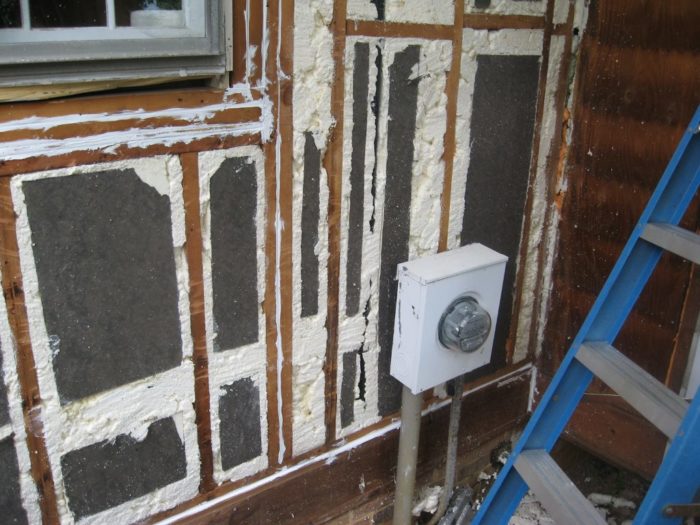
Image Credit: Michael Brahmey
Here at GBA, readers regularly ask about the best way to install rigid foam insulation between studs or rafters. A typical question might go like this: “I’d like to insulate between my studs with strips of 2-inch-thick polyiso. I plan to cut the rigid foam pieces a little bit loose, and seal the edges of the polyiso with canned spray foam. Will this work?”
Here’s my standard answer: “If you want to insulate your walls with rigid foam, you shouldn’t cut the foam into thin strips. Instead, you should keep the sheets of foam intact and install the foam as a continuous layer on the exterior side of your wall sheathing. That way, the foam will interrupt thermal bridging through the studs.”
Sometimes, I also point out: “Although the method you suggest, informally known as ‘cut-and-cobble,’ is often used by homeowners, it is such fussy, time-consuming work that it is never used by insulation contractors.” (The first person I heard use the term “cut-and-cobble” was Dana Dorsett, a regular contributor to the Q&A column on GBA. Dorsett first used the phrase in a web forum post in April 2012. “I’m not entirely sure if I was the first to use that term in a rigid insulation context, but I might be,” Dorsett told me.)
Time for a confession
If I had to summarize the theme underlying my cut-and-cobble advice, it would probably be, “Don’t do it.” But this advice leaves me feeling somewhat guilty. It’s time to come clean, and, like a newcomer at a 12-step meeting, announce: “My name is Martin, and I have cut and cobbled.”
Yes, I’ve done it — for the same reasons that lots of other people have done it. Sometimes, cut-and-cobble makes sense.
Weekly Newsletter
Get building science and energy efficiency advice, plus special offers, in your inbox.
This article is only available to GBA Prime Members
Sign up for a free trial and get instant access to this article as well as GBA’s complete library of premium articles and construction details.
Start Free TrialAlready a member? Log in
197 Comments
Cut'n Cobble
I love the name! I've seen this done and its rarely done well. The best was seeing a basement framed out in steel studs with lose board-stock XTPS roughly placed between steel members... Sadly, it was an engineer who prided himself on his DIY job.
Thanks for the chuckle!
Options
Cut-and-cobble do makes sense in many remodeling applications. When the cost of removing an existing cladding is too high (e.g., brick, stucco, etc.) or when Historical Districts do not allow for any cladding removal to install rigid foam on the outside of the wall.
Installing a ½”+ spacer between the sheathing and rigid foam creates a “venting” cavity that allows the sheathing to dry to the outside. One could install a permeable (e.g., wool) insulation in the cavity and continuous rigid foam on the inside of the wall, allowing the wall to dry to the outside.
alternatives interior?
Lets say you have a unfinished walkout basement (like myself)- where the above grade areas are 2x6 FG insulated and poly'd. I had contemplated bumping up insulation with a Mooney wall and cut/cobble between with foam.
But more and more i am reading of success stories of using XPS over studs, and then drywall right over the top. from sites like contractortalk. Just would need extended boxes for elec.
Thoughts on beefing up this code minimum wall without the wife causing a ruckus? ($$$) (we'll just say she doesn't know about all the LED's on our main level) LOL
Response to Nick T
Nick,
You forgot to tell us where you live. Unless you live very far north, the polyethylene is a mistake.
Since you describe your basement as "unfinished," I assume that your walls have no drywall. That means that your polyethylene is also a fire hazard.
The first step will probably be to remove the polyethylene. If you want your walls to perform well, the next step will be to remove the fiberglass batts and put them in a dumpster. That will give you access to the back of the stud bays so that you can perform air sealing work. Once that's done, there are a great many ways you can proceed to insulate your walls.
If you aren't willing to remove and dispose of the fiberglass batts, you'll have to accept all of the performance problems that come with the batts.
It is possible to install interior rigid foam if you want. The disadvantage of this approach is that it doesn't address the "cold sheathing" problem. If you have well-ventilated siding (vinyl siding or wood lap siding installed over a rainscreen gap), the approach is less risky than if you have poorly ventilated siding (for example, stucco).
option for floor joist retrofit
I am considering this option for between my floor joists. Fiberglass would be pretty much useless considering air flow, and spray foam is very expensive and might require a thermal shield; and going over the joists is impossible because of all the wires and pipes.
Of course most foam would also require a thermal shield, but if I can get my hands on this Thermax stuff of a descent price (1) then I might be cutting and cobbling.
Regarding the devilish details: it would be nice to spray some foam into the bay and then squish the 2' thick pieces into it and tack them in place ensuring an air seal and contact with the underside of the floor. I have not found any spray foam kits with adhesive qualities for the application however.
So far the plan is to put a bead of construction adhesive around the perimeter of the foam pieces, and nail them in place with a framing nailer and plywood chunks, then go back with spray foam cans and hit the cracks, or maybe I'll hit the corners with foam first then push them into place.
That part that I am dreading the most is spray foaming the edges. I have used a couple of the "professional" hand-held guns and they never want to spray when angled up, and it will never flow through the bendable tube either. I dread having to buy a zillion cans of great stuff.
Does anyone have product recommendations for this?
(1)http://building.dow.com/na/en/products/insulation/thermaxsheathing.htm
Response to Seth Rutledge
Seth,
Most hardware stores sell clear vinyl tubing in a variety of diameters. Buy some tubing that will slip over the plastic dispenser tube that comes with the canned spray foam cans you intend to use. Then you can keep your cans upside down (so they dispense well) and still deliver the caulk (through the vinyl tubing) to the location you want.
The tubing is fairly cheap, so you can dispose of the length you are using if it gets clogged.
More Cut & Cobble Problems
Martin--to add another data point to potential risks and failures, I looked at a cut-and-cobble roof job done by some dear friends of mine. They are located in Central MA (Zone 5A), and built a sloped unvented roof assembly using multiple layers of recycled EPS in the rafter bays (with expanding foam sealant at the perimeter), with a layer of foil-faced polyisocyanurate detailed as an air barrier under the rafters. Unfortunately, during their first winter, they started experiencing condensation dripping from the ridge. The patterns were all consistent with moisture migration up to the ridge of the attic, at the air channels formed around the foam (analogous to the "ridge rot" seen in SIPS panels from BSI-036/http://www.buildingscience.com/documents/insights/bsi-036-complex-three-dimensional-air-flow-networks).
Ripping the assembly apart and redoing it with spray foam was not on the table. The half-measure that I suggested was to add a "vapor diffusion vent" (a strip of Cosella Dorken Delta-Foxx), replacing the self-adhered membrane (vapor impermable) at the ridge. I have installed a moisture content monitoring system to keep an eye on things. So far, it seems like there's a rise in moisture content in the winter, but it mostly comes down in the summer. There are variations in moisture content--the "simpler" roof bays are drier than the more "complex" ones (i.e., dormer rafter framing). This is consistent with air leakage at the more complicated framing details. I'm going to be keeping an eye on moisture contents through this winter.
Unfortunately, this monitoring is not an ideal experiment--the "right" way to do this experiment would have been to leave a "control" bay with the failed assembly. That would have determined the effect of the diffusion vent--whether that's "saving" things. But an experiment like that is not something to do to your friends! :)
Response to Kohta Ueno
Kohta,
Thanks very much for sharing your story of a problematic cut-and-cobble cathedral ceiling. I have edited my bullet list of "disadvantages" to include your anecdote.
Response to Seth Rutledge (Dow Insta Stik)
I think that Martin has handled the air sealing side of the equation quite well. But if you want an option for using spray foam as an adhesive for rigid foam, I would strongly recommend the use of Dow INSTA STIK™ Quik Set Commercial Roofing Adhesive (http://building.dow.com/na/en/products/adhesives/instastik.htm). It is a single component urethane foam that you would apply to the back side of the rigid foam; it is intended for adhered commercial (flat) roofs (check out their installation videos). We have used it to adhere foam to masonry walls (also forming an air seal to the cavity between foam and substrate, if done correctly). You apply Insta-Stik to the rigid foam, press the rigid foam into place, hold it for about 30 seconds, and it "grips like cold death" (the product rep's words, but my personal experience corroborates this observation). ;)
For examples of the masonry installation, see Building America Report 1302: Retrofit of a Multi-family Mass Masonry Building in New England (http://www.buildingscience.com/documents/bareports/ba-1302-retrofit-multifamily-mass-masonry-building-new-england/), at Figure 24: "Test installation of foam on masonry (left) and use of polyurethane adhesive (right)"
Follow up with Martin
Martin,
thanks for the encouragement. On going for it. I am just north of Minneapolis, MN. Vapor barrier fire risk? Never heard that being an issue - pretty much all walkout basements in MN are insulated and vapor barriered if unfinished and left bare.
I will be hard pressed to push the cost of reinsulating our walls - as my wife would tell me "would most people just put up sheetrock and be done with it??..." my response...."aaah, ya, i guess..doesn't make it right....."
the hundreds if not thousands of dollars needed to insulate that wall with foam board or densepack Cel. is a energy retrofit that likely won't find traction. To replace a "perfectly good wall".... and of course we know that is a 'perfectly' wrong statement.
So as always, my goal with any energy savings be to make a safe system that has good bang for the buck. What can be done to improve the basement (maybe 'pretty fair house' standard lol) so instead of a semi leaky code built wall...(r-20 wall) to something better?
So far i have already IR camera'd on a cold night to help highlight weak spots (followed up with spray foam through the poly) and added cheap Fiber R30 over the existing 2" sprayfoamed rim joist.
Most of the retrofits talked about on here are often all or nothing and higher in cost than I see doing on a regular basis unfortunately. I guess I'll keep fighting the fight! Slowly adding insulation and some XPS as the budget allows.
whoa.
Are you telling me I could insulate the cathedral ceilings in my old timber framed house with a layer of unfaced mineral wool board insulation between the rafters and in contact with the sheathing, beautifully detailed with high quality caulking in every nook and cranny, and then fill the rest of the (furred-inward) cavities with dense pack cellulose, right up to R-60 or near to it? I've been looking for an insulation solution that doesn't involve plastics. Horizontal purlins in the hip roof framing prevent a vented assembly, and the brand new roof prevents exterior rigid insulation. Is this the answer to the question that's been keeping me up at night?
Response to Stacey Cordeiro
Stacey,
Q. "Are you telling me I could insulate the cathedral ceilings with a layer of unfaced mineral wool board insulation between the rafters and in contact with the sheathing?"
A. No. Mineral wool insulation is air-permeable, so it doesn't prevent warm, humid indoor air from contacting the cold roof sheathing. The insulation system you are suggesting would be a code violation, and it would also result in rotten roof sheathing.
The term "cut-and-cobble" is applied to a method of installing rigid foam insulation. The term is not applied to mineral wool insulation.
Note also that I am not recommending the cut-and-cobble approach for cathedral ceilings. That's why I warned, "Wood framing expands and contracts with changing humidity levels, raising the possibility that attempts to seal the perimeter of the rigid foam (whether with caulk, spray foam, or tape) will fail over time. Anecdotal evidence suggest that this danger is real, especially for cut-and-cobble cathedral ceilings. (A GBA reader recently posted an account of a cut-and-cobble roof insulation job gone wrong. Because of air leaks through cut-and-cobble cracks, the reader's flat roof is now raining condensation. Another report of a failed cut-and-cobble roof assembly is provided by building scientist Kohta Ueno in Comment #7.)"
For information on code-approved ways to insulate a cathedral ceiling, see How to Build an Insulated Cathedral Ceiling.
Hi Martin,
Sorry to resurrect such an old thread, but I have a very similar situation and would love your input. We have an existing cathedral ceiling with a new asphalt shingle roof (installed, sadly, with no insulation, just before we purchased the house). This is a shed roof on post and beam construction; Zone 3 (northern california). Roof joists are 2x10 on ~7'6" centers (3 large bays in total). Our goal is to insulate this roof and build out a new wood plank ceiling on the underside of the joists. Considering MemBrain in lieu of drywall under the planks due to door frame clearance issues.
Venting the roof does not seem feasible for several compounding reasons (no eave overhang, Wildland Urban Interface, among others). The unvented flash and batt approach seems a better route, but we want to avoid spray foam for health and environmental reasons.
Given the large joist spacing I'm wondering about 2" foil faced polyiso panels with taped seams at butt joints and EcoSeal around the bay perimeter. Since the layer of rigid would be nearly continuous across the ceiling, would you say this sufficiently addresses the cut and cobble concerns? How much does the fact the joists have been painted help with expansion/contraction issues?
Thanks,
Andrew
Andrew,
One factor in your favor is your mild Zone 3 climate, which reduces the chance of moisture accumulation in the cathedral ceiling. That said, I can't recommend an approach that has led to failures. It's risky. But it's your house, so feel free to roll the dice if you want.
The two preferred approaches are the following: (1) Ignore the age of the roofing, and install an adequately thick layer of continuous rigid foam on the exterior side of the roof sheathing, followed by another layer of roof sheathing and new roofing; or (2) Install closed-cell spray foam on the underside of your existing sheathing boards.
I decided to use cut and
I decided to use cut and cobble in a couple of small wall sections behind two minisplit units that I hung prior to completing the walls. I wanted the structure warm while I work and sleep on site. The conduit to the units does not run neatly, so I decided to create a base of foam behind the pipes and will fill around the pipes with loose fill or spray. Certainly not my preferred method of insulation but in very small doses tolerable.
thermax adhesive
I looked into hat foam adhesive and Dow says that it's not reccomended for Thermax panels. I guess if you have used it for that application and it worked then it might ok anyways?
The adhesives that they recommend are here, and none of them appear to be foam :(
http://dow-styrofoam.custhelp.com/app/answers/detail/a_id/3329/kw/foam%20adhesive%20thermax/session/L3RpbWUvMTM4NTY1MTk4Ny9zaWQva3RQNXd1R2w%3D
Re: thermax adhesive
Sorry, Seth--didn't realize that you were exclusively thinking of Thermax... and I didn't realize Dow didn't consider them compatible. In our work, we used Insta-Stik with XPS.
Insulating walls and ceilings
52 years ago, more or less, Dow brought Styrofoam to market, I read about people using it to insulate potato stores, deep freezers and boats, and thought this is an ideal product to insulate a home.
10 years later I bought my first house, gutted it, lined the walls and ceilings with inch thick Styrofoam covered with water vapor proof plastic sheet; finished with drywall and had a warm dry home. To help things along I laid fibreglass between the joists and much later over the joists.
The key thing, is facing the warm wet air inside the home with a warm surface. Water vapor always heads for the nearest cold surface to condense. Providing you only give it surfaces that are above “dew point” it behaves itself and usually condenses on the nearest cold window. Water vapor proof plastic sheet backed by Styrofoam provides a continuous warm surface, any cracks behind it in the insulation are insignificant. The usual minute holes in walls etc; allow any water vapor that does get past the plastic and insulation to escape into the colder sky, maintaining the integrity of the building.
Since then, I have moved on, these days I add up to six inches of polystyrene sheet between the joists, sealed with canned foam; and two or three inches of polyurethane sheet on the room side.
Continuous Rigid Insulation on Inside?
I'm currently building a log home on Vancouver Island (north of Seattle, moist but fairly mild and moderate climate), where we plan to insulate the walls from the inside. The outside walls are "structural" with solid 2 1/2" thick manufactured T&G boards. I'm planning to install following wall assembly (from outside to inside):
- 2 1/2" solid log wall, "failry" airtight
- Tyvek as air barrier attached to the inside of that log wall in case the outside wall has some air leakage
- 2 layers of 2" polyiso boards (staggered seems), fastened to the outside walls by vertical 1"x2" strapping
- 3/4" thick interior wall panelling attached to the vertical strapping
This assembly avoids thermal bridges and should be fairly easy to install. But the rigid insulation is on the inside, in contrast to all above suggestions (due to maintaining the outside look of the logs).
The question I have about this: Do I run any danger of getting warm moist air causing condensation problems? I will use lag screws to attach the vertical strapping through the insulation to the outside log walls... And how well does the insulation need to be sealed in the corners and at seams?
/Hermann
Response to Hermann Thoene
Hermann,
As long as you pay attention to airtightness when assembling your wall, it should perform well. Of course, you still need a plan for insulating your rim joists.
My own experience with cut and cobble
I have a lot of experience with this method of insulation. I think the pros and cons spelled out above are spot on. But if you're looking for an air-tight envelope on a rock-bottom budget, it's a viable option.
This describes my project and my experience insulating with salvaged polyiso.
http://www.finehomebuilding.com/item/23460/patricks-barn-insulating-with-garbage
I used a modified siding nailer to temporarily hold the insulation in the bays while I spray foamed the perimeter.
http://www.finehomebuilding.com/item/22229/patricks-barn-wrapping-up-the-exterior
Hi Patrick,
How did you modify your siding nailer? I couldn't find that detail in your linked writing.
Thanks,
Sean
Cut and Cobble with damaged EPS
I live in the midwest and we just had some severe weather (maybe you heard). Good news for me is no one was hurt. Bad news for me is that about $10k worth of ICF blocks got damaged to the point where I can't use them for my foundation walls anymore.
So rather than throw them away, I was thinking about this "cut and cobble" concept. So this blog is very serendipitous!
I was thinking of trying to use it in my vented attic where I had originally been planning blown cellulose to ~R-60. My idea would be to cut pieces of it to fit between the trusses against the ceiling. With extra emphasis up against the heel. I thought that I wouldn't really need to worry about air sealing the cracks/gaps between pieces because 1.) the cellulose would (hopefully) settle into all the gaps/cracks and 2.) the air barrier will be the drywall ceiling with no ductwork or lights penetrating.
Am I missing something here?
Response to Robert Kohaus
Robert,
You can't depend on cellulose to significantly limit air movement unless it is fairly deep (maybe 10 or more inches above the rigid foam scraps). Cellulose is cheap, and I don't see any advantages to mixing EPS scraps with your cellulose -- and there are several possible disadvantages (for example, the chunks of EPS might prevent the cellulose from reaching the nooks and crannies where you want it, and your local building inspector or fire marshal might be unhappy if any EPS was poking up).
I would stick with 100% cellulose in the attic if I were you.
Cut and Cobble with damaged EPS
I'll post a new question concerning this topic. Thanks Martin.
Separating from framing?
Thanks for the great article! I'm considering this method in a cathedral ceiling.
One of the disadvantages mentioned is that the expansion and contraction of wood framing may cause the seal to fail. Why is this any different than a "regular" closed-cell spray foam application? Does a full rafter bay of spray foam not run the same risk of separating from the framing?
Response to Dave Frank
Dave,
To be honest, we don't yet have a full answer to your question. Suffice it to say that an increasing number of researchers are focusing on the problem of damp roof sheathing above roofs that have been insulated with spray foam. As you might imagine, these problems are more likely if the roof was insulated with open-cell foam than if the roof was insulated with closed-cell foam.
Many cases have been reported where the cured spray foam has shrunk away from the rafters. These cases are concerning. The cases are rare, however. They are usually blamed on installer error.
In general, I think that you are much more likely to get an airtight and problem-free installation with closed-cell spray polyurethane foam than with the cut-and-cobble method.
Another option?
In another discussion on this site, installing full sheets of rigid foam on the INTERIOR side of the rafters (not between them) was mentioned. That would seem to avoid all of the cut-n-cobble disadvantages listed above, as long as you can live with the drop in ceiling height.
In my case, I'm looking to foam a large unfinished attic for (a) its air seal advantages and (b) to keep HVAC equipment within the envelope. But I'm put off by the expense and odor/health questions. Am I missing something or do you agree that such an application is a great solution? Is there any reason the air gap (the full volume of the rafter bays) between the insulation and sheathing would be undesirable?
A brand new shingle roof was already installed, so exterior installation is not an option, but this seems just as good.
Thanks!
What if there was venting
From Kohta Ueno's comments above with an unvented assembly, what would of happened if there was a vent channel 1" or 1.5" from soffit to ridge. Wouldn't that have solved the issues and made it that the sheathing can remain dry and prevent rot?
Response to Dave Frank
Dave,
If you want to leave your rafter bays uninsulated, and install a thick layer (or multiple layers) of uninterrupted rigid foam under your rafters, there is no reason why such an installation won't work.
Of course, it's important to list the usual caveats:
Pay attention to airtightness when installing the rigid foam. Use an appropriate tape at the seams.
Multiple layers of rigid foam with staggered seams are always better than one layer.
Make sure that the R-value of your assembly meets or exceeds minimum code requirements.
Don't forget to install a layer of gypsum wallboard to meet fire safety requirements.
Response to Todd Sherman
Todd,
Researchers haven't yet studied cut-and-cobble jobs, so we don't have much data on this type of roof assembly.
If I had to speculate, I would guess that a vented cathedral ceiling with cut-and-cobble insulation would probably be less risky and an unvented one. But I'm guessing.
Remember, a vent channel between the top of the ventilation and the underside of the sheathing isn't a miraculous solution, and it can be hard to create such a channel (especially in roofs with complicated geometry, hips, valleys, dormers, skylights, or chimneys). For more information on this issue, see All About Attic Venting.
Cut & Cobble
I'm in the planning stages for a large addition on my seasonal residence, which I plan to retire to. My original plan was to install two 1" layers of staggered seam polyiso on the exterior and to install 5.5" of cellulose in the wall cavities, but this doesn't achieve the R-40 wall target I had in mind. Time and labor are not issues, as I plan to complete all of the work myself over about a 5-year period. Would there be any drawbacks/issues with filling the wall cavities with 4-5.5" of polysio using the cut and cobble method, along with the two 1" layers of polyiso on the exterior?
Response to David Tontarski
David,
I don't recommend that you encapsulate your OSB or plywood wall sheathing by sealing both sides with vapor-impermeable rigid foam. It's best if your wall sheathing can dry in at least one direction. I think that you should stick with cellulose between your studs.
Your proposed wall assembly has an R-value of about R-30, which isn't bad (as long as the house is located in Climate Zone 6 or somewhere warmer; in Zones 7 and 8, you'll need a minimum of R-15 of rigid foam).
If you really want R-40, the best way to get there is to increase the thickness of your exterior rigid foam; I suggest that you install 2 layers of 2-inch-thick foam, for a total of 4 inches of exterior rigid foam.
Cut & cobble with cellulose as crack filler?
I've been wondering about the viability of cutting rigid foam panels 1/2" undersized on all sides and then using dense blown cellulose as the gap filler. It would seem to mitigate the threat of framing members shrinking or moving with humidity, at the expense of some air sealing. I'm thinking of using cut and cobble for a heated woodworking shop, so I could do proper air sealing from the outside as this would be new construction.
My own wall build is planned as follows. Please feel free to comment.
24" o.c framing with 2"x8" studs. Ribbed metal siding fastened to 3/4" horizontal nailers, wrb over 1/2" continuous plywood sheathing, 6" of cut and cobble foam (hoping to use polyiso or xps). Interior walls to have Mooney wall strapping, so there would be 3" cellulose (1.5" from foam to stud face + 1.5" Mooney wall area. Untapped or sealed plywood for interior sheathing.
Because foam would be left undersized
, the gap areas would have 9" cellulose with outside air sealing only.
Response to Rick Van Handel
Rick,
The idea behind a cut-and-cobble installation (or a flash-and-batt installation) is to prevent warm, moist interior air from contacting the cold wall sheathing. The layer of foam is an air barrier that separates the cold sheathing from the warm indoor air.
You can't use cellulose insulation to seal the gaps around the edges of your rigid foam, because cellulose insulation is air-permeable. It isn't an air barrier.
So, stick with canned spray foam (or, if the cracks are tiny, caulk or high-quality tape) to seal these cracks.
cut and cobble compared with spray foam
I think Dave Frank makes two good points, 1) is adhesion a potential problem for both cut and cobble and spray foam and 2) covering the bays with large foam boards, not just filling between the bays.
I have been able to fit 5 inches between bays and plan to cover the bays as well. I think expanded polystyrene works well because it can be cut close to the full width of the bay and then "shoved" into place, so that it is held by friction and also sealed with Great Stuff Pro and silicone caulk. Some has been in place for close to a full year with no adhesion problem. This is 2 layers, 2 inches each, and then a third layer of 1 inch EPS. Then at least one more full panel across the bays.
I am glad to have a project to work on during the long winter months.
Old Home with No Sheathing
"When a homeowner or builder wants to create a WRB in the stud bays of an older house that lacks sheathing."
Is this the best practice when insulating with no sheathing? I was set on using vertical strips of XPS (to create a little bit of a ventilation gap), Roxul, and a 'smart' vapor retarder.
Also, if I need a vapor retarder (climate zone 4, yes) how do you install it on a balloon frame? Past the floor, cut and tape around each floor joist? I was concerned about conditioned air from the crawl entering the wall cavity behind the drywall.
Thanks!
Response to Chris Thomas
Chris,
Yes, I think that the cut-and-cobble approach is often a good method of insulating stud bays in a house with no wall sheathing.
Q. "I was set on using vertical strips of XPS (to create a little bit of a ventilation gap), Roxul, and a 'smart' vapor retarder."
A. I don't advise your approach, because you will have no air barrier on the exterior side of your insulation. Roxul is air-permeable, and (with your approach) the performance of the insulation will be degraded by wind-washing.
Q. "if I need a vapor retarder (climate zone 4, yes) how do you install it?"
A. Perhaps the easiest way to install a vapor retarder is to install vapor-retarder paint or primer on the drywall layer.
Q. "I was concerned about conditioned air from the crawl entering the wall cavity behind the drywall."
A. The solution to this problem is air sealing, not installing a vapor barrier. (The purpose of a vapor barrier is to address vapor diffusion.) If air is entering your stud bays from the crawl space, you probably need to seal the bottom of each stud bay with spray foam before you insulate your stud bays. I suggest that you use a two-component spray polyurethane kit.
Clarification
Great point on the wind-washing. Do you recommend setting the foam back with furring strips?
I'm also a bit confused by your last response. My stud bay goes past the subfloor and to the sill plate. Are you saying to spray foam in between the floor joists that enter the stud bay?
Sorry for my need for clarification. Thanks!
Response to Chris Thomas
Chris,
Q. "Do you recommend setting the foam back with furring strips?"
A. Yes. Aim for an airtight installation of the rigid foam, but leave a little air gap between the rigid foam and the siding.
Q. "My stud bay goes past the subfloor and to the sill plate. Are you saying to spray foam in between the floor joists that enter the stud bay?"
A. It's hard to know the best way to seal the air leaks in this location without looking at it, but clearly these areas need to be sealed. It may be possible for you to install block of rigid foam in each bay, and then to seal above the rigid foam with spray foam. No matter what materials you use, the goal is to prevent any crawl space air or exterior air from entering the bottom of the stud bays.
Moreover, you also need to make sure that the rim joist is insulated on the interior with foam insulation. You can use rigid foam or spray foam -- it's your choice -- but you don't want to leave the rim joist uninsulated.
Question re: response to Dave Frank
Martin replied to Dave;
"If you want to leave your rafter bays uninsulated, and install a thick layer (or multiple layers) of uninterrupted rigid foam under your rafters, there is no reason why such an installation won't work.
Of course, it's important to list the usual caveats:
caveats ensued
My question Martin is, by installing a layer (or multiple) of rigid foam under the rafters, doesn't this prevent drying of the assembly to the interior? My understanding is one must always allow for drying of the assembly to the interior or exterior or both dependent on the design of the wall. Rigid foam (more so multiple layers) will likely impede drying to the interior (uncertain of the perm rating and effect of multiple layers on this variable). Would exterior drying be thwarted by tar paper and asphalt roofing shingles. Does the fact its not a heated space play significant role here? Thanks
Response to Sal Lombardo
Sal,
Many roof assemblies can't dry in either direction -- for example, an unvented roof assembly with a vapor-impermeable type of roofing that has been insulated with closed-cell spray foam installed against the underside of the roof sheathing.
As long as the rafters and roof sheathing are dry when these assemblies are insulated, I don't think that this type of roof assembly is particularly risky. But some builders, like you, prefer the roof assembly to be able to dry in at least one direction. I understand the logic, and you are free to design a roof assembly that dries to the interior if such an assembly seems less risky to you.
I'm currently doing this cut
I'm currently doing this cut and cobble method. I have 3/4 inch behind studs and putting 2" bwtn stud. It says on the 3/4" that it is R4 and 2" is R10. Will this be enough in zone 3, atlanta suburbs? I looked at the zone map and R requirements, I think the minimum is R13. Is this correct?
Response to Nat Hilton
Nat,
Although you didn't mention what type of wall you are working on, I'm guessing (from information posted in a comment on a different page) that you are working on insulating the interior of a basement wall. Is that right?
According to the 2009 International Residential Code, the minimum R-value for basement walls in your climate is R-5 if the insulation is continuous (in other words, not interrupted by studs) or R-13 if the insulation is interrupted by studs.
If you are installing R-4 continuous insulation -- that's the insulation between the concrete wall and the studs -- you don't quite meet minimum code requirements for continuous insulation. That forces you to try to meet the R-13 minimum requirement for insulation between studs. So R-4 continuous plus R-10 should satisfy your code inspector.
Thanks Martin,
Yes it's me
Thanks Martin,
Yes it's me again. I'm just trying to post questions in the right forum. ;) none of the rigid foam are continuous b/c the stud were already up. So, R-4 is not continuous . We had to put behind studs. A lot of work, but that part is done. Now we are putting up the 2" rigid foam, tight fit, then can spray foam (gap n crack) around edges.
Thanks again
Cut-and-Cobble worked well for this major remodel
We are nearly finished with a to-the-studs remodel of a 1950-era home on the Cape in Massachusetts. It was originally built with no insulation, so a complete upgrade was needed.
Major work started in November, when temps were too low to safely spray foam. With many changes planned to window and door openings, we also needed an incremental solution for insulation that we could install wall by wall. Cut-and-cobble was the answer. We cut XPS panels to fit each stud bay space, and carefully sealed the edges with the 'windows' version of Great Stuff, which remains flexible. This should prevent cracks as the assembly expands and contracts. A couple of photos are attached. With two layers -- 2" and 1" -- we could nearly fill each bay for a rough R value of 15 for the interior walls.
To boost insulation, reduce thermal bridging and block condensation on the sheathing, we also installed new housewrap over the exterior, covered by 2" of XPS foam board carefully sealed with Great Stuff. All of the panel joints and edges around window / door openings were also covered with a thick layer of flexible DAP 230 sealant. (For panel joints, empty a few tubes of the DAP sealant into a paint tray and apply it with a 3" paint roller. With pole extensions, it is easy to reach high up on your walls without a ladder.) A photo is attached.
In short, the cut-and-cobble approach took more time, but matched the rest of our upgrades and project schedule. We ended up with ~R25 wall assemblies and a tight air seal. The next step: 8" of closed cell spray foam on the underside of the roof, which will create a 'conditioned space' attic.
One key tip: I discovered that Great Stuff Fireblock is actually very flammable, and ignites at just 240 degrees F. We used Great Stuff Windows to seal our XPS panels -- but switched back to standard fireblocking caulk to fill and airseal holes in studs and plates. This non-flammable caulk is required for commercial buildings, and -- in my view -- is the best fireblocking solution for residential structures too.
I hope this is helpful.
Mark
hybrid venting
I am not sure I read anything clearly on the following method, but many posts have alluded to this:
When insulating an attic roof or cathedral ceiling in the cut-and-cobble manner, it has been recommended to add a cold air channel between the insulation and the sheathing. This was mentioned a few times even in unvented attic situations. Is there a benefit to leaving an gap when there is no ridge vent?
In our personal situation, we have a hip roof on a 1929 house in a zone 5b. The soffits are as good as open, although there is no technical vent there. Wood blocking was installed originally to slow airflow, but these could be pulled out with rigid foam installed. We have no ridge vent, however. If we installed blocking to the sheathing for the initial layer of rigid foam, wouldn't there be sufficient airflow the soffit to allow some kind of drying? Of course, even if this does work, it is only a backup, as the interior insulation will be air sealed.
I am asking if a hybrid method of putting an air vent channel in an unvented assembly has any merit, as a backup in case of failure of the insulation assembly to fully block air and condensation?
This cut-and-cobble method was recommended to me by both an insulation contractor and energy auditor. The insulation contractor also suggested this "peanut brittle" method of spraying an inch of closed cell foam over the cut rigid, to properly air seal it. I am very interested in avoiding spray, but will do whatever is required to make our situation work. We have access to both 3" and 1" polyiso at an excellent price.
Response to A. Bradford
A. Bradford,
Assuming you have a gable roof (and not a hipped roof that looks like a pyramid), it's quite easy to install (retrofit) a ridge vent on a roof that doesn't have one. I recommend that you do so if you are planning to build a vented roof assembly.
If you don't know how to do the work, any roofer should be able to do it for you.
hybrid venting
Martin,
That's the problem- we have a hip roof. I would happily have a vent installed otherwise.
Response to A. Bradford
A. Bradford,
As I wrote in my article, How to Build an Insulated Cathedral Ceiling, not all roofs are good candidates for the vented-roof option. If you have a hip roof rather than a gable roof, you need to go with an unvented roof assembly.
In that article, I wrote, "A vented cathedral ceiling only makes sense if the geometry of your roof is simple. You need a straight shot from the soffits to the ridge. That’s relatively easy on a gable roof without any dormers or skylights, but if the geometry of your roof is complicated — with features like hips, valleys, and dormers — it’s impossible to assure air flow through all of your rafter bays."
hybrid venting
I recall reading this. I have resigned myself to the fact our roof will be unvented.
When I read this article, I saw the following:
"The third step is to decide whether to push the foam as far as possible toward the exterior side of the framing cavity — the method that is usually used for walls with solid sheathing or for unvented cathedral ceilings — or whether you want to leave a gap on the exterior side of the framing bay — the method that is used for walls that lack sheathing or for vented cathedral ceilings. If you prefer to have a gap on the exterior side of the foam, you’ll probably want to install 1"x1" or 1.5"x1.5" sticks at the corners of each framing bay to maintain the desired gap."
I was curious about the function of leaving a gap between the insulation and sheathing on an unvented roof assembly, given that I am considering a risky method of cut-and-cobble. Even though there aren't proper vents, would this method allow potential condensation to escape via the soffit? Or do you only recommend a gap in fully vented assemblies? It wasn't clear in the article.
Theoretically I will have everything sprayed over after the fact. This was recommended to me by an insulation contractor. You mentioned the 'peanut brittle' method on here but gave no opinion of it.
An earlier post on this subject had an answer to spray 2'' inches directly on the sheathing, followed by cellulose. R values would be low but the assembly would function properly. Later I could add rigid foam to the exterior to super-insulate it.
The trouble is, I have access to all sorts of very cheap and clean polyiso in 3" and 1", and I am quite limited in funds. I could accomplish insulating to R-46 with 2 layers of 3" polyiso and then overlay the rafters with 1", all for under $1000 in material. I just want to do a good job, if I am to take this risky method.
I should mention the building has fairly fresh roofing shingles.
Response to A. Bradford
A. Bradord,
Only you can make this decision.
The right way to build a ventilated roof assembly is to provide a ridge vent at the top of every rafter bay. You can't do that, so you are breaking the rules.
Some unvented cut-and-cobble cathedral ceiling assemblies have experienced failures, presumably due to air leaks.
To some extent, you are entering uncharted territory. It's up to you to assess the risk and act on that assessment.
rigid foam insulation
Going on 2 years ago I gave up trying to find the leak destroying an addition, long before we bought the house and since the drywall ceiling was about to fall on me I tore the entire addition down to start over. My best friend is a guy who portrayed himself as a master builder. I believed him - 1st mistake. There is so much wrong with his carpentry and roofing that I'm now going around fixing what he got wrong, if at all possible. What we hadn't gotten to yet was the interior. This is my office/bedroom and as soon as I get the electric lines run it will finally be time for the interior paneling. My friend had me cut and cobble the RMatte PLUS-3 in between all rafters and studs. What a nasty job! I was ready to kill him by the time I was done. Last winter it went down to 13 degs here in East Texas so I scrambled to get full sheets of the R-Matte temporarily tacked over the studs on the interior. Since then I've decided to leave them up, better secured, and install the 1/4" paneling over top of them. I'm 69 yrs old and I cannot handle sheets of drywall but I'm afraid the thin paneling will warp without a solid backing This idea engendered a nearly friendship-ending email fight. He said it wouldn't work and I, having looked it up on the website for RMAXINC and they gave instructions how to put it up on top of interior studs, stood my ground. He finally said he'd do it my way and not say anything when it failed. Big surprise - I'm doing it myself, so there. . . Now I come across this article and comments and I'm feeling very deflated! Was my know-it-all friend right all along? This is a pretty big crow to try to eat! (the cut and cobble RMatte is still in the back of the studs right on the siding and caulked around)
Response to JoAnn Dibeler
JoAnn,
You've told us a story about your cut-and-cobble job. However, I don't understand your question.
Can you please re-state your question?
XPS or EPS?
I live in Zone 7 (Juneau, Alaska) and this method is intriguing. I was thinking of using this cut-and-cobble method as we remodel our home over the next few years and then flash fill the remainder of the wall cavity with closed-cell spray foam. However, your article raised two questions in my mind.
#1: Is there a disadvantage to using the cut-and-cobble method to install 4 inches of foam board (two 2" layers with staggered and sealed seams) and then filling the remaining 2" with spray-foam to ensure a seal)? It would seem to me that there would not be a disadvantage as long as I friction-fit the foam board and sealed all edges and the two-layers to eliminate air voids and penetration. Am I missing a consideration other than risk of error?
#2: All of Alaska is seismically active. Is the added strength of XPS such that it would be superior to EPS in a cavity installation to also add strength and durability to the entire structure? Or do you think I am overthinking this? Heck, what do you prefer in this method regardless, XPS or EPS?
Response to Emil Mackey
Emil,
Question #1: The disadvantages of this method are listed in my article. The main disadvantage for walls is that this method is very labor-intensive. The main disadvantage for unvented cathedral ceilings is the possibility that cracks will open up, leading to possible mold and rot.
#2. I think that you are overthinking this question. I don't think that XPS has any seismic advantages. From an environmental perspective, EPS is preferable to XPS because it is manufactured with a more benign blowing agent.
Cut and cobble versus partial insulation over-roof
Martin,
Like many others who have responded to your article, I read your cut and cobble description with a good deal of interest. We have a master BR addition that is currently framed and roofed but yet to be insulated. My wife really wants a cathedral ceiling (we have rafters versus trusses so this would just require removing some of our ceiling joists and reinforcing those that remain). At any rate I've been debating how to insulate the ceiling safely. It has a hip roof complicating venting. Personally, I'm just not comfortable with an unvented cut and cobble in a cathedral ceiling (which you also advise against). It seems like an awfully risky gamble considering there is no way to inspect for ongoing condensation and water damage.
In another article you wrote (How to Build an Insulated Cathedral Ceiling), I get the impression that insulating the roof deck would be the better/best solution. My hesitation is the amount of work and money required to retrofit the entire roof just to address the needs of one 500 sqft room. I also hate to dump the current system as I spent several painstaking weekends two years ago crawling around our attic air-sealing. I also added R-30 batts throughout (so the attic floor is fairly air tight and well insulated). Our asphalt shingles are ~15 years old. Not new but also not yet ready to be replaced. In short, over-roofing with insulation seems like a drastic and expensive change to address a vaulted ceiling in one room.
Here is my question. I'm wondering if there is any reason (other than aesthetics) I could not over-roof with insulation strictly over our new master - leaving the rest of the house with a traditional vented attic? We're in a ranch with a relatively simple roof line so it would definitely be noticeable that a portion of our roof was 6" higher/thicker than the rest. However, I would sacrifice aesthetics for the piece of mind knowing that our rafters were not secretly rotting. Further, my guess is the expense, while more than cut and cobble (which I'm not comfortable with), would not be much more expensive than closed cell spray foam (which I am). In short, if I'm going to bite the bullet and spend more than a cut and cobble job, it seems like over-roofing with insulation is the better approach. (the last sentence is actually a question)
The only real drawback I can see with a partial over-roof approach is the possibility of snickering neighbors laughing at my two-tiered roof line. However, they'll get over my split level roof a lot quicker than I would get over $20K worth of water damage to our rafters. The scope of work is small enough that I could probably handle a lot of the soffit retrofitting myself (another benefit as my guess is roofers will price their bids at a premium given some of this will be a pain in the butt).
Do you see any drawback to this partial over-roof idea?
Thank you,
Brian
Response to Brian Gray
Brian,
Q. "I'm wondering if there is any reason (other than aesthetics) I could not over-roof with insulation strictly over our new master - leaving the rest of the house with a traditional vented attic?"
A. No. Just make sure that you have considered details to make sure that the thermal envelope (the air barrier plus insulation layer) is continuous. Tricky transitions occur at the top of the wall (where the wall meets the roof) and at the kneewalls connecting the cathedral ceiling/roof with the insulation installed on the attic floor.
renovating two walls, suggestions welcome
Hi, first, please forgive me for the wall of text, I just want to be sure I give as complete a picture as possible. I know some or all of these points have been made already, but I just wanted to be sure I completely understand what’s been said, and am applying the correct logic to my project.
My situation:
- In the middle of gutting a kitchen/bathroom each with an exterior wall with all plaster and existing fill removed.
- Located just outside boston (not on the water)
- building is multi family, work is being done on the 2nd floor with kitchen/bathroom above and below
- building is old and very drafty. Originally had zero insulation anywhere. I had cellulose blown in 8 years ago. building is clad in two layers of wood (not sheathing, just boards), then asphalt shingles, then vinyl.
- I don’t plan to add house wrap or any exterior insulation because the asphalt shingles supposedly have asbestos, so I don’t want to touch that.
- I removed all the existing cellulose from the two walls (kitchen and bath) during demo.
- stud bays vary hugely in width (of course! it’s old and badly built). All are 3.5” deep
- it’s balloon framed, meaning I can see the cellulose stuffed into the stud bays on first and third floors
- I was going to use the two-part “froth pak” 650 from lowes to fill all the stud bays--that’s too expensive considering I’d likely do a bad job.
- I was thinking of hiring a contractor to spray (closed cell) foam into the cavities. but 1) my understanding is that it’s too cold in Boston in January and 2) the work is going in stages, so I’m not really able to arrange a single time for the contractor to do all the work
- anyways, spraying that much foam… I honestly don’t like the idea of releasing that much chemical into an occupied house.
My plan: stuffing each bay with layers of foam board and spray foaming around the edges (stack-of-pancakes):
- first 2” XPS against the outside
- then 1 ⅜ foil-faced polyiso (tuff-r from dow)
- then foam around edges with great stuff window and door foam (because it will supposedly move with the house--right?).
- ½” drywall on top. Some sections will be ½” cement backer and tile (around tub, which is up against the outside wall--unfortunate, but no choice here)
Questions:
- foam board choices--ok? I’m concerned that the foil face will trap moisture somehow--particularly in the bathroom, particularly behind the cement board, which will be sealed and painted with redguard, which supposedly waterproofs the shower walls. Should I use just XPS/EPS in the bays behind the cement board? In the entire bathroom? Everywhere? I’d like to get the best R-value, but let’s be honest, this house is not going to be tight, EVER, so I’ll settle for what I had before I tore out my walls: relatively warm, with no mold/persistent moisture issues.
- the tuff-r board is foil-faced on both sides. Dow site claims there’s some difference between the facings, but for the life of me all I can see is one side has writing on it… Am I blind/stupid?
- assuming the board choices are ok, how about that foam spray. I was planning on just cutting the boards loose in the stud bays (1” gap around edges) and spraying them in with the window/door foam because it’s flexible. Should I go smaller on the gaps, like ½”? Would the “gap filler” foam be a better choice for some reason? The gap filler seems to have some sort of fireblock chemical which I tend to avoid when I can, but let me know if I’m being silly.
- treating the transition from the existing cellulose in the bays above/below the foam/spray I’m installing. Anything to be careful about? I was just going to stuff the boards up against the cellulose and spray around the edges
Anything else I am overlooking? I’m new to foam and had started to buy different materials just to get a feel for it when I stumbled on your site. Obviously not the best “plan,” so any help you can provide is so greatly appreciated.
Thanks and happy new year!
Response to MZ
MZ,
1. It's too bad that you removed the cellulose; everything was probably just fine before you emptied the stud bays. (But perhaps you had to do some electrical wiring?)
2. If you care about the environment, EPS is more environmentally friendly than XPS. So I would suggest that you install EPS instead of XPS.
3. The size of the gap around the perimeter of each piece of rigid foam isn't too important, as long as the gap is wide enough for you to insert the nozzle of your canned foam dispenser.
4. Don't worry about trapping moisture. Don't worry about which way to orient each piece of rigid foam. Just pay attention to airtightness -- that's all that matters.
5. Don't overthink the choice of canned spray foam. Careful workmanship is the most important variable.
@Matrin
Thanks Martin!
1. yeeeup, sure wish I had kept that stuff. I couldn't in the bathroom due to some structural issues caused by old (bad) work, but kitchen... dang, should have just left the walls up and covered them with new sheetrock.
2. I do care about the environment, but I also care about getting a material that works well long-run. My impression of EPS is that since it's open cell, it is prone to developing mold. But now that I think about it, I'm guessing that's only if you create vapor barriers around it, which will not be the case here. I just want to be sure I'm not creating a headache for myself.
3.Sounds good
4. Just to be clear: are you saying I shouldn't worry about trapping moisture because I should use EPS which won't trap moisture? Or even with the closed-cell boards I picked up already I shouldn't worry about it. Since I'm new to this, I've been kind of alarmed by all the stories of trapped moisture due to wrong material selection/bad installation. Just want to be clear why I should not worry about trapping moisture. I will follow your advice about EPS, but on the chance that for some reason I can't get EPS boards from my local center, I want to be sure that the materials I've already gotten (and that are stocked to the ceiling at my local HD) are going to work ok for my application in case I have to use them.
5. Gotcha.
Thanks very much, Martin! Your article and comments have been incredibly helpful to me!
Response to MZ
MZ,
To have a moisture problem in a wall assembly, you need moisture. There are two main directions from which moisture can enter a wall: from the exterior and the interior. (It's also possible that a plumbing pipe in your exterior wall might leak, but you shouldn't have any plumbing pipes in your exterior wall.)
The way to keep exterior moisture out of your wall is with good siding, good flashing, and a water-resistive barrier (WRB). The best wall assemblies also include a ventilated rainscreen gap between the back of the siding and the WRB.
If there are flaws in your siding, flashing, and WRB, and your sheathing gets wet, it should be able to dry to the exterior -- unless, of course, the wall has a gross defect, in which case your wall is doomed. In any case, the rigid foam that you plan to install does not affect this drying mechanism.
The main mechanism by which interior moisture enters a wall assembly is by piggybacking on exfiltrating air. So if you do your best to keep the drywall layer airtight -- which means limiting air leaks at electrical boxes -- you'll stop this mechanism. Again, the foam layers shouldn't cause moisture problems.
@Martin
Got it--thanks again! I will use EPS with confidence and I'll be very meticulous about the seams.
cut and cobble wall
Martin I gutted my 1955 main bath in a brick veneer ranch in windsor heights, iowa. There is a 1 inch space behind brick then celotex like brown board on frame (2x4). Am planning on using stack of pancake method between the studs(closedcell foam boards). Then a 3/4" layer of foam over the studs sealed well every step of the way. This outside wall is 7' long 8'high. And will have tile backer and tile 3/4of the way up. Any issues with this?
Response to Greg Philliips
Greg,
If your workmanship is good, there is no reason why your suggested approach won't work.
Poly-iso cobble vs closed cell spray, w/ exterior foam in place
Martin, this is exactly the discussion I was looking for, so thanks! I'm weighing insulation options for between rafters in a walk in attic space. We're in Western MA in a 100 year old balloon framed house, 2x4" walls (with some vermiculite in the cavities, but that's another story). This past summer we replaced the shingle roof, and in doing so we stripped to decking, and built up with an assembly of 2 layers of 2" foil faced poly-iso, with seams staggered and taped, and then furred up 1" to a new plywood deck and standing seam metal roof to install a PV array.
I'm now looking into the options for the underside of the roof, and am considering poly-iso over closed cell spray foam, as the cure and offgassing issue is a concern for both my apartment and the rental unit in our two family home. Plus, I'm guessing there's cost benefit, as I'd outsource spray foam to pros but think I could handle the cobble job myself with the help of friends or low-hourly wage assistants. I'm familiar with the methods, already used on a rim joist last winter.
Rafters are full dimension 2x6, but were sistered with nominal 2x8 for structural reinforcement as part of the roof build. This means I could easily get a 3 pancake stack for 6" of poly-iso inside and 4" outside (r-70?) but I wanted to get input on the impact the 3.5" of wood (from the two sistered rafters) would have on that plan.
Good discussion. We continue
Good discussion. We continue to consider insulating a cathedral ceiling. Foam over in a few years is one option. but very expensive as someone else has pointed out. We are also considering working from the inside sooner, and there is lots of food for thought here. We have 14" rafter bays which now have 12" fiberglass batts and t&g boards beneath with no air sealing. There are soffit and ridge vents, but we don't know if there are baffles securing the venting channel. The roof has a couple of dormers, but these are not really part of the cathedral roof and are more conventionally insulated.
We are conflicted as to how to best do this. We'd like to avoid the expense of cc foam. Any suggestions/advice? Is there are way or sense in reusing the batts in a new format? In any arrangement it seems prudent to do an inch or two of rigid foam beneath the rafters for air sealing and reduction of
thermal bridging, as well as for increased R. We would then put t&g boards back up.
Response to Howard Gentler
Howard,
Here is a link to an article that lays out all of your options: How to Build an Insulated Cathedral Ceiling.
Cathedral ceiling insulation retrofit...
Martin and other advisors...I have read your excellent article on cathedral ceilings, more than once and the accompanying links. Sorry my post didn't sound like it. I think I need to ask more specific questions/advice.
As I mentioned, we are considering the foam over for an insulation retrofit, and I've gotten good info from this site, much of it from Dana. But we are leaning more toward an interior effort now. The foam over would be very expensive (we need R-25, so 5 or 6 inches of foam, depending on type)and a few years off. There are dormers that don't need foam (not cathedral), and the details from the extra thickness, trim and otherwise would be daunting, including the poss of different levels on the roof. (I read a blog by Dr Joe of BSC about doing a foam over on his house and the challenge and expense of making the trim look good).
If we go unvented, it sounds like a couple of inches of cc foam on roof sheathing underside would be best. We could then return the 12" batts, filling up the rafter bays. Is it then okay to do rigid foam on the underside of the rafters? Like 2" of EPS, carefully taped(this will add some R but is much more for the air sealing), furred over at the rafter undersides as nailers for the t&g boards? Are there concerns?
If the spray foam is too expensive, my understanding is that 2" of rigid foam could be pushed against the roof sheathing and carefully sealed at the edges with tape, caulk, spray foam or all in combo. Is that correct? I should avoid foil faced poly-iso in this stickup to allow for drying to interior, correct?
If we were to do vented (vents already there), could that stack up I mentioned above be essentially the same, -starting 2" down with rigid foam, pushed against retainers nailed to the rafters? Then the fiberglass batts, slightly compressed to 10", and then the rigid foam below for air sealing. Or is this not an appropriate stack up with vented? Do you have an opinion on whether we should do the vented or unvented? I know of your concerns with vents not working with complex roofs, but the part that is cathedral is on one end of the house and not impacted by dormers, which are in the center of the house. And, the rigid foam spaced 2" from the deck underside would improve upon the current vent channel and make it consistent.
Thanks for any advice.
Response to Howard Gentler
Howard,
Q. "If we go unvented, it sounds like a couple of inches of closed-cell foam on roof sheathing underside would be best. We could then return the 12-inch batts, filling up the rafter bays. Is it then okay to do rigid foam on the underside of the rafters?"
A. No. You should re-read my article, "How to Build and Insulated Cathedral Ceiling." The approach you describe is the flash-and-batt approach. If you follow this approach, building codes require you to install a foam layer that meets the minimum R-value requirements spelled out in Table R806.5 of the IRC, and (if I understand you correctly) you need R-25 for this layer in your climate zone. That means that you need about 4 inches of spray foam, not "a couple of inches."
Q. "My understanding is that 2 inches of rigid foam could be pushed against the roof sheathing and carefully sealed at the edges with tape, caulk, spray foam or all in combo. Is that correct?"
A. Not quite. I don't recommend the cut-and-cobble approach for unvented cathedral ceilings; this article explains why. (There are reports of failures.) In any case, 2 inches of rigid foam isn't enough for the foam-and-batt approach.
Q. "If we were to do vented (vents already there), could that stack up I mentioned above be essentially the same, starting 2 inches down with rigid foam, pushed against retainers nailed to the rafters?"
A. Yes. These details are explained in my article, "How to Build an Insulated Cathedral Ceiling."
Q. "Is this not an appropriate stack up with vented?"
A. It will not only work -- the vented approach is better than the unvented approach.
Q. "Do you have an opinion on whether we should do the vented or unvented?"
A. Vented is better than unvented -- especially if your unvented approach uses cut-and-cobble insulation.
Cathedral insulation...
Thanks Martin for noting my misunderstanding. Keeps us from making that mistake, and I see where you mentioned that in your article (R being the same as what would be needed for an above deck foam over).
Do you advise using EPS in the two places we would be using rigid foam, - at top as vent baffle, and under rafters for air sealing, as opposed to XPS? And to avoid poly-iso?
Response to Howard Gentler
Howard,
Q. "Do you advise using EPS in the two places we would be using rigid foam, - at top as vent baffle, and under rafters for air sealing, as opposed to XPS?"
A. EPS would be better than XPS, because EPS is more environmentally friendly. XPS is manufactured with blowing agents that have a high global warming potential.
Q. "And to avoid polyiso?"
A. Polyiso is relatively benign from an environmental perspective, so you can use polyiso if you want. If you intend to use the rigid foam as a ventilation baffle, it probably makes sense to choose a material for that location that is somewhat vapor-permeable (like EPS or polyiso with a vapor-permeable facing) rather than a foam that is vapor-impermeable (like foil-faced polyiso).
1915 home insulation upgrade
Martin, I am working on upgrading the energy performance of the upper (2nd) floor of a bungalow style wood framed wood siding home in lower zone 3 (georgia). The exterior cladding is the original heart pine lap siding without any sheathing. I will be gutting from the interior - exterior lap siding will remain in place. For walls - I am considering options that include cut and cobble with 1" - 2" of rigid EPS or XPS sealed between the studs. Does there need to be a gap between the rigid insul. board and the lap siding? If so - what dimension? The remainder of the 2x4 stud bays would be filled with mineral wool batt insulation. Alternatively, I've considered filling the stud bays with mineral wool batts and sheathing the interior of the studs with eps or xps riigid foam board and overlaying with drywall to create a two layer airtight drywall layer from the inside that would dry to the outside.
I have a portion of the ceiling that is a normal vented attic and a portion that is a cathedral ceiling. In the normal vented attic areas (flat ceiling but very limited head room accessibility in attic) is there any advantage to sheathing the ceiling with rigid foam board below the ceiling joists infilled with batt insulation and overlaying with drywall as opposed a thicker layer of more inexpensive attic batt insulation (no rigid foam overlay). I'm considering batts because attic is so shallow and want to insulate from below.
In the cathedral areas - I plan to ventilate the roof sheathing using baffles, then fill the rafter bays with mineral wool batts, then overlay with a layer of rigid foam insulation to get up to R30 and overlay with drywall to create an airtight assemble that is vented above. These cathedral areas vent to the main attic area and then to gable end vents.
I also have some knee walls that will be infilled with mineral wool batts and drywall from the interior. On teh attic sideof the kneewalls - I am considering a rigid insulation board to assist in air sealing and additional R value. Attic areas on the outside of the kneewalls will be vented.
Is there a good solution to insulation/airsealing some areas of the first floor ceilings that are painted wood beadboard ceilinsg with a vented attic space above. Currently a minimal amount of old blown in mineral wool insulation is in place. I was considering adding R30 mineral wool batts - but that doesn't address air tightness in the beadboard ceiling.
Response to Roman Stankus
Roman,
Q. "Does there need to be a gap between the rigid insul. board and the lap siding?"
A. Yes. This method is described in the article: "The cut-and-cobble method can be used .... when a homeowner or builder wants to create a WRB in the stud bays of an older house that lacks sheathing." The article also notes, "The third step is to decide ... whether you want to leave a gap on the exterior side of the framing bay — the method that is used for walls that lack sheathing. .... If you prefer to have a gap on the exterior side of the foam, you’ll probably want to install 1"x1" or 1.5"x1.5" sticks at the corners of each framing bay to maintain the desired gap."
Q. "If so - what dimension?"
A. The answer was given in the article -- either 1 inch or 1 1/2 inch. (See above.)
Q. "Is there any advantage to sheathing the ceiling with rigid foam board below the ceiling joists infilled with batt insulation and overlaying with drywall as opposed a thicker layer of more inexpensive attic batt insulation (no rigid foam overlay)? I'm considering batts because attic is so shallow and want to insulate from below."
A. Either way will work. Adding cellulose on top of the existing insulation is likely to be the cheapest solution, as long as you have enough room in your attic to get the R-value you are looking for.
Q. "Is there a good solution to insulation/airsealing some areas of the first floor ceilings that are painted wood beadboard ceilings with a vented attic space above?"
A. There are two possible solutions: (a) Remove the beadboard ceiling, install drywall, tape the drywall, and then re-install the beadboard ceiling, either re-using the old boards or installing new boards; (b) Temporarily remove the insulation above the beadboards, so that the back sides of the beadboards are exposed, and install spray polyurethane foam above the ceiling.
Torn over spray foam
I am building a small post and beam house (<400 ft^2) on a budget. the wall construction will be something similar to "remote system" and "wrap strap" method with recycled foam board insulation, so there an uninterrupted insulation air barrier enclosing structure. but challenge is that i really want have cathedral ceiling. are no perforations through roof or slope interruptions whatsoever--it's just going simple gable design light colored metal roof. my original plan was use true 2x12 rafters with, as you say, "cut cobbled" rigid fit in between then taped (with 2" gap above them for venting), after reading many of your articles this seems extremely risky.
However, I have the opportunity to have closed cell spray foam sprayed for me at $0.50 a board foot, in which case I would have a few inches sprayed and then meet the required R-value with air-permeable insulation (I'm in climate zone 5). My only reservation is that spray foam seems like it could be a serious health hazard. From what I've read--assuming it is sprayed properly and allowed to off-gas for the right amount of time--it should not cause any issues in the short term, but the long term health effects are still up in the air. It only takes cursory look at history to see that it is riddled with cases of industry assuring consumers that questionable products are safe (and consumer protection agencies condoning such products without proper long term research) only for such products to later be attributed to serious health problems.
I'm not going to ask you to allay my fears, but supposing I were to use sprayfoam, would there be a way to reliably "seal" it into the rafter bays to reduce the chances of harmful fumes entering the living space? I was thinking of some sort of heavy duty plastic stapled immediately below the rafters (and above the tongue-in-groove ceiling finish), but perhaps this would need to be so much of an air barrier itself that it would be redundant.
Second, I know the contemporary opinion seems to be that a spray foamed (closed cell) roof does not require roof ventilation, but I wonder how much evidence there is of unvented roofs holding up over the long term. Spray foam hasn't been around for too long and it just seems that while any issue with the air barrier could cause problems, it could be a disaster if coupled with an unvented roof. Are there risks with using closed cell spray foam to insulate a roof and then venting it anyway?
Thanks
Response to Claython Mclaw
Claython,
1. If you have access to recycled rigid foam insulation, why not use the same type of insulation on your roof? (I'm not talking about the cut-and-cobble approach.) Install several continuous layers of rigid foam (with staggered seams) above your roof sheathing, followed by ventilation channels created by laying 2x4s on the flat, then a layer of OSB or plywood, and then your roofing.
2. If you prefer to install spray foam from the interior, you can, but this approach results in inferior performance, because you won't be addressing thermal bridging through the rafters.
3. I wouldn't count on any air barrier material to keep out the odors from badly installed spray foam.
4. Jobs with stinky spray foam are very rare. Moreover, these problems show up immediately or not at all. If there are no odors after 48 hours, there is no reason to believe that there ever will be odors in the future.
5. No matter what type of foam insulation you choose to install, it's always a good idea to have a vent channel above the insulation layer.
Thanks for the suggestions.
Thanks for the suggestions. I think I will go with your 1. Even assuming I can get spray foam at cost, it is cheaper. However I may see if I can find a metal roof that will fasten to horizontal strapping (overtop the vertical strapping) because it would be expensive to put down a second roof deck (especially since I keep reading that I should use plywood instead of OSB due to screws supposedly not holding well in OSB)
Unvented Attic
Am I late to the party?
I live in 3B zone, (Southern California) in a 100 year old house. The house is unvented and with no insulation. The main house gets hot and cold, but it isn't too bad. The attic bedroom gets scorching however all the wood and framing is in excellent condition.
A section of the unvented cathedral attic was finished into a 250sq ft bedroom that has kneewalls and ceiling done with celotex boards (put in roughly 60 years ago), however it was not insulated beyond that and gets incredibly hot. The roofing is asphalt shingles on top of planks – no plywood sheathing -- with roughly 1/2inch between each plank.
The roof does not leak, but will need updated sheathing and maybe some insulation on top of that in the future, however new roofing is out of my budget for a few years.
The attic is being rewired due to safety issues and the old battered celotex boards were removed. I want it to be kept as a living space to generate some rental income, so my questions are:
1. For this climate, if I cut-and-cobble rigid between the rafters and insulate behind the kneewalls of just this room, will this help with the hot (much hotter than the downstairs) attic room issues I have, without new roofing, or insulating the entire space of the attic? (for now)
2. The rafters only have a 4-inch depth, can I put rigid foam between and then a layer over the rafters, or should I add some depth to the rafters?
3. When the roof is eventually redone, can insulation be placed atop the new sheathing and the attic room insulation is kept as is? Or should that work be redone.
If one was contemplating
If one was contemplating disregarding the problems that may arise from a cut and cobble installation in a cathedral ceiling, can you tell me what needs to be addressed in terms of fire rating? What if anything, must be applied to the surface of the rigid foam on the interior before finishing with drywall or paneling?
Thanks.Kim
Response to Kim Dolce
Kim,
It sounds like you're planning to ignore my advice, but I'll repeat: Don't use the cut-and-cobble method for a cathedral ceiling unless there is a ventilation channel between the uppermost piece of rigid foam and the roof sheathing.
If the rigid foam is protected on the interior side by a layer of 1/2-inch drywall, the drywall meets the code requirement for a thermal barrier. Paneling is a different matter entirely; you'd have to talk to you local building department to see if the paneling you are thinking of using would be approved as a thermal barrier.
Response to Joe Soda (Comment #76)
Joe,
Q. "If I cut-and-cobble rigid between the rafters and insulate behind the kneewalls of just this room, will this help with the hot (much hotter than the downstairs) attic room issues I have, without new roofing, or insulating the entire space of the attic (for now)?"
A. Probably. But it's hard to know -- you may need an air conditioner. Note that you can't cut-and-cobble between the rafters unless you first make sure that every rafter bay has soffit vents and a ridge vent. The cut-and-cobble method can't be used for unvented cathedral ceilings -- my article explains why.
Q. "The rafters only have a 4-inch depth. Can I put rigid foam between and then a layer over the rafters, or should I add some depth to the rafters?"
A. Either approach can work -- assuming, as I said, that you are talking about a vented assembly. You can't do that with an unvented assembly. This approach (and several more) are described in my article, How to Build an Insulated Cathedral Ceiling.
Q. "When the roof is eventually redone, can insulation be placed atop the new sheathing and the attic room insulation is kept as is? Or should that work be redone?"
A. If you insulate the cathedral ceiling using a vented approach, you'll need to seal the vent openings once you put rigid foam above the sheathing. It might make more sense (now) to insulate from the interior using an unvented approach. That approach (as my article makes clear) requires the use of spray polyurethane foam.
You realize Joe posted that over a year ago, right? @ Martin
76.
JAN 10, 2016 9:40 PM ET
(2016 not 2017)
Response to Dana Dorsett
Dana,
Occasionally, questions go unanswered on GBA, especially when things get busy. I don't like it when that happens. My parents taught me, "Better late than never."
If you find a library book under the sofa that's been there for 12 months, you should return it to the library.
Martin, a brief flirtation
Martin, a brief flirtation with the idea, but no, I will not be disregarding your advice.
Kim
Insulating above grade basement wall
Martin,
Just bought a 1910 house in Seatlle with a walk out basement. Basement needs insulation as it has none and is very drafty. I removed the lath and plaster and found no sheathing between the studs and external clap board, only what appears to be tar paper in good condition.
Question is now what to insulate the stud bays. Cut and cobble sounds plausible but Im unsure of where to put the vapor barrier, if at all? thicknesses for rigid foam? Fill the bays with rigid foam or go with a rigid foam and fiber glass hybrid? Do I need an air gap between the rigid foam and tar paper? if so how big? etc.
Your thoughts?
Spray foam is not feasible due to budget and access.
Thanks,
Craig
What siding type?
What's on the exterior side of the tar-paper, and how much roof overhang to do you have? It matters, relative to whether you absolutely need to build it with an air gap, but a minimum of 3/8" air gap would be required by code up in B.C..
In zone 4C you don't normally need a vapor barrier or vapor retarder other than standard interior latex paint on wallboard, as long as it's reasonably air-tight. If putting low-permeance foam board on the exterior of fiber insulation you don't want anything tighter than latex on the inteiror side, but you'll need at least 15% of the total R to be the foam. eg:
If it is framed with full-dimension 2x4s you have 4" of depth- if you slip in some half-inch polyiso that would be R3, and you'd have enough space for standard 3.5" thick R15 rock wool or fiberglass batts for a total of R18. The R3 would then be about 17% of the total, which is fine. You could put thicker foam in there and compress R13s if you want more margin.
RE: Insulating above grade basement wall
Exterior to the tar paper is the wood (cedar?) clap board that has been painted on its exterior. Roof over hang is too high up to measure so I'm guessing 24" Overhang is 2 stories up so I dont believe it offers much protection for the area I'm insulating. Is there a code/requirement for an airgap in Seattle WA?
Some background: I'm doing all of this because basement is extremely drafty. Basement wall is wood above grade and cement above grade on 1 side of the house. Cement wall is thicker than the wood above. We plan to have the entire basement finished so what Im doing right now is temporary and will be removed or improved when basement is finished including bringing cement & wood to same thickness for a flush wall.
That said: I will cover the interior of the insulation with drywall but dont to paint (garage finish?) Does this change any recommendations re: a vapor barrier. Or should I skip the vapor barrier and paint the drywall?
Other notes/questions:
bays are 3.5" deep
I thought compressing FG wasnt advised?
Should I seal the interior of the concrete? if so with what?
Dana, are you with GBA or just a helpful commentor?
Thanks,
Craig
Cut-and-Cobble Insulation for my assembly?
I'm also considering Cut-and-Cobble Insulation for the 1924 - 1000 sq.ft flat-roof bungalow I bought 2 years ago. Attached is my actual structure, which has zero insulation right now (zone 5, brrrrr!). There is 2 sections over the ceiling, one that is unvented and level, and on top of it one that is vented with 2 goosenecks with no intake and has a slight pitch to drain the water in the center of the roof.
I figured the best way to insulate this roof would probably be from the top, adding 7-8 inches of polyiso, a deck and a membrane to cap it all, but that is expensive, and since the actual tar and gravel seem to hold up well, and that I planned to do intensive interior remodeling that will require the ceiling tearing, I'd like to have a from-the-inside alternative.
If I tear down the ceiling (blue), I guess I could have the plank deck (green) sprayed with closed cell foam from underneath for R20, but I don't really like the idea of the whole chemical thing inside the house, even if I understand that the failure rate is very low (when choosing a certified contractor).
I then considered replacing the ceiling (blue) with a continuous 3inch of XPS under the joist, then a reflective / vapour barrier paper, then furring and gypse. The unvented sections in between each joists (red) would be filled with cellulose, leaving a 3-4 inches gap between the top of the lose-filled insulation and the plank deck (green). But I read several warnings how difficult it is to completely seal the vapor coming from inside the house, and since each independent sections would have no ventilation at all, the condensation risk on the deck (green) might be too great (?).
Then I read about the Cut-and-Cobble technique, which seem like a good alternative to the spray closed cell foam with less active chemical involved, and I could do it myself. I would install two staggered layers of 3 inch rigid foam in between each joist (red), right under the plank deck (green). Each rigid foam board seam would be taped, each sides would be sealed with canned foam. Then the rest of each cavity (5inch left) would be filled with cellulose at the same time the new ceiling would be installed, with no vapor barrier whatsoever so the assembly can dry from the inside (that is how I understand it anyway).
Am I on the right track here? Considering my actual situation, is this the best approach for a from-the-inside solution?
Thxs!
--Francois Desrochers
.
Response to Francois Desrochers
Francois,
The short answer to your question is that you have to follow the advice provided in this article: Insulating Low-Slope Residential Roofs.
The longer answer would inform you that the type of ventilation shown in your sketch does not meet the requirements to ventilate a low-slope roof. You need a "doghouse" vent in the middle of the roof, and lots of air intakes at the roof perimeter.
Finally, the cut-and-cobble technique has been associated with failures (moisture accumulation) unless there is robust ventilation above the insulation. I don't recommend cut-and-cobble for this type of roof assembly.
Hey Martin
Actually I thought I was following the recommendation from that article Insulating Low-Slope Residential Roofs, more precisely the section "What if you don’t want to depend on roof venting?". The poor ventilation of the top section of my roof, and the inexisting ventilation of the lower section, the one I have access from inside, had me believe I should consider the problem from an unvented perspective. I mean, even if I do improve the ventilation of the top section, it doesn’t connect to the bottom one where the insulation would be.
If this make sense, I was looking at the last alternative for unvented roof in that article:
"You can install a more moderate thickness of closed-cell spray polyurethane foam on the underside of the roof sheathing, supplemented by a layer of air-permeable insulation below that."
In my case though, the closed-cell spray polyurethane foam would have been replace by the cut-and-cobble (6 inches thick) directly on the underside of the wood deck (green), and the air-permeable insulation would have been the cellulose below that.
I like the idea of improving the ventilation of the top section of the roof with dog house, but this section would still be outside of the thermal envellop, kinda roof over the roof.
One thing that confuse me is that most low-slope roof diagram I see only have one section, not two like mine. Here’s an example from the article you point out -- [see second illustration].
Only one space between the drywall and the roof sheating. The unvented space I have (between blue ceiling and green deck) is almost always inexistent in the assembly I see.
Thxs Martin.
Response to Francois Desrochers
Francois,
My advice is unchanged. The use of the cut-and-cobble technique in unvented (or poorly vented) roof assemblies has been associated with moisture accumulation and rot. You don't want to use the cut-and-cobble technique for this type of roof.
You have three choices:
1. Install closed-cell spray foam on the underside of the layer you have labeled "Deck (wood planks)." You can either install all of your insulation as closed-cell spray foam, or you can install a combination of closed-cell spray foam and fluffy insulation, as long as the R-value of the spray foam layer meets the minimum R-value required for your climate zone, as explained in my article on low-slope roofs.
2. Improve the ventilation details as explained in my article on low-slope roofs, and then insulate with fluffy insulation.
3. Install rigid foam insulation above the roof sheathing.
Hey Martin
Hey Martin,
Ok, I understand #1 and #3, but about #2:
since the channels between red joist, below the wood plank deck (green) are not communicating with the above section, which is ventilated (poorly but still), do I need to improve the top section ventilation (doghouses) AND create some kind of openings in the wood plank deck (green) to help ventilate the below section, or the whole assembly will dry just as well?
I get that the deck (green) might not be totally air sealed in the first place, but would it be enough to dry any condensation happening on the underside of the cold deck (green) when moisture would actually hit it?
Do I need to create some openings between top and bottom section to help the air flow of the bottom section?
Thxs
Response to Francois Desrochers
Francois,
As I explained in my article on low-slope roofs, you have two choices: you can create an unvented assembly (an approach that requires either rigid foam above the roof sheathing, or closed-cell spray foam below the roof sheathing), or you can create a vented assembly (an approach that requires a central "doghouse").
In my Comment #89, #1 and #3 referred to unvented approaches, while #2 referred to a vented approach.
There is never any reason to create holes in the green layer in your assembly. Airtightness is good.
If you want to create a vented assembly, you need (a) a vented doghouse, and (b) adequate openings near the perimeter of your "attic" to allow exterior air to enter the attic.
Response to Martin Holladay
Ok I see.
When you say:
"If you want to create a vented assembly, you need (a) a vented doghouse, and (b) adequate openings near the perimeter of your "attic" to allow exterior air to enter the attic."
I assume those perimeter openings would be at the top section level, not at the below section level where the insulation would be installed from inside, correct?
So in your expertise, the wood plank deck (green) separation would not prevent the below section with insulation to dry properly if the top section is properly vented, am I understand this correctly?
.
Response to Francois Desrochers
Francois,
Q. "I assume those perimeter openings would be at the top section level, not at the below section level where the insulation would be installed from inside, correct?"
A. Correct.
Q. "So in your expertise, the wood plank deck (green) separation would not prevent the below section with insulation to dry properly if the top section is properly vented. Am I understand this correctly?"
A. You never want to encourage water vapor to flow from your warm, humid interior to your cold, dry attic. The point of the insulation layer and air barrier is to create a barrier that separates the warm, humid interior from the cold dry exterior. Barriers are good. This barrier should be airtight and should have a high R-value.
The purpose of the ventilation in your attic is to keep your attic dry, not to remove moisture from your house. For more information on these concepts, see All About Attic Venting.
Follow-up questions
Hey Martin,
so after much discussion with people around me, I have a some few follow-up questions if you don’t mind.
Concerning method #1, when you say:
1. Install closed-cell spray foam on the underside of the layer you have labeled "Deck (wood planks)." You can either install all of your insulation as closed-cell spray foam, or you can install a combination of closed-cell spray foam and fluffy insulation, as long as the R-value of the spray foam layer meets the minimum R-value required for your climate zone, as explained in my article on low-slope roofs.
Would the peanut-brittle insulation method you mentioned could be used instead? Or does it absolutely have to be closed-cell spray foam for the whole thickness corresponding to the required R value (for me, R-20)?
If yes, when applying the peanut-brittle insulation method, let’s say for a 2’ x 8’ rigid foam board section, is the whole surface needs to be covered by the 1” inch thick closed-cell spray foam, or is covering only edges and seams sufficient (with a generous overlap)?
Concerning method #2:
2. Improve the ventilation details as explained in my article on low-slope roofs, and then insulate with fluffy insulation.
My understanding is that I should concentrate my air / vapor sealing on the ceiling layer (blue), underneath the cellulose, to minimize the air / moisture transfer from inside the house into the below section of my attic. Possibly using a class one vapor barrier?
I should not do any vapor sealing between the below section of the attic and the top vented section of the attic, so whatever moisture that manage to go from inside the house to the below section, should eventually dry to the exterior / top section which ventilation has been improved with doghouses and openings on the perimeter.
All this is correct ?
.
Response to Francois Desrochers
Francois,
Q. "Would the peanut-brittle insulation method you mentioned could be used instead? Or does it absolutely have to be closed-cell spray foam for the whole thickness corresponding to the required R value (for me, R-20)?"
A. I don't recommend the cut-and-cobble approach or the peanut-brittle approach for unvented roof assemblies. This approach is risky.
Q. "My understanding is that I should concentrate my air / vapor sealing on the ceiling layer (blue), underneath the cellulose, to minimize the air / moisture transfer from inside the house into the below section of my attic. Possibly using a class one vapor barrier? I should not do any vapor sealing between the below section of the attic and the top vented section of the attic, so whatever moisture that manage to go from inside the house to the below section, should eventually dry to the exterior / top section which ventilation has been improved with doghouses and openings on the perimeter.
All this is correct?"
A. There is no requirement for an interior Class 1 vapor barrier -- only a vapor retarder (a less stringent layer). This code requirement can be met with vapor-retarder paint. That said, you can install polyethylene on the interior if you want.
What is far more important is that you install an air barrier at the ceiling. This requirement is usually met by installing taped drywall. It's also essential to address air leakage through electrical boxes, electrical cable penetrations, plumbing vent penetrations, and access hatches.
You are correct that you never want to install a vapor barrier on the top side of your attic insulation.
More peanut brittle questions
I’d like to understand a bit more about the peanut-brittle and the associated risk.
The way I understand it, peanut-brittle method is replacing some of the volume of spray foam with rigid panel to save on cost, and seal the whole thing with an inch of closed-cell spay foam at the end.
Is it risky because of the shrinking and movement of the peanut-brittle layer underneath? The 1 inch of closed-cell spay foam isn’t enough to keep the whole thing properly sealed?
How risky it really is? Like risky-it-WILL-fail, or risky-it-most-likely-will-work but better options out there makes it a wrong choice?
**********************
Honestly, I’m getting more and more confused. None of the 3 methods you mentioned appears very attractive to me:
1. Install closed-cell spray foam on the underside of the layer you have labeled "Deck (wood planks)." You can either install all of your insulation as closed-cell spray foam, or you can install a combination of closed-cell spray foam and fluffy insulation, as long as the R-value of the spray foam layer meets the minimum R-value required for your climate zone, as explained in my article on low-slope roofs.
Honestly, we are very uncomfortable with the idea of chemical sprayed inside the house. We understand the vast majority of spraying done by competent contractor are going well, but there is an element of uncertainty that we would like to avoid.
2. Improve the ventilation details as explained in my article on low-slope roofs, and then insulate with fluffy insulation.
Reading on the subject, it might prove to be difficult to achieve a good ventilation across our roof because of the poor access to the sides of the building. There is no soffit communicating, and the external walls are all brick.
It is also difficult to find a local contractor that doesn’t look at you like you are an alien when you mention Doghouses to them. Most will just say to install 2 - 4 Maximum and be done with it, regardless of the missing intake.
3. Install rigid foam insulation above the roof sheathing.
This would require a new roof membrane (the actual roof is still in good shape), so it would be very costly, but also we aren’t sure how we would insulate the perimeter of the house under the roof sheating. All sides of building are brick wall in good shape. We could access the below-deck from inside, but the upper-deck would require the complete removal of the roof sheating from outside or cutting through the deck from inside. A hell of a job.
So the lack of a clear choice for me is why I’m pushing to find alternative methods, but those seem to just add to my confusion.
Thxs for your time.
Response to Francois Desrochers
Francois,
Ultimately, you are going to have to step up to the plate and make your own decision -- especially if you are resistant to my advice. That's fine. I can provide advice, but you have to make your own decision.
Q. "Is the peanut-brittle method risky because of the shrinking and movement of the peanut-brittle layer underneath? The 1 inch of closed-cell spay foam isn’t enough to keep the whole thing properly sealed? How risky it really is?"
A. I don't know how risky it is. I don't have a number. I have heard reports from people I trust of cut-and-cobble failures when the method is used for unvented roof assemblies.
I'm conservative when it comes to unvented roof assemblies, because there are lots of failures. Since I'm giving advice over the Internet, I take my responsibility seriously. I don't want to provide risky advice.
The safest way to proceed (if you want to insulate an unvented roof assembly from the interior) is with closed-cell spray foam.
I have also listed other options. What you do next is up to you.
Cut and cobble in 1933 cape with no sheathing
Thanks for this article. I am working on remodeling an old house, and because I have lots of time but a tight budget, this looks like the best method for me. I am in zone 3a (west TN). The existing walls have 2x4 studs with tongue-and-groove wood on both the inside and outside of the studs. The inside then has paneling or wallpaper over the T&G, and the outside has wood siding over the T&G, covered by 1/2" XPS coated with plastic film, which is then covered by ugly vinyl siding. My plan is to eventually remove the vinyl and foam and refinish the original wood siding.
I have a few questions:
1. I understand that I will need an air gap between the foam board and the exterior T&G cladding as described in the "insulating walls with no sheathing" article. But that article recommends an air gap of .75" -1", which would mean I can only put 2.5 to 2.75" of foam in the walls. I would prefer to use a 0.5" or even 0.25" air gap so that I could put in more foam. Is there any reason that the air gap could not be thinner than 0.75"?
2. Would it create problems to put foam board inside the walls before I rip off the vinyl siding and foam board (which presumably creates a vapor barrier)? I would like to finish at least some of the inside before I tackle the outside so that I can live there during the renovation. But it will create a temporary (perhaps up to a year) vapor barrier sandwich with wood in the middle. Is that a terrible risk?
3. The house is a cape cod style with two dormer windows. The ceiling of the second floor is T&G wood. Loose-fill cellulose has been blown into the what is essentially a cathedral ceiling. The roof appears to be unvented -- there is no visible ridge vent. The roof is brand new. It sounds like the safest bet is to not try to further insulate the ceiling, but to leave the loose cellulose and to consider putting foam under the next roof. Is that correct? And it would be okay / desirable to put air-sealed drywall on the obviously air-permeable T&G ceiling, correct?
4. When installing foam board in the walls, is there any advantage to using construction tape like 3M all-weather tape either instead of or in addition to spray foam? Might it resist deformation over time more than does canned foam? It seems like it would made the job less messy if the first layer had tape so that the foam could not squish to the outside. But it might also create undesirable air gaps around that first layer. Any thoughts?
Thanks in advance!
Jennifer
Response to Jennifer Gruenke
Jennifer,
First of all, the advice in the article you refer to ("Insulating Walls in an Old House With No Sheathing") is irrelevant, because your house has sheathing. In fact, your house has high quality sheathing -- namely, tongue-and-groove boards. This type of sheathing was used for at least a hundred years before the invention of plywood, and many builders still install board sheathing.
For more information on board sheathing, see this article: "Wall Sheathing Options."
Q. "Would it create problems to put foam board inside the walls before I rip off the vinyl siding and foam board (which presumably creates a vapor barrier)?"
A. Probably not. Needless to say, if you see any signs of moisture entry during your renovation work, that would be a red flag that should cause you to reconsider your approach.
Q. "The house is a Cape Cod style with two dormer windows. The ceiling of the second floor is T&G wood. Loose-fill cellulose has been blown into the what is essentially a cathedral ceiling. The roof appears to be unvented -- there is no visible ridge vent. The roof is brand new. It sounds like the safest bet is to not try to further insulate the ceiling, but to leave the loose cellulose and to consider putting foam under the next roof. Is that correct? And it would be okay / desirable to put air-sealed drywall on the obviously air-permeable T&G ceiling, correct?"
A. You're on the right track. Task #1 is to install taped drywall on the interior side of the ceiling. Task #2 is to install an adequately thick layer of rigid foam on the exterior side of your roof sheathing.
Q. "When installing foam board in the walls, is there any advantage to using construction tape like 3M All-Weather tape either instead of or in addition to spray foam? Might it resist deformation over time more than does canned foam? It seems like it would made the job less messy if the first layer had tape so that the foam could not squish to the outside. But it might also create undesirable air gaps around that first layer. Any thoughts?"
A. It's hard to get a tight fit with rigid foam, so the usual method is to adopt a loose fit and to seal the perimeter with canned spray foam. That said, a high-quality tape makes sense for any seams that appear tight (in other words, seams without obvious voids). Use common sense.
Response to Martin Holladay
Thanks for the prompt reply. Are you saying that I can fill the whole wall cavity with foam, skipping the air gap? I don't think that there is a vapor barrier over the T&G sheathing, but I suppose there is no air gap with siding over housewrap in modern construction.
Response to Jennifer Gruenke
Jennifer,
You wrote, "I don't think that there is a vapor barrier over the T&G sheathing."
That's good. A house should never have a vapor barrier on the exterior side of the sheathing.
You are probably thinking of housewrap or ashalt felt. Neither of these is a vapor barrier. Housewrap is vapor-permeable -- the idea is to allow the sheathing to dry to the exterior if it ever gets wet.
Older homes often had asphalt felt or rosin paper between the sheathing and the siding. In some cases, there was no such layer, and the siding was nailed directly to the sheathing. That doesn't meet modern standards, but it is what it is.
Unless you note signs of water entry, don't worry. There's not much you can do about the problem until it's time to replace your siding. When you replace the siding, it certainly makes sense to install a water-resistive barrier (WRB) like housewrap or asphalt felt.
Response to Martin Holladay
Okay. That makes sense.
Unvented Tiny House roof assembly
Dear Martin,
I hope you still check this post!
I have read the relevant articles and all of the posts on this article.
I know you advise that if you cannot put rigid foam on the outside your only option is cc spray foam.
Here's my situation:
I am building a tiny house on wheels. It is 20ft long and 8 1/2ft wide. I have 10ft of unvented cathedral roof at a 38° angle and 10ft of roof that is a long former at a low slope of 7 1/2°. The roof has 1/2" plywood sheeting covered by Grace Ice and Water Shield and directly on top of that is a 1" standing seam metal roof.
The rafters are nominal kiln dried 2x4's. My original plan was to have someone spray cc spray foam. Unfortunately we only have one contractor that does this in my area. He says he sprays a thick layer that ends up 2 - 2 1/2" thick. Everything I've read about spray foam emphasizes the absolute importance of proper application which, as far as I've read means thin layers, one at a time. Otherwise it may not dry properly and possibly offgas for years. I am already somewhat chemically sensitive so this terrifies me!
In the article about how to insulate cathedral roof assemblies, a couple of times, in parentheses, it says... "or arguably rigid foam" instead of spray foam. Again, I understand that you don't recommend it, but this is what I am thinking... Someone in the earlier post mentioned using an adhesive on the side of the rigid foam against the interior side of the roof shearing. I was thinking this sounds good as it would make a solid roof assembly where no moisture could get behind the foam because of the adhesive... So... I would use 3 - 3 1/4" of rigid foam with adhesive on the underside of the sheathing, friction fit and sealed air tight with "one of those European tapes." The bays would have solid pieces of foam, no cobbling...
So what do you think? Can this work? I know it's not as good as spray foam, but if I am meticulous, can it work?
Thanks so much for your time!
Nymiah
Response to Nymiah
Nymiah,
If you want to avoid spray foam, the best approach is to install rigid foam above the roof sheathing, not below the roof sheathing.
If you ignore my advice and install cut-and-cobble rigid foam under the roof sheathing, you are choosing a risky approach. It's possible that you will get moisture accumulation or sheathing rot. The colder the climate, the higher the risk -- so one way to lower the risk is to park your tiny house in San Diego.
S " of hen
PS i live on the northcoast of California in Eureka. We are in the 4c marine climate zone. This calls for an r10 value for above roof rigid foam which you also say is the minimum for spray/rigid foam beneath the roof sheeting. I gueas if 3" of rigid is too much rigid, I was thinking 2" of rigid foam for the r20, adhered and taped for excellent air tightness etc. And then air permeable insulation for the remaining 1 1/2", and then maybe to finish, we're going to cover all with 1/4" finished plywood painted. Drywall too brittle for moving houses. ☺ And there we Are! What say you Martin of the building arts?
Response to Nymiah
Nymiah,
My advice is unchanged. Your approach is risky (although not as risky as it would be in a colder climate like Minnesota).
With changes in temperature and humidity, your 2x4s and roof sheathing will expand and contract. These expansion and contraction cycles eventually stress the caulk, foam, or tape used for air sealing, putting the sheathing at risk for moisture accumulation. That's why I advised you to install the rigid foam as a continuous layer above the roof sheathing rather than cutting narrow rectangles and installing the rigid foam between the rafters.
That said, it's your house. You get to evaluate the risk, and you get to decide your own appetite for risk.
Just saw that you wrote more,
Just saw that you wrote more, sorry.
But I would still like to
But I would still like to know what you think of the adhesive idea... trying to find small things that will add up to less risky.
Also: i already Installed the
Also: i already Installed the expensive metal roof and cannot afford to take it apart and redo it so as to be able to put rigid foam above the roof sheathing...
Martin, your article says...
Martin, your article says... "In spite of these disadvantages, cut-and-cobble sometimes makes sense. It can be used:"... and here I can point to 2 issues on your list that lead me to this method. So I am confused now when you say in these posts that it shouldn't ever be done, while your article lists "cut and cobble sometimes makes sense..." When... which is what I'm dealing with. SO... Will a good construction adhesive applied on the rigid foam and into the corners and then pushed into the sheathing and held tight while it has a quick dry so the sheathing at the back is completely sealed, which would hopefully make it unlikely moisture could get into the sheathing to condensate... So my question stands... Could this work?
Response to Nymiah
Nymiah,
Q. "So I am confused now when you say in these posts that it shouldn't ever be done, while your article lists 'cut and cobble sometimes makes sense.' When?"
A. Cut-and-cobble sometimes makes sense for walls or vented roof assemblies. As my article makes clear, it doesn't make sense for unvented roof assemblies.
Q. "So my question stands... Could this work?"
A. I've answered your question a couple of times. My answer isn't really a yes-or-no answer. My answer is, "It's risky." Here at GBA, we regularly receive reports of cathedral ceilings with damp roof sheathing. These reports have made me conservative in my recommendations.
Q. "But I would still like to know what you think of the adhesive idea."
A. Adhesive and caulk are similar (and in many cases identical). Either method of air sealing (adhesive or caulk) is better than nothing, but your suggested approach can still fail.
Q. "I already Installed the expensive metal roof and cannot afford to take it apart and redo it so as to be able to put rigid foam above the roof sheathing."
A. It's really important to finalize your insulation plan before you begin building. In your case, it's too late to take that advice. But other GBA readers might benefit from that advice. Here is a link to a relevant article: Plan Ahead For Insulation.
Here's the fancy European
Here's the fancy European tape...
TESCON VANA Specifications (PDF – English)
https://foursevenfive.com/wp-content/uploads/2016/06/TesconVanaSpec.pdf
Thank yo for answering so
Thank yo for answering so quickly Martin!
I am wrong to feel hopeful
I am wrong to feel hopeful regarding this part of your article about code? "In the 2012 version of the IRC, the language was corrected to include cathedral ceilings. The relevant section of the code (Section R806.5 of the 2012 IRC) reads, “Unvented attic assemblies (spaces between the top-story ceiling joists and the roof rafters) and unvented enclosed rafter assemblies (spaces between ceilings that are applied directly to the underside of roof framing members/rafters and the structural roof sheathing at the top of the roof framing members/rafters [otherwise known as cathedral ceilings]) shall be permitted if all the following conditions are met…” The required minimum R-values for the foam layer haven’t changed."
Martin,
Regarding your
Martin,
Regarding your comment about how I should have planned better... As I said in my initial contact I Had planned for spray foam, but I began to hear horror stories and have come around to wanting something else... too late. I am 58, and with minimal carpentry experience (4 years of stage carpentry in college and home projects over the years) I am finally building my own home! It has been a steep learning curve, and so I did not have all the information I needed at the time I put the roof on...
Insulating Thin Rafters
I'm restoring a small 150-year-old stone house with a hip roof in France. It has a slate roof and no sheathing. The rafters are narrow (10cm X 10cm; about 3-7/8"), and the ceiling is low above our low second floor. I was considering this "cut & cobble" method of insulating covered with T&G pine for a ceiling. I'm thinking the rafters are not tall enough for batt insulation. Any ideas?
Response to Phil Jamison
Phil,
First of all, I envy you. I imagine it's a beautiful building.
Second, it's important for you (a) to comply with all local regulations, of which I am ignorant, and (b) to get local advice. You don't want to mess up a historic building.
Here are some basic principles:
1. From a moisture perspective, a slate roof is forgiving. It dries readily to the exterior after it gets wet. That said, it benefits from having an air space between the underside of the slates and the air barrier or insulation barrier beneath the slates.
2. Every insulated roof assembly needs an air barrier. You need to plan for an airtight ceiling. Remember that tongue-and-groove boards leak like a sieve. They are not an air barrier.
3. When rafters are too shallow to provide enough room for insulation, it's common to add extra framing members to increase the available depth. Some of these techniques are mentioned in my article, How to Build an Insulated Cathedral Ceiling.
4. I don't recommend the cut-and-cobble method. To reduce thermal bridging through the rafters, and to improve your chances of obtaining an airtight ceiling, you might consider installing multiple layers of continuous rigid foam on the interior side of the rafters, with the seams in each layer carefully taped with high quality tape.
Good luck. Below is a cheat sheet with French technical vocabulary.
L'amélioration thermique et énergétique des batiments résidentiels = Thermal and energy upgrades of residential buildings
La rénovation basée sur l’efficacité énergétique = energy retrofit work
l'étanchéité à l'air = airtightness
l'étanchéisation à l'air de l'enveloppe = reducing envelope air leakage (air tightening work)
pare-air = air barrier
pare-pluie = water-resistive barrier
pare-vapeur = vapor barrier
l’isolation thermique = insulation
la mousse plastique de polystyrène = polystyrene foam
la mousse plastique de polystyrène expansé = Expanded polystyrene foam
la mousse plastique de polystyrène extrudé = Extruded polystyrene foam
l’isolant-mousse en panneaux rigides = rigid foam insulation
Le le fibre de verre - fiberglass
La laine minérale - mineral wool
Isolants pulvérisés sur place = spray foam insulation
les ponts thermiques à travers les matériaux d’ossature = thermal bridging through framing members
Thin Rafters
Thanks for your reply and the French terms, Martin. Any insulation would improve this space. When the sun shines, it's hot. When the wind blows, cold. I describe it as a Tiny House (a term the French use, though they should say Mini Maison), heated with a wood stove. The very low ceiling in this attic (which I hope to use as a sleeping space) precludes lowering the rafters much. I'll let you know what I do.
Phil
Mini Maison
Phil,
Show us more pictures. Everyone is jealous. The photo you should looks like a tile floor, and roofing that comes almost down to floor level. Is this the attic? It looks almost like ancient barn construction. I'd lover to see more.
You didn't mention what part of France, and what climate zone the house is located in. That makes a big difference.
An inch or two of cut & cobble insulation in the rafters would help, if you also include an inch or two of rigid foam insulation fastened to the interior of the rafters and taped as Martin mentions.
This would be relatively labor intensive with rough sawn (or hewn) rafters, but certainly a big improvement over nothing at all.
Response to Peter Engle
Peter,
The rafters don't appear to be hewn, although they may be rough-sawn (see enlarged photo below). I'm guessing that the roof framing and slates are newer than the stone house. The rafters, skip sheathing, and slates look in excellent shape.
.
Hi Martin,
Sorry if this comes across as a duplicate. I've been trying to post a comment and seem to be having some issues with the system posting my reply/question.
I have a roof with skip sheathing (1x6's) on top of which is tar paper with a metal tiled roof (Decra tile...see attached image). The roof has a good deal of life left in it, so I'm hesitant to rip it off but need to bring the attic space into the thermal envelope. The roof has 2x6 rafters, and a few hip roofs that jut out of the main roofline and no ridge-vent to speak of, so it seems a prime candidate for converting to an unvented assembly.
I have been planning a cut-and-cobble-styled approach, filling the rafter bays with polyiso against the skip sheathing and spray-foaming them in place, followed by an inch or two of polyiso under the rafters as well (with seams taped). Does this approach seem reasonable with skip sheathing? Most everything I can find for insulating under the rafters assumes plywood or osb sheathing. The assembly of the roof itself seems pretty airy -- the metal tiles have a lot of air-gap underneath them, so I believe that the existing assembly would have plenty opportunity to dry to the exterior.
The house is a 1970's ranch-style in San Jose (Climate 3c). Along with this I was thinking of adding rockwool batts between the ceiling joists as well, but wasn't planning on air-sealing the ceiling since the attic would now be in the thermal envelope.
Thanks in advance!
-Steve
Steve,
Since your roofing tiles aren't airtight -- based on the fact that you wrote, "the assembly of the roof itself seems pretty airy -- the metal tiles have a lot of air-gap underneath them" -- and since you live in San Jose (a mild climate), your plan to use the cut-and-cobble approach is probably safe.
Alternatively, you could line the rafter bays the cardboard -- stapled up against the underside of the skip sheathing -- and then hire a contractor to install closed-cell spray foam on the interior side of the cardboard.
French Maison
Our house is in a small village in the Morvan in central France. I had the roof replaced about 15 years ago. The original was slate with under-size split tree limb rafters which were sagging under the weight. Before that, the roofs in this area were thatch. The contractor replicated the original look. Attached is a photo taken last year when we had the chimney restored. The second floor has enough height for me to walk along its center, and tapers down to about 16 inches at the eaves. When I bought the house (in 1991), access to the attic was by a crude exterior ladder. I added a small interior stairway. A long-time project!
Phil
Toute petite! Et si mignonne!
Thanks for the photo and details.
Martin
If I use EPS or XPS as a baffle for a vented cathedral ceiling (bonus room over garage) in a new build with "fluffy insulation" underneath is this considered "cut and cobble" and does it come with the same risks?
climate zone 5 central Ohio
I plan on using osb roof sheathing and dimensional lumber for rafters. I was thinking thin foam for baffle with 2" vent space then fluffy to reach my R49. Would I be better off to use thin plywood or osb for baffles? Then just alot of fluffy. If I use foam for the baffles does it have to be R20 or is that just a requirement for continuous exterior? What about vapor barrier? obviously I'm confused.
I don't like spray foam so I was not considering that.
Thanks
Kyle
Thanks
Kyle,
Q. "If I use EPS or XPS as a baffle for a vented cathedral ceiling (bonus room over garage) in a new build with "fluffy insulation" underneath, is this considered "cut and cobble" and does it come with the same risks?"
A. No, it's not cut-and-cobble, and it doesn't come with the same risks -- because the ventilation channel helps remove any accumulating moisture (and therefore keeps the sheathing dry).
Q. "If I use foam for the baffles does it have to be R20?"
A. No, there is no minimum thickness for a rigid foam baffle (other than the obvious need for the baffle to be strong enough to resist any pressure that occurs when the fluffy insulation is installed). For more information on this issue, see "Site-Built Ventilation Baffles for Roofs."
Q. "What about vapor barrier?"
A. There is no code mandate for an interior vapor barrier in your climate zone -- only an interior vapor retarder (a less stringent layer than a vapor barrier). That requirement applies to walls but not vented cathedral ceiling assemblies. What matters is airtightness, not vapor permeance -- so strive to achieve an airtight ceiling.
Thanks!
Hi Martin,
I'm planning a home remodel where I'll be redoing plumbing, electrical, and adding HVAC. I'm in a 1920's Stucco home in central Minnesota (Climate Zone 6B). As part of these we'll be backing out the lathe and plaster on the interior. The exterior is in good shape and will be left as is. We currently don't have any insulation in our walls and want to remedy this at this time.
Per the instructions on this page. Our current plan, from outside to inside is to leave the stucco as-is. Install 0.5 - 0.75 spacers behind stucco in the stud bays. Cut 2" think foil faced polyiso foam (R-13) to fit between the stud bays. These will be sealed in placed with liquid nails to the spacer and stud bay (if we cut it close enough) or using canned spray foam. On top of the foam board we'll then install 2.5" thick rockwool (R-10).
To allow us to fit the foam and rockwool we plan on making our 2x4 studs wider by fixing 2x2 on top of them. The reason I don't know if the spacing will be 0.5 or 0.75 inches off of the stucco is I don't know if the current studs are 3.5 or 4" thick (I'm fairly sure they're 3.5", as that's what they are elsewhere in the house). On top of this we'll then install dry wall.
Does this plan sound correct? Also, I'm unsure if we'll need a vapor retarder under the drywall with this method?
Thanks!
User 7510659,
It would be helpful to know your name instead of just your "User number."
You are on the right track. It sounds from your description that your house has no wall sheathing. If my guess is correct, you may want to read this article: "Insulating Walls in an Old House With No Sheathing."
One possible change to your suggested technique: Instead of adding 2x2s to the studs to provide more depth, you might want to add Bonfiglioli strips. If you don't know what Bonfiglioli strips are, you should read this article: "Breaking the Thermal Bridge." (Note: See attached document below.)
Hi Martin,
Thanks for the quick reply! Sorry, my name is Chris, I'll work on getting that added to the site.
Also, I'll look into that Bonfiglioli strips, that is a great idea.
Am I correct to assume that in this case it is best not to put up a vapor retarder (we'll be using AC in summer and heating in winter) or is it ideal to install a smart vapor retarder like MemBran (assuming code doesn't dictate something else).
Thanks,
- Chris
Hi Martin,
I figure a photo is worth 1,000 words. I was able to cut into an exterior wall (well, now it's interior due to a add on). From the outside in we have:.
1.) Stucco
2.) Wire
3.) Tar Paper (hard to see in photo)
4.) 1x10 Sheathing
5.) Kraft Paper
6.) Studs
I'm hesitant to place the foam board directly up to the Kraft paper/sheathing on the inside as in some areas where I've opened wall before there is evidence of the kraft paper becoming wet (presumably from the outside). From reading this article and a few others you've linked to I think leaving the air gap is the best choice. I plan on removing the old kraft paper as it's damp in some locations and the rigid foam should replace it's function.
Then my final solution would be:
1.) Stucco
2.) Wire
3.) Tar Paper
4..) 1x10 Sheathing
5.) 1/2" air gap
6.) 2" rigid polyiso foam
7.) 2.5" rockwool
8.) Drywall
9.) Paint
Does this seem like a good plan of action given that I don't intend on removing the exterior stucco?
Thanks,
- Chris
Chris,
If the kraft paper is getting wet, you have evidence of a flashing problem. If I were you, I wouldn't engage in any air sealing work or insulation work until I had identified the source of the water entry problem and corrected it.
Fixing water entry problems (flashing problems) always happens first -- before anything else.
Hi Martin,
Thanks again for the reply and info.
We will certainly deal with any flashing issues we discover. I have a stucco guy coming out soon to inspect the house. I believe some of the wet areas are due to cracks in the stucco. The location where I noticed it was localized and on the second floor well away from any windows or the roof line (haven't been on ladder to inspect outside yet). I realize this installation won't fix any water intrusion issues, but right now the wall breathes fairly easily inside and out which has helped it to survive this so far (no evidence of rot on the sheathing in this location). I just want to make sure we're not shooting ourselves in the foot so to speak by adding this insulation into the stud bays.
We are also having all of our windows replaced with new full frame windows with nail in flanges. The window installers will take care of new/proper flashing and repair any rot at that time. When we open the walls we'll also be able to see if there are any other areas of concern.
I'm sure we'll find some other items we need to resolve, but outside of those does my general plan of attack for insulating the exterior walls look good? Also, is there any benefit/negative to removing the kraft paper since its function should be replaced by the rigid foam?
Final exterior wall insulation proposal?
1.) Stucco (untouched)
2.) Wire (untouched)
3.) Tar Paper (untouched)
4..) 1x10 Sheathing (untouched)
5.) 1/2" air gap (untouched)
6.) 2" rigid polyiso foam (adding new)
7.) 2.5" rockwool (adding new)
8.) Drywall (adding new)
9.) Paint (adding new)
The main reasons we want to go with rigid foam is to try and save a little expense from spray foam as we can do this project ourselves and the project is already getting costly and we don't want to go with spray foam due to chemical sensitives. I believe this to be a much better solution then cellulose or just using batts.
Thanks,
- Chris
Chris,
As long as you are confident that you can trace and solve the problems that caused the water entry, and as long as your window installers understand proper flashing procedures -- don't assume they do -- then your plan is fine.
Martin,
Sounds good. Hopefully this will be my last question for you (and thanks again for answering all my questions/calming my nerves). I'm fairly confident in the window installers. They're a larger franchise that's been around for awhile and are using one of the big 3's windows and have great reviews and warranty.
Your comment gives me some concern though. Assuming they don't follow proper procedures and we continue to have some water intrusion will this installation project exacerbate the issue?
My general understanding from reading your comments and GBA articles is that if there are exterior water intrusion issues that those will be issues independent of which retrofitting installation process we go with. I realize there are pros and cons to the different methods but want to make sure that structure integrity is not one of the cons I'll be dealing with or that we are at least following one of the better methods. In my mind rigid foam with an air gap should be able to better handle these issues then if we want with spray foam directly against the sheathing or with batts or cellulose. I'm certainly not the expert on this though.
Thanks,
- Chris
Chris,
Q. "Assuming they don't follow proper procedures and we continue to have some water intrusion will this installation project exacerbate the issue?"
A. Yes. Increasing airtightness and adding insulation to walls that are currently uninsulated slows the rate of drying and increases the risk of sheathing rot. That's why you need to pay close attention to flashing issues.
Ideally, with stucco, you would have a ventilated rainscreen gap between the stucco and the water-resistive barrier or sheathing layer. You don't have that -- so that fact increases your risk. More information here: "To Install Stucco Right, Include an Air Gap."
Hey Martin,
Just purchased a 100 year old home in South East Wisconsin and looking to finish the attic into a living space. A friend of mine who fixes up houses in the same area recently did the "cut and cobble" method (he calls it "poor-man's spray-foam") for his cathedral ceiling and suggested we could do the same. However, he didn't do any venting. And we weren't planning to either, mainly because:
A) we have fairly narrow 2x8 rafters.
B) inadequate venting situation (previous owner installed soffit vents every 4 rafters or so and box vents about 4' down from the ridge every 4 rafters, as well.
C) added cost of installing a ridge vent at the top and continuous soffit vent at the eaves.
D) we have a fairly large dormer that can't be vented - with even narrower 2x6 rafters.
Previous owner had seemingly "begun" to finish the attic by adding fiberglass insulation and covering with a clear plastic sheet. He also had collar ties put in about 1/3 down from ridge and ran the fiberglass across to create a flat ceiling (and venting channel above). We want to finish all the way to the ridge, however, which would eliminate the effectiveness (if any) of the box vents. We're not sure we can afford to install a ridge vent and continuous soffit vent, so we were planning to go ahead with the cut and cobble method, but after reading your articles it seems like maybe it's not such a good idea, mainly (if not only) due to the concern about the rafters swelling and shrinking every season..
A question; if we were to simply install XPS closed cell foam board between the rafters leaving a 1-2" gap between the roof sheathing, without proper lower and upper vents installed, this would basically be pointless, right? Just having an air barrier between the sheathing and foam wouldn't cut it, from what I understand..
So basically we need to vent with a ridge vent and continuous soffit vent if we cut and cobble, is what you're saying? Is there any way to avoid venting?
I'm curious about why conventional spray foam for unvented attics would be okay and not the cut and cobble approach.. can you clarify? I saw your response to a similar comment a while back but wondering if anything has changed..
This was our plan..
- 2" XPS closed cell foam board between the rafters, using adhesive to adhere it to the roof sheathing
- use canned spray foam around the foam board perimeter
- fiberglass batts (reuse the old ones)
- 2" strips of XPS foam along the rafter edge to create more depth (and probably more for the dormer to meet the depth of the rest of the rafters
- drywall, tape, paint
One other thing I was wondering, if we did the above method.. Given that the XPS foam would serve as the vapor barrier as well as insulation, wouldn't thermal bridging through the rafters create an opportunity for condensation between the foam and drywall?
Sorry for such a lengthy post. I really value this website and the comments here, so thank you all very much!
Isaac,
Q. "He also had collar ties put in about 1/3 down from ridge and ran the fiberglass across to create a flat ceiling (and venting channel above). We want to finish all the way to the ridge, however."
A. You need to consult with an engineer to determine whether these collar ties are structurally necessary. Removing the ties may be a mistake.
Q. "If we were to simply install XPS closed cell foam board between the rafters leaving a 1-2 inch gap between the roof sheathing, without proper lower and upper vents installed, this would basically be pointless, right?"
A. It wouldn't be pointless, but it would not create a vent channel. To create a vent channel, you need soffit vents and a ridge vent.
Q. "Basically we need to vent with a ridge vent and continuous soffit vent if we cut and cobble, is what you're saying?"
A. Yes.
Q. "Is there any way to avoid venting?"
A. There are two ways: Either (1) Install an adequately thick layer of closed-cell spray foam against the underside of the roof sheathing, or (2) Install an adequately thick layer of continuous rigid foam on the exterior side of the roof sheathing.
Q. "I'm curious about why conventional spray foam for unvented attics would be okay and not the cut and cobble approach.. can you clarify?"
A. Closed-cell spray foam is incredibly sticky. It acts like a glue. The risk of open seams and hidden air channels is much higher with the cut-and-cobble method than with closed-cell spray foam.
Q. "Given that the XPS foam would serve as the vapor barrier as well as insulation, wouldn't thermal bridging through the rafters create an opportunity for condensation between the foam and drywall?"
A. You are confusing two separate mechanisms. "Thermal bridging through rafters" refers to conductive heat flow -- it has nothing to do with moisture transport. Your worry about condensation is a moisture transport worry. Moisture can be transported by diffusion or by piggybacking on exfiltrating air -- but not by conductive heat flow.
Thanks so much for the quick reply, Martin!
I should clarify; we don't intend to fully remove the collar ties, we just want to finish with drywall to the ridge, but we'll still have collar ties/beams in place - functional and aesthetically pleasing! (to us, anyway)
The one thing I'm still a little confused about is installing a vapor barrier with the cut and cobble method when it's properly vented. Let's say we did the following;
- install rigid foam and canned foam between the rafters with a 1-2" gap between the sheathing for airflow
- 2" rigid foam along bottom edge of rafters to provide more depth for
- fiberglass batts
- drywall, paint
Would we need to install another vapor barrier somewhere in here? Or is the initial rigid foam / canned foam combo sufficient? I'm assuming it's not because of the concerns you've already stated.. If we WERE to install another vapor barrier, wouldn't we run the risk of potentially trapping in moisture (if the first layer of foam was done well)? Or, for this cut/cobble/vent method, should we skip the canned foam and leave a small crack around the perimeter of the rigid foam to allow air/vapor to escape, and then install a vapor barrier just under the drywall?
Also, regarding my thermal bridging question; in winter, wouldn't diffusion of warm, moist air occur through the drywall and fiberglass, eventually reaching the cold rafters within the wall and forming condensation? (if we were only relying on the rigid foam underneath as a vapor barrier, of course..)
Thanks again for your help.
Isaac,
Q. "Would we need to install another vapor barrier somewhere in here?"
A. There are no code requirements for interior vapor barriers. In colder areas of the country, including Wisconsin, there are some types of wall assemblies that require a vapor retarder. (Note that a vapor retarder is a less stringent layer than a vapor barrier.) For more information, see these articles:
"Vapor Retarders and Vapor Barriers"
"Do I Need a Vapor Retarder?"
"All About Vapor Diffusion"
There are no code requirements for an interior vapor retarder for an insulated roof assembly that include a vent channel between the top of the insulation and the underside of the roof sheathing. You don't need to worry about vapor diffusion through your drywall -- but you should be concerned about air leakage. Your drywall ceiling should be installed in an airtight manner.
Q. "For this cut/cobble/vent method, should we skip the canned foam and leave a small crack around the perimeter of the rigid foam to allow air/vapor to escape, and then install a vapor barrier just under the drywall?"
A. Attention to airtightness is always essential. Leaving deliberate cracks to encourage air leakage would be nuts. There is no need for either air or water vapor to "escape" from your house. As I wrote in one of my articles, "Although it’s true that indoor air is warm and humid during the winter, while outdoor air is cold and dry, that doesn’t mean that indoor moisture needs to “escape” from your house. It’s perfectly OK if the indoor moisture stays where it is without “escaping.” Some old-time carpenters look at walls that include a layer of rigid foam and exclaim, “That won’t work! If you put in a layer of foam, the moisture will have nowhere to go!” Moisture in your home isn’t like your retired parents in Michigan on New Year’s Day, itching to go to Florida. The moisture can stay right where it is, all winter long."
Q. "In winter, wouldn't diffusion of warm, moist air occur through the drywall and fiberglass, eventually reaching the cold rafters within the wall and forming condensation?"
A. Outward vapor diffusion through drywall does occur, although it is slowed down by paint. If you're worried, use vapor-retarder paint. In general, this diffusion doesn't cause problems, especially in vented roof assemblies, because the vent channel aids drying and the amount of vapor transmission is small. (Air leaks cause far more problems than vapor diffusion.) Note that condensation on the rafters almost never happens. Rafters are hygroscopic, which means they absorb moisture. In some cases, the rafter moisture content can increase -- but that's not condensation.
Thank you so much, Martin. I've reconsidered our options and am now considering this approach and hoping you can lend some insight.
- asphalt shingles and roof sheathing (pre-exisiting)
- install a ridge vent at the top and eventually a continuous soffit vent below the eaves (currently there are soffit vents only every 3-4 rafters)
- 2" airspace (probably using blocks of foam for this)
- 2-3" repurposed polyiso rigid foam between the rafters, sealed with closed cell canned foam
- 6' fiberglass bats
- 1" repurposed polyiso rigid foam below the rafters to prevent thermal bridging, taped
- drywall, taped, sealed, painted
My concerns are as follows;
1) The repurposed polyiso foam we're looking at doesn't have foil backing on either side - I believe it's paper..? What, if any, issues might arise with using such a material and what can we do about it? (Included a picture below)
2) We plan to install 2-3 skylights in the attic. Of course, we won't be able to fully vent those rafters. What can we do in this case? Same goes for the rafter that the existing brick chimney goes through and the sections of roof that make up the dormer. What's the best way to deal with "unventable" parts of the roof?
3) We plan to build some short knee walls (maybe just 1' high) where the roof meets the floor. If we have the rigid foam and fiberglass continuing down to the floor, sealing off the open space where the soffit vents are from the rest of the attic, do we need to do any further insulating behind the knee wall or will this open knee wall space be okay?
4) As far as running electrical, what are our options? We'd like to have outlets installed along the knee wall (which is why we plan to have knee walls in the first place) so I imagine we could just run electrical behind that, so long as we seal the space behind it (as mentioned in #3). But what are our options for, let's say, the ridge, where we'd like to have light fixtures hang? Can electrical be run behind the drywall and between the 1" layer of foam if we leave space? We plan to finish off the walls so they meet 1' below the ridge, forming a level surface for light fixtures to be installed (and I imagine we'll need to get creative with how to insulate the space above that).
5) What tape should we use for the last layer of foam below the rafters? Is tape the best option? Keep in mind this will probably be the same foam with paper backing..
Thanks so much in advance for any and all advice. Much appreciated!
Isaac,
Q. "The repurposed polyiso foam we're looking at doesn't have foil backing on either side."
A. There is no reason why this should worry you.
Q. "We plan to install 2-3 skylights in the attic. Of course, we won't be able to fully vent those rafters. What can we do in this case? Same goes for the rafter that the existing brick chimney goes through and the sections of roof that make up the dormer."
A. There is no good solution to this problem. Your options are: (1) Don't provide venting in the unventable rafter bays and cross your fingers, or (2) Use the unvented approach (closed-cell spray foam) for the unventable rafter bays.
Q. "We plan to build some short knee walls."
A. For information on this area, see "Insulating Behind Kneewalls."
Q. "As far as running electrical, what are our options?"
A. Talk to an electrician. You shouldn't encounter any problems. Electricians do this type of work all the time.
Q. "What tape should we use for the last layer of foam below the rafters? Is tape the best option?"
A. Siga Wigluv is one option, but there are others. For more information, see "Return to the Backyard Tape Test."
Thanks Martin. I think we'll go with this approach. After reading your article about knee walls, it seems like the best idea is to include the space behind the knee wall in the conditioned area - so we'll continue insulation and drywall all the way to floor behind the knee walls, and then add the knee walls in front with no insulation. This will make it easier to run electrical behind the knee walls without the concern for air escaping through the outlet fixtures. Same goes for the ridge along the top - we'll finish drywall to the peak right below the ridge, and add a horizontal surface about 1' below to serve as a route for electrical and a surface for lighting fixtures - which will be included in the conditioned space.
My one question about the unvented section of the roof is this;
- Even though the unvented areas around the dormer don't extend to any soffit vent below, they still exit up to what will eventually be a ridge vent. What if we treated these rafters the same as the others and left some space for airflow, albeit not much, regardless of having access to a soffit vent? My concern is that whether we do this or not, the ridge vent will still be there. So do we try to cover the ridge vent in this area with foam and treat the rafters as unvented? Do we try to avoid cutting the ridge vent it in this area at all? (I'm less inclined to try that as it seems difficult to get it just right from the outside). Or, do we let these rafters vent out the ridge and hope that any amount of space between the sheathing and foam is better than none? (I don't see us hiring someone to spray foam as it's a pretty small area). And for the skylight section I'd ask the same - since the rafter areas below the skylights may have a soffit vent but no ridge vent, and the rafter area above the skylights would have a ridge vent but no soffit, should we still leave airspace in hopes that some is better than none?
One more question, regarding the box vents that were already in place, can we leave those there or should we try to cover up the interior portion?
Thanks again!
Isaac,
You don't merely have dormers -- your roof appears to have multiple valleys. A roof with valleys can't be vented. The only safe approach in your case is an unvented approach.
If these concepts are new to you, I suggest you read this article: "How to Build an Insulated Cathedral Ceiling."
Yes, we have a single dormer which creates 2 valleys. The 2 pictures above are of the same area (sorry, should have clarified!). All in all, I count around 20 rafter spaces involved in this part of the roof that don't lead to a soffit vent - all of them, however, lead to the main ridge and the dormer ridge. The rest of the rafters throughout the attic all go straight down to the floor and open to the eaves where (some) soffit vents are located - as I mentioned before, the plan would be to eventually install a continuous soffit vent for all of these rafters. This conundrum area around the dormer makes up about 1/6 of our attic, maybe less. Correct me if I'm wrong but I've read through many of your articles and many, many comment sections and have seen you suggest a hybrid approach to some individuals that find theirselves in a similar situation - which is why I considered this and asked you in the first place.
Are you saying that because of this one dormer / valley section of the attic, we must spray foam our entire roof? If so, then I suppose we'll reconsider our options. Otherwise, if there is a chance to approach this as a "partially-mostly-vented roof" then I am still curious about the questions I posted above.
Thank you!
Hi Martin, thanks for all the advice!
I have a question regarding the intersection of site built baffles (https://www.greenbuildingadvisor.com/article/site-built-ventilation-baffles-for-roofs) and the "cut and cobble" method. In a vented cathedral ceiling, using impermeable rigid foam baffles (1" or more polyiso/XPS) appear to be the same thing as "cut and cobbling". Consider these two assemblies (assuming zone 4A):
1) 1.5" air space, R6 1" polyiso baffle (foam sealed), R38 fiberglass, drywall air sealed. R value total: R44
2) 1.5" air space, R18 3" polysio ("cut and cobbled"), R30 fiberglass, drywall air sealed. R value total: R48
What's the difference? Site built baffles are heavily recommended, but "cut and cobbling" is not. What is the performance difference between these assembles? It would seem that assembly 1 has a greater risk of condensation (due to air leaks from the interior) since the impermeable layer is R6 (min R15 in zone 4A), whereas the second assembly has enough impermeable R value to prevent condensation. Both would also seem to the have same risk of air leakage to the cold sheathing (foam sealed the same, thus same leak potential.).
To me, it just appears that "cut and cobbling" (in a vented system) is just thicker baffles. So what's wrong with that?
Thanks!
Jonathan,
A 1.5-inch-deep air space doesn't provide any degree of safety if it's not connect to a soffit vent at the bottom and a ridge vent at the top.
However, if the air space is connected to a soffit vent and a ridge vent, you have a vented assembly. A vented assembly is less risky than an unvented assembly because the air flowing through the ventilation channel carries away accumulating moisture and keeps the sheathing dry.
A cut-and-cobble approach is risky with an unvented roof assembly. However, a cut-and-cobble approach is perfectly acceptable with a vented roof assembly.
“[Deleted]”
Hi GBA Community!
Thanks Martin for this very informative article. It's very pertinent to my current renovation in California (San Jose, climate zone 3C). We are looking to unvent our attic space (for ductwork, storage, etc), but have a metal tile roof with plenty of life on it, so we didn't want to tear it off unnecessarily. This drives us to the approaches laid out here. The problem I'm facing is that the roof only has 1x6 skip sheathing and tar paper under the cladding (no plywood or OSB over the top).
In terms of venting, there are a eave vents spaced every 4ft or so apart, and a couple of vents under two hip roofs that are well below the ridge. Also, there is no ridge vent in the current assembly. That said, the skip sheathing and metal roof seems to be a pretty airy assembly already (there is a lot of air gap under the tiles).
My initial plan had been to fill the cavities with polyiso (5.5 inches) and then run 1-2 inches of continuous underneath the rafters (seams taped). From what I could find this would give me a roof assembly with ~R44. Leaving an air-gap would drop that to roughly r38, but it would also mean having to install more vents along the perimeter of the attic, which is ultimately something I'd really like to avoid if possible.
The questions I have are:
1) Does it make sense to install the rigid foam directly to the skip-sheathing between the rafters or should there be an air-gap?
2) If an air gap is required, do I need to add more vents or is the fact that there is an air gap alone sufficient and vents aren't required?
3) I chose polyiso because it seems to have the highest r-value without going to spray foam (which I'd like to avoid), but this article brings up the point that EPS or XPS might make more sense for its vapor permeability. Is there any issue with PolyIso with this configuration above, or does EPS/XPS make more sense?
I attached a photo of the under-roof assembly. The insulation has been removed as has the ceiling (abated for asbestos in the skim coat), so it's a pretty good opportunity to do this.
Thanks!
-Steve
Hi Martin,
Glad to see you are still responding to questions on this post.
My house is located in Zone 5 Idaho, built in 1890, ballon-framed 24" (ish) OC with rough-sawn 2x4s for studs and rafters. Roof over two-story section is T-shaped (two valleys), 12/12 pitch, essentially unvented, with ductwork for upstairs heating. Access to attic is via pulldown ladder, and the attic is used for storage.
Separate roof over single-story section lower-pitch, hipped, poorly vented, and that attic has some plumbing and wiring, but no heat. Roof will be replaced sometime in the next 5 years.
Both roofs/attics are virtually uninsulated.
I was considering the cut-and-cobble method for insulating rafter bays in the two-story attic, but from your article and comments, it seems that's a lot of labor, and a big risk.
To insulate these spaces, does it make sense to plan on unventilated roofs? Maybe blow as much cellulose as possible into the single-story unconditioned attic (which isn't used for storage or ductwork). For the two-story conditioned attic, maybe have rafter bays filled with closed-cell spray foam trimmed flush with rafters, and then multiple layers of EPS across the rafters on the interior for a thermal break. Would this approach allow me to add additional rigid foam on the exterior of the deck when re-roofing?
Thanks for any advice. I've just renewed my subscription to GBAPrime after a number of years—as always, the site's a goldmine!
David,
One attic has ductwork. The other attic has plumbing. Therefore, you can't install insulation at the ceiling plane. All insulation must follow the roof plane. (Unless, of course, you want to move your plumbing and ductwork to new locations inside your home's thermal envelope.)
Assuming that you agree that the insulation must follow the roof plane, so that you can create two unvented conditioned attics, and assuming as well that the roofing will be replaced soon, by far the best approach is to install an adequately thick layer of rigid foam on the exterior side of the existing roof sheathing, followed by a layer of new roof sheathing and new roofing. Here is a link to an article that explains how to do that: "How to Install Rigid Foam On Top of Roof Sheathing."
You can't create vented roof assemblies, because your roof has two big valleys. So you need to create insulated unvented roof assemblies.
If for some reason you don't want to follow my advice to install exterior rigid foam, your second-best solution would be to install an adequately thick layer of closed-cell spray foam on the underside of the roof sheathing, followed by another layer of insulation on the interior side of the closed-cell spray foam -- perhaps open-cell spray foam, or perhaps mineral wool batts. If you use mineral wool batts, you need to come up with a way to ensure that the batts stay in direct contact with the cured spray foam.
Here are links to two articles that discuss your options:
"Creating a Conditioned Attic"
"How to Build an Insulated Cathedral Ceiling"
Thanks so much for the prompt response and links.
I should add, the plumbing in the single-story attic is (4) 3/8" PEX supply lines, running in the joist bays for a distance of less than 10'. These lines are currently covered with fiberglass batts, installed by a remodeling contractor when they finished the room below, but the rest of the attic (2/3 or so) is uninsulated. Needless to say, snow doesn't stay on my roofs very long, and we get some very impressive icicles.
I've read the articles you linked, which are very helpful. It seems putting enough foam on top of the roof deck to get to R49 may be a tall (literally) order (9" polyiso, if I'm reading correctly). Not possible on the single-story roof, where gaining 9" or more interferes with windows and trim detail on the adjacent second story. Plus, we live in a fairly small area with fairly conservative contractors—not sure I can find one willing to run screws through 9" of foam trying to hit unevenly spaced rafters, esp. working two stories high on a 12/12 pitch.
That seems to leave Option 2 from the How to install rigid foam.. article. Something like 4" polyiso on top of the roof deck, and some sort of vapor permeable insulation in the attic on the underside of the deck, with rafters furred out to provide adequate depth. With 4" of polyiso on top of the roof deck, could I insulate the rafter bays by attaching drywall to the furred-out rafters and then have dense pack cellulose blown into the bays?
Finally, do I have it right that there's no way to insulate the ceiling plane of the single-story attic with blown-in insulation, because venting is required and being a hipped roof, it can't be adequately vented? A less expensive method of insulating the attic over the single-story area is obviously preferable, as it seems insulating the attic over the two-story area is going to be unavoidably complex and spendy.
Thanks again for your help.
David,
Q. "With 4 inches of polyiso on top of the roof deck, could I insulate the rafter bays by attaching drywall to the furred-out rafters and then have dense pack cellulose blown into the bays?"
A. Yes.
Q. "Do I have it right that there's no way to insulate the ceiling plane of the single-story attic with blown-in insulation, because venting is required and being a hipped roof, it can't be adequately vented?"
A. If you can be sure that your pipes won't freeze, you can insulate the ceiling plane without worrying too much about attic ventilation -- as long as your ceiling is airtight. (Note, however, that ceilings in old houses are rarely airtight.) For more information on this issue, see these two articles:
"All About Attic Venting"
"Air Sealing an Attic"
A couple more thoughts, Martin:
I noticed reading comments on the Creating a Conditioned Attic thread this exchange:
******************
Joell Solan | Dec 03, 2011 10:20am | #49
rigid between rafters
Thanks for thinking so much about insulation, i'm still new to thinking about this so please bear with me.
I live in the Northwest, am planning to gradually finish a 600 sq foot attic space with cathedral ceilings, new roof put on about 5 years ago, before we moved in. my rafters are only 2x4 and i don't want to lose much living space. My tentative plan has been to put 2-2.5 in. polyiso between and 2 in. under rafters for now. This won't get us to code but would be better than what we have now. now i've been thinking that someday the roof will need to be replaced and i could add rigid on top.
Which brings me to my questions:
if "ventilated rafter bays are incompatible with rigid foam insulation installed on top of the roof sheathing" does this approach make sense?
and since poly-iso is faced, can i use 2 layers on top of each other and if so do i create a sandwich with the faced surfaces or layer them with facing to the interior? thanks
User avater GBA Editor
Martin Holladay | Dec 03, 2011 10:38am | #50
Response to Joell Solan
Joell,
Don't bother to include ventilation. Instead, fill the 3.5 inch rafter bays with 3.5 inches of polysio (one 2-inch layer, and one 1.5-inch layer). Seal all gaps with canned spray foam. Then install a continuous layer of 2-inch polyiso under the rafters to stop thermal bridging.
Using several layers of foil-faced foam is fine -- there is no problem with making a sandwich like this, except that it is slow, fussy work.
********************
This is pretty much my exact situation--I assume you've changed your thinking regarding the risk of cut & cobble since then?
Finally, the 'radical approach' proposed at the end of the article—abandoning forced-air ducting and a conditioned attic, and replacing with a ductless mini-split—might make sense for me. Our second story is pretty small, 600 SF with three small bedrooms and small bathroom (that has its own heat). Plus, A/C for the two or three weeks every summer when it get a little warm upstairs would be a bonus. Assuming the attic can be properly vented when the roof is replaced.
David,
I provided that advice to Joell back in 2011, before I heard about cut-and-cobble failures. I'm more conservative now -- because I have more data from the field.
I just finished insulating my vented cathedral ceiling in southern Wisconsin.
Below the roof sheathing I have site-built OSB vents, all seams caulked. Then, between 2x12 rafters, I have about five inches of dense-packed cellulose, and then beneath that 4 inches of cut-and-cobbled rigid foam. I attached 1x3 slats perpendicular across the bottoms of the rafters, which the drywall will attach to. Then between the slats I cut and cobbled another 3/4" rigid foam. I'm about to start drywalling the ceiling, but a question first. Do I need to tape the seams between the 3/4" foam and the 1x3s? I put that layer in there pretty tight in most places, so caulking would be hard.
Thanks,
Joe
Joe,
Q. "Do I need to tape the seams between the 3/4-inch foam and the 1x3s?"
A. Not necessarily. But make sure that your drywall is installed in an airtight manner -- which means that you need to pay attention to ceiling penetrations like electrical boxes.
Will do. Thanks, Martin.
In your experience what type of spray foam works best for sealing the perimeter of the rigid foam boards in the stud bays? The Window and Door or the Gaps and Cracks type?
Martin,
Can you please clarify, regarding cut-and-cobble steps you listed:
"The third step is to decide whether to push the foam as far as possible toward the exterior side of the framing cavity — the method that is usually used for walls with solid sheathing or for unvented cathedral ceilings — or whether you want to leave a gap on the exterior side of the framing bay — the method that is used for walls that lack sheathing or for vented cathedral ceilings. If you prefer to have a gap on the exterior side of the foam, you’ll probably want to install 1″x1″ or 1.5″x1.5″ sticks at the corners of each framing bay to maintain the desired gap."
My takeaway from this is that you considered it optional whether to create/leave a gap between sheathing and insulation, but perhaps I was seeing a wishful ambiguity in that, and you intended to say that a ventilation channel of one type or the other is something you consider vital. I began to suspect my interpretation was wrong after reading in some responses to the many follow-on questions since those 2013 days (eg #77, "...I'll repeat: Don't use the cut-and-cobble method for a cathedral ceiling unless there is a ventilation channel between the uppermost piece of rigid foam and the roof sheathing,") it seems a ventilation channel is a /requirement/, not a choice, apparently to provide drying for the sheathing (or elements below?) when/if needed.
I don't really need to parse that wording so much as I may need an innovative/tailored fix for my unique cut/cobble situation, in which my air-seal is bottom-most and in which I've got much confidence. Most or even all of the caveats you've listed as reasons for concern about cut-and-cobble are eliminated by climate, since I'm in Honolulu: thermal bridging doesn't matter to me; we generally don't insulate wall cavities at all, and since my air-barrier exists below the surface of my OSB ceiling and is all-elastomeric, I have little concern for expansion and contraction messing it up. R-values are not important numerically other than "more is better" in terms of minimizing heat-transfer from our blazing sun to my home's interior, and the 3.7" of closed-cell iso make it impossible to sense any heat penetrating from solar radiation, so as an insulation system, it's totally satisfactory even without any thermal breaks at rafters.
Roof is hip, nominal framing depth is 3.5". My 'pancake' layers thus far -- over about 80% of the roof at this point -- from top-to-bottom, are:
modbit underlayment
5/8" CDX sheathing
1.7" closed-cell iso-board
1.5" closed-cell iso-board
1/2" OSB
3M 4" flashing tape (at OSB joints)
primer and elastomerics (caulk and two coats of exterior-intended roof-coating) to create a continuous near-perfect bottom-side air-barrier, sealed back to the CDX sheathing
XPE foam ceiling tiles (strictly decorative)
My plan was to add standing-seam aluminum roofing once I'm finished with the re-sheathing entirely, since it's costwise silly to do the metal roofing in stages.
I've already found a lot of moisture in the OSB, almost certainly mostly residual from heavy rains during my slow one-man construction process. But even months later, it hasn't fully dried, and this has me back to wondering how to provide for drying to the roof side, even if slow, both for this immediate purpose and for any unexpected moisture incursions in the future. Moisture accumulation in OSB could also be from convective-transfer, exacerbated from long duration of work, before the air-barrier was added below.
I have good confidence in the impermeability of my painstakingly-detailed sealing of the ceiling and eave-ends with the aforementioned elastomerics. (Covid-19 lockdown made me even MORE inclined to sweat the details.) Am I correct in understanding that, as long as this barrier is intact, venting by some range of other means from above would/should not present future problems?
If major rework to correct this is required, and assuming I have options as to how to do this, I'd by far prefer to tear off my modbit underlayment. It's permeability is not specified on the Owens website, but I take it this stuff is extremely low-perm, since it's mod bit...? I could, if needed, torch it off and replace with something - anything - that would provide the needed moisture release. I'm not even married to the standing-seam roof, if that matters, though their longevity here is unsurpassed. Might even a simple old-school underlayment (asphalt-paper, even) suffice? I'd certainly be interested in more modern, robust permeable underlayment options that would be compatible beneath directly-laid metal roofing, but as mentioned above, everything above the sheathing CDX is "open for discussion," owing to being less painful to rework than any interior-rework at this point.
Mahalo - Dave
David,
Q. "Can you please clarify, regarding cut-and-cobble steps you listed? ... My takeaway from this is that you considered it optional whether to create/leave a gap between sheathing and insulation, but perhaps I was seeing a wishful ambiguity in that."
A. The discussion about whether the air gap was optional or not was in reference to walls, not cathedral ceilings. I do not recommend the cut-and-cobble approach for unvented cathedral ceilings.
Your description of your roof assembly is confusing -- it's hard to tell whether your insulation is on the interior side of your roof sheathing or the exterior side. If you are installing a continuous layer of rigid foam on the exterior side of your roof sheathing (rather than cutting the insulation into narrow strips and inserting it between the rafters), then the assembly is safe.
Q. "I've already found a lot of moisture in the OSB."
A. That is concerning. I'm not going to provide advice, because it's impossible to do that without a site visit. Suffice it to say that it is essential that you figure out the source of the moisture, because damp OSB is bad news.
Martin,
The stack-up is indeed cut-and-cobble, with my iso-board layers fitted tightly between rafters, squeezed directly against the CDX roof sheathing. My "top-to-bottom" list of layers shows the details.
Below /everything/ (even the ceiling) is/will be my air-barrier, which consists of the elastomerics that envelope the entire stack of materials, and wrapped back up to the underside of the same CDX sheathing. I'm thinking this situation would at least benefit from, if not absolutely /require/, some form of vapor relief out the top, eg through a permeable underlayment, then shingles or perhaps the metal roof I'd hoped to install. What's your recommendation?
David,
I'm not familiar enough with the Hawaiian climate to advise you. If you have an impermeable vapor barrier on the interior of your assembly, the damp OSB sheathing will never dry out unless there is a drying path to the exterior.
Vapor-permeable roofing underlayment would allow that, as long as you install either (a) vapor-permeable roofing, like cedar shingles, slate shingles, clay tiles, or concrete tiles, above the underlayment, or (b) a vented airspace above the roofing underlayment (created by installing 2x4s 16 inches on center) with some type of roofing that can span the 2x4s above that -- for example, metal roofing.
Thanks Martin, that's getting me somewhere.
Regarding roofing choices over a new permeable underlayment: you exclude standing-seam, but I wanted to ask why. I'd taken standing-seam in general to be sufficiently air-leaky to allow drying (the lap-seams, the standing-seams themselves, the ridge-cap, all are far from vapor-tight) Is it that standing-seam, what with the large direct-to-underlayment contact area, wouldn't be so great at allowing evaporative transfer?
You've mentioned Vapro in some posts, IIRC. I just looked a little at https://vaproshield.com/public-documents/product-overviews/592-slopeshield-plus-self-adhered-overview/file . This product claims to be water-shedding, yet highly vapor-permeable, so it sound like the roofing underlayment for me. And their illustration appears to feature standing-seam being applied directly to the stuff, so maybe that's my solution?
Going further with the Vapro stuff, if it's indeed the silver bullet it's presented as, which allows moisture to escape fairly freely up through my roofing while still maintaining watertight-ness from drips, then it seems like it's commensurately a lot less important that I create a complete air-seal at the bottom, to begin with - and I could thus dispense with all the fussing with elastomerics...?
Otherwise, maybe I'm going to have to give up on standing-seam in favor of another; I can't imagine a batten system that would result in a walkable standing-seam roof, unless it was crazily heavy-gauge - and I'd still have to replace my existing Owens underlayment. Whatever the materials are, they have got to be light, considering the rest of the structure. Other thoughts?
David,
I don't think standing-seam metal roofing allows drying to the exterior. The metal itself is a complete air barrier and vapor barrier, and the amount of air leakage at the seams would be insignificant -- not enough to depend on for outward drying of damp sheathing.
Thanks Martin.
I think the un-answerable question of "how much moisture needs to be released?" would first have to be addressed. At least here in Hawaii, metal roofs are not expected to be vapor-sealed, so while there is an unintended pathway provided, it's not predictable nor quantifiable.
Mfr's rep from the standing-seam company just confirmed with me that they don't "require" an zero-perm underlayment, and that there are in fact new products out that (like Vapro, apparently) offer one-way breathability while being drip-tight. FT Synthetics was the company they're generally supporting, with I think this particular product in mind for my setting: https://www.ftsyn.com/hydra-breatheable-underlay/
I got some input also from a building scientist at Vapro, whom I reached to verify the basics (that Vapro would indeed work below standing-seam as pictured, that it acts as a vent for vapors, yet is 'drip tight' against leakage through the roofing).
He suspects that (as you mentioned) Hawaii's climate is far from GBA's normal 'territory', and this is perhaps the basis for my current state of bewilderment/ mixed responses. I have to continue my conversation with him to get more particulars, but he seems to be indicating that my selection of OSB (Techshield OSB with incised foil face) as the bottom (ceiling) layer ("1/10 the permeability of plywood") was only my first step in the wrong direction. Sadly, this was compounded by my extensive efforts to make air-tight the entire bottom surface - another misstep, according to him, though I thought I was "praying to the GBA Mecca" during all of that time. Instead, he recommends a very-permeable bottom layer (even more permeable than the top sheathing - the CDX - if possible) and demo/replacement of the air-tight Weatherlok underlayment I've installed thus far with their Vapro product.
If I understood correctly, this input was based on the mechanics of moisture being driven from what he described as higher vapor-pressure (the great outdoors, in this case, eg the airspace immediately above my usually-hot roof) to lower (my roof interior and living space). So without providing a viable vapor transit path to compete with that pressure-driven mechanism, from bottom to top, I've inadvertently created a sort of ponded-accumulation of moisture, which won't be inclined to evaporate upwards, even with the benefit of the Vapro permeability.
I'm now considering whether to rip out and replace my ceiling (Techshield) with some unknown highly-permeable surface that would INCREASE breathability, rather than trying to keep any vapor out of the layers. Does some or all of this sound reasonable, in the forever-steamy-summer context that generally exists in Honolulu?
David,
It sounds to me as if you have been misinterpreting GBA's advice. You have confused airtightness with vapor impermeance. They're different.
Here at GBA, we advise readers who are building wall assemblies or roof assemblies with a vapor-impermeable exterior layer (like rigid foam or roofing) to choose a vapor-permeable interior finish (like drywall) so that the assembly can dry to the interior. This basic advice is found in many GBA articles, including these two:
"Calculating the Minimum Thickness of Rigid Foam Sheathing"
"Sandwiching Roof Sheathing Between Two Impermeable Layers"
Your attempts to make the interior layer airtight were not misguided. It was the selection of a vapor-impermeable interior finish material (rather than drywall, which is vapor-permeable but which can be installed in an airtight manner) that was misguided.
My advice to you focuses on the fact that you know that your OSB is damp. So the OSB has to be able to dry out, or it will rot.
Hey Martin,
I'm insulating my unfinished concrete basement with a layer of 2" GPS foam and a stud wall inside of that. I was previously going to use mineral wool batts but I've come across some cheap fibre faced polyiso that i was thinking of cutting between the studs and sealing with spray foam. Will the polyiso trap any moisture between the stud wall and foam, therefore encouraging mould? Is there a better way to use it in the wall assembly?
Shmeado,
Here is a link to an article that should answer your questions: "How to Insulate a Basement Wall."
You describe the use of "GPS foam." You probably mean either XPS rigid foam or EPS rigid foam -- I'm not sure which.
If you install a continuous layer of rigid foam on the interior side of the concrete wall, followed by a stud wall on the interior side of the continuous rigid foam, you need to follow a few rules on the minimum R-value of the continuous rigid foam layer. The colder your climate, the thicker the continuous layer of rigid foam has to be. A conservative rule of thumb is that you should follow the same rules that apply to above-grade walls with a continuous layer of exterior rigid foam. For more information on those rules, see "Calculating the Minimum Thickness of Rigid Foam Sheathing."
Once you are sure that your layer of continuous rigid foam is thick enough, you can install almost any type of insulation between your 2x4 studs without condensation worries. Cut-and-cobble polyiso will work between your studs if you want to use that type of insulation, but it would still be best if your layer of continuous rigid foam between the studs and the concrete wall met minimum R-value requirements for your climate zone.
Hey Martin,
I've spent some time reading through this thread and the How to Build an Insulated Cathedral Ceiling post I haven't been able to deduce an answer to the use of foil-faced polyiso (non-permeable) or an un-faced polyiso (~ 4 perms) in a vented cathedral ceiling. I am planning to use the pancake method with several layers of Polyiso sealed with canned spray foam around the edges. As well as one continuous layer under the rafters for air sealing and thermal bridging. I was planning to use foil faced throughout, but now I am wondering if I need to use it only on the interior side under the rafters. Would it be an issue if they were all foil faced or if only the exterior and interior layers were foil faced? I am in SC (climate zone 3).
I understand the main way the cut and cobble method fails is with poor air sealing resulting in condensation either in the foam or on the sheathing. I don't believe the foil facing will matter significantly, but don't want have issues later down the road.
Also, do you have a recommendation for the tape to use with to air seal the continuous layer?
Home,
You didn't mention whether this is a vented assembly or an unvented assembly. You'll need to have a ventilation channel between the top of the insulation layer and the underside of the roof sheathing, and this ventilation channel needs to be connected to a soffit vent at the bottom of the channel and a ridge vent at the top.
If you have this ventilation channel, the assembly will be safe. If not, it won't be, as I explain in my article.
If the assembly is a vented assembly, you can use either foil-faced polyiso or polyiso without foil facing. Either type of polyiso will work.
For more information on high-quality tapes, see "Return to the Backyard Tape Test."
Martin,
Sorry about that. Yes it is going to be a vented assembly leaving 1 1/2 inches above the polyiso. Thankfully our roof is a very simple roof and we have a ridge vent running the length of the roof. We have had to make some minor adjustments at the soffit to ensure it will provide airflow to each rafter bay.
Thanks for your input!
OK -- sounds good.
Martin, I asked this question generally about my re-insulation of a 4:12 shed roof while re-roofing with metal standing seam (so on top of plywood will be hi-temp ice and water shield) https://www.greenbuildingadvisor.com/question/insulating-shed-roof and got some feedback. There is currently venting which I want to maintain and I am hoping to maximize the R-value but I cannot add foam on the top of the sheathing and am leery of full closed cell spray foam. For a lot reasons I've decided on cut and cobble (trying to do this myself and save money, have the time and patience to get the details right, etc.). In short, I have 2x10s with about a 16' span. I will place 3 layers of 2" polyiso and a 1.5" layer. I will rip them to fit the 16" o.c. rafter bays. I will maintain a 2" vent channel soffit to ridge. A few detail questions:
1) On the forum thread, an expert member suggested (and you do in the article) that with the vent channel, the stakes are lower. Will it be acceptable to meticulously edge foam and caulk the first layer (set on top of ceiling drywall) around all sides and at butt joints but subsequent layers can be cut to size and set in place without much or any foam/caulk? Or should every layer be sealed?
2) I have a Great Stuff foam gun--is there a preferred foam for doing this? The gaps/cracks? The window/low expansion? Would a tighter fit and a really good flexible caulk (such as OSI QuadMax) be preferable? Foam the perimeter, set first in place, then caulk the top of the panel perimeter?
3) Does it matter whether the polyiso has a foil face or a kraft face? Is it fine if all four layers have the foil face? (I've been surprised, in the DMV area, how difficult it is getting polyiso boards and I can't be too choosy).
Interestingly, the current assembly, that is "vented," has the full 9.5" inches stuffed full of fiberglass. The areas I saw (due to a branch that had punched through) in the middle of the rafter span, were bone dry and had no signs in 50 years of moisture buildup.
Michael,
I'm not sure what you mean by the DMV area -- you live somewhere near the Department of Motor Vehicles, perhaps? In what state?
In general, you're worrying too much. If you have a good vent channel, just get at least one layer of rigid foam in each rafter bay as airtight as you can make it, and stop worrying. Canned spray foam is fine, and caulk is also fine. Foil facing is fine, and other types of facing are also fine.
If you want a reduce thermal bridging through your rafters, finish off your job with a continuous layer of rigid foam on the interior side of the rafters (between the bottom of the rafters and the ceiling drywall).
thanks. DC/MD/VA = DMV. It is probably as annoying as the DMV lobby most days.
With all due respect (which is gobs), I'm worrying too much because I've been reading you for so long and see all the things that I could make go wrong! But I feel somewhat absolved with your guidance here. THANK YOU.
I would have loved to have added that layer of foam to mitigate bridging, but that ship sailed.
Dear Martin, I wanted to come back and thank you for the guidance and advice (and thank a few others in the Community Q&A). Your wisdom gave me the courage to pull the trigger and get this project done in August. I probably was "worrying too much" but most of the articles you wrote about this started with images of rotten roof framing, so I stand accused. Anyway, I tore off the shingles and proceeded to remove two pieces of plywood at a time (I got a denailer gun and wow did that make the plywood removal safe and easy). The bottom row of plywood had actually been replaced previously and had an intact ice/water shield on it. Given the 2.5 overhang, and given the fir plywood I was using was back up to $70 a sheet, I left that row in place and just nailed to code spacing. With two sheets removed in a staggered pattern, we worked to clean out the cavity of the old poorly installed fiberglass, ran a bead of spray foam around the edges, placed a 1.5" piece of polyiso cut to width (found it worked best to have a bit of play, so cut them 1/4" narrow), then spray foamed and repeated for each layer, with a total of one 1.5" and three 2" pieces. That gave me 7.5" of polyiso with air tight sealing the whole depth. I also then was able to maintain the 2" air channel above that, under the new fir plywood (that then got hi temp ice/water shield and the metal roofing assembly). By working on two sheets removed at a time, I could get three full rafter bays done, and prep the lower or upper half of the next one. We would then replace a sheet that covered half of the just completed rafter bays and half of the previously done. We just kept pulling off one sheet at a time and replacing a sheet one by one until we got to the end, and that way we had solid surface to do most of the work (there were some I had to straddle and reach, but not many). As for venting, it turned out that while I had eave and soffit venting (on this shed roof), the builder had installed solid full depth blocking right up the middle, so there was no effective venting (!). Regardless, there was no sign of any moisture problems. I removed the upper 2" of the blocking (drilled holes and then chiseled in between) to create a full channel from bottom to top. At the bottom, we started the insulation over the wall plate and terminated the insulation on the outside of the top wall, so both plates are now under the full depth of insulation.
In the end, it was two pretty grueling, hot, tough days, with my three landscapers helping me (yeah, yeah, landscapers, but they do what I ask them, they work hard, they don't complain). But we got it done, the roof is super solid (5 ply fir nailed properly was way stiffer than the 3 ply that was on there previously).
The results were instantaneous. On the hottest summer days, my a/c actually will cycle off occasionally and I experience no temperature gain (I used to struggle to maintain 3-4 degrees above my set point). My energy bill dropped about $150 the last two months of the summer and my run time of the a/c went down by about 35%. My only challenge now is that because the a/c is cycling on and off more, the relative humidity in the house was up around 75%. I will get a dehumidifier for next year to run full time to draw out some of that moisture. So thanks so much!
I am seriously considering the cut and cobble method with XPS foam for my 2x8” rafters in northern Michigan. I have a solid ridge beam and at this point am only doing half of my cathedral ceiling with a 2.5/12 pitch, and there is no ridge vent or movement from one side of the house to the other but I do have soffit vents. The roof was completely redone last winter with Grace ice and water and steel.
If I was to consider the cut and cobble with 4” XPS foam, sealed with canned foam at the perimeters and Roxul to fill the remainder of the cavity, should I give any consideration to leaving a 1/2” gap between the roof sheathing and the XPS foam. Although it wouldn’t have a ton of air flow, it would at least provide a drying direction for the sheathing? The ceiling will be finished in either drywall or T&G wood. I know I can’t reach any minimum required R values, and because of a relatively low ceiling, I am not willing to give up any ceiling height. My utility bills are already low and anything I do will be an improvement to what is there already. This project is 100% about preventing any condensation damage to the bottom of the roof sheathing.
As noted in my article, I don't recommend the use of the cut-and-cobble method for unvented cathedral ceilings, especially in cold climates like yours, because of the risk of moisture damage to the sheathing. In your case, I recommend that you use closed-cell spray foam.
I appreciate the response, but if a 1/2" gap left between the roof sheathing and foam, would that not allow the assembly to dry out if any moisture did happen to pass/leak through the foam?
Code minimum for a vent space is 1", and most building science people recommend at least 1 1/2" or 2". The blowing agents in XPS are potent, persistent greenhouse gasses. Pretty much any other material, or nothing, would be better than using XPS. The new formulation is about 25% better but still worse than any of the options. If you're sold on foam, I'd use HFO-blown spray foam or polyiso rigid foam. Or find recycled product.
Bachert,
You stated that you have a solid ridge beam and no ridge vent. Therefore you have an unvented assembly. Without air flow, there won't be any drying.
Would soffit vents not still provide a minimal amount of drying even without a ridge vent?
Bachert,
Vented roof assemblies work because of ventilation drying. Ventilation drying depends on air flow. To have air flow through a cathedral roof assembly, you need both soffit vents and a ridge vent. Even though I've advised you three times that your cut-and-cobble plan is risky, you seem to want to accept the risk. It's your roof. I don't think you are looking for advice -- you seem to be looking for affirmation.
Bachert, the IRC building code allows for venting only at the soffit but the vent area needs to be at least 1/150 of the floor area, vs. 1/300 if half the venting is at the ridge. That doesn't mean it's the best approach, but I use soffit-only venting regularly where shed roof ridges meet a sidewall, but I make sure there is an excellent variable-permeance interior air barrier/vapor retarder.
Michael,
Again this is one of those things that is probably very climate dependant, but here I wouldn't be comfortable leaving a shed roof that abutted a sidewall unvented at the peak, even if our code allowed it.
I'm really wary of building assemblies that rely on the absolute integrity of interior air and vapour control over their lifetime.
If you want to use XPS foam, please get one of the new versions that reduce the global warming impact: "NGX" from Owens Corning or the new gray DuPont Styrofoam. Or use a different foam: EPS and/or polyiso.
Response to Malcolm, #187: Good point, and I should have said that when I can't avoid a shed roof terminating at a sidewall rather than "I regularly use." I have also used spray foam insulation to make those roofs reasonably safely unvented. On a current project I am using a tiny attic space and venting at the gables.
Michael,
Part of this has nothing to do with building science and much more to do with the differing trajectories of our careers. You are one of the innovative designers who I am very indebted to for improving and pushing the limits of where building can and should go. I am increasingly risk adverse, adopting new techniques long after I probably should.
Hi Martin,
Thank you for putting all of this information together. I wasn't sure what the best insulation solution was for the cathedral ceiling in my 40’s built cape (maine zone 6) but now it is clear that 5” of closed cell creating an unvented “hot roof” is the way to go. However, I have a related issue that I am not sure how to solve and would greatly appreciate any insight. The current roof sheathing is not in the best of shape and will need replacing once the asphalt shingles run their course (another 10-15 years as the roof shingles are fairly new). I am looking for a sacrificial product to line the rafter bays with to protect the spray foam from adhering to the roof sheathing as it will peel apart when it comes time to replace it. Thus far the suggestions are ¼” foam board or ¼” lauan plywood. I would prefer to use the foam board due to ease of installation (lots of nails coming through the sheathing) but I am concerned that it will melt when the closed cell foam is applied. Is there a foam board or something else that would work for this application?
Thank you
Mike
Mike,
Thin rigid foam will work; it won't melt. You could also use cardboard, kraft paper, asphalt felt, or polyethylene.
Looking way down the road to your tear-off, I'd use the heaviest poly sheeting you can buy. Impale it on any protruding nails as needed, to keep it in place, maybe using a bench-sweep in the manner of a hammer. Nothing in the known universe will stick to that stuff. I'd anticipate it will probably peel away from the foam (vs the underside of your sheathing) when the time comes, though that may not matter.
The following seems like a contradiction, so I must be missing something:
"Install closed-cell spray foam against the underside of the roof sheathing...Since spray foam prevents air movement, it almost eliminates this [condensation] problem."
Versus what it says in the cut-and-cobble article:
"Wood framing expands and contracts with changing humidity levels, raising the possibility that attempts to seal the perimeter of the rigid foam (whether with caulk, SPRAY FOAM, or tape) will fail over time." [my emphasis]
Is the answer that pro-installed spray foam is a bit flexible while canned spray foam is not?
The cut-and-cobble article scared me about doing cut-and-cobble polyiso in the rafter bays of my unvented roof in CZ-2, so I'm considering using 44 cans of Great Stuff for the affected area instead (as detailed in a separate post), but if there's indeed expansion/contraction of the rafters, I should be able to get a *better* air seal with cut-and-cobble, by caulking the holy living mortal crap out of each layer of polyiso with acrylic caulk, which is stretchy.
Michael,
When a spray-foam contractor does a good job of installing closed-cell spray foam, the foam is tenacious. It's actually an excellent glue -- and as you guessed, the cured spray foam has a little bit of give to it, so it can accommodate a little expansion and contraction.
A thin bead of canned spray foam behaves differently. For one thing, it's hard to get the foam installed in a uniform way -- it's incredibly easy to miss certain spots, or to fail to insert the plastic straw deep enough to get a consistent installation of foam. And because the cured foam is thinner, it lacks the tenacity and flexibility of professionally installed closed-cell spray foam. Experience shows that cut-and-cobble jobs are more likely to have air leaks, especially a few years after installation, than professionally installed closed-cell spray foam.
michaelbluejay,
To add to what Martin wrote: If spray foam fails it is by pulling away from the rafters on either side, leaving the foam still adhered to the sheathing above. If the spray-foam around the perimeter of foam boards develops gaps, the air can make its way to the gap behind the foam board to the sheathing - which is what we are trying to avoid.
Log in or become a member to post a comment.
Sign up Log in