on top of all my roof sheathing but about 1/2 my roof is not over any bonus space and part of it is a large overhang in a vaulted living room that hangs over an outdoor deck which would be a waste of foam on top but would be needed since they share the same roofline. In the half of the house with no bonus room, my plan was to flash n cellulose fill the ceiling which would be separated by an insulated wall / air barrier in attic from the other half of the house which contains the bonus rooms. Because of numerous hips and details, I don't think venting is a good option. Therefore, here are my questions:
1) Can I do unvented rafter bays by flashing with 1" of closed cell foam, then packed cellulose (or other type), then 2" of rigid foam under the rafters to stop thermal bridging? Is this permissible or would this cause any moisture issues. I've looked and saw something like this reference in this article, but wanted to confirm.
2) Alternatively, could I use open cell foam to fill the bays and still rigid foam over these with 2" foam, and if so, what type? We are out of city so codes are not enforced but I believe code calls for R49 ceiling so depending on my rafter bay depth, we may have to do something different or settle for less in this area.
3) In bonus truss, Is it permissible to go unvented from soffit area with the above mentioned insulation method, then insulate the top cord (ceiling) of the bonus room the same way? In this case, would I need a ridge vent at the peak over this area?
I'm just trying to see if I can build a non-vented roof in this attic space or if there would be a better way to do this. I'm open to a vented assembly but only about 70% of my rafter bay's have soffits below and the ridge vent would be even less space with the hips. In addition, venting 1.5" would reduce my overall thickness of insulation so I really feel non-vented wins out here. I attached a sample detail sketch up - pardon my drawing capabilities.
Trent,
Here is a link to five common types of cathedral ceilings that work, some of which are un-vented. You may want to pick a couple to reflect the different situations you have, or maybe just one that will cover everything.
https://www.greenbuildingadvisor.com/article/five-cathedral-ceilings-that-work
Yes you can go un-vented for the lower portion of the roof and then vent the small attic above. You will need a ridge vent, and I believe your code wants a higher ratio of ventilation for situations where you don't also have lower ones. Also remember that whenever you have a concealed space like an attic over a certain height, you need to provide access to it.
This may seem odd, but I would stop thinking of these spaces as Bonus Rooms, or in some way different than any other of the living areas you are building. They have the same needs, and cost the same amount as the rest of the house. The name was thought up as a marketing gimmick to make people feel like they were getting something for free.
Thanks Malcom for your reply,
I did see those 5 types of cathedral ceilings and the one that looked closest to what I was thinking was assembly #5, but with added 2" foam below the batts or cellulose. So it would be roof sheathing - 2" of closed cell foam, as much fluffy insulation as would fill the rafter cavity, and then 2" rigid foam on bottom of rafters for thermal break. My little sketch did not post, so I retried it and now it displays. Also, good point on the "bonus room" description. You are right that sounds good for marketing but it is quite expensive space if you condition it correctly.
Trent,
Yes that would work. It does seem like a quite complicated assembly though. I don't have much experience with un-vented roofs. Hopefully someone like Akos will come along and propose a simpler solution.
Questions posed in the Recent Article Comments tend to disappear quickly. It might be a good idea to re-post it in the Questions and Replies where it will elicit more responses.
Trent,
Here is another alternative that works with irregular roof shapes - and wouldn't waste foam over the attic portion. https://www.greenbuildingadvisor.com/article/building-a-vaulted-high-performance-and-foam-free-roof-assembly#comment-230636
Thanks for the detailed article. I'm a little confused about the insulation strategies mentioned above, but I know the original article is now almost 13 years old, codes have changed (some of which is mentioned in the article), and I'm on the east cost of Canada. I only have a little experience with the IRC from some time ago working on projects in Utah.
Above it says: "According to the 2009 IRC (Section R806.4), it’s possible to build an unvented roof assembly with a combination of rigid foam insulation above the roof sheathing and air-permeable insulation in the rafter bays. The code requires that “rigid board or sheet insulation shall be installed directly above the structural roof sheathing as specified in Table R806.4 for condensation control.”"
Then in the following section on ventilation it goes on to say: "if ventilation is omitted, only “air-impermeable” insulation can be used in contact with the roof sheathing.
Although the 2006 IRC neglected to include a definition of “air-impermeable insulation,” that omission was rectified in the 2009 IRC, which defines air-impermeable insulation as... In other words, an air-impermeable insulation must meet the same airtightness standard as an air barrier material. Although spray foam insulation and rigid foam insulation can meet this standard, dense-packed cellulose cannot.
If you choose to install a fibrous insulation like fiberglass or cellulose between your rafters, you must include a ventilation channel between the top of your insulation and the underside of the roof sheathing."
At first I thought those two sections contradicted each other, but I assume it's because the second section is not contemplating a layer of continuous insulation on the exterior side of the roof sheathing? I can't figure out what the ventilation channel would be for if not allowing potential condensation on the underside of the sheathing to vent out. And if there is an appropriate amount of continuous insulation on the exterior of the sheathing keeping it warm condensation risk is greatly (if not entirely) reduced. And, because assembly #3 in the article on 5 cathedral ceilings that work shows exactly this.
Does my thinking make sense?
Thanks!
Will
Will,
Malcolm provided the answer -- which you had already guessed. Because of your useful comment, I have re-written my article to clarify the section that appeared contradictory.
Thanks for the comment and questions.
Will,
Yes that's it.
Thanks, all!
Great article! I want to convert the vented attic of my 1980 house in Florida (CZ 2A) to an unvented attic. The main reason is to avoid risk of sweating HVAC ducts. The ducts have to be in the attic due to the layout of the house.
I have two main restrictions:
1) I can't use spray foam.
2) I can't install rigid insulation on top of the roof sheathing (the roof is pretty new)
From this article (https://buildingscience.com/documents/building-science-insights-newsletters/bsi-119-conditioned-unconditioned) I gathered that there is a third way besides spray foam or rigid exterior insulation to control condensation in unvented attic. A Vapor Diffusion Port.
And it sounds like it works for both conditioned unvented attics and unconditioned unvented attics.
Does anybody have experience with building either a conditioned or unconditioned unvented attic with a vapor diffusion port and air-permeable only insulation.
It looks like a valid option for me but I'd love to confirm that with experts or someone that has first hand experience.
Thank you so much!
Niko
Niko,
Another one of Martin's blogs lays out everything you need to know about vapor diffusion ports, including the code requirements where you are: https://www.greenbuildingadvisor.com/article/vapor-diffusion-ports
“[Deleted]”
Log in or become a member to post a comment.
Sign up Log in