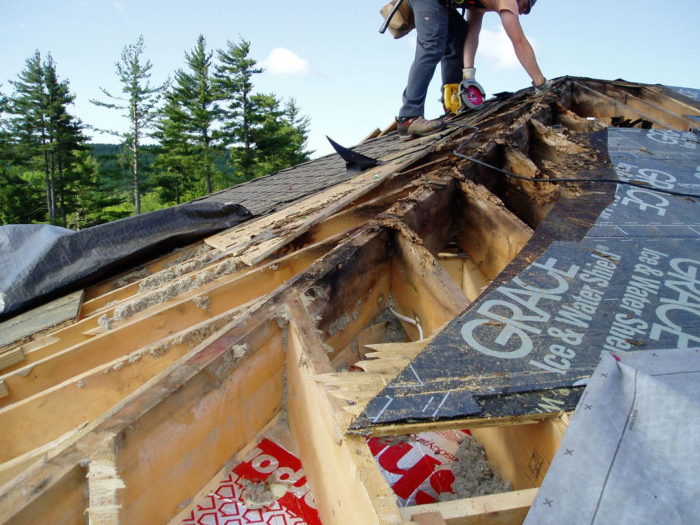
Image Credit: Peter Yost
UPDATED on August 31, 2018 with information on vapor diffusion ports.
Although the GBA website already contains many articles on the topic, we continue to receive frequent questions about the best way to insulate a cathedral ceiling. It’s therefore time to pull together as much information on the topic as possible and publish it in one place, to clarify the building science issues and code requirements governing insulated sloped roofs.
In this article, I’ll attempt to answer the following questions:
- Does a cathedral ceiling need to be vented?
- What’s the best way to build a vented cathedral ceiling?
- What’s the best way to build an unvented cathedral ceiling?
- What do building codes require?
- What risky practices should be avoided?
What is a cathedral ceiling?
This article will discuss insulated sloped roofs. The methods described here can be used to build an insulated cathedral ceiling over a great room, a section of sloped roof above a kneewall, or any similar section of insulated sloped roof.
This type of roof differs from an uninsulated roof over an unconditioned vented attic.
A brief history of cathedral ceilings
Insulated cathedral ceilings are a relatively recent phenomenon. The craze for insulated cathedral ceilings (and great rooms) really took off in the 1970s and 1980s, when examples began popping up like mushrooms after a warm rain. In those days, most builders stuffed cathedral ceiling rafter bays with fiberglass batts. Sometimes they included flimsy Proper-Vents between the fiberglass and the roof sheathing, but often they just specified thin batts to ensure that there would be an air space above the batts for ventilation.
The cathedral ceilings of the 1970s and 1980s were thermal disasters. In most cases, these ceilings leaked air, leaked heat, created monumental ice dams, and encouraged condensation and rot. In many cases,…
Weekly Newsletter
Get building science and energy efficiency advice, plus special offers, in your inbox.
This article is only available to GBA Prime Members
Sign up for a free trial and get instant access to this article as well as GBA’s complete library of premium articles and construction details.
Start Free TrialAlready a member? Log in
523 Comments
Vented Over-Roof Hybrid
For Affordable High Performance...the closing sentence in Martin's Article is worthy of a Rant.
THE MOST UNDERAPPRECIATED BUILDING ASSEMBLY
Joe Lstiburek: "A vented attic, where insulation is placed on an air-sealed attic floor, is one of the most underappreciated building assemblies that we have in the history of building science."
If you do not care for affordable or buildable....
This BSC article is helpful
http://www.buildingscience.com/documents/published-articles/pa-crash-course-in-roof-venting
same article at Fine Homebuilding
http://www.finehomebuilding.com/how-to/articles/a-crash-course-in-roof-venting.aspx?langtype=1033
here is a good video and discussion about roof ventilation
https://www.greenbuildingadvisor.com/blogs/dept/building-science/lstiburek-s-rules-venting-roofs
I like Joe's comment #53 where he mentions the "vented unvented roof hybrid"
I think this is how many/most of the European Compact Roofs are Built
I think the same strategy(vented over-roof) could be used to improve the Marc Rosenbaum type roof.
I appreciate all the links above, but foam in Europe is far less toxic then it is here, not to mention that foam “still” traps moisture, and passive house has been building unrated or vented roofs in the East for a few years now without the issues in the article.. so NO, I don’t agree with foam or that air permeable insulation that apparently doesn’t work, is just not true… (See 475 articles)
I use in climate 4c, cellulose or mineral wool with or without an air channel with a inside vapor barrier like mento or Siga and an outer smart vapor barrier and sometimes Gutex as my exterior insulation thermal break.. it works just fine…
Image 1
Martin, I really,really like Image 1
(I also like that it is High Resolution)
GBA has posted it before for other articles.
The image shows an almost perfect storm (including the Ice & Water Sheild)
Do you know the original source for this photo and if it is possible to view other photos of this fascinating failure.
It is hard to tell exactly where the cellulose was and wasn't before the demo.....
but it appears that the areas that were packed with cellulose(lower left) show less damage.
Rafter vent channels
I would add to Martin's list of materials for rafter vent channnels, fiberboard sheathing. I use I joists for vented cathedral ceilings and staple 1/2" fiberboard to the bottom of the top cord of the I joists. It can be ripped on a table saw and installs quickly, fiberboard does have a high perm rating and may allow small amounts of moisture to pass through into the vent space. I like a vented eave and ridge and have never had a problem with this assembly. A cathedral ceiling can be energy efficient if built properly with high levels of insulaton. You also get full insulation over the outside wall top plate which eliminates ice dam potential providing the building is airtight.
other photos of this roof failure
Hi John -
This project was in Vermont in a ten-year old home and as the caption indicates, the main culprit was leaky can lights in the cathedral ceiling. But the situation was exacerbated by an attached greenhouse, which communicated with the rest of the home, and a clothes dryer vented to the indoors during the winter. Interior relative humidity in the winter was running about 60 - 65%. The roof framing cavities were filled with cellulose; the cellulose was air permeable enough to allow the can light penetration and wiring run lead the leaking moisture laden air up the rafters to the hip.
I am including a photo of the solution: spray foam held down from the top edge of the rafters so that air can be drawn up from soffit vents to gable vents in the truncated attic cavity. This roof cavity is actively ventilated with a fan, not because the remodeler who did the fix was not confident about his new roof assembly, but because the owners were so gun shy of keeping their roof assembly dry.
Response to Doug McEvers - & a video for cold-climate builders
Doug,
Thanks for your suggested addition to the list of materials for making site-built vent baffles. I have edited the text of my blog to include your suggestion.
* * * *
On an unrelated topic: The Cold Climate Housing Research Center has produced a video (below) showing one method of building an insulated cathedral ceiling. The method shown in the video is particularly appropriate for builders in climates subject to ice dams.
Dense pack cellulose in vented athedral ceilings
Martin,
It seems if one were to use dense pack cellulose in a vented cathedral ceiling the vent channel material should be rigid enough to withstand the pressure. This would be a good insulation choice especially when using I joists, batt insulation is typically sized for dimension lumber and does not fill the space completely without modification.
Response to Doug McEvers
Doug,
You're right. In How to Install Cellulose Insulation, Bill Hullstrunk said that he has had good success with AccuVent baffles, which are evidently rigid enough to withstand the pressure of dense-packed cellulose.
A comment from Bill Rose
[Editor's note: Bill Rose just sent me the following comments in an e-mail; he included his permission to post the comments.]
A few things come to mind:
1) Simple roof geometry always permits venting, tortured roof geometry does not. So if we permit non-simple geometry, then we need solutions that do not rely on venting. Or we strictly forbid complicated roof geometry, and blame future problems on designers of non-simple roofs.
2) The lead photo shows ugliness right at the ridge. There are a lot of phenomena occurring there. A ridge is actually a corner, with all the effects of corner geometry (change in film resistance, radiant reflections, shape factors, etc).
3) Ugliness right at the ridge also prompted an inquiry about still-air stratification. How do lighter molecules like water vapor stratify against the heavier air molecules? I'll leave that as a homework exercise (it's a neat one). Short answer is that buoyancy plays a big role in air movement, but stratification of still air does not.
4) Have there ever been moisture problems in any roofs caused by effects other than, first, roof leaks, and second, air flow of one kind or another? My limited experience (honest!) is that airflow always plays a role in problematic roofs. And if the answer is that air flow from below is always a partial culprit, then are we so sure of our roof-venting skills to make sure that our vent strategies provide pure dilution and play no role in inducing flow?
I forget where you leave things in the post, forgive me. But the "tipped-up commercial foam-based, no air-path sandwich" is a good approach, a keeper. I stop taking bets on cathedral ceilings that use venting in other than simple, straight-run, air-tight-underneath conditions.
-- William Rose
Response to Bill
Bill,
Thanks for your perceptive comments. I will edit my blog to reflect your point about roof geometry.
Air tightness
As Bill Rose notes, air tightness of the assembly, both inside and out, is of critical importance - we need to stop the air flow. Therefore I'd propose an assembly that utilizes materials meant to provide air tightness while also maximizing the drying potential of the roof assembly. The detail illustration I've attached shows such an approach. Solitex Mento 1000 membrane is used on the outside of the insulation - a vapor open, yet water and air-tight material - with vented cavity above - allowing for maximum drying out and preventing any wind/air penetration of the insulation. On the inside is Intello Plus, an air-tight membrane with vapor control intelligence - being vapor closed in winter and vapor open in summer - and protected with a service cavity. (Full disclosure, we are now supplying these products to the American market at http://www.foursevenfive.com.) A robust air-tight insulation assembly that doesn't require foam.
Response to Ken Levenson
Ken,
Thanks for posting the detail. Two comments:
1. Your suggestion is only a slight variation on a detail that is already discussed in my blog, namely cellulose installed with a vent channel between the top of the cellulose and the roof sheathing. You’re just using an air barrier material instead of cardboard, plywood, or fiberboard sheathing to separate the cellulose from the ventilation gap.
2. I think your proposed detail would be difficult to build. How easy is it to balance on the rafters as you install the membrane, presumably with staples, and then install the 2x2 spacers, presumably with nails or screws, all without putting a foot between the rafters? I wouldn’t want to do it.
We just did exactly this for two days — stapling Solitex Mento Plus overtop TJIs spaced 16" and 24" OC atop a two-floor residential build, followed by 2x strapping parallel to the TJIs and then another layer perpendicular for a 3" ventilation channel. The risks were high and required extreme focus maneuvering around the TJIs but we felt it was worth it to have a solid air barrier on both sides of the insulation bays. Everything got much easier after the first layer of strapping was on.
vent channels and installs
Martin,
My sense is that if we are worried about air leakage compromising the insulation's effectiveness, vent channels are problematic.
Regarding installation: While it's been successfully installed in Europe for many years, we've just gotten the material, and so we look forward to getting it on a job site soon and actually installing it - and of course, reporting back how it went.
Vent channels
Ken,
I am with Martin on this one, your detail is labor intensive for little if any gain in my opinion. The vent channels we describe can be done after the roof is on from the underside (dry side). For those of us building in a cold climate this is a huge advantage, we spend as little time as is needed on the roof. A lot of new products out there looking for a home with some tough construction details to make them work. Your system as I see it would negate the use of dense pack insulation.
That’s the problem, labor intensive? Ya can’t get something for nothing…the work that passive house accomplishes is way beyond what you do now, hence this discussion!
Robert,
The discussion above -- between Ken Levenson, me, and Doug McEvers -- isn't a debate about "passive house" versus "non passive house." It's about two different methods of creating a vent channel above the insulation layer in a cathedral ceiling.
One method is the traditional American approach, involving the installation of vent baffles under the roof sheathing. The other method is a method used in some European countries, involving stretching a membrane above the rafters before any sheathing is installed. Either method can work fine for a passive house, or for a house that doesn't achieve passive house standards, as long as the installers pay attention to airtightness.
The debate concerns whether it's difficult to balance on rafters while securing membrane, compared to working from the inside.
new products
Doug,
Admittedly these are new products for Americans but they've been used successfully in Europe for years - so not really new. It will be interesting to see how the installation is adapted to our market. I can say we are not selling these products at arms length, we are working closely with the architects and builders on these projects. Like I mentioned, we look forward to reporting back from the field.
Regarding dense pack cellulose: not sure why dense pack would be negated - I think it perfectly suited.
thanks
Thanks for the summary of this condition. Makes a good reference point.
I like the detail provided but I wouldn't call that a cathedral ceiling condition as it includes ceiling joists spanning at the bottom of the roof rafters. I would call this an insulated attic.
Yes a cathedral ceiling detail would be very similar but the challenge of many cathedral ceilings is the added structural elements, electrical boxes, and the desire for wood board ceilings all which start compromising the drywall layer which in your detail is used at the air barrier.
Where are failures
I have built dense-packed unventilated roof assemblies several times without problem. Of course I haven't torn into them either. I would like to see more examples of failures in these kinds of assemblies if they're out there.
Vented ridge only
I have to wonder if the failure in the photo would have occured if the hip and ridge was vented and everything else the same?
Dense-packing accuvent
I was skeptical of Bill Hulstrunk's claim that AccuVent baffles could withstand being dense-packed in an enclosed cavity. So at Bill's suggestion Jim Millhouse (also from National Fiber) and I ran a couple of 'tests'. Bill was right, and the results weren't ambiguous. During the process the baffles showed few signs of deflection.
To be clear, we tested the AccuVent cathedral ceiling extension, not the standard AccuVent shown in Joe Lstiburek's Fine Homebuilding article on roof ventilation. Also, a small amount of material ended up on the wrong side of the baffle, which probably means folks would do well to follow Martin's advice on sealing them during installation.
About "Where are the failures?"
Dan,
I agree with you: I'd like to see more information on this issue. I'm not aware of any failures that have occurred in properly dense-packed unventilated rafter bays. The Building Science Corp. people refer to a failed roof that, if memory serves me, was a low-slope or flat roof with many peculiarities -- not a typical installation.
I suspect that Bill Rose is right: all of these failures involve moisture that is carried by moving air. These are not diffusion failures. If the rafter bays really are properly dense-packed -- a big if -- the chance of air movement is very low.
I think that people who write building codes are concerned that, if the code allows unvented rafter bays to be insulated with cellulose, failures will occur due to sloppy cellulose installation. Some installers will fail to dense pack every cavity, and there will be rafter bays with air movement, and we'll be right back to having problems with sheathing rot.
But if the installer is conscientious, and the rafter bays really are dense-packed, my guess is that everything will be fine.
Why not just do it right plus
Why not just do it right plus build with pressure treated roof sheathing. Even standard plywood can handle wetting cycles many times more than our number one super inexpensive OSB.
Any home being built better than the absolute minimums should at the very least not use OSB for roof sheathing. Imo
Concerning post #19
Martin,
Perhaps your "memory" is from Joe's Don't Be Dense Insight and Bill Hulstrunk's comments
see post #9
https://www.greenbuildingadvisor.com/community/forum/energy-efficiency-and-durability/19174/joe-lstiburek-says-dont-dense-pack-unvented-c?page=1&cm_BOqHX%24B7W8pUB8eKwgDiDDMa_B7W8pUxeh-0=1319665667
Plywood is better than wuzwood
It won't/didn't save a bad design like Image 1
Thanks
John
Thanks for finding the thread above...note that in post #17, Robert Riversong talks about the "vented over roof". I agree with you that this method deserves some attention for cathedral ceilings.
Looking at the fatal pic I
Looking at the fatal pic I feel there might be a simple though unorthodox solution. All the rot from warm wet air meets cold wood is right close to where a vented hip may have averted all and WITHOUT vent chutes.
So a hybrid approach needs to be investigated. Dense packed cathedrals with warmside ridged foam to add R, taped, no recessed lighting or other air paths and then belt and suspenders... Add venting even though there is no normal 1" vent path.
Doug... For some reason I did't see your post #17. Looks like two of us at least think there might be a very easy inexpensive solution.
aj builder
The main flaw in this roof looks to be the ice and water membrane at the highest point in the rafter bays. Would just regular felt paper have allowed enough moisture to dissipate through the roof sheathing avoiding rot?, I sort of doubt it. Plywood clips do give a bit of spacing between 4 x 8 sheets and depending on the location may have helped with regular roofing felt. There had to be some major air leaks in the air barrier to show this kind of damage. I am a plywood devotee and never use OSB anywhere but I think under the same conditions plywood would have failed also.
Whew, I'm confused now.
Hello all,
I thank you for this impeccably timed blog, as I am currently framing my semi-basic cathedral ceiling hip roof (with short ridge). I would like to describe my detail and try to understand where I am on the right track and more importantly, where I will have failures. Hope I can amuse some of you...I feel like the more I try to address a concern, the more of a concern it becomes, and I certainly don't want to take great time, care, and detail to facilitate the demise of my roof.
The existing: hip rafters, ridge, continuously connected top plate of wall perimeter are all i-beam construction, welded together & to each adjoining member. Remaining space is filled with dimensional 2x12 @24" o.c.
The plan: Part A: I came across 1" Dow rigid foam backed 5/8CDX for the same price as the bare CDX, and I plan to double it up like a SIP, installing the bottom sheet foam side up and the next sheet on top (staggered of course) with the foam facing down, giving me 2" of insulation between the plywood.
Part B: Install ice/water shield over the whole roof.
Part C: Install treated 2x4's from eave to ridge, long bolting into each respective rafter.
Part D: Either notch the treated 2x4 spacers for fitting 1x4's horizontally across them in order to ...Part E: Install metal roof over this.
My understanding as I read this blog is that I do not have to worry about creating an air channel above the sheathed portion because of the rigid foam. So simply install the metal roof on top of the ice/water ??? Will the properties of the metal cause condensation on the backside without sufficient airflow?
Thanks for your input.
Response to Deniz Bilge
Deniz,
1. You are building an R-10 roof. That's not much insulation; as far as I know, it won't meet code anywhere in the U.S. Where are you located?
2. It sounds like you are using steel beams to frame your hips. As I'm sure you know, these steel beams are thermal bridges. All insulation has to be on the exterior side of the steel.
3. Using continuous Ice & Water Shield is sometimes risky, but it's OK if you are following the PERSIST approach and putting all of your insulation on the outside of the peel-and-stick. The method can work, but you need much more foam on the exterior of your roof.
Doug I agree, too many wrongs
Doug I agree, too many wrongs "overthinking" and overdoing. I once had to resupply a doctor building an aircraft with dozens of AN aircraft bolts because they were tightened to the point of breaking the bolts. Less is more sometimes... Along with the KISS rule.
Back to the vent idea. I really think venting a roof that is airsealed in the interior well and built without vent chutes is possibly the best way to build cathedral ceilings. I think vented roofs have too much airflow and aid interior air getting out in the first place wasting energy and moving moisture to where we don't want it.
Response to Deniz
If your climate is not too severe it's probably okay to have just the R-10 foam over the structural steel, although there's some risk that the steel could sweat in cold weather. I'm assuming you also intended to insulate the 2x12 joist bays to get your total R-value to a reasonable level. I'd suggest using asphalt felt rather than impermeable membrane, so the upper plywood has some ability to dry if needed. You are wise to include the vent space below the metal roofing.
Science-code disconnect
What a timely discussion for me!
I am building a forensic laboratory constructed in Massachusetts, and am having a difficult time reconciling applicable building code with my read of the literature pertaining to insulation and roof deck condensation.
We decided to forego ridge and soffit vents during framing and roofing, trusting advice that an unvented roof insulated with spray foam was the better option. However, subsequent research and first-hand experience examining aged polyurethane foam (in a different context) that reverted to a liquid phase due to improper mixing 20+ years ago leave me extremely reluctant to use spray foam insulation.
Heres a snapshot of the roof: 2 x 12 fir rafters (12/12 pitch), 3/4 inch tongue and groove plywood underlayment, Grace membrane near eaves/felt elsewhere, asphalt shingles. The only ceiling and roof penetration will be a plumbing vent (no can lights, ductwork, etc.). Radiant heat, room air conditioners, and dehumidifier to contain RH at or below 40% (a must for one of my spectrometers).
My read of the literature suggests a low to moderate risk of roof deck condensation for my building, which could be reduced and managed using airtight drywall installation and a low perm primer or paint.
However, the applicable code does not appear flexible, with respect to buildings like mine.
I would greatly appreciate recommendations from experts: bite the bullet and risk of spray foam insulation, or send the builders back up on the roof in December to cut ridge and soffit vents?
Thank you,
James
What about an insulated nailbase product like Cool-Vent?
Thanks for this great discussion!
I am designing a house and we are using cellulose in 2x12 roof rafters, and I came across a product that looked great. It is an insulated nailbase called Cool-Vent by Hunter Panels. It provides up to 25.6 R-value in foam insulation (in thicknesses up to 6" which include a 1" airspace and plywood) while providing a cooling vent under the shingles, and easy installation for the roofing with the nailbase. Is this a product anyone has used? And do you think it is a better solution than not providing any venting, but using layers of poly iso over the 2x12 rafters filled with cellulose - a hot roof?
Thanks,
Malka
Response to James Martin
Sounds like you have the framing and roofing in place. Your options are described in the article above--you can add venting by installing baffles below the sheathing to hold back the insulation, or you can install at least R-20 of air impermeable insulation. If you go with spray foam, choose an experienced installer who understands the effects of temperature and other factors that can lead to failure. There are many reports on this website about what happens when foam is installed improperly, and it isn't pretty.
Flat roofs, spray foam and vents
Many spray foam roofing contractors in our market are touting their ability improve efficiency on old hot tar and graveled flat roofs by adding 3 to 4 inches of closed cell spray foam. Most of these old homes are flat roofs joisted with dimensional lumber, with parapets and have stucco vents cut into the rim joists. It has always been questionable to me as to the effectiveness of the occasional stucco vent to ventilate solid lumber joists, but we see little to no rot failure in homes even up to 60 years old.
As the head of our local HBA, I have strenuously pointed out that foam over a vented flat roof assembly does not provide the insulation values promised. Some builders have suggested they could simply seal and stucco over the stucco vents and eliminate the ventilation. The problem is the rim joist is not insulated above the level of the ceiling's batt insulation and therefore creates a major thermal bridge, which could lead to condensation problems from the rsing moist air stack effect. Then they point out that the 3 inches of foam over the roof deck would keep the deck and joists warm enough to mitigate condensation.
I want to promote cost-effective efficiency in my market, but not at the expense of roof failure. We are a 5B climate zone with 6000 HDD, heating from mid-October to mid-April. We are also extremely dry at 7000 ft above sea level.
So the question is: seal the stucco vents and add the spray foam roof and don't worry about condensation? There is very little low-hanging fruit in our type of construction, especially on existing homes, which is why people are being sucked into the spray foam roof scam.
Condensation control
Martin, I think your note re: 2009 IRC table R806.4, min impermeable insulation levels req'd for condensation control in unvented roof assemblies per climate zone, needs clarification; you stated
"After you have installed the code-mandated thickness of rigid foam above your roof sheathing, you’re free to install as much fluffy stuff as you want between the rafters."
However, I presume those min levels are based on the assumption that total roof insulation levels are around code requirements given the climate zone, e.g R-38 for CZ 5 (roughly double the R-20 impermeable ins. above roof deck req'd). So if one were to create an R-50 assembly, they better be providing R-26 impermeable insulation above the roof deck. In other words--it's the proportion of above vs. below roof deck insulation that matters, not absolute R-value provided above, that determines condensation potential.
alternatives to spray foam underneath sheathing
for an unvented construction with no insulation above the sheathing, how about using wood fibreboard between the rafters directly below and in contact with the sheathing? All gaps between the boards and the rafters filled with expanding foam / sealant. You could then cover the rafters with rigid foam to bring your insulation up to required R level and reduce the risk to the rafters and sheathing, and then install your airtight drywall underneath this. Also you could install T&G OSB onto the underneath of the rafters with all joints / edges bubble glued before your rigid foam and drywall go on. This would be another air barrier in your construction, perhaps more reliable than the rigid foam and drywall alone.
Take another look at the no foam option:
Ken's detail (#10) does a good job of cold climate safety. It has what we are looking for: Good airsealing at the interior, fluffy stuff in the middle, and good drying channels for water vapor at the top. By changing from a low permeability sheeting to a high permeability membrane (at top) with venting above, there is no more concern for roof rot while at the same time wind washing is prevented in the bays by the air & water tight membrane with taped edges and seams. It appears to me to be a very durable assembly.
Changing the Intelo membrane to glued & taped OSB or Plywood with a service cavity below made of framing lumber does make the assembly much easier to build. You can now walk on the Plywood/OSB as you work since it is glued (thats why glue + Tape rather than just tape) and also supported by the service cavity (via perpendicular framing lumber).
This assembly was recently built just south of Portland OR. I posted it a couple of weeks ago. Here it is again (with the builders comments) I think it's a pretty straight forward build once you get past the idea of adding service cavities to your build.
"Albert, Mark and Michael,
Yesterday we blew the insulation and installed the SIGA Majcoat on the CAPACES Leadership Institute. There was more than 8,000 Cubic feet of insulation to install, so our insulators had 2 of their blower trucks and a good crew on site. They were blowing cellulose as fast as they could and the the rain was heading our direction.
Less than 45 minutes after the insulation was completed we had finished the Majcoat and were busy taping seams. Because there is an airspace above the insulation, I am confident that the small amount of moisture that got on the insulation will be able to dry to the exterior.
I have attached a few photos showing the installation process and the dried in roof. The roof sheathing plywood is going down as I type and the roofers will be here on Tuesday to install the membrane for the living roof."
Response to James Martin
James,
Q. "Should I bite the bullet and risk of spray foam insulation, or send the builders back up on the roof in December to cut ridge and soffit vents?"
A. Either approach will work, as long as you get at least the minimum code R-value for your roof, and as long as you use construction techniques that pay attention to airtightness. Most homeowners are happy with their spray foam jobs. Your decision depends in part on how important it is to you to avoid spray foam.
Response to Malka van Bemmelen
Malka,
Using ventilated nailbase panels is a perfectly good way to build a cathedral ceiling. The same rules apply as when using SIPs: be sure that the seams are sealed to be as airtight as you can make them, and be sure that the total R-value of your roof assembly meets or exceeds minimum code R-value requirements.
Response to Katy Hollbacher
Katy,
You wrote, "It's the proportion of above vs. below roof deck insulation that matters, not absolute R-value provided above."
From a building science perspective, you are, of course, correct. However, the code does not use building science methods. The code requirements are as I reported them. The proportion of R-value above and below the roof sheathing are not cosidered by the code.
The old Canadian rule of thumb -- at least 2/3 of the total R-value on the exterior side of the vapor barrier -- is a rough-and-ready way to address this question; it's also possible to approach the question by performing a dew-point analysis or a WUFI analysis.
In the real world, however, we're all interested in determining the actual risk and hearing failure stories. I haven't heard any failure stories related to the problem of "too much fluffy insulation below the sheathing in a roof assembly with 2009 IECC levels of rigid foam above the sheathing."
Your caveat is appropriate and conservative. For the vast majority of builders, however, the code requirements will keep roofs free of problems.
Response to Kim Shanahan
Kim,
My advice would be to seal the existing vents.
If insulation contractors in your area are installing 3 to 4 inches of closed-cell spray foam above the roof sheathing, you don't have to worry about condensation or moisture accumulation in your sheathing. You're certainly right, however, that you don't want to have any ventilation under roof sheathing that has spray foam above it.
Response to James Brown
James,
Q. "For an unvented construction with no insulation above the sheathing, how about using wood fibreboard between the rafters directly below and in contact with the sheathing?"
A. Your suggested approach probably meets code requirements, since wood fiberboard insulation isn't air-permeable. However, high-R wood fiberboard is not yet manufactured in North America, so the only way to get enough R-value using your approach would be to import the insulation from Europe. That's expensive.
Response to Albert Rooks
Albert,
I think that most contractors would worry about the buildability of your approach. The photo shows a low-slope roof over a flat ceiling; this allows workers to stand on the ceiling joists. If the roof were steep and high, however, they would have to balance their feet on the rafters while installing a membrane. This membrane needs taped seams. That's tricky, fussy, work to do without any roof sheathing. If you add fall protection equipment, it becomes even trickier.
Buildability
Albert,
Martin makes a good point.
the example you posted does look to be tricky and labor intensive.
Buildability and WORKER SAFETY matter.
Of course a high pitch roof is problematic with other Not-So-Buildable stratagems too.
I would rather be the contractor on Albert's roof ... at least I would probably survive the fall
Martin & John: Yep. Your right of course...
Magic bullet status is not achieved. It's a design for a low slope roof.
It's very much along the lines of Doug McEvers use of high perm fibre board to create vent channels above dense packed cellulose. The idea is that it might be a "quicker build" to stretch a membrane across the top, tape seal it, and then cross batten, vent, and then sheet for roofing.
Like Doug's design, the focus is on creating a high perm layer for drying to the exterior, that will still allow venting while blocking wind washing in the fluffy stuff.
The specific design shown was for a Passive House. The roof thickness & use of a service cavity might appear to be overkill for most projects, but if you want an airtight lid, a service cavity will get you there - permanently... And allow you to wire and light the interior.
Not really Vaulted
Albert, It looks like your example is a Flat Ceiling project ?
It looks like it could be used with vaulted ceilings... (scissor truss)
It looks like a lot of trouble for a flat ceiling....
You mention wind-washing ... but isn't that mostly an issue near the soffit area?
Thorsten Chlupp is in a much more challenging climate and he seems to be doing fine with simple loose fill on the attic floor....of course he is using "ample" amounts (cellulose galore)and he has baffles near the soffit.
Vaulted, compact, & sealed but drying
John,
Sure the example shown is for a low pitch (not flat) roof. But change it to a pitched roof less than 6-12 and the details are still a good method (I think). Regardless of how you assemble it, the idea is airtight on the bottom, fluffy stuff in the middle, and a high perm layer at the top that seals from the wind (and rain, and animals (to a degree), and bugs...) with venting on top of that.
It's certainly not limited to an R 80 Passive House roof. Take out the parallel chord trusses and thin it up.
Sure it's a lot of trouble. It looks like less trouble that the detail posted as example in the blog above and uses no foam... Which is a "biggie" for me.
Since you brought up Thorsten Clupp, think of it as his Arctic Wall on a pitch (new picture below & still no exterior sheeting. Just a membrane, in this case Siga Maijcoat... Amazing...)
He gets a bit more snow that needs to be shed from the roof than you might in Texas, so of course he builds a high pitched roof and puts enough fluffy stuff on the roof deck that we could both have a soft landing after jumping from Mt McKinley.
Since the point of the string is making roofs that don't fail, there are going to be assemblies that really work well but are a bit of a departure. If we had the absolute best practices that we could ever imagine, already in hand and on job sites, we wouldn't be here (at GBA) and Martin would have far less to do... I'm sure he would enjoy writing about facial cream since the building stuff has been all figured out!
JB -Greetings from Olympia!
-a.
aha.....Parallel Chord trusses
Ok. Albert.... I understand now
I thought I was looking at conventional raised heel trusses with a flat ceiling.
Yeah... I could be more clear
JB- I really ought to post sketches as Ken did. It would probably save some trouble. For me this was harking back to the compact roof string.
Experience in Yukon
I have built log homes in the Yukon Territory in northern Canada for 30 years. Most log buildings have cathedral ceilings. Most of the roofs we have built are as follows (from the bottom up): log purloins, nominal 2" (2x6) t&g decking, 6mil poly, 1 1/2" extruded polystyrene foam, 2x10 rafters on 24" centers, 7" fiberglass, 2x4 strapping, 7/16 OSB, underlayment (15 lb paper, 30lb felt, or now we would even use ice and water shield). There would be about an inch of air space below the strapping for both vertical and horizontal air flow. All roofs are vented with strip vents at the eaves and vents in the soffit (2x6 t&g) at the peak at both ends. I would disagree that venting is not needed if you stop the airflow on the warm side, for 2 reasons. First it is very difficult to stop all airflow, especially with conventional traditional practices (ie chimney and plumbing vent penetrations through the roof) We have several techniques developed over the years to seal the vb at the eaves and gables, but there are still nail penetrations through the vb. Overall I think we had very tight seals but one could never say airtight. (Then blower door tests would be pressurizing the building and seeing if it dropped at all, like testing your plumbing for leaks. The fact that we are talking air exchanges says we are not air tight.)If the warm side air barrier is compromised so much that venting creates a bigger problem then the horse is already out of the barn. When it is 70 to 80 degrees inside and -60 outside there is a pressure differential, a vented roof will let even the frost evaporate a little during the winter and will dry what little moisture there might be there out with the warm days of spring. The second reason is for keeping a cold roof surface. With 3 feet of snow (good insulation, as long as you keep it below freezing) and no ventilation just where is the freezing point going to be? Do you have 3 feet of insulation in your roof? No, so there will be times when the freezing point is above the roof, if this happens enough you will have an ice dam and a leaking roof. Even with 3 feet or more snow on the roof the only time one of our roofs will have and icicles is in the spring when the warmer days will start the snow melting and the nights are still freezing the water as it runs under the snow to the edge.
Unless one uses extreme care with the warm side air barrier and this includes knowing that all fastener penetrations are sealed as well you should assume some air flow. The installation referred to here with the ice and water shield under the shingles obviously made a better air barrier than whatever was on the warm side. But if there had been no recessed lights would it just have taken longer? IF it was tight enough that the minimal amount of moisture was able to evaporate and move out of the roof enough to keep humidity levels low enough to stop any mold and decay growth than it may have lasted for ever. But to be properly vented above the insulation would certainly help with the big IF.
Better check the walls too
If they were venting the dryer inside (code violation?) and have an attached greenhouse I bet the walls are moldy too. Start in the laundry room with its perfect moisture point source "dryer".
Can I get some more commentary on the "whole roof" of Ice & Water Shield? I think this had very little to do with the failure. The reason why I ask is I have a similar "whole roof" design coming up, HOWEVER, the rafter bays are all straight runs with soffit vents, continuous vent baffles (1/2" plywood) and continuous ridge vent. Dense pack cellulose, 2" XPS below 2x10's, air tight drywall (XPS could be sealed up too).
Thanks,
John
[Editor's note: Click "page 2" to continue reading comments.]
Response to John
John,
I used to work as a roofer, and roofs that are entirely covered with Ice & Water Shield make me nervous. I see this type of design as lazy and potentially problematic. A well designed roof shouldn't need a continuous layer of peel-and-stick, and the peel-and-stick introduces several new problems: the plywood has zero ability to dry outward, and future sheathing repairs become difficult.
I know that many people note that drying to the exterior doesn't happen with most types of roofing, and that's true. (The exceptions are slate, clay tiles, concrete tiles, and cedar shingles, as well as steel roofing over purlins.) But I remain convinced that the peel-and-stick is just one more way to push a roof assembly toward danger.
So, I believe that the best roof assemblies don't have peel-and-stick (except at eaves and valleys) and do have ventilation. These two measures provide safety.
Snow Country Cathedral Roofs
Dan Reams, thanks for your comments. I also live in snow country near Yellowstone National Park. I often have well over 3 feet of snow on my cathedral roof. I believe the dew point is often in the snow rather than in the roof. The R value of the snow is often near the R value of the roof. This can lead to massive ice dams. A simple thermal analysis shows that you cannot put a practical amount of insulation in the roof to prevent the ice dams and move the dew point into the roof. A vented cold roof is the only solution. Most roofers in the area use 100% ice and water shield. Of course, stopping air leaks is critical. A solution that works in areas with little snow may not work in snow country. Many articles I read in Fine Home Building and Journal of Light Construction do not adequately address deep snow on the roof.
Unvented cathedral questions
My home built in 63 here in Ohio has a cathedral ceiling with no ventilation. In fact there many cross-supports running perpendicular to the main joists and other framing elements that would make this unfeasible. So I want to make it an effective unvented roof.
Half of the roof has 2x8 joists and the other half has 2x12s. Right now there is a membrane covering (rubber) that's worked well for over 20 years but is showing signs of deterioration and might need replacing soon. Having done remodeling on the inside and walking on the roof I know that a lot of the sheeting needs to be replaced along with the little insulation that is there now. We've had condensation issues in the past so I now there are air infiltration and bridging issues. Any insulation will have to be done from above when I take the sheeting off.
After reading this article I have some questions. I was thinking that I would spray in cellulose from above, then put on 3/4 sheeting, then rigid foam, then the 1/2 OSB required for membrane roofing, then the membrane.
I read this "First of all, you can’t use air-permeable insulation (for example, fiberglass batts, mineral wool batts, dense-packed cellulose, or blown-in fiberglass) to insulate an unvented roof assembly unless the roof assembly also includes a layer of air-impermeable insulation (either spray polyurethane foam or rigid foam panels) directly above or directly below the roof sheathing."
Since I have the rigid foam above the cellulose should my idea work OK?
Response to John W.
John,
Your plan will work fine, as long as the layer of rigid foam on top of your roof sheathing has an R-value of at least R-20. If you are using XPS, you need at least 4 inches of foam. If you are using polyisocyanurate, you need at least 3 inches of foam.
You are in climate zone 5. I explained the minimum R-values for the approach you are taking in one of the paragraphs above, in which I wrote, "According to ... the 2009 IRC, “rigid board or sheet insulation shall be installed directly above the structural roof sheathing as specified in Table R806.4 for condensation control.” The table calls for a minimum of ... R-20 for Climate Zone 5..."
OK, I was figuring that the
OK, I was figuring that the total of the rigid foam + cellulose had to be a certain R-value in combination and had been thinking of using less rigid foam.
I've been reading about different kinds of cellulose. Since I'm installing from above would something like stabilized cellulose work since it has a little water added? I would imagine loose fill could blow all over the neighborhood! Also in the case of my 2x12 section of roof, would 11.25 inches of cellulose cause any sagging in the ceiling drywall? Does that cavity need to be filled all the way?
I notice the IRC you mentioned called for a vapor barrier for Zone 5. How could I handle this?
Thanks for your response Martin.
More answers for John W.
John,
Q. "Since I'm installing from above would something like stabilized cellulose work since it has a little water added? I would imagine loose fill could blow all over the neighborhood!"
A. You should only use an installation method that your insulation contractor is familiar with. Here in the Northeast, many contractors would probably fill your rafter bays using the dense-pack method after your new roof sheathing was installed. For more information on dense-packing rafter bays with cellulose, see How to Install Cellulose Insulation.
Q. "Also in the case of my 2x12 section of roof, would 11.25 inches of cellulose cause any sagging in the ceiling drywall?"
A. Again, talk to your installation contractor. In most cases, you should be fine -- but the answer depends on the skill of the installer.
Q. "Does that cavity need to be filled all the way?"
A. Ideally, yes.
Q. "I notice the IRC you mentioned called for a vapor barrier for Zone 5. How could I handle this?"
A. There is a code requirement for a vapor retarder in some types of assemblies, but there is no requirement for a vapor barrier. Your layer of rigid foam is already a vapor retarder. No further vapor retarding layer should be installed.
Thanks again for the answers.
Thanks again for the answers. Now I just need to find an installer in this area who knows what they're doing (so far it's been iffy)!
Zip Roof over 16" Heeled Trusses
Martin,
We had a Zip Roof installed and a metal Roof placed over it. The roof assembly is not vented and taped all around the soffits. Ideally I'd like to pack the entire cavity with blown cellulose. This string of conversations is giving me pause for thought. If I dense pack the ceiling right to the sheathing, will I incur condensation problems? I'm right on the Zone5/6 line in Southern NH. My intention is to control Indoor Humidity with a Panasonic WhisperSense Bathroom Fan With Motion & Humidity Sensors - FV-11VQC5. Can condensation be dried to the Interior?
Zip Roof Assembly
As in this.
Response to Jim Peck
Jim,
Your proposed assembly is a code violation. If you want an unvented roof assembly, you need to keep the roof sheathing warm with spray foam or rigid foam. Cellulose insulation is classified as an air-permeable insulation and can't be used in such a roof assembly.
The danger is that interior moisture will migrate to the cold sheathing, leading to condensation or moisture accumulation.
To comply with the code -- and to adopt a building system that is less risky -- you need to either include ventilation channels or you need to install a layer of spray foam on the underside of the roof sheathing, following the guidelines explained in the article on this page.
Now that I have explained the right way to do it, I will also let you know that many people have done what you propose. A few cellulose insulation dealers, including Bill Hulstrunk, claim that you can get away with omitting the ventilation channels if you do a perfect job of dense-packing the cellulose.
Why risk it, though, with a new construction job?
What formula to calculate the
What formula to calculate the amount of ventilation?
Response to Jim Peck
Jim,
Here's the standard answer for those who need to comply with most building codes (the answer comes from an article by Mike Guertin):
"The standard roof ventilation requirement used in building codes and asphalt roofing manufacturers calls for 1 square foot of "net free ventilation area" for every 300 square feet of ceiling area (attic floor area) when vents are evenly divided — half of them high on the roof at the ridge, gable, or a high roof, and half low on the roof at the eaves. The alternative is to vent only with low (soffit) vents, by doubling the "net free vent area" to 1 square foot per 150 square feet of ceiling area.
"All manufactured roof venting products (soffit vents, venting drip-edge, gable vents, roof vents, and ridge vents) are labeled for "net free vent area." In the case of soffit vent strips and ridge vents, this capacity is listed in square inches per linear foot. For fixed-sized units, the capacity is published for the entire unit. Often it's necessary to convert the square footage of vent area to the published net free vent area in inches to make sure you are meeting the requirement.
"For example, a house with a 28-foot by 40-foot ceiling has an area of 1,120 square feet. With soffit vents only, you'd divide that area by 150 square feet to come up with the "net free vent area" in square feet (1,120 / 150 = 7.47 square feet). But because the net free vent area for most vents is listed in square inches, I find it easier to convert the calculated square foot vent area into square inches. There are 144 square inches in a square foot (12 inches x 12 inches), so I multiply 7.47 x 144 = 1,075.68 square inches of net free vent area. Using a strip vent product listed for 9 square inches per linear foot requires you to make only one simple division calculation: 1,075.68 / 9 = 119.5 linear feet of vent."
Venting
Thanks Martin,
I seem to recall this but, it has been awhile. Seems there are several options for us here. Thanks for all your help and the refresher. Once again I celebrate the useful dissemination of knowledge in this technical age vs hunting for a book.
Unvented Cathedral questions
Martin,
Excellent article and discussion. I have a question about an existing unvented attic assembly. The rafters are 2x4's and the bays between them are completely filled with closed cell spray foam. I would like to add two 1in layers of polyiso towards the interior of attic and then cover with a vapor open membrane to airseal the assembly. This assembly seems like it would have poor drying potential and as such taping the seams of the polyiso seems like a bad idea. The interior covering would be either T&G planks or plywood. I am located in zone 6.
Thanks for your posts and articles
Response to Michael Collins
Michael,
You're right that this type of roof assembly won't dry to the interior. But it isn't supposed to. I would tape the polyiso -- the tape won't cause any problems.
Thanks so much
Thanks
Advice Needed - Retrofit Solution for 1915 House Zone 5/6
I have a series of questions that incorporate many of the topics that you have covered in these articles, but I am trying to apply them in a retrofit situation.
We're working on upgrading the energy efficiency, including added/updating insulation, for our almost 100 year old 2-1/2 story balloon frame house (stucco over lathe exterior). The walk-up attic will be utilized space. The location is southeastern Wisconsin, which puts us close to the borderline of zones 5 and 6. Ground snow load here is about 30lb/sq.ft.
Did I mention that money is tight?
Rafters are 2x4, 12/12 slope, and the roof is complicated with intersecting ridge lines, valleys and dormers. (The house originally had a cedar roof. The deck is the traditional spaced fir planks.) Due to the construction, there is almost no chance of getting adequate air intake via soffit vents. (On top of the layout issues, there are problems because all the spaces between rafters where they meet the top plate were bricked in, apparently at time of construction). Proper traditional flow-through underdeck roof ventilation will be difficult.
When we first looked into this project, the building inspector asked us to still use vent channels (cheap polystrene was OK) to capture whatever ventilation we could. (Note: Re-roofing is on the horizon. We anticipated installing ridge venting at that time, and maybe figure out a way to get around the soffit problems.) Rafters were furred down with 2x2's so we could fill the rafter bays with R-11 fiberglass batts against the vent channels, and then we planned to layer the underside of the rafters with 2" XPS to build up to a nominal R-21 and help limit thermal bridging.
I've started on that work, but I'm beginning to doubt whether this is the best way to proceed. I'm looking to improve things.
Q-1: Confusion over the relative merits of low/medium/high density fiberglass batts.
Would high density R-15 fiberglass batts, or even medium density R-13, be a significant improvement over the low density R-11 (beyond the nominal difference of their R ratings).
This is a hard one to figure out from the reading I've been doing. The question relates to how much (if any) the low density fiberglass loses insulation value due to convection during moderate to severe cold (wind-wash), and whether the medium (R-13) and/or high density (R-15) are really any better. The high density fiberglass seems like it should be substantially less prone to wind-wash, as it is substantially more dense, but of course just because that seems logical doesn't make it true! (It definitely costs a lot more, though!)
(Side Question - couldn't you just compress two layers of the R-11 together when filling a 3-1/2" deep space and achieve R-15 that way? Per the R-Value charts for compressed fiberglass, it seems like that should work, and then you might have a less wind-wash prone space? I ask because I've got a lot of R-11 on my hands that might not end up being used if R-15 is a worthwhile upgrade.)
Q-2: To vent or not vent the underside of the roof deck.
(Side note - as mentioned below, we hope to re-roof in the next year, so options open up then.)
If I'm already not going to get adequate under-deck ventilation due to the inability to get adequate soffit vent air intake, might it make sense to just skip the attempt at roof ventilation and maybe instead put 1" XPS in place of the vent channel on the underside of the current roof deck? (It's labor intensive, but you can achieve a pretty tight fit between the rafters.) It's a tempting idea, because that would bump the nominal R Value of the assembly to R-30. (From the top down that would be R-5 for the 1" XPS against the underside of the roof deck, R-15 for the fiberglass batts (assuming a switch to high density fiberglass makes sense) which will fill the remainder of the rafter bays, and then another R-10 from the 2" XPS spanning the underside of the rafters.)
From reading, it appears that trapping water vapor becomes a potential serious issue to be concerned about. The 1" XPS has a perm rating of somewhere between 1.1 and 1.5 (depending on what source you refer to.) The 2" XPS has a perm rating of around .7 If moisture can't easily get in from either the topside or underside, but can basically exit just as readily as it can enter, is that a more or less neutral situation?
Another issue that comes up in that scenario is whether that could promote condensation on the underside of the 1" XPS when it is cold enough outside because the underside of the XPS could be below the dew point?
Q-3: What to do when we re-roof.
As mentioned above, we hope to replace the roof this next year. If so, at that time I'd like to upgrade to either an unvented roof or if necessary a cold roof (a vented over-roof). (I don;t know that it matters in the equations, but we're looking at buying and installing stamped metal shingles. The goal would be to get an exceptionally long life span out of the roof, and to do so while putting much less weight up on those 2x4 rafters than would be the result if we used asphalt dimensional shingles.)
Something I saw in the Building Science dot Com article "A Crash Course in Roof Venting" by Joseph Lstiburek (see http://www.buildingscience.com/documents/published-articles/pa-crash-course-in-roof-venting ) looked like it might be applicable to our situation. In the article Mr. Lstiburek had a side bar titled "Master Class - Unvented Roofs", where he discussed three possible unvented roof approaches. In one of those he illustrated using a combination of insulation above and below the roof deck to achieve your total insulation requirements. His illustration shows a roof with 2" R-10 XPS on the top side of the deck, and R-30 under the deck (in the rafter bays).
That looks very appealing: go with R-30 on the underside of the deck at our house using a combination of fiberglass batts and XPS as I described above, and then add an additional R-10 (2" XPS) on the top side when we tear down and re-roof? Unfortunately that sounds like it's too easy.
Can we (does the code allow it)? Does it make practical sense? Are there pitfalls due to our climate? How might we have to modify that to fit it to out situation?
In the alternative, if we can't do a ventless roof that way, can we achieve our total insulation needs by combining the above and below deck R-Values if we top it all with a vented over-roof?
Thanks for your time and your advice! Dan
Response to Daniel Grade
Daniel,
You've got a lot of restraints, and those restraints are leading you to some convoluted thinking. Instead of advising you to adopt a series of compromises, I'm going to explain the right way to address your roof, even if the right way is expensive.
1. You should get an engineer to evaluate the safety of your 2x4 rafters. "Furring down with 2x2s" doesn't improve the ability of your 2x4s to bear the snow load. It's possible that an engineer will advise you to sister 2x8s or 2x10s onto your existing 2x4 rafters.
2. You have described a roof that is hard (or impossible) to vent, for two reasons: complicated geometry, and the impossibility of installing soffit vents. That means you need an unvented roof assembly.
3. According to the building code, an unvented roof assembly needs R-20 of rigid foam above the roof sheathing for Climate Zone 5, or R-25 of rigid foam above the roof sheathing for for Climate Zone 6.
4. Once you have R-20 or R-25 of rigid foam on top of your sheathing, you can safely insulate below your sheathing with almost any kind of insulation you want to use to bring your insulation up to minimum code requirements.
Good luck.
Response to Martin Holladay
Thanks for the input. I see a visit with a structural engineer and 35 square of polyiso in my near future.
On the subject of fluffy insulation, are there any sources you can refer me to which address the differences between low, medium and high density fiberglass batt insulation from the standpoint of loss of R-Value due to wind-wash (whether due to air infiltration or convection as a result of significant temperature differences front to back)?
Most of the information I run across seems to be from the cellulose industry that claims wind-wash is a big problem with fiberglass; and from the fiberglass industry which asserts that the cellulose group overstates the issue and that to the extent wind-wash occurs it is really inconsequential.
I have a lot of walls to re-insulate, and once the roof is dealt with I'll have rafter bays to insulate, and it would be helpful to have some insight into which type of fiberglass gives you what benefit for its cost.
The high density fiberglass is so much more dense than the medium and low density fiberglass that it seems like it should reduce the potential for convection within the batts, but at 2 to 3 times the cost of medium density fiberglass batts the gain may be nominal and not worth the added cost.
Thanks for sharing your expertise,
Dan
Second response to Daniel Grade
Daniel,
Ideally, you want to have an airtight barrier above and below your fiberglass batts. If you can achieve those two air barriers, then wind-washing isn't an issue in a roof like yours. (It can be in a vented unconditioned attic, of course, especially near the soffits.)
If you intend to build a ventilated insulated sloped roof assembly, choose a type of ventilation baffle that can be installed in an airtight manner. Site-built baffles are best.
I don't have any data from thermal performance tests of fiberglass batts that attempt to make a wind-washing comparison between (for example) R-11 and R-15 batts. But it stands to reason that denser batts will perform better. You're right that stuffing a fat fluffy batt (or two fat fluffy batts) in a small cavity can mimic some, if not all, of the benefits of a dense batt.
Response to Martin
Thanks for your response Martin. Would you still be happy to use that unvented method for a renovation situation where there is non-breathable membrane (eg bitumous 'felt') above solid board sheathing? So the build up is, from outside to in; tiles, battens, aforementioned felt, solid board sheathing, rafters with tight fitting wood fibre board between and below, airtight drywall.
Response to James Brown
James,
It sounds like you have an existing roof with tile roofing. I'm guessing that you're writing from Europe. It sounds like the insulation consists of "tight-fitting wood fibre board" between your rafters -- thickness and R-value aren't specified.
If you want to create an unvented insulated roof assembly, you probably don't want to disturb the tile roofing. That means that the most appropriate insulation would be spray polyurethane foam. Of course, the existing insulation should be removed before you install the spray foam.
However, I think you are wrong about your asphalt felt; I doubt if the felt is impermeable to water vapor. Most types of asphalt felt are somewhat permeable -- typically 5 perms when dry and up to 60 perms when wet. Since your roof assembly can dry to the exterior, you may be able to use cellulose or mineral wool insulation between your rafters, if local building codes permit the practice.
Proper vapor barrier for vented?
This article was EXTREMELY helpful, Thank you! I have one question about creating a vented assembly by making an airtght system with accuvents. If I do that then install fiberglass, then an interior vapor barrier (this is for zone 5-6) am I creating the risk of trapping moisture between the two barriers? What type of interior vapor barrier should I use, if any?
Response to Jaime Masick
Jaime,
U.S. building codes do not require the use of interior vapor barriers, even in cold climates. What they do require is an interior vapor retarder. This requirement can be satisfied with kraft facing on fiberglass batts or vapor-retarder paint.
It is far more important to have an interior air barrier than an interior vapor retarder. Be sure that you have created a good air barrier by sealing all penetrations and cracks.
For more information on vapor retarders, see Vapor Retarders and Vapor Barriers.
vented cathedral ceiling in climate zone 3, edge to zone 2
I'm opening up my house and installing cathedral ceilings, I just wanted to confirm my plan since I got second thoughts reading more and more about it. My original decision was to go with a vented roof system and R38C batts. I read a lot about the different methods and it still appears to me that this is the best. Livint in Atlanta GA we have to deal with both hot humid summers and cold winters, so humidity control is a problem, that's why I believe the vented approach is the best. Anyhow, I'm down to the rafters and roofdecking and furred out the existing 2x6 with 6" metal studs, so I have about 11.5" for insulation. Mt plan was to create a continuous ventilation under the roofdeck, my question goes towards to use baffles, xps board build baffles or insect screen nailed at furring strips to allow for the airspace. This is followed by either R38C or R30C depending on the baffle design. Next I want to cover everything with 1/2" XPS and taped seams to add insulation and guarantee air tightness as well as vapor barrier. No penetrations due to air tightness, so I go with indirect lights. Now the inside XPS will help with thermal bridging and help in the winter months to stop humidity to enter the insulation and condense at the roof decking, at lest by not using the baffles. If I use the baffles I would crate a condensation plane and trap any moisture in the fiberglass insulation. I've read a lot of problems that the baffles create. Will the air tightness on the inside that I'm planning prevent these problems? Should I rather use my insect screen baffle idea to let the insulation breathe? What will happen to this assembly in the hot humid summer, where it should be the other way around here in zone 3?
Should I use airtight baffles or not, I don't see a way to have moisture escaping in a assembly with airtight baffles, fiberglass and xps on the inside, no matter what the dew point will be inside this assembly and possibly create condensation that cannot evaporate without ventilation. It appears to me that XPS baffles or any baffles that are airtight just worsens the problem, am I missing something?
Response to Michael Meyer
Michael,
The point of the ventilation gap is not the encourage moisture to flow out of your ceiling. The point is to try to handle any moisture that makes its way there in spite of your best efforts to prevent any moisture from getting there.
You don't want to use insect screen, because fiberglass batts need to be enclosed by an air barrier on both sides. When the top side of fiberglass batts are subject to wind-washing, the moving air degrades the performance of the insulation. During the winter, the moving cold air pulls heat out of the fiberglass batts as it moves by. You don't want that.
So, whatever baffle material you choose, make your installation airtight. You can't make insect screen airtight. So use an air barrier material like plywood, rigid foam, or fiberboard sheathing.
If you want a vapor-permeable material that is still an air barrier, choose fiberboard sheathing. But use caulk around the perimeter, and tape at the seams, to be sure that the material is installed in an airtight manner.
Response to Kimbark Smith
Kimbark,
Q. "Does open-cell foam qualify as an air-permeable insulation?"
A. Open-cell spray foam is vapor-permeable but air-impermeable.
Q. "If I execute the unvented roof as designed and put 4 inches of polysio on the roof deck, can I then use open-cell foam between the rafters?"
A. Yes.
Does Open Cell foam qualify as an air permeable insulation
Zone 5/6, I am trying to upgrade my cathedral ceiling and only have 2 x 4 (real)construction. Rather than extend the rafters, if I execute the unvented roof as designed and put 4" of polysio on the roof deck, can I then use open cell foam between the rafters?
thnx
I assume using closed cell would create the dreaded sandwich?
Response to Kimbark Smith
Kimbark,
Q. "I assume using closed cell would create the dreaded sandwich?"
A. Yes indeed.
Hot humid climate-all metal cathedral roof-must use R-11 batts
Incredibly helpful (5*) thread. So, if you must use fiberglass insulation batts, and you dont have access to spray foam or closed cell boards, what do you do? I guess the key is to make it unvented and add in other air-impermeable layers.
I am about to insulate a new all-metal cathedral pitched gable roof in the Caribean. The plan is to fill the cavity between the 4" Z-purlins with R-11 batting (vapor side facing the living space). For additional heat conduction resistance we plan to roll another thinner (filleted?) layer of this batting over the top of the purlins (ie between the purlins and the sheeting). I am thinking of installing this upper batt with its facing towards the metal sheeting. We also plan to seal the underneath of this "insulated purlin cavity" with a poly vapor barrier sheet and then screw in sheetrock (to the bottom of the purlins).
The overall house is *continuously* well ventilated with lots of louvered shuttered openings (No AC). There is a 4 x 3 vented window high up on the back cathedral gable, allowing hot air to excape. Basically the set up is very different to your typical northern-US home, but could be relevant to a non-airconditioned "eco-green" South Florida dwelling.
This is where I got the above idea. It's the "Double Layer banding system."
http://steelbuildinginsulation.com/highr.html
Many of my neighbors here have cathedral ceilings, no attics and absolutely no insulation (basically they have aluzinc roofs on plywood with pine rafters). These high roofs are pretty cool, which is good as most of us cant afford to A/C. We wanted a metal roof specifically to avoid the termites that plague the latter roofs eventually.
1) Is my plan OK?
2) Will we need more air barriers (how about above the top layer of batting, just below the metal sheeting)?
3) (bonus) How would you go about installing this roof?
Answers to any of the above are very appreciated.
PJ
Response to PJ PR
PJ,
I don't have experience building in the Carribbean or building steel buildings, so I'm not the best person to comment. But here are a few reflections:
1. You don't want an interior vapor barrier. In a hot humid climate, the vapor drive is always from the exterior toward the interior (assuming your building is air conditioned). If your building isn't ever going to be air conditioned, the vapor drive will still be from the exterior to the interior, but there won't be much vapor drive. If you want any kind of vapor retarder -- and I'm not saying you need one -- it would go on the exterior side of the insulation, not the interior.
2. Whenever you install fiberglass batts, air barriers are much more important than vapor control. You need a good air barrier on both sides of your fiberglass batts. A material like MemBrain (with taped seams) is one possibility. Other materials that can be used to create an air barrier are plywood with taped seams or gypsum drywall.
Hi Martin,
Thanks for the
Hi Martin,
Thanks for the feedback. We will never A/C the building (it will be solar powered). The wind is pretty constant, but it is a humid environment, so moisture control is certainly on my mind.
You say "You don't want an interior vapor barrier," but you also say that "you need a good air barrier on both sides of your fiberglass batts." The latter would turn out to be an interior vapor barrier not so? Ie. If I install a polyethlene sheet between the bottom of the batting and the sheetrock [it would be attached to the purlins], wouldn't this be an interior vapor barrier? Maybe I'm not getting what you mean by an interior vapor barrier.
The other question I have is will the gypsum sheetrock be enough (do I need the polyethlene)?
Cheers ,
PJ
Response to PJ
PJ,
Q. "You say 'You don't want an interior vapor barrier,' but you also say that 'you need a good air barrier on both sides of your fiberglass batts.' The latter would turn out to be an interior vapor barrier not so?"
A. No. Not all air barrier are vapor barriers. For example, gypsum drywall is an air barrier, but it is not a vapor barrier. Similarly, MemBrain is an air barrier but not a vapor barrier. For more information on these issues, see these two articles:
Vapor Retarders and Vapor Barriers
Forget Vapor Diffusion — Stop the Air Leaks!
Q. "If I install a polyethlene sheet between the bottom of the batting and the sheetrock [it would be attached to the purlins], wouldn't this be an interior vapor barrier?"
A. Yes, it would. I don't recommend the installation of interior polyethylene in your climate.
Q. "Will the gypsum sheetrock be enough (do I need the polyethlene)?"
A. If your goal is to install a good air barrier, then drywall is certainly adequate, as long as you seal all penetrations to avoid air leakage. For more on installing drywall in an airtight manner, see Airtight Drywall.
Light on regarding vapor & air barriers
Aha....I get it now.
Our cooler mornings may make the interior of my metal roof sheeting to sweat slightly since it will be in contact with the warmer unvented fiberglass-insulated purlin "cavity" underneath. Once our hot Caribbean sunshine starts to kick in I want this moisture to dry and/or diffuse out of this cavity, through the gypsum sheeting, into the cathedral living space below, to then be blown out of my 4x3 gable window. A vapor barrier would completely retard this process. Finally, the reason for installing an air-sealed gypsum drywall is to LIMIT the amout of humid air that gets into the purlin cavity in the first place. Consequently, as much as possible of the hot daytime humid air is directed out of the interior building space by the Caribbean breeze flowing through the continously open shutters that I installed. How does that sound?
Aside: I wish I had access to foam spray or the foam boards. But we can only get our hands on double bubble or R-11 batts (the latter arrived today).
Finally (I promise this is my last topic). Regarding my fiberglass batts: Will the facing that comes with it retard the drying out process that I described above (does it matter what side I put it on within the purlin cavity?) and will 2 layers of R11 be too much to compress in my 4" purlin space (I realize that codes in the US call for more insulation, but I will have a good amount of cool breeze flowing through my house). The folks at http://steelbuildinginsulation.com/highr.html say I should filet an inch off the upper batt, concur?
Thank you Jedi masters at greenbuildingadvisor.....PJ
1st layer of R11 going on ...
Well the roof is going on with the first layer of insulation (on-top the purlins, under the roof sheeting). There appears to be enough space left in the 4" purlin cavity for the second layer of R11 to be installed without any modification. I realise however that, having been compressed for so long in these big rolls, the fiberglass may "swell up" over the next few days... We shall see.
Any thoughts about the paper facing? (see my post immediately above). Obviously (from the photo) the first layer was installed facing up. The second layer I propose to install face down.
The plan is to install it (from the inside of the house) about the same time the drywall is put up. I will instruct my crew to make sure there are no air pockets in the purlin cavities & no air flow into the latter. I will supply them with cans of great stuff to make sure they get to all the gaps.
Thoughts? ideas? PJ
Flat roof cathedral ceiling
We're going to give it a try. Existing is a fourteen year old roof with 2" of closed cell roofing foam with an acrylic elastomeric coating. Below is 1x decking and 2x4 rafters. Our plan is to put rigid board up between the 2x4's, caulk the edges, and then hang sheetrock. We'll air seal the one electric junction box for the room light. And cross our fingers.
This is in the San Francisco Bay area fog zone (a heating climate).
The one question: should we vent the space above the sheetrock to the interior?
Response to Bryce Nesbitt
Bryce,
Q. "Should we vent the space above the sheetrock to the interior?"
A. No, that won't be necessary.
Old cottage cathedral ceiling
I have a 50 year-old seasonal cottage in a northern climate. The simple 6/12 gable roof is composed of actual 2x6 rafters (24" oc), sheathed with 1/2" plywood and covered with asphalt shingles. There is no insulation in the ceiling and I suspect little to no effective insulation in the 2x4 walls. In the summer the heat gain inside makes living almost unbearable. I suspect that the biggest bang for the buck would be to address the ceiling insulation issue first, but would like to maintain the interior appearance. Would it be reasonable to strip off the shingles, lay down (in order inside out) 6mil VB, high density foam board (6 to 8"?), roof deck and shingles? Would it be better to strap under the new deck with 2x's from eave to peak to vent the deck? Is a separate VB necessary with that thickness of foam board? Any advice would be appreciated. Thanks.
Question: Bunkhouse
Client wants exposed cathedral ceiling (cool moist climate - Zone 5-6).
I looked at the unvented schematics and I am not sure that fits the bill for up here (Canada - west coast).
My feeling is that the dew point profile would end up in the XPS foam board, hence a VB should be put on first deck.
In order of assembly:
Rafters
1/2" ply
Blueskin (peel'n stick rubber membrane - VB)
2 layers of 2.4" XPS glued and taped
Furring strips 1/2" over XPS aligned with rafters held in place by 8" screws into rafters
1/2" ply
Roof felt
Asphalt shingles
Bug screen for vented space between XPS and ashpalt deck, and ridge cap vent.
Any thoughts would be appreciated. Melli
Response to Mellisa Macmillan
Mellisa,
Condensation cannot occur in the middle of a chunk of XPS because the XPS is neither air-permeable nor is it particularly vapor-permeable. More information on that issue can be found here: Are Dew-Point Calculations Really Necessary?
The peel-and-stick membrane is still a good idea, but its main purpose is to act as an air barrier, not as a vapor retarder.
Your assembly calls for about 5 inches of XPS, for a total R-value of only R-25. That's not much. If you are going to all that trouble to build a complicated roof assembly, you should aim higher. U.S. building codes call for a minimum of R-38 ceiling assemblies in a climate like yours; that would require at least 8 inches of XPS.
Thanks Martin! Yeah, I agree
Thanks Martin! Yeah, I agree that with XPS being closed cell, it's ability to hold vapour is limited. As far as the R-value is concerned, it is the clients wish, not mine...I'd have the cavities filled...
I have a thing for blueskin, as a both an air and vapour barrier, but also it will act as a seal for the screws that hold everything down. In reference to the vaulted schematics on this site, it shows vapour/air barrier on top of insulation, which got me wondering. As good as I am installing materials, nobody is perfect, and an air leak may develop between XPS seams. Once ANY moisture gets down to lower sheathing, it is game over...imho. Being on the wet coast, it means mold.
I've been pouring over the Dow site looking at compressive strength of XPS - 30psi. I've heard through a suspect grapevine that XPS, after repeated compressions, loses it's shape. Some folks have taken to putting in furring strips between XPS boards to support XPS. This seems counterproductive (thermal break). I think I found that confirmed on the Dow site, but their application instructions lost me...lol
fiberboard
I'm a homeowner in Seattle. Have a newly-framed, vented cathedral ceiling to insulate. Straight bays, 2x12, 24" o/c. The current plan is to use batts of some kind in the bays, take care to air seal the interior surface, avoid penetrations, air seal the vent channel too (bays fully sealed), double prime the inside surface for vapor resistance. I have a couple questions about baffling the vent channel:
1. Some of the building professionals I'm working with feel the jury is still out on baffles and are recommending leaving the batts open to the channel except near the vents, assuming the 1-2" air channel can be maintained. Concern is condensation on the interior surface of the baffle. Is this really still an open design issue? I thought wind-washing would degrade the performance of the batts. Is Seattle's moderate climate at play? Do we need to take extra steps for vapor resistance on the inside surface?
2. Assuming the baffle is still necessary, any recommendations on fiber board? From a web search I see there are many brands. Bildrite's site says their product is vapor permeable (good), but I don't know about the others. Will Homosote work? What about hardboard? - that's cheap at Home Depot and seems water would run off pretty well.
Response to Jim Bohrer
Jim,
The thermal degradration in the performance of batts due to wind-washing is a much bigger problem, in my opinion, than any risks due to moisture accumulation. If you pay attention to airtightness, you shouldn't have any moisture worries. So, yes, you need a top-side air barrier.
All fiberboard products that I am aware of, including Bildrite fiberboard and Homosote, are vapor-permeable. I don't know about the vapor permeance of Home Depot's hardboard, however.
Closed cell foam and a roof leak
We have been recently installing a lot of closed cell foam directly to the roof sheathing with great results. However I wonder if you have heard about what happens when the inevitable roof leak occurs? I imagine it builds up hyrdostatic pressure until it finds a way out, but that could take years and could rot a great deal of the roof before anyone notices. On top of that, many roofs are being covered with very low permeable underlayments. This concerns me...any thoughts?
Response to Bo Jespersen
Bo,
You are not the only person with this concern. For those who (like you) are concerned about the issue, there are two choices:
1. Stop using spray foam.
2. Install sturdy site-built ventilation baffles in each rafter bay before you spray the foam. That way you end up with a vented cathedral ceiling.
I like it
Right on! Venting the slope protects the sheathing from being caught in between two vapor barriers/retarders and gives the water a place to go when there is a leak....a technique I will start using immediately.
Thank you very much Martin.
Insulating existing ceiling
ok, so I'm a little worried reading this thread. I have a great room that is paneled on top of the rafters, which are 4x8, and I installed sloped cans and was going to insulate and finish ceilings. My primary purpose of doing this is that the roof is directly on the beams and it gets very hot in the summer, winter not so much of problem as I live in San Diego and temps rarely dip below freezing. Since it is existing and has no vents, and I don't want to tear my roof off at the moment, looks like I have to go with unvented system. Looking for any suggestions or opinions on what my best option or two looks like?
Response to Joe Lethert
Joe,
Your description is confusing. I'm going to try to see if I understand what you are saying.
I think you mean this: Your cathedral ceiling is presently uninsulated. When you are indoors looking up, you can see your rafters. Above the rafters you can see a layer of boards. Is that correct?
If I understand correctly, you have just finished installing some recessed can lights, and now you want to know how to insulate around and above these can lights. Your intention is to install a new finish ceiling, under the rafters, once the insulation is installed. Is that correct?
Assuming I got that right, here is my advice.
1. Remove the can lights and throw them away. Recessed can lights should never be installed in an insulated cathedral ceiling.
2. Go to a good lighting showroom and choose some surface-mounted ceiling fixtures that you like.
3. Install electrical boxes at the locations where your surface-mounted fixtures will be installed.
4. Insulate the rafter bays with spray polyurethane foam, as described in the article.
5. Install your new ceiling.
unvented attic and rigid foam in rafter bays
Thank you for this detailed article and discussion.
First, is it easy to identify whether a roof is ventilated? If no soffit vents or side vents are visible on the roof from the ground, does that mean the roof is not ventilated?
Second, can you please confirm this: "If you want to use just one type of insulation in unvented rafter bays, you are limited to spray polyurethane foam."
I have been using rigid breadboard style expanded polystyrene in the rim joists and thought the same could be put under the sheathing between the rafter bays, and with any gaps sealed with a urethane spray foam such as Fill and Seal. Is there a quality which makes spray foam acceptable and rigid foam unacceptable?
Thank you.
[Editor's note: An answer to this question has been posted on Page 3. Click the box below to reach the next comment page.]
Response to Erich Riesenberg
Erich,
Q. "Is it easy to identify whether a roof is ventilated?"
A. Not really. One of the problems is that many U.S. roofs are "kind of" ventilated. The builder may have included polystyrene baffles, but didn't realize that the valleys and dormers interrupted the ventilation. Or maybe there used to be a ridge vent, but when new roofing was installed, the roofer just ripped out the ridge vent and roofed over the ridge. At that point, the rafter bays are "kind of" ventilated, but not really.
It's safe to say that an existing house doesn't have good roof ventilation if there aren't any soffit vents or ridge vents. It's also safe to say that, even if there are soffit vents and ridge vents, the roof isn't really ventilated if it includes valleys, hips, dormers, or skylights.
Q. "I have been using rigid breadboard style expanded polystyrene in the rim joists and thought the same could be put under the sheathing between the rafter bays."
A. This is a gray area in the building code. It's safe to say that no commercial insulation contractor would use that technique, which many people call "cut and cobble." It is fussy, time-consuming work, and it is hard to be sure that everything is properly air-sealed. It's the kind of approach that is used by a homeowner with lots of spare time and the idea that they may save a little money.
If you want to use rigid foam, the best place to put it is on top of your roof sheathing, not under your roof sheathing.
That said, if your local building inspector approves of your plan, and if you have lots of time on your hands, and you are capable of doing a meticulous job of air sealing, you can go ahead and try the cut-and-cobble approach.
cobble is the right word
Thank you Martin. Installing about 100 linear feet of rigid foam in the rim joists, 2 layers at 2 inches each layer, has taken perhaps 35 hours. It is tedious but this is my first work with foam and it does get easier with experience. As to cost, the foam is probably $35 and the spray foam and caulk to seal about $30.
Having spent all my life behind a desk working on this is a bit of a break. The roof is going to be done in perhaps 4 sections so may try rigid foam and spray foam to compare what works. Rigid foam is tedious but minimal sticky residue. Thanks.
unvented spray foam + polyiso inside
Martin, you wrote:
"To summarize, there are three ways to build an unvented roof assembly:
- Install spray foam (either open-cell foam or closed-cell foam) against the underside of the roof sheathing, and no other type of insulation. Be sure that the thickness of spray foam is adequate to meet minimum code requirements."
This is an option I'm considering in my house to save the previous owners newly installed roof shingles, but the depth of the rafters cannot accomodate enough insulation to meet code. I'm wondering if I should furr out the rafters to get the desired thickness of spray foam, or if installing a few inches of polyiso foam to the underside of the rafters, after the spray foam, could work? I'm not certain which is cheaper, but the added foamboard on the underside of the rafters would reduce thermal bridging, so I'm leaning towards this option but I'm not sure I understand your quoted advice above. Suggestions?
Response to Mark Fredericks
Mark,
Q. "I'm wondering if I should furr out the rafters to get the desired thickness of spray foam, or if installing a few inches of polyiso foam to the underside of the rafters, after the spray foam, could work?"
A. As I wrote in the article, "Most rafters aren’t deep enough to accommodate the insulation needed to meet minimum R-values required by code, especially if the rafter bays include a ventilation channel. ...
Builders solve this problem by furring down or scabbing on additional framing below the rafters to deepen the rafter bays. Another technique is to add a layer of cross-hatched 2x4s, 16 inches on center, installed beneath the rafters."
If you install 2x4s (or 2x3s on edge, installed with long screws) perpendicular to the rafters, you will address most of the thermal bridging concern without the need to add a layer of rigid foam.
Engard in the rafters
I'd like to do a unvented cathedral ceiling but don't want to use any spray foam. So I guess my options are (1) SIP roof or (2) exterior foam with cellulose on the second floor ceiling. The roof has a 12:12 pitch, so we are actually dropping the ceiling through the second floor. There will be plenty of room to pump in cellulose. One other option I was wondering about was whether Engard batts could be use in between the rafters with rigid exterior foam. Does anyone know if spun polyester is considered an air barrier.
Steven Knapp
Steven,
EnGard insulation is a type of fibrous insulation that resembles a fiberglass batt. It uses polyester fibers instead of glass fibers. It is definitely not an air barrier. If you intend to install EnGard insulation batts in an unvented cathedral ceiling, you'll need to have a significant layer of rigid foam insulation above the roof sheathing.
Commercial unvented roof question
Martin,
I'm dealing with a little different condition that I'd love some input on. I'm building a winery tasting room in a masonry building (8" monolithic concrete walls) in 4C/5B climate zone in So. OR. I've got an exposed 2x10 T&G ceiling over GLB purlins @ 5'oc, so I'm building it from the bottom up and the last layer to go on is the sheathing under the metal roofing. I had planned to install an air barrier over the T&G deck (taped felt) then frame 2x8 @ 24"oc with high density batts to fill the cavities, over which is the sheathing under the metal roofing. I can't really spray foam the underside of the top sheathing layer, so would I be achieving the same effect with rigid foam over the sheathing / under the roofing? local code for commercial only calls for R-30, so I can get that in the 2x8 with high-density batts. Can I just tape the top sheathing layer? Thanks for your input
Response to Milo Shubat
Milo,
You don't explain whether this is new construction or the renovation of an existing building. I rather suspect it is a renovation -- or else one might think that the designer of the building would also have provided a design for your roof.
You describe your proposed air barrier as "taped felt." I don't think asphalt felt can be successfully taped, and I don't think that asphalt felt makes a very good air barrier.
As I explained in the article on this page, you can't use fluffy (air-permeable) insulation in an unvented roof assembly unless you include rigid foam or spray foam above the fluffy insulation. So you will need R-10 or R-20 (depending on your climate zone) of rigid foam insulation on top of the fluffy stuff.
Most commercial roof assemblies don't bother with the fluffy stuff. They just meet 100% of the R-value requirements for the roof with rigid foam (either EPS or polyiso) and skip the batts entirely. That's the way I suggest that you proceed.
Any commercial roofer in your area should be familiar with this type of roof assembly.
Commercial unvented roof question
Martin,
Thanks - this is new construction, I'm the designer / builder, and the more I look at it, I'm liking all rigid - less fussy. The top layer of rigid over fluffy makes my eave too thick anyways. The air barrier for the T&G ceiling is actually the sandwich of felt and taped 3/8" CDX.
Response to Milo Shubat
Milo,
Taped CDX plywood makes a good air barrier. It sounds like you are all set.
Unveiled air space
Situation similar to Eric, above. If closed cell foam is sprayed or "cobbled" from xps, do you have to fill the entire space, or only to thickness for desired R value? Can space between rigid foam and drywall be left empty? Or must it be filled with fluffy stuff or more rigid foam the he rafters are a full 8" deep. The ceiling is in zone 3.
Response to Annemarie Belteu
Annemarie,
I don't know what you mean by "unveiled." In zone 3, you need at least R-30 of insulation (which means 6 inches of XPS). Once you have installed R-30 of spray foam or XPS, you're done. You can leave an air space between the bottom of the foam and the drywall if you want.
Of course, you'll still have thermal bridging through the rafters. But you won't have any moisture problems.
polyiso facing question
I have an unfinished attic, with cathedral ceiling, no insulation at this time. in 5-10years we will be adding dormers, but in the meantime i would like to add insulation and drywall in the simplest, most reversible/salvageable manner. My plan is to hang 2 layers of 2 inch polyiso under the rafters, taped with staggered seams leaving the rafters empty, so essentially a vented assembly. I have added blocking to the floor joists and will make the polyiso continuous in the knee walls. I thought i would add furring strips on top of the insulation then hang drywall, thinking that the furring strips would create an airgap, allowing the foil to act as a radiant barrier. While this won't provide ideal R-value it should make a significant difference for a reasonable cost, $ and labor. 1) does this make sense or is there a better option? 2) i've recently gained access to cheap roofing polyiso--black backing on both sides. My feeling is that putting this backing against the rafters in contact with that vented air might be inviting a mold problem, and if i face it towards the room i lose the radiant barrier. Please advise and thank you!
Response to Joell Solan
Joell,
Q. "Does this make sense or is there a better option?"
A. It makes sense to you because it meets your needs. As you are aware, it's not an ideal way to insulate your roof assembly. But you have described it as a temporary stop-gap measure.
Q. "I've recently gained access to cheap roofing polyiso -- black backing on both sides. My feeling is that putting this backing against the rafters in contact with that vented air might be inviting a mold problem, and if i face it towards the room i lose the radiant barrier."
A. The polyiso will not create a mold problem. While you are correct that black facing does not provide a radiant barrier, the difference in performance compared to foil-faced polyiso would be minor.
Bringing ducts "inside" and duct condensation
I have a partial cathedral ceiling in the finished attic of my house in zone 4 (TN). Each slope of the roof is divided roughly in thirds by 3 different situations: knee walls at the outer thirds, "cathedral" ceiling in the middle thirds, and a vented "attic" in the middle third with a ridge vent - a common situation with finished attics, at least around here. I have a big problem in the summer with overheating. The insulation isn't working well because it was poorly insulated with just R-19 fiberglass batts between the rafters without a ventilation baffle or adequate soffit venting and only r-19 blown into the "attic space". Moreover, my upstairs HVAC ducts are run in the really hot "attic" space under the ridge.
Based on what i haved learned from several articles here, my planned solution is to cathedralize the entire roof, eave to ridge: install continous air-tight site-built 2" vent channels using foil-faced polyiso board (as suggested in http://www.buildingscience.com/documents/published-articles/pa-crash-course-in-roof-venting), installing continuous soffit vents to drastically improve the airflow from soffit to ridge, creating an air-tight ceiling below the rafters, and, most importantly, bring the ductwork inside the conditioned envelope. I plan to fill the rafters with rigid polyiso to yield r-30, but might opt to fur out the rafters and use fiberglass or cellulose instead. My plan is to leave the ductwork "exposed", hanging below the ridge and above the collar-ties that run between the rafters. (The idea to dress up my round ductwork with a clean white insulated wrap and disguise the collar ties as solid beams by wrapping in a plywood box.) Once that is done, knee-walls and room partition walls can go back inside the new air-tight ceiling. Hopefully this is a sound plan... Let me know if I missed anything.
Other than asking you readers for a review of my plan, I have another question brought about by concerns expressed by a local builder. He is concerned that once the AC ducts are inside the conditioned space that the ducts will be prone to sweat and will drip all over my furniture. He has suggested that I will need either expensive internally-insulated ducts (like some restaurants use) or I will have to make sure that my duct wrap will be sealed enough to "hold" any condensation.
If the air inside my house was humid unconditioned air, I would be equally concerned. But won't the inside air be relatively dry due to the on-going air conditioning? Should I be concerned out condensation forming on my AC ducts if I cathedralize my ceiling?
Thanks, Jim
Yes, duct condensation can be a problem. Conceptually, some additional air handler air bypassing the evaporator coil (which will increase duct temperature) is another way of addressing the problem.
Response to James Anderson
James,
Your plan to install a stack of rigid foam rectangles in each rafter bay is called the "cut-and-cobble" method of insulation. It is a method often chosen by homeowners, but never chosen by insulation contractors. Spray foam would make more sense, because cut-and-cobble is fussy work that takes a very long time to do well. (The perimeter of each piece of rigid foam needs to be carefully sealed with caulk or canned spray foam.) Good luck.
I live in northern Vermont, and I don't have enough experience with air conditioning to answer your question about condensation on interior ducts. I suspect that you won't have a problem; but if you want a more informed opinion, you should post your question on our Q&A page, where more GBA readers are likely to see your question.
Cathedral Ceiling repair work
Dear Experts:
I am a homeowner with cathedral ceilings that were added during remodeling and expansion of my home in the late 90s. Only the ridge beam is exposed. The rest of the ceiling is covered with drywall. Through the years there has been some condensation leak down the side of the ridge beam on some mornings in March/April.The home is about 4 miles from the coast in Southern Califonia, so zone 3b. There are 4 recessed lights in the ceiling on the side of the beam that gets the condensation, but there are also lights on the side that is always dry. There is no air conditioning in the home. Heat is used during the night only about a dozen nights a year, not during the condensation. Usually the windows are open. It seems the condensation shows up on mornings when there is no marine layer (no clouds in the morning) and the temperature heats up fairly early after a very cool night. The problem ceiling faces east/west and the condensation is on the east facing side of the beam. The roof is black asphalt shingle. I know that there is no caulk/sealant between the side of the beam and the place where the drywall butts against it, so there is a small air gap there. My memory is that fiberglass insulation was used. There is definitely no vent in the roof, but I seem to remember that the insulation didn't go all the way to the beam, a gap was left as would be if there were to be a vent.
My theory is that on those mornings that heat up fast the moist air that got inside and cooled the beam at night heats up fast with the sun shining on it and the beam stays cool for a few hours and "sweats." I've been contemplating a way to fix this without tearing open the whole roof or ceiling. I'm getting some scaffolding to acces it, it's a 14 foot ceiling, and I want to cut open a small access hole in the drywall to make sure the framing is not rotting from the occasional moisture. After that I want to find a way to get some insulation into the void around the beam for the whole length of the beam. The joists are 2x8 and the beam is 6x14. I figure the gap between the beam and drywall needs to be sealed and I also want to clean up the look of the beam by sanding off the water stains. Is there any way for me to insulate around the beam without opening the ceiling, like drilling holes and spraying some kind of insulation inside? Hope I didn't leave out anything important.
S.Chapman
Response to S. Chapman
S. Chapman,
Here is what you wrote: "I know that there is no caulk/sealant between the side of the beam and the place where the drywall butts against it, so there is a small air gap there. My memory is that fiberglass insulation was used. There is definitely no vent in the roof."
You are describing a cathedral ceiling that incorporates all possible mistakes. There was no attention to air sealing. The worst possible insulation was used (fiberglass). And the roof assembly is unvented. So it is no surprise that you are seeing condensation.
I doubt that the condensation is occurring against the cold ridge beam. Rather, I think it is likely that condensation is occurring on the underside of your ridge shingles or the underside of the asphalt felt underlayment.
To prevent moist interior air from contacting cold surfaces near the ridge, you need a real air barrier and a real insulation layer. The right way to fix this problem is to expose the rafter bays -- either from above or below, it's your choice -- and pull out the fiberglass insulation. Put the fiberglass in a dumpster. Then fill the rafter bays with spray polyurethane foam.
If you want to attempt a halfway solution that may or may not work, you can cut out some of the drywall near the ridge, and install spray foam insulation on the underside of the roof sheathing, just in the area near the ridge beam. (From the ridge to perhaps 12 inches down from the ridge on both sides.) Then patch your ceiling. This may solve your problem.
Thanks for the confirmation
Thanks for the confirmation and advice. Since everything is dry this time of year and the home was recently tented for termites, I will insulate by the beam and seal up the obvious air entryways. Once I can see inside I think I'll have a better idea how much moisture has been in there over the years. I can also see if there is improvement next spring. Then when it is time to reroof I'll have to take care of the rest. That gives me some flexibility to plan the timing.
Ironically, my former husband was the contractor/engineer who did the work, and he now works as an expert in construction defect litigation. I wonder if I should mention this problem to him? lol
SC
Venting an arched cathedral roof
Martin,
I'm a bit stumped on this one - I'd like to vent this roof assembly, but I can't say whether there will be a natural convective flow as there would be with rafters sloping with the roof pitch. My rafters are running level but they sit on parallel curved top plates. I can use 12" rafters and make 10" of batt work, leaving plenty of ventilation space. I can drill the tops of the engineered joist flanges to allow ventilation 'up-slope' (perpendicular to the rafters) as well as in the rafter bays, and I can provide continuous perimeter ventilation (Cor-A-Vent strip) at my roof fascias (eave, ridge and gables). Can I assume that any exterior air movement will promote a natural convective draw through the assembly without an otherwise typically sloped rafter layout? I am maintaining a neutral air pressure in the assembly, which leads me to believe the moisture won't otherwise be trapped in the roof.
Venting an arched cathedral roof
Here's a graphic for the roof framing
Response to Milo Shubat
Milo,
I think you should take one of two approaches: either:
(a) design this roof as an unvented roof, using spray foam or rigid foam above the roof sheathing, or
(b) install curved ventilation channels above the roof sheathing, perpendicular to the rafters, with a second layer of sheathing on top of the ventilation channels.
Venting an arched cathedral roof
Martin,
Thanks for the reply. For reference, it's in a 4C (mixed marine) climate zone.
I don't have a lot of room above or below the roof structure for insulation / venting. Would a flash / batt unvented assembly work under the single sheathing deck? My insulator has done quite a few of these locally.
Are you thinking the 'flat' vented cavities won't provide the assembly with an exhaust path for moisture?
Reponse to Milo Shubat
Milo,
Needless to say, sometimes you need to plan ahead to be sure that your rafters are sized adequately to allow for insulation and venting. For more information on acceptable ways to insulate low-slope roofs, see this article: Insulating Low-Slope Residential Roofs.
Venting an arched cathedral roof
Thanks Martin - Now I see why my original plan for a SIPS envelope was so elegantly simple. It looks like min R-10 sprayed under the roof sheathing and then a full-fill of the bays with batt / fluffy, and a vapor sealed drywall lid will get me the 'hot' (unvented) roof system the SIPS was from the get go.
With this system , there's no problems with a full peel-stick roof underlayment on top of the deck is there? I have a metal roof on this project and the underlayment will be fully adhered to the roof sheathing.
Response to Milo Shubat
Milo,
I'm not a fan of full peel-and-stick roofs, for a variety of reasons. But your plan will probably be fine. Just make sure that your roof sheathing is dry on the day you install spray polyurethane foam -- because the sheathing won't be drying very much in either direction after it's encapsulated between peel-and-stick membrane and spray foam.
If you choose to install open-cell spray foam instead of closed-cell spray foam, your roof assembly will be able to dry somewhat to the interior. Just make sure that the spray foam layer is thick enough to keep your rafter bays above the dew point during the winter.
Cathedral ceiling question
I am changing my ceiling to a cathedral ceiling. I am at a mile high in southern california so I get some cold winters, but very dry mild summers and 13 1/2 inches of precip at year.
I want to properly insulate my cathedral ceilings and was thinking to spray 2 inches of closed cell foam to sheathing, then fill with dense packed cellulose. I am wondering if I can attach craft paper and pine paneling to the 2x8 rafters and then fill the bays with cellulose. I.e. can I do it with out drywall? I don't want to add the extra weight and I figure that if the cellulose is dense packed, it will reduce fire spread similar to how drywall would serve that concern.
Any thoughts or suggestions?
Response to Daniel Cabe
Daniel,
Code interpretations are subject to the determination of your local building inspector. Ultimately, it doesn't matter what I think -- what matters is what your local code official thinks. So ask him or her.
It wouldn't surprise me if your building official insisted on a layer of drywall.
response to milo
sips are great but in the coldest of climates they have encountered problems. google problem applications in alaska - apparently a group of homes there were built but not enough attention to detail for the plumbing and roof vents were taken into account (absolutely air tight foamed in penetrations), mated panel seams and fastener punctures caused the top level osb to rot. needless to say the whole roofs needed replacement.
What to do with ridge vent in unvented assembly
We plan to convert to an improperly vented cathedral ceiling to an unvented one. Sealing up the soffit vents is a no-brainer. What's the best way to deal with the ridge vent? Thanks!
Response to Hari Kamboji
Hari,
Air sealing methods are similar in all areas. Big gaps are filled with solid materials (rigid foam, plywood, or OSB). Somewhat smaller gaps are filled with spray foam. Narrow gaps are filled with caulk.
WSU for Valleys/Eaves/Low-Slope on Unvented Cathedral
It makes sense to make sure the top layer of sheathing can dry to the exterior when using rigid insulation on an unvented cathedral ceiling. But what about the recommended waterproof underlayment for valleys, eaves, and low-slope sections of roof?
I have gotten to the stage of laying down the tar paper for the unvented cathedral ceiling on my self-built house and don't know if I should add waterproof shingle underlayment to the valley, eaves, and a 2 in 12 section of roof. I see that it is added in the drawing detail found here:
https://www.greenbuildingadvisor.com/cad/detail/unvented-roof-cold-climate-cathedral-ceiling-asphalt-roofing
Is it okay to add peel-and-stick membrane to select areas of the roof and keep the rest breathable with tar paper?
I attached two photos—the two taped layers of polyiso, and the current stage of the roof
Response to Eric Matsuzawa
Eric,
Most types of roofing are vapor-impermeable, or close to it -- the exceptions include cedar shingles, slate, and concrete tiles -- so outward drying of roof sheathing is usually impossible.
If a builder really wants roof sheathing to be able to dry outward, it's always possible to create ventilation channels above the roof sheathing. In your case, however, you'd end up with three layers of roof sheathing if you went that route. That's complicated and expensive.
The bottom line is that, as long as your roof sheathing is relatively dry when the roof is closed in, you should be fine, even without outward drying. I would go ahead an install the peel-and-stick membrane in the valleys and at the eaves without worrying.
Response to Martin Holladay
Thank you for your advice, Martin. Green Building Advisor has been the best for answering specific questions I've had from the basement all the way to the roof. I wouldn't be able to build my own house solo like this without you and other readers helping me out with information.
not a perfect science
I just opened up a roof, a-frame, that was built and insulated in 1977 with the cheap pink crap. The house is in summer shade and no shade winters. Climate is hot springs, Arkansas...humid summers!!!
The roof was shingles on t&g pine decking. Insulation was right up against that pine decking since 77 and is 2014. Stuff looks like it was installed yesterday. Not a bad spot anywhere, no roof vents completely unvented roof. However between the first and second floor there was no sound batts or insulation and those 2x10 cavities did have some mold in them. I just wonder why this roof is in such good shape after all these years.
Also, why not zip panels taped and then roxul batts with drywall over that. Roxul is awesome stuff I have been testing for years in crazy ways trying to see its abilities. I think that zip panels, taped properly, with roxul batts will last as long as the roof!
Response to John Vickery
John,
I'm glad to hear that your insulated roof assembly has no rot. That's good news.
Just because a roof assembly doesn't follow the rules established by the building code or recommendations of building scientists doesn't mean the roof has to fail, and your roof is proof of that.
Let's say that a certain building practice results in a 20% failure rate. That practice would be totally unacceptable to builders, who don't want callbacks or headaches. But that practice would still result in 80% of customers being satisfied.
Remember: just because your roof assembly is dry, doesn't mean it is well insulated. Your assembly could have massive air leaks that act as thermal bypasses. (Or not. It's hard to tell without a site visit.)
The last time you posted comments on your roof (on 4/8/2014, when you posted Comment #6 on the Q&A thread titled Insulating unvented cathedral ceiling), Dana Dorsett and I provided several possible explanations for why your cathedral ceiling is dry.
In my answer to your last post, I wrote:
"Every house is unique. The factors that may have saved the roof sheathing of the house you describe could include:
(a) It's not in a cold climate, so the roof sheathing never gets very cold.
(b) The roof is steep, so snow doesn't sit on the roofing for long.
(c) It's possible that the indoor relative humidity is relatively low -- you never know until you measure it.
(d) There may be enough air leakage at the "soffit" and ridge to provide air flow that acts the way a ventilation gap ordinarily would.
Of course, I'm speculating. The proof is in the pudding -- the roof sheathing isn't rotten. That's good."
Dana Dorsett provided the following comment:
"R-19 batts are very air permeable, and on long unobstructed rafter bays you have quite a stack effect. It doesn't take a huge amount of air leakage to provide some drying there. Also, if the batts are unfaced or kraft-faced, the drying toward the interior would be substantial. And a T & G plank roof deck is far more tolerant of wintertime moisture drives than OSB, not to mention that those moisture drive in Arkansas climate zone 3 aren't nearly what it is in cold climates."
The air leakage that Dana mentioned would keep your roof dry, but would undermine its thermal performance.
Hi. I am somewhat new to
Hi. I am somewhat new to wood frame construction, and am trying to understand how to properly seal and insulate a shed roof. I have a low-slope roof of 2 to 12, with a standing seam metal roof on 3" rigid insulation on a p.t. plywood deck. We have a cavity space with 9-1/4" TJI rafters, but we would like to eliminate batt insulation and the requirement of gyp. board underneath for 2" of closed-cell spray foam insulation to the underside of the deck. We were also hoping to use recessed light in the cavity if we were able to go this route. So, if anybody is still checking this, please reply. Basically, what I am asking is can you use a combination of rigid insulation on top with closed-cell spray foam underneath? Or in other words, can you use two impermeable insulation types? (Please click on the images below. One of them is a partial building section.)
Another question is, should I continue the same insulation assembly outside? The last image shows a large 10' overhang. Should I vent this exterior portion or seal the underside of the p.t. plywood deck with the closed-cell insulation?
Perfect Storm - vaulted ceilings, low-slope & recessed lighting
Hi Everyone.
I see I am a little late to the party on this thread but I hope someone can still help me. From my subject line you can see I have quite the house. I am the home owner and frustrated with my leaky roof. I live in WI and my roof has asphalt shingles.
With my house the middle section (20ft) is vaulted, a 3x12 slope and has 8 recessed lights throughout. I have had leaks in numerous locations in this section of the house, the leaks happen with the thaw and refreezing. It got the point last year where I had to shovel the entire roof after each snow fall. I did notice several areas of ice damning, so I am going to assume that is the source, getting under my asphalt shingles, i am also going to assume that their is not proper ventilation under the sheathing. The other sections of the house have the same slope, but no recessed lighting and no vaulted ceilings, no ice damning. I also have seen a few leaks when we get driving rain.
This article was very informative and seemed to give a lot of advice on cathedral ceilings. But what what my perfect storm? The house is 30 years old (80's) and im sure the ceiling is not air tight. I want to do something this summer/fall to try to fix these leaks but I am worried that whatever I do wont work and will be a waste of money, especially since I havent heard of a solid solution.
What I want to so is rebuild my fire place chimney (wood structure) and reflash, currently it is step flashed. As well as remove the ridge vent and sky light (original with house). After reading this article it seems their is more to it and that I should consider doing a above sheathing insulation/ventilation system (possibly the cool vent Hunter Panels). Would you guys recommend this solution, or would you go a different route? There is soffit vent and ridge vent already in place.
Lastly, I kow the recessed lighting is horrible, but what can I do if it is already installed? With one of the lights I changed it over to a pendant light which reduced the heat near the roof but the air barrier is still a issue. Can anyone recommend a solution addressing already in place recessed lights in a vaulted ceiling?
I have been racking my brain on this for some time now, I hope someone can give some guidance. I can include pics if needed.
Thanks, Jeff
Response to Jeff Newcomer
Jeff,
If you want to do it right, you need to address air leaks, address your recessed can problem, and add enough R-value to at least meet minimum code requirements. It's a lot of work, but it's not rocket science. Fixing these problems may be expensive, however.
The best solution is to address the situation from above, by adding a significant amount of rigid foam above your existing roof sheathing. You can build up the layers yourself, of you can buy SIPs or nailbase panels.
If you are intimidated by the details, it may be time to hire a contractor.
Above sheathing ventilation detail
"If you prefer, you can locate your ventilation channels on top of the roof sheathing rather than under the roof sheathing. You can create 1 1/2-inch-high ventilation channels above the roof sheathing with 2x4s installed on the flat, with the 2x4s located above the rafters, 16 inches or 24 inches on center. Although this approach is less fussy than installing vent baffles underneath the sheathing, it usually costs more, because most types of roofing require a second layer of plywood or OSB on top of the vent channels."
Could you please provide a detail of above sheathing ventilation using a continuous Ice&Water membrane, and metal roofing for a mixed climate? Thank you
Response to Derek Dykstra
Derek,
The GBA website does not provide custom details. That's what an architect or an engineer is for; I suggest that you hire one.
If you are a GBA member, you already know that GBA has hundreds of architectural details in its detail library for you to study and download.
Here is a link to a GBA detail for a vented insulated roof assembly with metal roofing and Ice & Water Shield:
https://www.greenbuildingadvisor.com/cad/detail/vented-roof-siding-cold-climate-metal-roofing-fiber-cement-siding-over-rigid-foam-furring
Here is a link to a GBA detail for an insulated roof assembly with vent channels above the roof sheathing and metal roofing:
https://www.greenbuildingadvisor.com/cad/detail/sip-backventing-roof-cladding
I'm guessing that neither of these details exactly fits your needs. But as I noted earlier, if you want a custom detail, you probably need to hire an architect or an engineer. Good luck.
3" Closed Cell Foam + Roxul + Rigid Foam
In the final summary it reads: "If you are using fluffy insulation, you need two air barriers: one below the insulation, and one above the insulation." I would like to use 3" of closed cell foam against the inside of the sheathing + 5.5" of Roxul and cover the whole thing with 1" rigid foam to reduce thermal bridging. Is this an acceptable strategy?
Response to Chris Heard
Chris,
Unless you tell us your climate zone, it's impossible to answer your question.
Depending on your brand of spray foam, 3 inches of closed-cell spray foam will give you about R-19.5 -- which is almost enough for Climate Zone 5, but definitely not enough for Climate Zones 6, 7, or 8.
Best Option Recommendation
I purchased a disaster of a house that was partially remodeled, it's in Zone 16 (a California designation similar to IRC zones). It has a 6/12 vaulted ceiling over the living/kitchen area. The roof is held up by two long beams that run 4 feet out parallel to the ridge , thus there is no straight air path a the way up to the peak ridge beam. The other half of the house has flat ceilings with attic space above them. The front half (vaulted) part of the house is unfinished raw, 2X6 rafters. It is separated from the back half of the house with sheetrock going up to the underside of the sheathing. So in short, the back half of the house is sealed off from the front and has plenty of insulation above the ceilings.
The roof appears to have a layer of asphalt shingles over the sheathing with a tin roof over that. The soffits are closed off. The house is way off the beaten path and it's difficult to get any contractors out there to work, let alone provide bids so I'm pretty much on my own. Can you provide some ideas of the best, worst case scenario. I realize it may not be to code, but what do you think of the following approach:
1.) try to make sure soffits are sealed off from the inside as best as possible.
2.) fill 2X6 bays with R-21 fiberglass bats.
3.) install ceiling of taped sheetrock
4.) remove tin roof and shingles eventually and install a layer of rigid foam and replace tin roof.
The house is at about 4,500 ft. We only get about 3' of snow a year and it rarely stays on the roof for more than week a couple times a year. I'm on a very tight budget, just trying to make the place livable. Any suggestions are welcome.
Response to Jen Gah
Jen,
The longer that you wait to install rigid foam above your roof sheathing after your rafter bays are filled with fluffy insulation, the greater the risk that your roof sheathing will accumulate moisture. One or two years should be no problem, but I wouldn't stretch the work out much farther than that.
The best approach is to do all the work at once: rigid foam above the roof sheathing (as recommended in the article), and fluffy insulation underneath.
Unvented attic (new construction)
I've gone through this section, looking for guidance for my particular design problem: I want to install my HRV centrally in the attic, and building code requires an unvented attic, with R-50 under the roof, so I'd like to use either 9"+ of XPS, or, preferably, EPS of a thickness of 10", or more. I will cut 1.5" wide channels, 4 or 5 inches deep, at 16" o/c, and drop these 8' wide x 4' high foam blocks over of the glue-on-top roof trusses, then screw them down with the proper long screws & washers. My stucco guy says he can immediately lay down an absolutely waterproof layer on the top surface, so no joint taping, as such, required, and also says he can do a stucco roof. I can foam in cavities around the EPS & truss members, and use the same procedure on the outside of the kneewalls above the main ICF shell, but I will have to drywall the whole attic.
Your thoughts?
Response to Edward Skakie
Edward,
I think that you need to post a sketch. I can't visualize what you are talking about from your description. If you want to install an HRV in your attic, why do you need to install a waterproof stucco roof over some type of EPS box? Isn't your attic already dry? Most attics have roofs.
If you want to create a conditioned attic, this article tells you what you need to know. For more information on the topic, see Creating a Conditioned Attic.
Two other points:
1. It's usually a bad idea to install an HRV in an attic. HRVs need to be accessible enough for the homeowners to routinely change the filter.
2. Stucco isn't roofing. There is no such thing as a stucco roof.
Unvented attic
Sorry, Martin, I now realize that "new construction" does not necessarily mean "new home to be built", and "an unvented attic, with R-50 under the roof" should have been "an unvented attic, with an R-50 roof'. Just because it's clear to me doesn't mean it's clear to everyone else.
I now understand that stucco cannot be applied to a roof, so I will revert to the a steel roof, but still want to have an unvented attic. I've read through "Creating a conditioned attic", and am still not sure as to the best way to proceed.
My question is on the roof structure.: in the attic, we will have manufactured trusses 16" o/c, covered with blocks/buns of EPS, 10" thick, 8' wide x 4' high, or x 4'W x 8'H, with channels on the bottom to allow a snug fit over the trusses; screws, with plastic washers, will be screwed through the EPS down into the trusses, & the EPS then covered with 5/8" sheathing. We will then waterproof the whole roof, then install vertical strapping under horizontal strapping to create a ventilation space, and, lastly, the steel roof on top. Sprayfoam will be applied in the attic, on the underside of the EPS, to ensure there are no leaks of any kind. The gable end ICF walls will run right up to the roof underside. Our building code requires the attic interior be drywalled, and I want to ask your opinion as which sprayfoam should be used, and if we will need to install a vapour barrier of any kind.
Thank you.
Response to Edward Skakie
Edward,
You are proposing an unusual method of insulating your roof. If I understand you correctly, you intend to install EPS between the tops of your roof trusses and your roof sheathing.
Before proceeding, you need to talk to two people: (a) an engineer, and (b) your local code official. There are important structural reasons why trussed roofs usually require a layer of OSB or plywood (roof sheathing) to be fastened directly to the top of the trusses.
EPS is somewhat squishy, and I can imagine problems from your plan.
The usual ways to use EPS foam to insulate this type of roof include:
1. Install a thick layer (or layers) of rigid foam above the roof sheathing, followed by a second layer of plywood or OSB.
2. Install SIPs, following the SIP manufacturer's instructions.
3. Install nailbase above the roof sheathing. (Nailbase panels are like SIPs, but with OSB on only one side.)
Cut and cobble
Martin: I have combed this thread and hope my question is not already answered. I am building a roof with a 6/12 pitch using a 24" parallel cord truss with an energy heel for a 24'x26' apartment over a garage. I want to use 2" of XPS foam attached to 1-3/4" furring strips down from the bottom of the 5/8" ply between the trusses creating an air channel between bottom of ply and top of foam. I was also considering spraying a thin layer of closed cell foam in all corners and in truss gaps. Then filling cavity with blown fiberglass and adding 1-1/2" rigid taped insulation at bottom of truss, then drywall. According to code apparently my rigid insulation must be placed against the bottom of the plywood so I assume my method will not meet code. I am avoid an unventilated roof but want to maximize my insulation. Should I abandon this plan, use OSB (or Solitex Mento 1000 WRB) to form the air channel and add all of the rigid insulation to the bottom of the truss with battens securing it. Is there a more vapor permeable insulation board that I could use on top (to make the air vent cavity). My goal is an R-80 roof in a zone 7 climate. My walls will be R35 (5-1/2" blown fiberglass plus 3" xps on exterior) and I will be using Alpen windows U.16 (ish). My assumption is if I use board, fluff, board method that I am creating a insulated cavity that will have no way to dry. But what if that cavity cannot get wet as the rigid insulation below will be sealed and taped?? Thanks and sorry for any redundancy.
[Editor's note: Click the box for page 4, below, to read the response to this post.]
Response to Jim Boyd
Jim,
You are proposing a vented roof assembly. For a vented roof assembly, the code does not require that any foam insulation be placed in direct contact with your roof sheathing -- on the contrary. (That requirement only applies to unvented roof assemblies.) For a vented roof assembly, the code requires an air gap under the roof sheathing, as you are proposing.
Your plan to use 2-inch-thick EPS as your ventilation baffle will work. The EPS is somewhat vapor-permeable, so it will allow a little bit of outward drying. (In any case, if you build a fairly airtight ceiling, there won't be any moisture in this assembly that needs to escape.)
If you want to choose a material that is a little bit more vapor-permeable for your ventilation baffle, you can -- for example, some people use thin plywood or fiberboard in this location -- but you really don't have to. The EPS will work
Mansard roof question
I have a mansard roof with steep sides with gables, and a nearly flat top with a rubber roof. There are no vents, it has never been insulated before I started working on it and have 2 questions:
I have insulated the sides with R-19 fiberglass and now I'm wondering: was that a mistake? It has craft paper and I was planning on a plastic sheet as well, should I skip that?
Should I treat the flat roof as a cathedral ceiling and go with spray foam (or board), fiberglass, and no moisture barrier?
Thanks, for any help, I've been getting lots of conflicting advice.
Response to Seth K
Seth,
Like most mansard roofs, your roof is unvented. Your mansard roof has different sections -- the steep sections at the perimeter, and the low-slope section in the center. All of these sections need to be insulated in a similar way, because all of these roof assemblies are unvented.
If you want to create an unvented insulated roof assembly, you have two choices: (a) You can add rigid foam to the exterior side of your roof sheathing, followed by a second layer of roof sheathing and new roofing, or (b) You can insulate the underside of your roof sheathing with spray polyurethane foam.
It is a code violation to install an air-permeable insulation like fiberglass batts between unvented rafters. It's also a bad idea, because moisture can accumulate on your roof sheathing if you try this method, and you'll end up with sheathing rot.
More information on how to insulate an unvented roof assembly is provided in the article on this page.
Mansard
I have already insulated the steep sides of my unvented mansard roof with 6" fiberglass (and I had it inspected), do you recommend I rip that out and use spray or board foam? I've gotten conflicting info on whether to treat it as a wall or a roof.
Thanks again, Seth
Response to Seth K
Seth,
My opinion is that the steep side of a mansard roof is a roof. This is especially true if the exterior of the sloped assembly is finished with roofing.
Most types of roofing are vapor-impermeable. (There are exceptions, of course, including cedar shingle roofing, slate roofing, concrete tile roofing, and clay tile roofing.) If you have vapor-impermeable roofing on the exterior side of your steep mansard roofs, you definitely can't insulate these roofs as if they were walls -- because these assemblies can't dry to the exterior.
Mansard
The sides of the roof are covered with asphalt shingled (GAF Slateline to be exact). It sounds like I should pull down the fiberglass and have it spray-foamed before I drywall. This room is a bathroom, so moisture is even more of a risk I imagine. I'm in Boston so it sounds like I need R-20, which is about 3 inches of spray foam, right?
However, 2 other areas of side-roof have already been dry walled over with fiberglass and a plastic sheet -- the bathroom closet and the hallway. I'm afraid to ask but should I open those up again? The closet is easy but the hall would be a pretty big job. Also, a bedroom currently has no insulation and my plan was to have cellulose blown into the steep part of the mansard. Is that a bad idea as well?
Thanks again
Response to Seth K
Seth,
I'm not sure if you are interested in a building science answer or a code answer.
From a code perspective, this is a roof that needs to be insulated to R-49. However, you can either (a) ignore the building code, which may not apply for the type of work you are doing, or (b) contact your local code official to find out whether your local code differs from the 2012 IRC.
From a building science perspective, R-20 of closed-cell spray foam, properly installed, would protect the sheathing from moisture damage.
I'm sorry to be the bearer of bad news, but the sections of roof that are insulated with 6 inches of fiberglass and interior polyethylene were not insulated correctly. In those sections, the roof sheathing is at risk of moisture accumulation and rot.
Mansard
Code doesn't seem to apply since it's grandfathered in. It sounds like I need to redo the hall ceiling.
As for my energy auditor recommending blowing cellulose into the mansard sides, you also recommend against that? I was under the impression blown cellulose prevents moisture migration.
Thanks again.
Response to Seth K
Seth,
You wrote, "I was under the impression blown cellulose prevents moisture migration."
You are mistaken. Cellulose is vapor-permeable. It is also air-permeable, although not quite as air-permeable as fiberglass.
Cellulose insulation can store a lot of moisture. This "moisture buffering" ability is cited by some cellulose fans as a major advantage, and indeed this ability can sometimes prevent a small moisture problem from causing a lot of rot. However, the ability of cellulose to store moisture is also evidence that cellulose is not capable of (as you put it) "preventing moisture migration."
Closed Cell + Fiberglass + EPS?
Great article!!!
Does it make sense to spray and cut and cobble 4 inch closed cell foam/board on underside of sheathing followed by fiberglass inside the bays and 1 inch of eps/iso under the rafter (to stop thermal bridging) before finishing with drywall? Will I create a vapor sandwich and better leave the final EPS and accept the thermal bridging?
I already sprayed and cut cobbled 4 inch of closed cell. I will redo the roof next year, but I guess now it is too late to think about eps/iso on top of roof since i already unvented the attic.
I am in Zone 5 in a 100 year old house.
It's a bit risky doing it with foam board.
As the house flexes with changes of temperature it's possible, even likely that some of the foamed-in air sealing will leak. It might be worth doing 2" of open cell foam on the interior side of which would be a more flexible and reliable long term air seal.
It's fine to add foam board above the roof deck even with the closed cell foam-board (what type?) on the interior. Roof decks can't dry to the exterior through 0.1 per shingles anyway, particularly since in zone 5 it will spend a significant amount of time covered in snow/dew/rain with the moisture drive heading inward, not outward. If the moisture content of the roof deck is low when re-roofing (measure it- under 20% is good, under 15% even better), put a self sealing peel'n'stick membrane (eg Grace Ice & Water Shield) over the roof deck, and put the rigid foam above that.
An inch of EPS on the interior isn't much of a thermal break, but better than nothing. Better yet would be to cut some rafter-edge strips of 1-1.5" rigid polyisocyanurate. 1.5" polyiso on the edge strips with a complete fiberglass fill does more for the whole-assembly R than a full layer of 2" EPS.
The R value of your cut'n'cobbled foam + exterior foam has to be at least 40% of the center-cavity R value for dew point control at the foam/fiber boundary in zone 5. If it's coming up a bit shy of that before adding the exterior foam it's not a big deal in the short term, but if it's going to be 5-10 years before re-roofing to raise the foam-R to above 40% of the total it's worth using vapor barrier latex primer on the gypsum board, or a smart vapor retarder between the gypsum board & fiberglass.
Retrofit
First, thanks Martin for the wealth of knowledge this website has. I've been visiting it regularly for the last few years, ever since purchasing my first home.
I am also located in northern VT, zone 6 but I think we may be pushing 7 due to localized conditions. I've recently had an energy audit performed and wanted to verify one of the recommendations. We have an area with a cathedral ceiling, and also a shed dormer built into the cathedral. The cathedral ceiling is insulated with r38, and the shed dormer with r19. Both are kraft faced fiberglass. The roof is 12/12 on the cathedral, not sure but less on the dormer, and has snow coverage (often over 8") from the beginning of January until mid March. There are soffit and ridge vents.
I was told that hanging polyiso sheets under the rafters and sealing the seams with caulk or tape would be the most efficient way of reducing air leaks and adding insulation. This seems to be contrary to most of the advice , which reverses this assembly. Will this assembly cause any issues with dew points / condensation? I am looking for a cost effective improvement, but want to make sure I'm not causing problems along the way.
Last detail, it is a newer construction (2007) but the rafters are still exposed, so I have access.
Thanks for your time,
Response to John Poulin
John,
You wrote, "the rafters are still exposed," but I'm not sure what you mean by that. Do you have kraft-faced batts between the rafters, with the kraft facing still visible? Or do you have decorative rafters with nice T&G boards above the rafters, and then a second insulated roof assembly above the T&G boards?
We really don't know if these roofs have proper vent channels, or what type of vent baffles (if any) were used to maintain the ventilation gap between the top of the fiberglass insulation and the underside of the roof sheathing.
If this were my house, and if the fiberglass batts are visible, I would pull all of the insulation out of a few rafter bays to see what's up there.
Once we know what you have for an existing assembly, it will be easier to give advice.
urgently need advice re: cathedral ceiling insulation
I have an urgent problem and would be very grateful for advice on insulating our house’s family room cathedral ceiling, built in the 1970’s and currently being re-roofed. (The old roof has been torn off, and they are about to start installing the new shingles.) The house is in San Jose, CA, climate zone 3. The contractor does not want to put insulation above the sheathing, which is 2x8 pine tongue and groove, which up til now served as the finish ceiling. The new roof over the cathedral ceiling will consist simply of the pine T&G, then felt, then asphalt shingles. This is almost the same as the previous roof, except that the previous roof included ½” of sound insulation board, which provided almost no thermal insulation.
Below the 2x8 pine T&G, there is 9" of beam exposed, but we only have 4” or at the very maximum 5” to play with, because at the top of the stairs which ascend the side of the room, the ceiling is barely above a tall person’s head as it is. In addition, we want to maintain an exposed beam profile for the aesthetics. I hope the attached photos illustrate the situation.
I believe an unvented roof assembly is the only possibility here, as the highest point of the cathedral ceiling is not the ridge of the roof.
I am envisioning some combination of XPS board, Roxul Comfortbatt, and/or Roxul Comfortboard IS underneath and directly adjoining the pine T&G. We intend the new finish ceiling to be a new layer of T&G, either pine or cedar, 1x6 or 1x8.
I would like the insulation stackup to include at least 1” of some Roxul product because I am concerned about sound insulation - as noted above the previous roof included 1/2" of sound insulation board.
We want to add track lighting to the new ceiling, with its electrical supply running through the new cavity created for the insulation. The existing fan also needs its electrical supply to run through that space.
A new standalone direct vent gas stove is going in at the far end of the room under the metal box. I figure if we use XPS board, it would have to be pulled back several inches from around that area, but I didn't think it would prevent me from using XPS entirely. Seems like Roxul is less of an issue in terms of heat/fire.
I don’t think I can meet all of the guidelines that I’ve read on this website, given existing construction constraints and reluctance of my contractor to implement insulation above the sheathing and foam for the new cavity. Given these limitations, what would be the least incorrect way to implement this? What about an unvented assembly consisting of:
Shingles
Felt
Pine T&G
XPS board
Roxul board or batts
Gypsum drywall
New 1x T&G
Can I get away without some of those layers given my climate zone? For example, can I use all Roxul, without XPS? Do I absolutely need the drywall?
Thanks very much for any advice.
Response to Debra R
Debra,
Don't make any hasty decisions that you will regret. If necessary, tell your roofer to stop all work on this project until this issue is resolved (assuming, of course, that your roof sheathing is protected by asphalt felt or a similar underlayment.)
The right way to proceed is to install rigid foam above the roof sheathing. There really aren't two answers to this question. The time to do the work is now. If your contractor won't perform the necessary work, you'll need to hire a different contractor.
For more information, see How to Install Rigid Foam On Top of Roof Sheathing.
Is your contractor doing it for free?
If not, he doesn't get to refuse to put foam above the sheathing, which would be better and cheaper than fitting it between the beams.
thanks, we will reconsider
Thank you, Martin and Stephen. Fortunately we are in a situation where we can pause and reconsider, as the new felt has been placed, but they haven't started installing shingles yet. I will discuss the situation with the contractor again. I may be able to get him to reconsider.
A few follow-ups:
I see the recommendation is that when starting with board sheathing, one should place a watertight membrane over the sheathing before installing the lowest layer of foam. However, in my case the roofer has already completed placing new felt over the T&G board ceiling/roof deck. Can that felt substitute for the prescribed watertight membrane, here in San Jose/Climate Zone 3? Is a watertight lower membrane something that is more important in colder climates? Alternatively, if I have them pull off the already installed felt, and put down a membrane instead, will the felt be ruined, or will they be able to reuse it on top of the final topmost layer of plywood, just below the shingles? I'm guessing it will be ruined and we'd have to throw it out and start over.
If we're going to put some insulation above the ceiling, then I want to put ALL the insulation above the ceiling, and avoid the cost and hassle of a new lowered ceiling. That means a build-up of 8", using XPS. If we build up the roof line above the cathedral ceiling of the family room by 8", we presumably need to build up the rest of the adjoining gable roof as well. However, the rest of that gable roof, other than the part over the family room, goes over the second story bedrooms, which have a conventional 8' drywall ceiling and a vented attic with blown-in cellulose to R-30. Is there any problem mixing these two roof systems, i.e. putting 8" of foam over the roof of the already insulated vented attic?
I'm not sure what to do about the electrical for the existing fan, and for the not-yet-installed but much desired track lighting. In the old roof, the fan's electrical supply ran on top of the T&G ceiling, and was covered by what looked like electrical tape, then by a 1/2" layer of sound insulation board, and then by the felt and shingles. We had disconnected that electrical supply in preparation for running it through the new interior cavity, but if we no longer need an interior cavity for insulation, it will have to go back on top of the ceiling somehow.
Thanks again. Appreciate your valuable input.
Response to Debra R.
Debra,
Directly above the ceiling boards, you need an air barrier. This is necessary in all climates.
The existing asphalt felt can stay, even though it is not an air barrier, if you put a new airtight membrane (or new sheathing, like OSB, with taped seams) above it. Or it can be removed, to facilitate the installation of an airtight membrane. There is no way to make asphalt felt airtight. Once it is removed, it can't be re-used.
Your plan to install 8 inches of rigid foam is a good one, but you may be able to install thinner foam if there is a compelling reason to do so. Of course, 8 inches of rigid foam has a higher R-value, and will perform better, than a thinner layer. Check with your local building department to find out whether you have to comply with minimum code requirements for insulation thickness on this type of job.
If you decide not to extend the rigid foam over the parts of your roof that have a conventional vented attic, your builder (or an architect) can come up with a trim detail that you may be able to live with. However, if the aesthetics of this change in roof plane bother you, you can continue the rigid foam over the entire roof. That way, you will end up with a conditioned attic. If you do that, you will probably want to seal the soffit vents for that attic.
You should consult an electrician about the best way to serve your ceiling electrical boxes. There are several possible solutions -- some visible from the interior, and some hidden by the new foam.
attic questions
Martin, re: changing the attic over the second story bedrooms to a conditioned attic and sealing the soffit vents.... Prior to this latest idea about insulating with rigid foam on top of the cathedral ceiling, we had been planning to cut a ridge vent into the gable ridge, in order to meet ventilation code requirements. Currently we have eave vents plus two fairly useless gable vents, one on each side. We had been planning to block off the gable vents and install 15' of ridge vent instead at the center of the ridge instead. Are you saying that increasing ventilation to that second story attic would actually be a bad idea, if we continue the foam over the entire second story gable roof, and instead we should make it completely unvented?
Perhaps the way to go is to settle for 4" of foam over the cathedral ceiling, rather than 8" of foam, and NOT continue the foam over the vented attic. There will be a weird jog in the roof line where the foam starts, but it will mostly only be visible from the back of the house, not from the street. Yes, 4" won't get us to R-38, but compared to the basically zero insulation we've been living with for the last 20 years, the R-20 we would achieve would be heavenly.
Thanks again.
Response to Debra R
Debra,
Q. "Are you saying that increasing ventilation to that second story attic would actually be a bad idea, if we continue the foam over the entire second story gable roof, and instead we should make it completely unvented?"
A. To take advantage of the insulating value of the rigid foam over the attic, you definitely want to seal up any attic vents, and you certainly don't want to create a ridge vent.
Of course, if you don't care about the cost (and usefulness) of the new rigid foam, nothing would stop you from keeping a vented attic. But that seems a shame. The foam is expensive and useful -- so why not take advantage of its insulating value? (Obviously, inviting outdoor air to ventilate the space under the insulation makes the insulation basically worthless.)
For more information on this issue, see Creating a Conditioned Attic.
attic, etc.
Martin, thanks. I just talked to the roofer and he rejected the idea of only putting the foam over the family room cathedral ceiling. That weird "jog" in the roofline, having it suddenly bump up 4" or 8" where the family room starts, in the middle of the back side of the roof, would defeat the idea of a continuous slope for rain to come down when it hits the upper part of that back roof. So the 4" or 8" height addition needs to continue across the entire second story roof line.
So now I'm thinking either (a) 4" of foam added across the entire second story roof, or (b) 4" of foam over the family room cathedral ceiling, and 4" of non-foam height (some other cheaper material, or just build up the framing by 4"?) over the bedrooms' vented attic, and keep the existing attic ventilation/add the ridge vent. I have a feeling the (b) option is not a good one as far as the roof/shingle integrity, though...??
If it seems like I'm out of my depth here... yeah, you bet, I am. I'm just a homeowner, with only a few days of internet research under my belt. But the contractor is not familiar with this roofing technique, so we're having to figure it out together. Appreciate your help immensely.
Response to Debra R
Debra,
Either (a) or (b) is possible.
You could add 2x4s (which are 3.5 inches high), installed 16" or 24" o.c., and 1/2" plywood or OSB, over the attic. That would provide you with your 4 inches.
roof assembly stack-up
Thanks again. The roofer agrees that 2x4 framing to raise the height over the vented attic would be a workable solution to match up the roof lines.
For the roof assembly over the cathedral ceiling, does the stack-up below capture all the elements I would need?
2x8 pine T&G (already in place, remains as the finish ceiling)
asphalt felt (already applied)
airtight membrane (is this the same as an ice & water guard?)
2 layers of XPS foam, each layer 2" thick, seams staggered between layers, and taped within each layer
plywood
asphalt felt
asphalt shingles
BTW, for the foam type, I am leaning toward XPS because 1) I have the impression that ISO is somewhat fragile, such as if it gets at all wet, and 2) the possibility of long term outgassing with ISO. Hopefully any such outgassing would go upwards and outwards rather than downwards into the house interior, but the chance that it would outgas into the interior really worries me. If I'm missing some reason why XPS is a bad idea, please let me know. I know XPS is unfortunately less green of a material than the other rigid foams, but that is a secondary concern at this point.
Thank you for the generosity of your time and advice!
Response to Debra R
Debra,
You can use Ice & Water Shield as an air barrier if you want. But if you choose to use that product, you'll have to remove the asphalt felt so that the Ice & Water Shield can be adhered to the roof boards.
Other options: a synthetic roofing underlayment that is also advertised as meeting air barrier requirements. Options include Solitex Mento 1000, Delta-Vent-S, or Titanium UDL 30.
Polyiso is used all the time for this type of roof assembly. Polyiso does not outgas. It is more environmentally friendly than XPS -- and it has a higher R-value per inch.
air barrier, vapor barrier, etc.
Martin, thanks to your excellent and timely advice, we are now headed toward a solution of rigid foam over the exterior of the ceiling. Thank you for pointing me in this new and improved direction. We are still working out some details, such as...
Re: the air barrier to be placed above the pine T&G ceiling and below the foam, would you recommend that we use something which is both an air barrier and a vapor barrier? Or is it important to make sure that the product we select is NOT a vapor barrier, so that any moisture that gets into the roof assembly can dry to the inside? As a case in point, the Grace Ice & Water Shield is both an air barrier and a vapor barrier (0.08 perm/Class I), so I'm wondering if that would be a bad product to use. Of the other underlayments that you mentioned, I see that the Titanium is also a vapor barrier, but the Solitex and Delta products are vapor permeable. Does that make Solitex or Delta the way to go?
Another dilemma I'm having re: Ice & Water Shield is that I was looking forward to removing the newly placed asphalt felt that is currently over the pine T&G and replacing it with a different material, because the asphalt smell of the felt is coming through the T&G ceiling and bothering me (just in case I needed any evidence that that ceiling is horribly air permeable...). But then I read in the Grace Ice & Water Shield installation instructions that "Due to its slight asphaltic odor, do not apply Grace... Ice & Water Shield... where the membrane is exposed to interior living areas." So if I replace the felt with Ice & Water Shield or a similar asphalt-based product, I'd probably just be jumping from the fire into the frying pan, odorwise. This is leading me to think that the Solitex or Delta products would be better. I haven't priced these but I understand they will be expensive. I guess my other alternative for an air barrier that is not asphalt-based would be a layer of plywood with seams taped, but that would not only be expensive, but also add extra weight to the roof. Am I on the right track with evaluating the options, and would you recommend one direction over the others? I guess fundamentally before I can settle on an air barrier solution, I need to understand whether it should be a vapor barrier or not. I'm guessing it should not but would really appreciate your input.
Thanks very much again.
Response to Debra R
Debra,
Q. "The air barrier is to be placed above the pine T&G ceiling and below the foam. Would you recommend that we use something which is both an air barrier and a vapor barrier? Or is it important to make sure that the product we select is NOT a vapor barrier, so that any moisture that gets into the roof assembly can dry to the inside?"
A. The air barrier can be a vapor barrier, because the rigid foam is also likely to be a vapor barrier (or close to it) in any case.
Q. "If I replace the felt with Ice & Water Shield or a similar asphalt-based product, I'd probably just be jumping from the fire into the frying pan, odorwise. This is leading me to think that the Solitex or Delta products would be better."
A. I agree. In light of the odor issue, I don't think that my suggestion to use Ice & Water Shield was a good one -- so I withdraw it. Either plywood with taped seams, OSB with taped seams, or one of the European membranes (or one of the U.S.-made synthetic roofing underlayments -- especially those advertised as air barriers) would be a better choice.
I don't think that the weight of plywood or OSB is going to be an issue, but if you are worried about the additional weight, you can always consult an engineer.
are R-values from separate compartments of insulation additive?
Martin, thanks again. Another question: we currently have blown-in cellulose to level R-38 on the floor of the attic above the second story bedrooms. (Going from memory I had said R-30 earlier, but I checked and it was actually specified at R-38). The cellulose, of course, does not reach the top of the attic, so there is a substantial air gap between the cellulose and the roof sheathing. If we put R-20 of rigid foam above the roof sheathing and close off all the vents to that second story attic, does that give the interior space R-20 + R-38 = R-58 insulation level? Or is insulation not additive when it is in two non-contiguous compartments, so we'd actually be downgrading from R-38 to R-20 by doing that?
Thank you.
Response to Debra R
Debra,
If you do as you propose, you would gain an addition benefit from the R-20 insulation above the roof sheathing. That said, the approach you describe wouldn't meet code requirements for new construction, because ideally any insulation used to supplement the rigid foam above the roof sheathing needs to be in direct contact with the underside of the roof sheathing.
This is a complicated topic, and if you are worried about code requirements in your town, then by all means you should ask this question at your local building office. In most cases, renovation work can be performed without bringing all aspects of your house up to current code requirements.
In general, though, there is no harm, and there will be a thermal performance benefit, from proceeding as you describe.
Response to Debra R
The reason to put the additional insulation in contact with the underside of the roof is that it's hard to verify that you have successfully closed off all vents to the attic. But if you really do succeed in doing that, there should be no problem. With a blower door is possible, though tricky.
Cathedral roof vent
Have room over garage center with closets on both sides between the closet kneewalls and the eaves. Insulation over the room section is 6 inches of foam slabs sealed by "Great Stuff" spray-in foam. Above this ceiling foam and under the roof plywood, there are 1 inch x 20. inch unobstructed foam encased ducts between the rafters for venting to the roof peak vent. The side sections outside the knee walls are insulated with rolled fiberglass fiber with durovent ducts between the insulation and the roof plywood. There are substantial soffit vents at the base of the durovent ducts. After a new roof was installed, the fiberglass started to absorb substantial moisture and mold appeared on the plywood as shown in the picture. This only happened on the north side of the garage, none on the south side. Since the plywood must now be removed, I am thinking of increasing the duct heights by raising the roof to give 2 " ducts rather than the 1". Also I would add a mid-roof SmartVent to increase airflow. In addition I would increase the peak vent from Coravent 300 to CoraVent 600 to double the outlet area. Does this look like a reasonable fix?
Sorry for beating a dead horse
http://buildingscience.com/documents/insights/bsi-081-zeroing-in
This roof assembly looks pretty cathedral but if i understand correctly its not vented at all, but has generous above sheathing foam. Is this considered a vapour safe assembly considering this article says
"Install rigid foam insulation above the roof sheathing and air-permeable insulation between the rafters. If you choose this method, it's possible to install vent channels between the top of the rigid foam and the top layer of roof sheathing by installing a series of parallel 2x4s — one above each rafter — extending from soffit to ridge."
Response to George Baum (Comment #180)
George,
It looks like you posted your questions on two different pages. I have provided an answer on the other page where you posted. Here is the link to my answer:
https://www.greenbuildingadvisor.com/community/forum/gba-pro-help/57976/need-correct-moisturemold-problem-cathedral-roof#comment-150916
Response to Alan B (Comment #181)
Alan,
You provided a link, but you never explained which illustration you were referring to in the article you linked to. I'm guessing that you were talking about the illustration that I have reproduced below.
Yes, it is safe (although before you ask a question about a particular roof assembly, it would be good to know your climate zone).
You seem uncertain. For example, you wrote, "it's not vented at all." But in my article -- the article on this page, where you posted your comment -- I wrote, "there are three ways to build an unvented roof assembly." I then proceeded to explain how to build this type of roof.
I said that it is possible to install vent channels between the top of the rigid foam and the top layer of roof sheathing. I never said that it was necessary. Unvented roof assemblies are safe. The main reason that some people install ventilation channels above the rigid foam is because they live in areas with lots of snowfall, and they prefer a "cold roof" to minimize ice damming problems.
Thanks for your comment. I will edit my article to try to clarify any ambiguity on this issue.
.
roof assembly stack-up, again
Martin, following up on our earlier discussion:
We've decided to insulate on the exterior of the roof sheathing all the way across both sides of the gable roof, in order to match up the roof lines. We will eat the cost of the foam in the areas where there will be a vented attic underneath the foam -- basically the foam will simply be an expensive spacer on that part of the roof.
How does this look for a plan? Anything you would change/add/reorder? Do you agree with taping the seams in both layers of plywood?
Existing roof deck (2x8 T&G boards in back of house/cathedral ceiling, 2 x 4's in front of house over attic)
1/2" CDX plywood, seams taped -- air barrier (the felt which is currently in place will be removed)
2 layers of rigid foam, each 2" thick, staggered horizontally and vertically, seams taped
1/2" CDX plywood, seams taped
30# asphalt felt
asphalt shingles
Thanks much.
Response to Debra R
Debra,
It sounds like an excellent plan. Depending on what type of rigid foam you select, you will end up with insulation in the range of R-16 to R-24. While that's less than code requirements, it's much, much better than what you have now.
You could skip the tape on the top layer of plywood to same some time and money. That's probably what I would do if I were you. That said, there is no harm in taping the seams of the top layer of plywood.
Response to Ryan Nelson
Ryan,
The best insulated sloped roof, in my opinion, is described in these two articles:
How to Install Rigid Foam On Top of Roof Sheathing
Combining Exterior Rigid Foam With Fluffy Insulation.
In your climate zone (Zone 4C), here's what that roof would look like, from the top down:
1. Roofing.
2. Roofing underlayment.
3. Roof sheathing.
4. If desired, a 1.5-inch-deep ventilation channel created by flatways 2x4s.
5. R-10 of rigid foam (2.5 or 3 inches of EPS).
6. An air barrier.
7. Roof sheathing.
8. R-39 or R-40 of fibrous insulation (cellulose or mineral wool) under and in direct contact with the roof sheathing.
I've heard too many reports of homeowners with problematic SIP roofs installed in the 1980s -- some of these roofs are now rotting at the seams due to condensation of moisture from exfiltrating interior air -- to feel comfortable recommending a SIP roof.
New build on '47 foundation
Martin,
I just joined GBA, and I'm looking for some wisdom.
I'm in zone 4 (Portland, OR), and want to rebuild the house on an existing foundation. The foundation is sound, but what's above it is horrible.
Having visited Premier SIPs up in WA state, I'm 90% sure SIPs are a great way to go. More importantly, I've convinced my wife (the finance manager for this project) as well! That is, for the walls at least...
I would like a cathedral ceiling for this build, and the roofline will be moderately "tortured", as you say. After reading your blog and some of the comments, i think a non-vented, insulated ceiling is best. I'm down to, 1. SIPs all the way, or 2. stick framed with rigid foam inside, as well as outside roof sheathing.
By the time i add several layers of rigid foam, and two layers of sheathing, i think i will be wishing i went SIPs... my question to you is, if you could start from scratch on a new roof in zone 4, would you recommend my options 1 or 2, or something different altogether? And also, do you have any quantitative or even anecdotal cost comparisons between my options 1 and 2?
Martin, I'm grateful for your time, and after reading many of your replies, i can see you are passionate about building things right. Right for people, and the planet. Thank you for what you do!!
Ryan Nelson
New build on '47 foundation
Martin,
Thank you for your reply. Those articles are both very informative. I'm getting the sense that SIPs can be done well, but can be beat in price with exterior rigid foam systems as you've recommended, with equal or better performance (with emphasis on air-tightness). I'm happy to rethink my stance as I'm still in the planning stages.
For the air gap in layer 6, is 1.5" a good thickness? Flatways 2x4 parallel and aligned to the rafters for that as well? Sounds like I should expect to be using 10" screws for the full assembly, is that about right?
Should i fully support sheathing seams parallel to the ridge line, for sheathing above an air gap? Wouldn't that isolate the air under each sheet of sheathing, and is that okay?
Thanks again,
Ryan
I mis-read you,
I misread you, i see layer 6 is an air barrier, not an air gap! My mistake!
Response to Dylan Kinsey
Dylan,
There are a couple of potential problems with your approach. The first problem is that plywood roof sheathing isn't very vapor-permeable; when dry, plywood has a vapor permeance of 0.5 to 0.7 perm, so it meets the old definition for a vapor retarder.
Its saving grace (in your application) is that it has variable vapor permeance; as it gets wet, plywood becomes more permeable.
The second problem is that not all building inspectors will accept the "above-the-roof-sheathing vent channel" approach, and may deem that your proposed roof assembly is non-compliant.
The best way to proceed would be to choose a more vapor-permeable sheathing material -- something like fiberboard.
If you go ahead with your plan, you should include a smart vapor retarder on the interior side of the assembly, to minimize the transport of moisture from the interior to the sheathing.
Venting over roof sheathing
Hi Martin,
I'm trying to decide on a roof venting strategy for my next project; a story and half cape with 12" double 2x4 walls with dense pack cellulose for R-40, and 2x10 rafters built down from inside like a Larsen Truss to 18" depth to achieve R-60, also dense packed cellulose. On the interior, I'd like to use Intello for vertical walls and taped cdx on sloped ceilings.
I'd like to use the exterior wall and roof sheathing as my primary air barrier; cdx plywood with all seams taped, which sort of forces me to keep the roof venting on top of the roof sheathing, as you describe in paragraph 7 of this article. I'd like to use Solitex Mento as a permeable roofing underlayment, as well as a WRB on vertical walls, and 2 layers of cross hatched 1x4 strapping over roof ply and Mento; one running down the roof slope, nailed to the rafters, and the second run horizontally over them to support corrugated steel roofing. (rake and eave overhangs are "applied" after Mento is installed, so as not to interrupt the air barrier).
Does this strategy sound as effective as vent channels constructed on the inside of the roof sheathing? I'm struggling to see why this wouldn't work as well or in practically the same manner as an in-board site-built vent channel. It's essentially like a rain screen or vented cavity, same as on the walls. Any thoughts on this?
Thanks!
Martin,
I see your point. I
Martin,
I see your point. I haven't worked with fiberboard. Can it be taped and considered a reliable primary air barrier?
Not much worry about building inspectors here in South Albany, VT, but I'll keep my eyes open. : )
If I changed my venting detail to a site built style, between the rafters, as in your many blogs on this topic, my air barrier would need to transition back inside before it got to the sloped roof; very cumbersome at the gable walls. Not really sure how I'd do that.
Also, wouldn't the site-built plywood baffles between the rafters have the same issue; slow drying via diffusion? ( I suppose I could use fiberboard for baffles)
What got me started on the "air tight walls and roof sheathing" was your article of the same name; specifically South Mountain Company's great article on the Martha's Vineyard housing development. I saw Marc's presentation on those houses at BBD as well.
The wall and roof section of those houses indicates that they're unvented assemblies. (Still unclear to me how that is safe). I thought if I did basically the same thing, but added over-sheathing vent strips for steel roofing, I'd be golden, but I think I'm missing something here.
Response to Dylan Kinsey
Dylan,
Most people building vented cathedral ceilings use the interior drywall as their ceiling air barrier. The standard way to make the transition between the exterior wall air barrier and the interior ceiling air barrier is to install a wide piece of plywood on top of the wall's top plate. If the top plate is 5.5 inches wide, the plywood is 7 or more inches wide. That gives you an interior lip -- you can seal the seam between the plywood and the drywall on the interior, and you can use tape on the exterior to seal the seam between the wall sheathing and the plywood that is installed above the top plate of the wall.
The South Mountain Company built unvented cathedral ceilings packed with cellulose -- probably a code violation, and a method that the South Mountain Company no longer uses.
Concerning questions around whether ventilation baffles need to be vapor-permeable: those questions are addressed in my article, Site-Built Ventilation Baffles for Roofs.
Response to Martin
Martin,
I'm familiar with that approach and have used it on previous double walls with flat ceiling/ truss roof assemblies. Worked beautifully.
Thinking it through on my Cape, I might prefer to go back to the method you describe; make the air barrier jump back inside at the wall top plate, vent the sloped ceilings with a site-built vent channel between the rafters, and go back to a flat ceiling on the second floor, using gable wall vents to vent an unconditioned attic. The only stumbling block I see is transitioning the gable wall exterior air barrier to the interior flat ceiling air barrier; one of the reasons I was seduced by the simplicity of the "air-tight wall and roof sheathing" approach. Looks so tidy and straight forward, but thinking now that it's too difficult to incorporate a robust proven venting strategy for that assembly and the poor drying-potential risk factor is too high.
Your blogs on this topic have been extremely helpful and I appreciate your advice. ( I do study before I submit questions : )
Thanks!
wood cathedral ceiling?
Hi Martin,
Before reading all this great info I replaced some beams and completely re-boarded the roof deck with unfinished 3/4" beaded pine to be the ceiling.
Project is:
1 room on 2nd floor of 1-3/4 sty ell
200 yr old timber frame
400 total roof area 5:12 pitch
zone 5 in MA
Was planning to do the following:
1. cover boards with IKO synthetic underlayment ("roof guard cool grey")
2. 4-1/2" polyiso
3. 4-1/2 EPS
going to lay down 2x4's 16 o.c mid way in foam. to increase fastening spots for top plywood (have horiz. purlins 30" apart)
4. 1/2" plywood (unvented top deck)
5. either ice and water full coverage or more IKO synthetic underlayment
6. IKO architectural shingles
Having tight, staggered, taped, panels
and at least at the ridge, where joints are close together, to can foam with low expansion flex foam
Questions I have are
1.Can this work to have an unfinished wood ceiling?
2.Having trouble finding 2" 4x8 EPS foam. Home Depot and Lowes have 1" thk or 2" 2x8.
Do you know of a retail seller in east MA or south NH
3. Are the 3/4 boards and synthetic underlayment a sufficient thermal barrier?
4. Would there be a benefit to foam and tap all joints.
Any suggestions will be greatly appreciated
Thanks
Chuck
Reclaimed foam
Chuck- Google "reclaimed foam." There are a number of sellers of reclaimed foam in MA. You'll save a bundle and help the planet to boot.
Reclaimed foam and exposed pine board ceiling
Chuck,
I'm doing the same detail on my new construction. I bought the insulation from David Volpe @ NationwideFoam.com. There is a location in Framingham, MA. I bought several tractor trailer loads to insulate my house and barn for a very, very reasonable price. Reclaimed insulation can be hard to source (most suppliers don't/won't store it for long because it isn't as valuable as Iso), so they will usually source it from an active job site.
It may be hard to find insulation that is the exact measurement you want, so it can be helpful to source the insulation, and then design around that. That is what I did, and it's working out great.
There is also a source in Barre, VT for Iso.
I would recommend a cold roof on top of the insulation.
If you need long screws look to Tru-fast screws from Cor-ten.com When it comes to the screws, make sure to use a slight upwards slope of about 5 degrees to create a truss out of the screw.
If you don't have any luck sourcing it let me know and I'll help you out.
Response to Chuck Collins (Comment #195)
Chuck,
Q. "Can this work to have an unfinished wood ceiling?"
A. Yes, you can have a board ceiling on the underside (interior side) of this roof assembly, as long as you have a good air barrier (either synthetic roofing underlayment with taped seams, or rigid foam with taped seams) directly above the board layer.
Q. "Are the 3/4-inch boards and synthetic underlayment a sufficient thermal barrier?"
A. Whether of not 3/4-inch boards are acceptable as a thermal barrier or ignition barrier depends entirely on your local building inspector, since code interpretation on this point varies widely from jurisdiction to jurisdiction. Call up your local building department for more information on this issue. You might also want to read this article: Thermal Barriers and Ignition Barriers for Spray Foam. (Although the article talks about spray foam, rigid foam is treated similarly by building codes.)
Q. "Would there be a benefit to foam and tape all joints?"
A. Yes, because taping the joints of the rigid foam reduces air leakage. For more information, see How to Install Rigid Foam On Top of Roof Sheathing.
Response to Peter Anderson
Peter,
Q. "Can I use rigid insulation below interior plaster finish to increase R-values?"
A. Yes.
Q. "I was concerned with duplicating vapor retarder. No problem sandwiching existing plaster?"
A. No -- no problem.
Q. "Is adding as little as an inch of extruded or polyiso worth it?"
A. Only you can answer that question. In my mind, it's worth it. Two inches is even better, of course.
Adding insulation
Zone 4a. Have cape with 2x6 rafters, filled with r13 3.5 inch insulation with baffles above. Insulation has vapor retarder facing. Can I use rigid insulation below interior plaster finish to increase R-values?
Martin, yes I would sheet rock below rigid insulation. I was more concerned with duplicating vapor retarder. No problem sandwiching existing plaster? Obviously am never getting to code minimums, but is adding as little as an inch of extruded or polyiso worth it?
Re: Replies 196,197,198 Stephen,Brad,Martin
Thank you guys for your input / answers.
Did find the reclaimed foam suppliers in the Worcester and Framingham areas.
Nationwide, who you bought from Brad, only sells tractor trailer loads.
Green Insulation Group has some 3-1/4", not ideal but may have to work with it as you suggest.
As a DIYer this site has been a great help thanks again
Chuck
If simply blocked the soffit/ridge vents, would I be better off?
New to the site and really like it. I have such a 1975 house (Austin, TX) with cathedral ceiling with under size batts albeit rockwool. When we had a Galvalume roof, we got R-9 polyiso on top of the roof deck, underneath the Galalume. Now we have "Remember: if you choose to install rigid foam on top of your roof sheathing, don't install ventilation channels under the roof sheathing; these two practices are incompatible." If blocked the soffit vents and the ridge vent in an airtight manner, our R value sounds like it improves right away because then we aren't "wasting" the R-9 on top of the deck. Right?
Response to Brian Lengel
Brian,
Yes, you guessed right. If you have rigid foam on the exterior side of your roof sheathing, you don't want to have any ventilation air on the interior side of the roof sheathing. So you need to seal the vent openings near the soffits and at the ridge.
Hi Martin, wanted to revive this thread/article for this specific point. Would keeping the ventilation channel be reasonable failure proof though? The benefit of the polyiso on top would allow for some mitigation of thermal bridging through the rafters, but not so much for R-value no?
Guillow,
No, you don't want a ventilation channel if you have polyiso on top of your roof sheathing. All the ventilation channel will do is rob your roof assembly of heat during the winter and add to your cooling load during the summer. You want to seal the soffit vents in an airtight manner, and seal the ridge vent in an airtight manner, to prevent outdoor air from getting in your insulated assembly.
Remember, in summer outside air is humid--and inviting outside air into an insulated assembly, where the outdoor air might encounter cold surfaces, could increase the chance of hidden condensation.
Thanks Martin! Sorry to clarify, in zone 6. So having 2inches of polyiso really doesn't do much except slow down some thermal bridging no? Wouldn't it be similar in R-value and temperature effect on the sheathing as nothing?
I'm trying to minimize internal space intrusion (otherwise would put polyiso inside), and cost (hence only 2in vs 8-10inches in zone 6) on a 100 year old retrofit. So was thinking of the typical vented assembly with a bit of a thermal bridge boost with 2in of polyiso on the exterior. Would that work?
Guillow,
On a vented roof, if you want to slow down thermal bridging through the rafters, the continuous layer of polyiso belongs on the interior side of the rafters, not the exterior.
The problem with your theory -- that exterior polyiso on a vented roof slows down thermal bridging through the rafters -- is that exterior air is contacting those rafters, because exterior air is flowing through the vent channel. The polyiso might have some very slight effect, but basically your plan is a waste of polyiso.
Thanks Martin! Is there any concern of putting the polyiso on the interior side regarding vapour permeability? Would one still put Intello plus on top of the polyiso? or direct to drywall? (Zone 6...)
Old capes?
"Insulated cathedral ceilings are a relatively recent phenomenon. The craze for insulated cathedral ceilings (and great rooms) really took off in the 1970s and 1980s"
This question may show my ignorance concerning... well anything really... but, are not 'Cape' style houses (1 1/2 story) fairly old and traditional (in New England), and did not these include insulated 'cathedral ceilings'?
As a follow-up; If one were building a story and a half, is there any advantage/disadvantage to insulating the slope up from the knee wall (if high posted) and then insulating horizontally over the interior ceiling vs insulating a straight shot up the slope to the ridge?
Response to Tyler Keniston
Tyler,
Most old Cape Cod homes had no insulation in the sloped ceiling sections (even at the Levittown houses built after World War 2). That said, you are correct that sloped ceilings have existed for thousands of years. (Even tipis have sloped ceilings.)
For more information on this issue, see Insulating a Cape Cod House.
Q. "If one were building a story and a half, is there any advantage/disadvantage to insulating the slope up from the knee wall (if high posted) and then insulating horizontally over the interior ceiling vs insulating a straight shot up the slope to the ridge?"
A. For a thorough discussion of this question, see “Two Ways to Insulate Attic Kneewalls.”
-- Martin Holladay
Response to Martin Holladay
"Most old Cape Cod homes had no insulation in the sloped ceiling sections"
Ah ha. I didn't realize that. Thanks for the info and links.
Tyler
T&G under closed cell spray foam
I am in zone 6 and plan to use closed cell spray foam between the rafters in a cathedral ceiling, no venting. I was hoping to install t&g cedar on the rafters for the finished ceiling, but I'm confused by the statement in the article 'If you are building a cathedral ceiling, the biggest air-barrier blunder is to install tongue-and-groove boards as your finish ceiling without first installing taped gypsum drywall. A board ceiling is notoriously leaky, and this type of ceiling is often associated with roof sheathing rot.' Does this statement apply in my case?
Closed cell foam at code-min R is an air barrier.
If you're installing R49 (7-9") of closed cell foam you won't have moisture accumulation on the surface of the foam even if the t & g leaks as much air a tennis racquet. The temperature of the surface of the foam will be very close to room temperature, and well above the dew point of the room air. Closed cell foam that thick is also an air barrier, and a class-II (almost a class-I) vapor retarder, which keeps moisture from reaching the roof deck as well. The t & g has to be thick enough (1x or thicker) to qualify as a thermal barrier against ignition of the foam, but half-inch gypsum board qualifies on it's own.
That much closed cell foam is the opposite of "green", especially closed cell foam blown with HFC245fa (the vast majority of the market). In zone 6 only half the total R needs to be closed cell foam to provide dew point control on an equal amount of (much greener) fiber insulation, so dropping back to 4" of foam (R24-R28) and R25 of fiber snugged up to the interior side of the foam would be fine. HFO-blown foam has ~1/1000th the amount of damage from the blowing agent, but it's slightly more expensive, with only a few vendors. It has the advantage of being able to install 4"-7" at a time without quality or fire-hazard issues. (HFC blown closed cell foam has both problems if installed in lifts thicker than 2", with a substantial cooling period between lifts.)
But closed cell foam still has a very high polymer/R ratio making it still one of the least-green insulation options, even when blown with low-impact blowing agents. Using the minimum necessary for dew point control would be kinder to the planet, and kinder to your wallet.
With the air leaky t & g it's still useful to have some sort of air barrier to keep moisture from accumulating in the fiber during cold-snaps, but a membrane type of vapor retarder such as Intello Plus or Certainteed MemBrain detailed as an air barrier should be enough, either of which is far cheaper than another inch of closed cell foam. Don't substitute (much cheaper) 4-6 mil polyethylene here, since it has the potential of creating a moisture trap.
Response to Steve Harris (Comment #207)
Steve,
Dana Dorsett gave you good advice.
You quoted my article, but you left out important information from the section you quoted from. If you had read the entire section, your question would have been answered. Here's what my article states:
"Do I need to install an air barrier under the insulation?
"Yes, of course — especially if you are using fluffy insulation like fiberglass batts, blown-in fiberglass, or dense-packed cellulose. (If you insulate your ceiling with spray foam, the spray foam should create an air barrier, as long as the installer does a good job.)
"If you are building a cathedral ceiling, the biggest air-barrier blunder is to install tongue-and-groove boards as your finish ceiling without first installing taped gypsum drywall. A board ceiling is notoriously leaky, and this type of ceiling is often associated with roof sheathing rot."
I'm in zone 6. New structure
I'm in zone 6. New structure build. I'll be installing a beam/purlin system and overlaying 1x6 tongue and groove pine boards. Then I plan to build up a roof which I want to make unvented and at least R40. I plan to overlay a 5/8" sheathing layer (am assuming this should *not* be zip system to avoid a vapor barrier here, right?) on top of the tongue and groove, and tape it, in order to improve the fire resistance to internal (to the structure) fires, as well as to address the air barrier issue. Am intrigued by the detail at the gable edges to break continuity of the T&G into the overhang, still figuring that out. Here's my main question... I plan on at least 8" of insulation above the sheathing, then another sheathing layer (zip system?) and then standing seam metal roof. An obvious approach would be 2 sheets of 4" thick XPS, with joins offset. However... I would much prefer to use mineral wool than XPS. Say, 3 sheets of 3" thick Roxul Comfortboard... in which case I might even forgo the bottom sheathing layer and just use Membrain over the tongue and groove. But I've seen commentary previously to avoid mineral wool on roofs. Not entirely clear why. Would be grateful for comments either way as to why not to use mineral wool there, or alternatively how to use it properly to avoid whatever the issues are. Thanks!
Response to N/A N/A
(It would be nice if you told us your name.)
Semi-rigid panels of mineral wool are almost never installed on the exterior side of the roof sheathing on a sloped roof. I'm not saying you can't do it -- just that it is very rarely done, so you will be one of the guinea pigs learning from the experience. This information will either spur you on or turn you off, depending on your personality.
If you want to hire a builder or a roofer to do the work, the builder or roofer will almost certainly balk, and tell you that you are crazy.
Whether you use mineral wool or rigid foam, you need a very robust air barrier above the tongue-and-groove boards. (Moreover, the tongue-and-groove boards should not cantilever beyond the exterior walls if you want to avoid air leaks.) Taped plywood or OSB is fine. If you are using rigid foam above the roof sheathing, the vapor permeance of the air barrier is irrelevant. (After all, the rigid foam is already a vapor barrier.)
Semi-rigid mineral wool boards are a little squishy, which makes some builders nervous. John Straube directed a group of builders to use mineral wool as you propose on a project on his own property, and Straube told me it worked. That said, he wasn't the installer.
By the way, most green builders prefer EPS or polyiso to XPS, because XPS is manufactured with a blowing agent with a very high global warming potential.
Attic Roof Insulation - Thermal Bridging, Vapor Permeability,...
I plan to convert my attic into conditioned space for housing a heat-pump air handler and associated ducts. It's a 1950’s L-shaped ranch house with a 4/12 roof pitch. The main section of the house has 2"x8" rafters (actual size 1-1/2" x 7-1/4"). The short extension (other side of the L shape) uses 2"x6" rafters (actual dimensions 1-1/2” x 5-1/2”). The house is in Westchester County, NY. I believe it's in climate zone 4 (R38 roof insulation required).
I am thinking of installing site-built ventilation baffles using 1" foil-faced polyiso (with 1" air gap) as shown here and closed cell spray foam insulation under the baffles.
With the 5-1/4" left after accounting for 1" air gap and 1" polyiso, should I fill the remaining rafter cavity with closed cell spray foam? Or should I use 2" of closed cell and 3-1/4" of mineral wool batts?
With a vapor impermeable layers of polyiso (ventilation baffles) and closed-cell spray foam, possibly followed by a vapor permeable layer of mineral wool, what are my options for board insulation under the rafters for addressing thermal bridging? Board insulation under the rafters would make it like a cathedral ceiling. Would it be OK to use another layer of foil faced polyiso (vapor impermeable)? Should I use something like Roxul ComfortBoard (vapor permeable)? Any other options?
If there was no board insulation under the rafters, would mineral wool under closed-cell spray foam suffice as a thermal barrier and/or ignition barrier?
If there was no mineral wool, would foil-faced polyiso and/or Roxul ComfortBoard qualify as thermal or ignition barriers?
I don’t have the option to insulate above the roof deck. Therefore, I’ve been considering all options for achieving adequate insulation and venting under the roof deck. In the section of the roof with 2x6 rafters, I believe I’ll have to fill the entire rafter cavity (after 1” air gap and 1” polyiso) with closed-cell spray foam. That would still leave me short of R38; I’d have to add 2 inches of board insulation to achieve the R38 target. Any other suggestions? Thanks!
Response to User-6874083
User [It would be nice if you would share your name],
Q. "With the 5-1/4 inches left after accounting for 1" air gap and 1" polyiso, should I fill the remaining rafter cavity with closed cell spray foam? Or should I use 2" of closed cell and 3-1/4" of mineral wool batts?"
A. In the section with 2x8 joists, you have room for about R-34 of spray foam. (Of course, the installer will probably have to install this foam in at least two lifts.) You should know, however, that it can be difficult for spray foam contractors to fill a framing bay completely with closed-cell spray foam, which is very difficult to trim. It will probably be less than 5.25 inches thick.
But if we assume R-34 for the spray foam, you'll also have about R-6 for the ventilation baffle, for a total of R-40.
If you instead use the flash-and-batt technique, you'll have R-6 [baffle] + R-13 [closed-cell spray foam] + R-13 [mineral wool] = R-32.
Either method would work, although the use of closed-cell spray foam is often avoided by green builders (unless you specify one of the new types of closed-cell spray foam that uses a blowing agent with a low global warming potential; for more information on this topic, see Next Generation Spray Foams Trickle into the Market).
Q. "With a vapor-impermeable layer of polyiso (ventilation baffles) and closed-cell spray foam, possibly followed by a vapor permeable layer of mineral wool, what are my options for board insulation under the rafters for addressing thermal bridging?"
A. I would say that any type of rigid foam would work. This type of assembly is not at risk for moisture accumulation, because the ventilation channel provides safety.
Q. "Would it be OK to use another layer of foil faced polyiso (vapor-impermeable)?"
A. Yes.
Q. "Should I use something like Roxul ComfortBoard (vapor-permeable)?"
A. That would be unusual (and possible hard to deal with, because it's squishy), but it might work.
Q. "If there was no board insulation under the rafters, would mineral wool under closed-cell spray foam suffice as a thermal barrier and/or ignition barrier?"
A. Yes.
Q. "If there was no mineral wool, would foil-faced polyiso and/or Roxul ComfortBoard qualify as thermal or ignition barriers?"
A. Foil-faced polyiso is neither a thermal barrier or an ignition barrier. If you have a layer of rigid foam, you would need to cover it with drywall. Roxul ComfortBoard, on the other hand, could probably be left exposed (although I would check with your local building office to make sure that your inspector agrees with my interpretation).
Spray Foam Roof
Hi everyone,
I am working to build a small 100 square foot loft cabin, much like the "Cottage Life Bunkie" by Wayne Lennox. Unlike in that design, which has no insulation, I am looking to use this cabin year-round. I've been reading through as many of the articles on this site, which have been an excellent resource for me, but I've got a few questions I've not explicitly been able to find answers to. I’ve limited building experience, so bear with me on some of the more basic questions.
1. For the life of me I can't confirm my climate zone. I'm assuming a Zone 7 equivalent for the Huntsville Ontario Canada area. Am I correct in that?
2. I was surprised to read the article on warm sheathing in “Calculating the Minimum Thickness of Rigid Foam Sheathing”, and the risks of making walls too thick, and it got me thinking about my roof. If I were to spray a thinner layer of foam (say R-20 or so) on the underside of the sheathing, but ventilate the roof, would this mitigate rot concerns? Would this low an R value end up producing condensation on the interior face of the spray foam? My biggest concern with the cabin is rot/mold, not heating costs.
3. I haven’t been able to find any information on insulated floors. The floor of my cabin will essentially act like an exterior wall. In planning insulation for this floor, should I approach it in the same way as I would an exterior wall?
Thanks in advance for feedback. I’ve only just completed the foundation this summer so I’ve got lots of time to stew about my approach to the actual building itself this coming spring…
Andrew
It looks like about 4800HDD-C
It looks like about 4800HDD-C (base 18C) for the 25 year average in nearby Muskoka:
https://muskoka.weatherstats.ca/charts/hdd-yearly.html
That would make it the cool edge of zone 6, not zone 7:
https://www.greenbuildingadvisor.com/sites/default/files/images/Table%20301.3%282%29_0.preview.jpg
Condensation only occurs on the surfaced colder than the proximate air mass. What you're really concerned about is whether the interior moisture drives will be taken on as adsorbed water in the moisture susceptible roof decking. With R20 of closed cell foam (about 3") the vapor diffusion rate is quite low even when the roof deck is quite a bit colder than the dew point of the conditioned space, and it really wouldn't matter if it's ventilated above the roof deck or not. But any fiber insulation below the foam would have to be no more than R20 to keep the fiber insulation dry. How deep are the rafters?
But if it's R20 of open cell foam on the underside of the roof deck it could be an issue, unless there there is slightly more R than the total cavity insulation R mounted ABOVE the roof deck.
It's really the ratio of the R value above the deck to the total R that determines the average winter temp of the roof deck. The roof deck has to be reliably warmer than the dew point of the interior air to be fully protected from interior moisture drives. In a 4800HDD climate it would need to be 50% or more of the insulation value on the exterior for roofs (which suffer radiational nighttime cooling to below the outdoor air temperature, unlike walls.) If re-roofing is an option, installing 4" of polyisocyanurate above the roof deck would have an average wintertime performance of R20 or greater with R20 of fiber insulation under the roof deck.
What's under the floor? A vented crawlspace with a dirt floor? An open pier foundation? Elves seated on mushrooms holding up the floor with tiny hands? Is there any plumbing under the floor to worry about?
Response to Dana
Q: How deep are the rafters?
A: I'm using 2x8 rafters. Though, I was hoping to avoid any fiber insulation below the closed cell spray foam.
This will be a completely new build, so I have all options open. The challenge I foresee is my own ability to install polyiso on the roof exterior effectively. I had thought of doing a nice thick layer of polyiso on the roof deck but have read a lot of horror stories for the challenge of breaking screws and missing rafters.
Q:What's under the floor?
A: I actually laughed out loud at the elves on mushrooms idea. It's an open pier foundation with no plumbing.
Response to Andrew Southam
Andrew,
Here is a link to an article that discusses ways to insulate floors that are exposed on the underside to outdoor conditions: How to Insulate a Cold Floor.
Response to Martin
Thanks Martin, appreciate the guidance.
Membrane or underlayment required
Awesome article, thank you! I want to enclose my attic by using only closed cell spray foam. What underlayment or membrane is recommended to place on top of the roof deck sheathing in two scenarios: 1) a hot roof without ventilation and 2) a hot roof with a ventilation panel such as Hunter Cool Vent panels? The project is located in Climate zone 6, Dry. Thanks again!
unvented cathedral and closed cell spray foam in rafter bays
First of all...Thank you for this great article.
I know you said, in no uncertain terms, do not install tongue and groove ceilings nor install recessed lighting BUT if I use closed cell spray foam for the full insulation (2 X12 rafters) which will give great R values and vapor barrier, what do you thing of using slim LED recessed lighting (about 1 inch thick) and tongue and groove ceilings?
Your comments would be greatly appreciated. Thanks.
Response to Trent Willey (Comment #219)
Trent,
Q. "I want to enclose my attic by using only closed-cell spray foam. What underlayment or membrane is recommended to place on top of the roof deck sheathing in two scenarios: 1) a hot roof without ventilation?"
A. Since most manufacturers of synthetic roofing underlayment forbid the use of their products over an unvented roof assembly, your safest bet is ordinary asphalt felt. If you do choose to use a synthetic roofing underlayment, call the manufacturer to check whether they allow the use of their underlayment over unvented roof assemblies.
Q. "What about a hot roof with a ventilation panel such as Hunter Cool Vent panels?"
A. You can use any type of roofing underlayment you want. Asphalt felt is traditional, and still works well. If the roofing underlayment will be exposed to the weather for several weeks or months, you may prefer to use a synthetic roofing underlayment.
Response to Andre60 (Comment #220)
Andre,
Q. "If I use closed-cell spray foam for the full insulation (2 X12 rafters) which will give great R-values and vapor barrier, what do you think of using slim LED recessed lighting (about 1 inch thick) and tongue-and-groove ceilings?"
A. In my article, I addressed the situation you raise. I wrote, "Do I need to install an air barrier under the insulation? Yes, of course — especially if you are using fluffy insulation like fiberglass batts, blown-in fiberglass, or dense-packed cellulose. (If you insulate your ceiling with spray foam, the spray foam should create an air barrier, as long as the installer does a good job.)"
So, to be absolutely clear: If you have insulated your rafter bays with closed-cell spray foam, you have an air barrier. So in that situation, slim LED recessed lighting and tongue-and-groove boards are OK. The only issue you have to clarify with your local code authority is the need for a thermal barrier (usually interpreted as 1/2-inch drywall) in the interior side of the spray foam for fire protection. Different inspectors interpret this code requirement differently, but many inspectors will require the 1/2-inch drywall between the spray foam and the tongue-and-groove boards. For more information on this issue, see Thermal Barriers and Ignition Barriers for Spray Foam.
Response to Jason
Jason,
I don't know the definition of an "architectural" standing-seam roof. I'm assume you are talking about what is usually called a standing-seam metal roof -- probably painted steel. Does "architectural" mean something else?
As my article indicates, the type of roof you are describing can be detailed as a vented roof (as you propose), but only if you include soffit vents (something you didn't mention), and only if there are no interruptions in any of the rafter bays from the soffits to the ridge. That means no valleys, no hips, no skylights, and no dormers. If you have that type of roof, the unvented approach is fine.
As my article also indicates, you can also detail your roof as an unvented roof, as your contractors propose.
You didn't mention the name of your state -- I assume that "coastal Carolina" could include either North Carolina or South Carolina. It sounds like you are in Climate Zone 3, where the minimum R-value for roofs from the prescriptive table in the building code is R-38. Your plan to install R-30 insulation isn't ideal, although there may be legal ways to go with R-30 if you really want to. (For more information on this topic, see Three Code-Approved Tricks for Reducing Insulation Thickness.)
If you decide to create an unvented roof assembly with spray foam, remember to use closed-cell spray foam, not open-cell spray foam.
I don't think the existence of a ventilation channel improves the chance that a roof leak will be detected earlier than otherwise.
Humid Climate
Hello all,
Thank you Martin, for this and many other fantastic articles. Another thanks to all the commenters, this site is such a great forum.
I'm working on a new build outside of my familiar climate zone and would greatly appreciate some guidance. Research consistently turns up solutions most geared to northern climates. This job is in Coastal Carolina, which is quite humid. I'd previously reviewed this thread and shared the following intended approach with some reputable local contractors:
-'Architectural' Standing Seam Roof
-over underlayment
-over roof sheathing
-over framing w/ 'accuvent cathedral vent' and continuous 1-2" depth vent vaffle under sheathing. Tape-and-caulk air sealing of vent from wall to ridge vent. R-30 Roxul insulation below baffle.
-Drywall Ceiling
My intention was to provide drying capacity to the sheathing without adding the cost of two layers of strapping and a 'Structural' standing seam roof system. The metal roof is already going to stretch the budget.
The contractors both said to forget the baffle, and instead spray foam directly onto the underside of the sheathing. They advised that any vented/unconditioned space, even the full unfinished attic spaces in the project, will quickly be full of mold. I see no reason to doubt their knowledge about the climate.
However my major concern with their approach is that any leak through the metal roof/underlayment will be undetectable until massive rot has occurred. The sheathing will just have no capacity to breath. Another concern is heat gain as the current design calls for a dark grey metal roof.
Thank you in advance, looking forward to your thoughts on this!
Jason
Response to Martin
Martin,
Many thanks for the quick reply! The project is Zone3 near Wilmington, North Carolina, where I believe R-30 is the required insulation value. R-38 would be accommodated if needed.
'Architectural' seems to be an industry term that indicates direct installation over sheathing is required, vs 'structural' which can go directly over strapping.
Soffit vents would be used, but as you've said, my proposed approach would only add some resilience, it would not allow significant leaks to be detected.
The roof has a 9/12 slope and is as simple can be. I also have the ability to eliminate all roof penetrations, so perhaps I'll go that route with a high end roofer and dig deep to find some faith in the unvented assembly.
Even in this location (which has about 2000 annual heating degree days & 2000 cooling) you do see the closed cell foam as a prudent investment?
Thanks again, and have a great weekend!
That's US climate zone 3A
Wilmington is zone 3A. The IRC 2015 calls out R38, but local code may be based on earlier versions.
At 3" or more closed cell foam becomes structural, and at R30 (4.5" of HFO blown 2lb foam, or 5" of the more environmentally damaging HFC blown goods) would be enough that even if the sheathing rotted away completely the roof still wouldn't collapse.
Response to Jason (Comment #225)
Jason,
Q. "Even in this location (which has about 2000 annual heating degree days & 2000 cooling) you do see the closed-cell foam as a prudent investment?"
A. I wasn't implying that closed-cell spray foam is preferable to mineral wool. Indeed, it has disadvantages from an environmental standpoint.
Assuming that you or your contractor understand air barriers and airtight construction techniques, R-value is R-value. You'll get the same performance from R-38 of mineral wool as you will from R-38 of spray foam -- assuming you know how to prevent air leaks.
That's not exactly true @ Martin & papajay18
"You'll get the same performance from R-38 of mineral wool as you will from R-38 of spray foam -- assuming you know how to prevent air leaks."
Sort of, maybe, but not really. That's only true if it is NOT being thermally bridged by framing, which is never the case if applied to the under side of the roof deck.
The ~50% higher R/inch of closed cell foam compared to mineral wool means a shorter, and thus lower-R framing fraction. The overall performance of the assembly is LOWER with R38 of closed cell foam than it is with R38 of mineral wool due to more heat being transferred through the framing.
With very small framing fractions such as I-joist rafters 24" o.c. the performance hit is small almost negligible, but at typical ~7-8% framing fractions of milled 2x lumber raftered roofs it's a real hit (albeit a smaller hit than with the 20%+ framing fractions typical of walls.) But in this assembly R38 rock will will outperform R38 closed cell foam on a thermal basis.
In climate zone 3A it only takes an inch of closed cell foam on the underside of the roof deck for dew point control, and at 1" most closed cell foam is still over 1-perm, a class-III vapor retarder. A flash-inch of closed cell (or even 2 inches) filling the rest of the rafter bay with rock wool would offer a LOT more drying capacity than R30-R38 of closed cell alone. If it's 2x10 rafters 2" of closed cell (R13-ish) would leave just enough space for an R30 rock wool batt, for R43 total. With 2x12 rafters just ONE inch of closed cell (R6-ish) and doubled up R23s (R46), or R30 + R15 batt stackup would fill the space for ~R52 total.
At 2" closed cell foam would run about 0.5-0.7 perms (depending on vendor- look up the specs), which is about the same vapor retardency of the deck itself when the deck is dry, and still a sufficient drying path. At just 1" the closed cell foam is somewhat more vapor permeable than a dry roof deck, but not so vapor permeable that the roof deck will accumulate significant amounts wintertime moisture via diffusion from the interior in climate zone 3A.
Response to Dana Dorsett
Dana,
You're right, of course. While R-38 = R-38, the closed cell spray foam is thinner, so it leaves more rafter sticking out, exposed. The mineral wool covers more of the rafters, and therefore the mineral wool assembly performs a little better.
Regarding the "prudent investment" @ papajay18
At a buck or more per square foot per inch (15-18 cents per R per square foot) R38 of closed cell foam is going to cost on the order of $6 per square foot, give or take.
Holding the foam line at no more than 2" (R14 max) the foam is going to run $2.00-2.50 which leaves you $3.50-$4 to spend on filling the rest of the bay with rock wool. In most areas the cost of R30 rock wool is going to come in well under $3 per square foot, in some places it would be close to $2 per square foot. But say i'ts $3 per square foot, added to the $2-2.50 for 2" of foam it's still quite a bit cheaper than an all-foam solution.
So a 1-2" foam + R30-38 rock wool solution has:
* higher center-cavity R
*better overall performance due to the reduced thermal bridge
*lower overall cost.
An additional unaccounted for cost is the time-is-money and management cost of having to schedule two insulation crews rather than just one, but on a per square foot basis that should be pretty small.
That adds up to a more prudent investment than a rock wool only or closed cell only solution, since it's more protective of the roof deck than a single insulation type solution, and it's cheaper and higher performance than the foam-only solution.
Thank you Dana and Martin!
I hugely appreciate the thoughtful responses. I hope you both had nice holiday weekends!
-Jason
Underlayment Question
Hi everyone,
In the scenario shown in Image 3 of 3, with an insulated roof assembly with all insulation on the exterior side, where would roofing underlayment be required? Atop the first layer of sheathing below the insulation; atop the second layer of sheathing below the metal roof; or both?
Thanks!
Response to Andrew Southam
Andrew,
Building codes require roofing underlayment under the roofing -- which in the case you are discussing means above the top layer of sheathing.
It's also necessary to have an air barrier under the bottom layer of rigid foam. This might mean taping the roof sheathing seams (for example, with Zip System tape), or it might mean a layer of Grace Ice & Water Shield.
For more information on this type of roof, see "How to Install Rigid Foam On Top of Roof Sheathing."
Underlayment Question
Thanks Martin! I'm going to be using T&G so it will have to be the Grace Ice and Water Shield. Appreciate the advice.
Andrew
Response to Andrew Southam
Andrew,
Note the other possibilities mentioned in the article I linked to -- for example, a European air barrier membrane like Solitex Mento (a product available from 475 High Performance Building Supply), or a layer of synthetic roofing underlayment that is rated for use as an air barrier (with taped seams, of course).
Some homeowners worry about possible odors when using Grace Ice & Water Shield above exposed board roof sheathing. I have no opinion on the matter, but I thought I should mention it.
Deep Scissor trusses and blown cellulose
Hello,
I'm a newbie here, and wish I had found you a while ago. I am in the throes of building a straw bale house...bales in and scratch coat of hydraulic lime plaster on. My roof is a 6/12 pitch with scissor trusses. My house is 40 x 40, with an 8 foot porch all around, so my trusses are 56 feet wide. None of the interior wall are going to the ceiling, although I will have 2 chases through the ceiling to meet the vents in the roof for plumbing and for a solar tube that goes into the master bath. Only 3 electrical boxes in the ceiling for ceiling fans.
I have about 3 feet between the roof sheathing and the bottom of the truss. Here in Chewelah WA, about an hour north of Spokane, no insulation company I've talked with will blow cellulose in a 6/12 pitch. So I guess I need to figure out how to do it myself. :)
Here in Stevens County, I am building without a permit, called the owner/builder ordinance. So inspections aren't an issue. I DO want to do it right though. I am under the impression that code isn't ALWAYS right, it's just the code. So with that in mind, what are your suggestions for this 3 feet of space? I'd like to get to at least R60. I'm using radiant floor heat in slab, with a wood stove for quick heat-ups in fall and spring. I have 2 dormers on the south side for light. The roof ridge is vented, porch ceiling not in yet, but soffit vents will be placed.
For the dormers, should I just use closed cell spray since that is flat and unvented? Actually, I should just shut-up now and listen to your suggestions!
Thank you!
Kathryn
Response to Optimist 008
Optimist,
First of all, I'm going to have to provide a message to other GBA readers -- even though the advice I'm about to give won't help you very much. Here's the advice: Plan your insulation details before you begin construction. Once the roof trusses and roofing have been installed, it's too late to follow certain strategies. For more information on this idea, see "Plan Ahead For Insulation."
So, Optimist: Roof assemblies can be either vented or unvented. If a roof has dormers, a vented strategy is usually impossible, because dormers usually interrupt the path of a ventilation channel from the soffits to the ridge.
However, it's hard for me to tell what's going on at your house from your photos. Perhaps some rafter bays can be (theoretically) vented, while other rafter bays can't be vented. I'll warn you, however: trying to mix vented strategies with unvented strategies isn't easy, because you can easily end up with ventilation channels that face a dead end instead of reaching the ridge vent, and you don't want that.
If you think you can vent part of your roof, remember that every single rafter bay needs a clear channel, from the soffit to the ridge, with no impediments.
Any rafter bay that can't be vented needs an unvented approach.
To create an unvented insulated roof, your only option is to install closed-cell spray foam on the underside of the roof sheathing. Further details are in my article.
Kathryn
It's hard to tell from your photos but scissor trusses are usually a different pitch on the bottom than the top. Are yours really 6/12 on the bottom too. If not, installers may be more willing to fill them knowing that.
I know you aren't subject to inspections, but in an area of high seismic activity a roof like that needs additional bracing and hardware - especially structural blocking between the trusses at the exterior walls. It might be worth someone to the a look at it for you.
Thank you, Martin and Malcom
The entire north side can be vented, but the south side can't be totally vented due to the dormers. Your articles are awesome. Thank you.
Malcolm, the porch part of the rafters are a 4/12 pitch, but won't be insulated. I do have special Simpson ties at the exterior walls, but seismic activity here is very low on the scale.
I truly appreciate your feedback.
Kathryn
.
Closed and open cell
Kathryn,
Like Martin said, I would used Closed cell spray foam against the under side of the roof decking (probably 6 inches or so? You could then attach netting on the bottom chord of the trusses and then dense pack with fiberglass or cellulose. However, I think an easier approach would be to forgo the fluffy stuff and simply add open cell foam (6-8") after spraying in the closed cell. This will be much cheaper than using closed cell foam for the entire roof and also be better for the environment. Assuming you drywall the ceiling later- you will have a nice, conditioned service cavity for ductwork, can lights, etc.
Good luck!
Response to Rick
Thank you for your response. I need to do some calculations on what is needed depth-wise for the dormer areas and whether I will need to increase the depth of the walls on the dormer to get the R-value where I want it.
Right now, I'm leaning toward using closed cell where it is required (no open air flow) for the dormers and baffles and blown cellulose everywhere else. I have a contractor coming tomorrow for a quote, but he has already stated he won't use blown cellulose on a 6:12 pitch, so we'll see!
Kathryn
Kathryn
The contractors aren't being difficult, loose fill cellulose won't stay put on a 6/12 pitch.
Reponse to Malcolm
Malcolm.
I understand the loose fill won't stay put, but in a video you referenced several years ago, at about 8:35 or so, the gentleman teaching shows how to use blown in cellulose on a 6/12 roof. Is it just that it isn't common or just not done anymore? Or where you assuming I was talking about loose, not dense blown-in?
Thank you,
Kathryn
Response to Kathryn / Optimist
Kathryn,
You can't use the dense-pack method when insulating a scissiors truss. The dense-pack method requires a sealed cavity, with the cellulose filling 100% of the volume of the cavity.
When there is air above the top of the cellulose -- as when cellulose is installed on an attic floor or in a scissors truss -- you end up with blown-in cellulose, but the cellulose can't be dense-packed.
Question about air barriers.
Hello there,
It's hard to find good resources for this stuff.
My question was concerning air barriers the rigid foam + fluffy insulation roof type.
As I understand the articles:
I have an underlayment on the top sheathing.
An air barrier on top of the bottom sheathing
Do I need another air barrier below thethe fiberglass as well?
The detail provided doesn't seem to match the text for this roof type: It's missing at least one air barrier.
Response to User 7111533 (Comment #245)
User 7111533,
(By the way, it would be good to know your name.)
1. The roofing underlayment installed above the top layer of roof sheathing doesn't have to be an air barrier. Ordinary asphalt felt will work for this layer. It doesn't have to be airtight. Note that roofing underlayment is required by building codes.
2. How many air barriers you include in your roof assembly depends on your level of fastidiousness, how worried you are about future problems, your budget, and your airtightness goals. Clearly, you don't want to have a roof assembly that is so leaky that air movement causes moisture problems. At a bare minimum, you need an air barrier at the layer of the bottom roof sheathing. This might be taped Zip sheathing, a peel-and-stick product, or a European air barrier membrane with taped seams from Small Planet Supply or 475 High Performance Building.
An additional air barrier at the ceiling level -- usually taped drywall suffices, as long as your ceiling has no leaky electrical boxes or recessed can lights -- is good insurance.
Air Barriers
In the first bullet of your final summary you mention needing two air barriers if using fluffy insulation. I understand below the insulation would be taped drywall, but what would constitute an air barrier above the insulation? Any details you could provide would be helpful. Trying to understand what this looks like between my venting and the start of the batt insulation. Thank you!!
After posting this I saw the previous question and answer (245 & 246) which seems to be the same question I had. If understand your answer, you are suggesting a barrier attached to the bottom side of my roof sheathing, then the vent channel, then starting my batt insulation. Please confirm.
Response to Lance1320
Lance,
If you are using a fluffy insulation like fiberglass batts to insulate a vented cathedral ceiling, the lower air barrier would be (as you correctly noted) the drywall, while the upper air barrier would be ventilation baffles installed in an airtight manner.
The best insulation baffles are site-built, but most brands of commercial ventilation baffles can also be installed in an airtight manner, if their edges and seams are sealed with caulk or tape.
For more information on ventilation baffles, see "Site-Built Ventilation Baffles for Roofs."
The roof deck or insulation chute.baffle would be an air barrier
The diagram didn't label it, but the vented-no-foam picture clearly shows a barrier between the ventilation clearance and fluff:
https://www.greenbuildingadvisor.com/sites/default/files/images/Vented%20cathedral%20ceiling%20-%20FHB.jpg
Other pictures show the roof deck or spray foam layer as the exterior side air barrier:
https://www.greenbuildingadvisor.com/sites/default/files/Insulated%20cathedral%20ceiling.jpg
https://www.greenbuildingadvisor.com/sites/default/files/Cathedral%20ceiling%20with%20all%20insulation%20on%20the%20exterior%20side%20of%20the%20roof%20sheathing.jpg
https://www.greenbuildingadvisor.com/sites/default/files/images/Flash-and-batt%20method%20of%20insulating%20a%20cathedral%20ceiling.jpg
More about site-built insulation chutes/baffles ihere:
https://www.greenbuildingadvisor.com/articles/dept/musings/site-built-ventilation-baffles-roofs
Air Baffle Gaps
One further question.....some manufacturers of air baffle (venting) products recommend a gap between each adjoining piece. Doesn't that defeat the purpose of it being an air barrier itself? What is your recommendation?
[Click the number "6" below to advance to the next page, where the answer to this comment is posted.]
Response to Lance1320
Lance,
Q. "Some manufacturers of air baffle (venting) products recommend a gap between each adjoining piece. Doesn't that defeat the purpose of it being an air barrier itself?"
A. Yes.
Q. "What is your recommendation?"
A. Ventilation baffles should be installed in an airtight manner, with caulk or tape to seal the laps.
We have a cathedral ceiling with 2x12 rafters that we are planning to fill with dense-pack cellulose.. Above the rafters is triflex, above the triflex are 2x2s parallel and on top of triflex and rafters creating a 2 inch ventilation space from soffit to ridge. Plywood sheathing is on top of 2x2, then tar paper, and metal roofing. We need a thicker rafter bay to meet our r-value. Someone at Efficiency VT recommended 1.5" taped poly-iso sheet foam on the underside of our rafters before we install sheetrock. Our other option was furring out rafters another 2.75" with 2x material and then dense-packing the whole bay with cellulose. Either way we are finishing with taped sheetrock. Thoughts on which system would be superior?
Ryan,
There are two kinds of Tri-Flex that I am aware of. (I assume you are talking about Tri-Flex synthetic roofing underlayment.) One is called Tri-Flex Xtreme; it has a vapor permeance of 0.04 perm. Another is called Tri-Flex 15; it has a vapor permeance of 0 perm.
In other words, these synthetic roofing underlayments are vapor barriers.
That means that your ventilation channel is mostly useless, because it won't help remove moisture from the bottom layer of roof sheathing -- the layer of roof sheathing that gets wet during the winter. It also means that your roof assembly is illegal, because you need an effective ventilation channel above the top of your cellulose layer to meet code requirements.
You've got a problem, in other words. Any chance you can rip out the Tri-Flex and substitute a vapor-permeable roofing underlayment?
There is a 2" air space between the tri-flex (covering all rafters) and the backside of the roof sheathing. Why won't this air space help remove moisture from the bottom layer of sheathing?
I understand (now!) that the Triflex XT will not be vapor permeable, but I'm wondering how this will be an issue. Can't the ceiling dry to the inside?
And I am now am at a place of deciding how to finish off the inside of the ceiling in a way that 1. is air-tight 2. allows inward drying (if outward it seems like is not a possibility) and 3. achieves our desired thickness.
Martin, I think the Tri-flex is being used as ventilation baffles over the rafters, but under the vent space created by 2"x2"s.
Malcolm,
Whether or not there are two layers of roof sheathing or just one layer of roof sheathing, the Tri-Flex underlayment is a vapor barrier that prevents the ventilation channels from performing any useful drying. So my comments remain valid in either case.
Martin, the problem is probably mine, but as I read his stack up it is:
- Rafters
- Synthetic underlayment stretched over roof framing
- 2"x2"s on top of (parallel to) each rafter
- Plywood
- Building paper
- Metal roofing
With the cavity created by the 2"x2"s being vented at the eaves and ridge.
That's correct Malcom. And Martin, I hear your concern that its permeability is only 0.04 so it won't allow outward drying. But based on your article (https://www.greenbuildingadvisor.com/article/site-built-ventilation-baffles-for-roofs) the fact that tri-flex isn't vapor permeable shouldn't be a serious issue if air sealing is done properly on all six sides of the cellulose.
I still have all of my above questions:
"There is a 2" air space between the tri-flex (covering all rafters) and the backside of the roof sheathing. Why won't this air space help remove moisture from the bottom layer of sheathing?
I understand (now!) that the Triflex XT will not be vapor permeable, but I'm wondering how this will be an issue. Can't the ceiling dry to the inside?
And we are now at a place of deciding how to finish off the inside of the ceiling in a way that 1. is air-tight 2. allows inward drying (if outward it seems like is not a possibility) and 3. achieves our desired thickness."
Unless this seems like a disastrous plan, we would like to proceed without changing the triflex (it would either require roof removal or cutting from the inside and replacing with something that would be tricky to get as air-tight).
Ryan,
OK, I get it. And I'm sorry for the confusion.
I think that it would have been better to choose a vapor-permeable membrane to separate the cellulose from the ventilation channel. As things stand now, moisture that accumulates in the cellulose over the winter can't dry outward (although the ventilation channel does dry out the sheathing layer).
Will this assembly be problematic? It's hard to predict. As I wrote in one of my articles, "Site-Built Ventilation Baffles for Roofs":
"What if interior moisture is able to reach the underside of a ventilation baffle — isn’t it possible that the moisture might condense against the baffle (especially if the baffle is cold)? If so, isn’t this a good argument in favor of using vapor-permeable materials (for example, fiberboard, cardboard, or thin EPS) for ventilation baffles?
"The answers to both questions is a qualified yes. Anyone worried about this possibility should probably make their ventilation baffles out of a vapor-permeable material.
"That said, there really aren’t any reports of failures or problems resulting from the use of vapor-impermeable materials — for example, polypropylene, vinyl, or foil-faced polyiso — to make ventilation baffles. The main reasons:
• Not much moisture manages to make its way to the ventilation baffles (especially in homes that pay attention to airtightness);
• The air in the ventilation channels is often warmer than outdoor air, a fact which limits condensation; and
• Any moisture that does make its way there seems to be incorporated into the rafters via sorption. The ventilation channels are able to remove a limited amount of moisture from the rafters, and it appears that the rate of drying exceeds the rate of wetting."
In your case, the rafter ends don't extend into the ventilation channel, so this last method of moisture transfer is missing. This reduces the rate of drying compared to a system that includes conventional ventilation baffles between protruding rafters, so that is a potential worry.
In your case, I would advise (1) paying close attention to airtightness, and (2) crossing my fingers. I think you'll be all right. (That said, other GBA readers who are contemplating this approach should choose a vapor-permeable membrane like housewrap to separate the insulation from the ventilation channel.)
When it comes to a choice between (a) adding a continuous layer of interior polyiso and (b) thickening the framing cavity to allow for more cellulose, the second choice is somewhat safer, because it allows the cellulose to dry inward during the summer. If you go with option (b), including interior MemBrain will also add a layer of safety, by reducing outward vapor movement during the winter.
Thanks Martin. That is what I supposed based on what I read last night while trying not to have a heart attack thinking about tearing our roof off to change the membrane. That being said, I did a lot of research last year on but overlooked this; and I took a friend's advice on the tri-flex assemby, not knowing it was vapor-impermeable.
What's the proper way to determine the soffit vent size I will need for venting my roof. I've explained the system above and am now preparing to close in the soffits but want to make sure there is adequate ventilation. My carpenters asked if the rainscreen could provide enough of a vent space if it connected into the soffit. My inclination was that would not be enough and we should build a space between the plywood in the soffit as a vent, covered with hardware cloth and insect guard. Every rafter bay has a 2" by 24" space that runs from the eves to the peak and then is vented out through the space under the metal ridge cap. How wide of a gap in the soffit do I need for proper venting? And should this run continuously down the whole eve soffit of the house? Thanks.
Ryan,
Q. "What's the proper way to determine the soffit vent size I will need for venting my roof?"
A. The code formula is explained in this article: "All About Attic Venting."
Q. "Can the rainscreen provide enough of a vent space if it connected into the soffit?"
A. In some jurisdictions, this type of rainscreen-to-attic-vent connection is illegal. For more information, see "All About Rainscreens."
Does this same code formula apply to a vaulted ceiling assembly so that the "attic floor area" would actually be the sq ft. area of the baffles in each rafter bay?? (1 square foot of net free ventilation area for every 300 square feet of attic floor area)
Ryan,
When it comes to cathedral ceiling assemblies, the only code provision that applies to the vent size is found in section R806.3 of the International Residential Code (IRC): “A minimum of a 1-inch space shall be provided between the insulation and the roof sheathing and at the location of the vent.”
You'll be safe if (a) you use a commercial soffit vent and a commercial ridge vent, (b) every rafter bay is vented (which means that you can't use this approach if you have valleys, hips, or dormers), and (c) you maintain, at a minimum, the code mandated ventilation gap of 1 inch between the top of the insulation layer (or the top of the ventilation baffle) and the underside of the roof sheathing.
This is an incredible resource. Thank you for this article. I'm designing a house in Laredo, Texas (Zone 2) and am calling for Flash & Batt between 2x8 rafters. From out to in: Shingles, Membrane, Sheathing, Closed-Cell Spray, Batt, Gyp. The R-Value for this zone is R-30. Will using R-15 CCFoam + R15 Batt meet the requirement. Finally, would there be need/room for a radiant barrier in the assembly?
Pvel,
Q. "In Zone 2, will using R-15 CC Foam + R15 Batt meet the requirement?"
A. Yes, as long as your local building inspector accepts R-30 as adequate. (Some building codes require a minimum of R-38 in Zone 2.). For more information, see "Flash-and-Batt Insulation."
Q. "Would there be a need for a radiant barrier in the assembly?"
A. No. A radiant barrier only works if it is adjacent to an air space. In any case, R-30 insulation is far more effective than a radiant barrier. For more information, see "Radiant Barriers: A Solution in Search of a Problem."
Hugh Knowlton
I am a home owner living in a house as old as I am (67 years) located in Bergen County, NJ. I replaced the shingle roof in April of 95 with Woodlines 25 year GAF architectural shingles (This was the 3rd roof the house has had and as far as I know there has been no need to replace any plywood sheathing.).
I have a number of issues (like rotted fascia) not directly related to the state of the shingles that have me leaning on replacing the roof sooner than 25 years. I am trying to educate myself on attic ventilation and hope that GBA can help me.
I have 2 concerns with ventilation: one with the attic and the other with a cathedral ceiling in the master bedroom which was installed in the 70's or early 80's. I will express my concerns and questions with the attic ventilation in a separate post.
About half of the roof contractors that have given me estimates for replacing the roof and rotted fascia have suggest installing a ridge vent on the main roof ridge which is 56.5’ long. About 16-17’ of this ridge vent would be over the cathedral ceiling. I have read a number of GBA’s articles on roof/attic ventilation.
The roof rafters are 2” x 6” with 16” o.c. spacing and from my investigation have fiberglass insulation with no vent baffles; there are 4 small vents (not many) at the soffits. My concern is that installing a ridge vent over this cathedral ceiling might introduce more moisture problems than alleviate them. I seriously doubt much air will flow from the limited vents at the soffit to the ridge. With no vent baffles between the rafters I assume that insulation is right up against the roof sheathing: preventing airflow. From what I have read on your site airflow over fiberglass is not recommended anyway.
The condition of the drywall on the cathedral ceiling is good; there is some cracking in the drywall on one wall near the peak but is not a major problem. Where the joint is taped at the peak of the ceiling does show with time some bubbling in the tape. We repair this whenever we paint the room. Perhaps, this is due to the lack of ventilation at the peak where there are high temperatures.
I realize my house is imperfect and the way this cathedral ceiling was built would not be the way it would be done today. Because there is no evidence of rotting plywood sheathing and no leaking inside (and it has been like this for at least 35 years) I am inclined to leave this section of roof “as is” with no ridge vent. I can make the house more perfect by spending money but is it necessary? For now, my thinking is even though this cathedral ceiling is not perfect ”it doesn’t seem to be broken so why fix it”. Would you agree or suggest remedial steps to improve the ventilation? I don't mind spending money but just want to do it wisely.
Thank you in advance for you advice!
Hugh,
As my article notes, adding a ridge vent without performing air sealing work at the ceiling level can make the situation worse.
Your suggested approach -- doing nothing to change the ventilation details -- will probably work (in the sense that your roof assembly will perform no worse than it did before). But there are a lot of unknowns here -- there may be moisture damage near the ridge that you are unaware of.
In general, it's best to improve the situation by following up-to-date advice and current best practices. But if you can't afford to update the details on your roof assembly, you can leave everything the way it is, and skip the ridge vent.
Thank you very much, Martin.
I have another concern with attic ventilation in other areas of our house. I have 2 questions below. Attached is a colored plan that shows where there are cathedral ceilings, accessible attic areas and unaccessible attic areas.
The front (east side) of the house has on the left side the garage with a bedroom above. There is a ridge vent with styrofoam type baffles in the rafters similar to what is in the attached pic which I got off the internet. The ventilation here seems adequate although the baffles would not be the ones of choice used today; they are better than nothing!
The front (right side) of the house has a steep roof and the accessible attic is basically a crawl space to access the air conditioning fan unit and ductwork. The soffit vents are open and airflow seems adequate.
The back (west side) of the house is almost completely dormered with the exception of about 4’ on the north end and 1’ on the south end. The cathedral ceiling on the back right side is in the master bedroom and bath and is the area I was referring to in my previous post.
The unaccessible attic on the back left side is the area of concern. I marked the location of soffit vents on the back side of the house with an ‘X’. Some of them are circled. These circled soffits were added when we dormered this section of roof shortly after we bought the house in 1990. This enlarged the existing bedroom and adjacent walk-in closet, which became a bathroom. The contractor who did this work also finished the open space over the garage making it a small children’s bedroom.
I presume the circled ‘X’s (soffits) have the same kind of baffles that are in the cathedral ceiling in small bedroom over the garage. However, I am almost certain that these vents were blocked with blown in insulation, which covers the existing fiberglass batts and is a white fluffy material (I don’t recall the type).
I should mention that the other soffit vents on the back side of the house (X’s not circled) are likely not baffled as I have noticed in the construction that I can see in the accessible portion of the attic.
If I have the roofing contractor (who will replace our singled roof) add a ridge vent over this section of attic (location shown in red on the plan) it makes sense that I have him make sure that the rafters leading to the soffit vents are not blocked. The only way I think this can be done is to lift or remove the section of plywood sheathing closest to the soffit vents. If there are styrofoam baffles there these will likely break and need to be replaced.
Do you have a suggestion as to what baffles can be purchased and installed or secured from the top of the rafters (rather than the underside)? I should mention that this entire back section of interior ceiling is cathedral ceiling (sheet rock attached to rafters), which means that the existing insulation would only be a maximum thickness of 5.5 inches (the rafters are 2 x 6’s). Even though vent baffles are recommended to be 2” depth I think in this situation a 1” vent baffle would be better suited because it would minimally compromise the existing insulation. Your input is welcome!
You will notice that there is an existing attic fan, which I would remove for the reasons you have explained in one of your articles. There is an open area where air can pass between the two sections of attic (only 10’-11’ long). Do you think that the ridge vent installed over the unaccessible attic section will adequately exhaust air coming from the accessible section of attic? I would think it would be limited.
I appreciate your input and advice, Martin. I am thankful that there are experts in the field that the ‘average Joe’ like myself can turn to. Thank you!
I ran across this earlier today while researching how to construct our ceiling in the house we are building. I didn't get through every post in the thread, but there seems to be a high level of knowledge and experience here so I registered for the site and am hoping I can get some advice.
The house we are building has a shed roof throughout the upper level with all 16" TJI joists. Roofing is going to be standing seam metal over a layer of waterproofing titanium rolled on top of 5/8" plywood. The current insulation plan is for a few inches of spray foam insulation directly under the sheathing and then fiberglass batt insulation below that to fill the remainder of the cavity. With a minimum of 2" of spray foam I think we will be able to surpass an R-60 rating for the ceiling. However, as I am slowly discovering, there are two potential issues we may still run into.
First, we are planning on our primary light source throughout the house being can lighting. We are going to go primarily with 4" LED cans and hopefully we can get them in a low profile so they don't steal too much space that would otherwise be insulated. I'll also request that we get airtight fixtures to minimize air infiltration around the fixtures. Hopefully, with the combination of a thick ceiling cavity, spray foam insulation, cooler temperature of LED fixtures, and airtight fixtures we won't have a huge problem with the lights allowing too much air into the ceiling.
Our bigger problem though is that we really would like to install a plywood ceiling with aluminum T-bar trim between the panels. Before discovering the issue of air infiltration into the ceiling and the resulting condensation and rot, I figured we'd just attach the T-bar trim up to the rafters and fit the plywood inside of it. Now I realize that it might not be that straight forward. I guess the best course of action would be to just do a drywall ceiling and then skin it with 1/4" plywood. However, as good as that could end up looking, I am a purist at heart and don't like the idea of the plywood only being for aesthetics - not to mention the additional costs involved. That leads me back to just using the plywood as the ceiling and wondering if the spray foam insulation and thick and heavily insulated ceiling cavity might be enough to combat air intrusion up to the roof sheathing?
Any ideas if we are going to be running into issues with our plans. I know the prudent/practical approach would be a regular drywall ceiling with minimal protrusions (can lights) into the ceiling. Putting that aside for now though, if we move forward with things the way I described what are the odds that we will have issues down the road? Any other suggestions how we could accomplish what we are shooting for?
Thanks for any input or advice.
Matt
Matt,
You are planning to follow the flash-and-batt approach. For more information on this insulation method, see "Flash-and-Batt Insulation."
Your plan to use only 2 inches of spray foam will only work if you live in Climate Zone 1, 2, 3, or 4C. If you live in Climate Zone 4A, 4B, or anywhere colder, then 2 inches of spray foam isn't enough. See the article for a full explanation.
If your spray foam contractor is skilled, the spray foam layer will provide a fairly good air barrier -- although there are cases where the spray foam shrinks away from the roof framing, leaving cracks and air leakage paths. Omitting the interior air barrier is possible but somewhat risky.
If this were my house, I would either come up with a better lighting design -- one that doesn't involve recessed cans -- or I would purchase airtight electrical boxes to house the LED fixtures. (Pay attention to air sealing when installing these boxes.) I would also abandon the idea of a plywood ceiling, and instead would install gypsum drywall.
Response to Hugh Knowlton (Comment #267):
Q. "Do you have a suggestion as to what baffles can be purchased and installed or secured from the top of the rafters (rather than the underside)?"
A. SmartBaffles will work. Here is a link: SmartBaffle.
What is good product to tape SmartBaffle? Duct tape?
Russ,
For a long-lasting airtight seal, I would choose a quality construction tape like Siga Wigluv or 3M All Weather Tape.
Had I read this article first, probably would have skipped the cathedral ceilings--I have two of them. Framing now. Based on this article, closed-cell foam seems the most error-resistant method. Cold edge of Zone 4. The larger room has 2x8 rafters; the smaller room has 2x6 rafters.
Planning on R-49 attic per code. Majority will be vented gable with blown fiberglass. Talked to insulation sub about 7" closed cell R-49 on 2x8 and R-35 on 2x6 for cathedral ceilings. No cans. He says if doing the closed cell, only need sealed, non-vented R-30 to be the equivalent of R-49 blown in vented attic. He'd be happy to sell me more, but says he'd only put R-30 cathedral in his own home.
Seems that R-49 is R-49, shouldn't matter if blown or closed cell. Thoughts? Thanks.
Bruce,
Yes, R-49 is R-49.
Yes, you want R-49 insulation if possible, which means that it might be a good idea to find a way to add framing thickness to your 2x6 rafters.
Yes, spray foam contractors often mislead customers about whether it's a good idea to meet minimum code requirements for R-value. (For more information of this topic, see "It’s OK to Skimp On Insulation, Icynene Says.")
Yes, it probably would have been a good idea to figure these details out before you began framing your house. (Interested GBA readers can learn more on this topic by reading "Plan Ahead for Insulation.")
For some ideas on how you can thicken the framing cavity to solve the problem with your 2x6 rafters, see the article above (that is, the article where you posted this question).
Now that the complicated attic & roof are framed and I can visualize this better, I have some new questions. One room with a cathedral ceiling is maybe 55% within the attic and about 45% is no attic. The rafters are 2x8. Can I put 7 inches (R-49) closed cell foam in the non-attic part and use 13.5 inch (R-49) batts between the rafters in the attic. Of course the batts would stick out 6.25 inches above the rafters into the attic. If OK, should the batts be faced?
The second, smaller, cathedral room is about 50-50 with 2x6 rafters. I can do 5.25 inches closed cell (R-37) on the non-attic and still do the 13.5 inch batts (R-49), sticking out 8.25 inches above the rafters into the attic. I would make sure the rafters between the batts and the foam at a 45 degree angle are blocked off and the foam is completely sealed on all six sides. Is this a good plan? Thanks.
Bruce,
Your description is unclear, but I think your reference to "55% within the attic" means that about 55% of your ceiling is horizontal (with an attic above), and the other 45% of your ceiling is sloped. Is that what you mean?
Yes, you can insulate your horizontal ceilings with fiberglass batts (although cellulose would be much better, because cellulose fills all the nooks and crannies, and does a better job of limiting air leakage).
You have to follow the usual rules for continuity: You need air barrier continuity and thermal barrier continuity. Where your sloped ceiling meets your horizontal ceiling, make sure that your air barrier is continuous -- with no unsealed seams -- and make sure that your insulation is continuous (with no uninsulated voids, and no areas where the insulation isn't in contact with the air barrier).
Sorry Martin for the lack of clarity. See the attached drawing of the roof plan. The black line is the cathedral ridge (two different ridges). The blue is the cathedral outside back deck continuing into the great room. Red is the cathedral outside the attic; green is cathedral inside attic. This applies to two rooms.
For orientation, in the picture, you can see the back covered deck has the ceiling installed. Outside these two vaulted rooms, ceilings will be standard blown fiberglass. All products will be JM. Thanks.
Recently purchased a log home in NW Montana, zone 6 with a big snow load.
Here is the construction as explained to me by former owner, from roofing down to ceiling:
Metal exposed fastener roofing
Felt paper
.5" plywood
2x12" on edge with fiberglass batt insulation (Unknown depth)
poly (Unknown thickness) barrier
T&G pine as finished ceiling.
Roof is gable end with two dormers on each side so I am dealing with valleys all over the place. There are soffit vents in the areas where the bays look to run all the way to the ridge. The entire home is one large cathedral ceiling.
Due to some installation issues I may take off the roofing next year and reinstall to correct some issues. The house is a energy pit (log homes I know...) and I think a large part of that is the roof being air leaky and under insulated. It is also really the only part of the house I can do anything about.
If I tear off the roof what is the recommended way to improve this? Taking down the T&G from below is not an option due to exposed logs forming the purlins, etc... I have an idea of what to do, but the more I read the more I realize I don't want to get this wrong.
Thanks for any guidance.
KNPV_PSD,
First of all, can you tell us your name? (I'm Martin.)
Because of the valleys, a vented approach won't work. You need to create an unvented assembly.
You have two choices:
1. When the roofing has been removed, you can install rigid foam insulation above the existing roof sheathing -- as thick as you can manage. Then install either 2x4 purlins, 24 inches on center, to support your metal roofing, or a second layer of OSB or plywood roof sheathing above the new rigid foam. If there are any soffit vents and ridge vents, seal the openings with spray foam.
or:
2. When the roofing has been removed, pull up the existing plywood sheathing, one area at a time. Remove the existing fiberglass insulation, and all the rodent droppings that will be mixed in. Then install closed-cell spray foam from above, directly on the tongue-and-groove ceiling -- as thick as you can manage. Note that if the tongue-and-groove ceiling has big gaps or knotholes, you may need to install strips of cardboard before you install the spray foam. Then reinstall the plywood roof sheathing, felt underlayment, and metal roofing.
Sorry about the name, I didn't see where to add that. I thought I was stuck with a username for some reason...thanks for responding so quickly.
If I go with 2, do I remove the plastic above the T&G? Or can I leave it in place to take the place of the cardboard you described. Also can I go with say 5" of spray foam and then use the remaining 7" for a lower cost material? And do I seal up the vents in option 2?
Thanks again for the help.
Loring,
You don't have to remove the polyethylene (which I forgot about) -- it will do instead of the cardboard I suggested.
With option 2 -- also an unvented approach -- you need to seal up the soffit vents and ridge vent. And yes, it's possible to combine 5 inches of spray foam with a lower-cost insulation material.
More information on Option 1 here: "How to Install Rigid Foam On Top of Roof Sheathing."
Great, I appreciate it Martin.
Any advantage to a hybrid? Doing option 2 to air seal and get the insulation in and then add a single layer of rigid to get a thermal break on the 2x12s? Or is the juice not worth the squeeze?
Loring,
I suppose you could do both. If you do, it's really important to seal up all hidden air leakage paths, so that there is no air movement between the foam layers.
I have a low slope 2:12 cathedral ceiling. The joists are 16" TJI's and I have 13" (R50) mineral wool insulation. There is approx 3" of air gap for ventilation above. The snow load is such (zone 6) that there are so many wall studs around window openings etc.that I am using split external/internal insulation on the walls. 6" mineral wool externally (Roxul Comfortboard) and 3" internally. The air/moisture barrier on the walls is external (Delta SA)
This means that the insulation in the roof has to project out as far as the external insulation.
The air barrier will be poly attached with sealant and internal finish will be drywall.
I've just realized that there is no way of preventing wind washing coming up through the soffit into the roof insulation and having cold air penetrating along the joint between the TJI flange and web.
This will make the poly air barrier cold and probably lead to moisture build up in the drywall. No matter how well you pack the insulation in against the TJI's there will be some cold air flow.
How can I solve this please.
Jim,
You have several issues here. The first issue is that you haven't detailed the ventilation properly for a low-slope roof. You should red this article: "Insulating Low-Slope Residential Roofs."
Air does not generally flow easily from soffit vents to a ridge vent in a low-slope roof, so you need a minimum air gap between the top of the insulation and the underside of the roof sheathing of 6 inches. Three inches isn't enough. You also need a special kind of vent in the center of the roof -- a doghouse vent or cupola. At this point, I'm not sure what you can do about these flaws -- a remedy depends on what stage of construction you are at.
Second, it's usually not a good idea to install interior polyethylene, especially if your house will ever be air conditioned in the summer. For more information on this issue, see these two articles:
"Vapor Retarders and Vapor Barriers"
"Do I Need a Vapor Retarder?"
Your concern about wind-washing is valid, but the other issues raised in my response are more worrisome.
Hey Martin,
I was preparing to finish my Cathedral ceiling with, "tongue-and-groove as the finished ceiling without first installing taped gypsum drywall" when I came across your article, How to Build an Insulated Cathedral Ceiling _ Martin Holladay _ November 18th 2011.
I've read it through but felt I should ask you to please consider responding to my question:
How should I best finish this ceiling?
Here's the details:
... log cabin 20' x 16' x 8' eave height and 13' center ridge beam height (parallel w/16' wall)
... (no collar ties, no joists)
... simple, vented, gable roof with 12/6 slope
... 16'x3'metal roof panels ( https://integritypoststructures.com/post-frame-metal/ )
... on top of Blueskin RF200 Self-Adhesive Ice and Water Barrier
... on top of plywood sheathing
... on top of 16' long 2x6 (16" centers)
... 6" pink fiberglass insulation between 2x6's (not to code)
Thanks for the heads up.
Alan Dyck
Calgary
Alan,
You called this a "vented gable roof" but you didn't provide venting details. Does the roof have soffit vents? A ridge vent?
Does every rafter bay have a ventilation baffle?
Were the ventilation baffles installed in an airtight manner?
How deep is the ventilation channel between the tops of the ventilation baffle and the underside of the roof sheathing? (If your rafters are 2x6s that measure 5.5 inches deep, and you have fiberglass batts that are 6 inches deep, you must have compressed the fiberglass -- and I'm not sure if you even have any ventilation channels.)
When the fiberglass batts are perfectly installed, they have an R-value of about R-19 -- but the thermal bridging through your rafters seriously degrades the performance of the fiberglass, dropping the performance of your insulation to well below R-19. Since you need R-49 in your climate zone, you've got a fairly big problem here in the R-value department. How you finish your ceiling is the least of your problems. (Briefly: you can finish your ceiling any way you want, as long as you have an interior air barrier like drywall.)
Solving your R-value problem is going to cost some money. The least expensive fix is probably to remove the metal roofing, install one or more layers of continuous rigid foam above the roof sheathing, and then install a second layer of roof sheathing. Once that work is done, you can install roofing underlayment and re-install the metal roofing. This fix requires you to seal the soffit vents and ridge vent (if these vents exist). For more information, see "How to Install Rigid Foam On Top of Roof Sheathing."
Thanks Martin,
yes the roof R-value is weak, the R-value in the walls is also, but this cabin is an outbuilding on a farm, and has no utilities, w/wood stove heat, seasonal use, in rather dry climate.
I appreciate your response,
Alan
Hello and Happy New Year,
Thank you Martin and others for the invaluable information on this site. I learned a lot in just a few days.
I'm Greg, I bought my first house in Staten Island, NY (zone 4) not too long ago. My question is about venting the cathedral ceiling rafter bays ending at roof hip to prevent moisture buildup. I apologize for lengthy description but I am afraid I could miss some important details.
Background: the house is almost 30 y. o., 50' x 30', the roof is about 6/12, framed with 2 x 8" at 16" o. c., asphalt shingles over plywood sheeting. NE part of the top of the house is a large living room (33' x 15'). The room has a cathedral drywall ceiling with one long side and the front triangular side directly below the roof, while the other long side is facing the non-conditioned attic, i.e. the ridge of the roof is above the attic. The room has been too cold in the the winter and too hot in the summer.
As I was recently investigating a minor leak, I discovered that some R-19 fiberglass was missing. Eventually I ended up taking down the ceiling and the insulation and discovered that a lot of insulation was "stolen" by mice who apparently lived in the attic for quite a while as the second floor was uninhabited for several years due to former owner's passing. The fiberglass was deposited and densely packed inside the ventilated soffits.
The roofer, at his suggestion, just now installed a second layer of shingles over the original one (nearly 50% cheaper than brand new roof). I chose the lightest color available (light gray). He also installed ridge vent in addition to the existing power vent. I will do the inside insulation myself. I am about to make 1" vent channels using 1" XPS for the rafter bays. I will also drop down the ceiling another 2" or so by strapping hat channels with extra spacers at 24" o. c., to allow just enough space for R-30 Roxul bats. I know the total assembly R is slightly lower than the code minimum but dropping the ceiling any more might not look nice.
Now, as I mentioned, several rafter bays (the longest ones being just over 8') hit the hip ridge on both sides at 45 degrees. The drywall in that area was originally installed using some spacers here and there between it and the rafters. It was also attached to the hip ridge which is deeper that the rafters (2 x 10). The roofer advised me against installing a hip ridge vent due to water penetration concerns.
I imagine several solutions to mitigate potentially damaging moisture buildup on top of those rafter bays:
1. Apply a layer of closed cell foam with fluffy insulation under it just in the problem bays. But I am not sure if the sheeting will have enough opportunity to dry outside. Also, being somewhat on a budget, I am reluctant to hire a contractor just for that purpose, and the two-component DIY kits do not look promising. I wonder if I could just use several cans of TiteFoam instead. But overall, I'm not a fan of that solution.
2. Provide, say, 1-2" space between Roxul bats and sheeting and install no vent channels or vapor permeable channels or channels with some space left between their top ends and the hip ridge. In this case, the moisture can escape to the attic through the space provided by the strapping above drywall ceiling.
3. Build airtight (or nearly airtight, since I am using XPS) vent channels but connect them to each other and, eventually, to the nearest channel that reaches the attic by drilling a series of, say 3/4" holes at the top of each rafter directly below the sheeting., so the holes are part of one channel system that ends up in the attic. I assume this could be done without compromising the structural integrity of the rafters.
I realize that neither solution is nearly ideal but I am just looking for the most acceptable one in my situation. Or is there another solution I did not think of?
I also have two skylights in that room, each two rafter bays wide. I am not as much concerned about those as their bottom and top are only 2.5' away from the soffit and the attic, respectively. Still, I wonder if it would help to add vent channels to the bay sections above and below.
I would really appreciate a prompt reply, as it is winter and I need to wrap up my project ASAP.
Thank you!
Greg
Greg,
You can't vent rafter bays that die into a hip. That's why my article notes, "if the geometry of your roof is complicated — with features like hips, valleys, and dormers — it’s impossible to assure air flow through all of your rafter bays."
All of the rafter bays that fail to terminate at your ridge will need to be detailed as unvented assemblies. If you can't install rigid foam above the roof sheathing -- I'm assuming you can't, since your house has new roofing -- the only way to proceed is to install an adequately thick layer of closed-cell spray foam on the underside of the roof sheathing.
You can either install all of the desired R-value as closed-cell spray foam, or you can use the flash-and-batt method. For more information, see "Flash-and-Batt Insulation."
Martin,
Thank you very much for your quick reply! You are correct that I can't install rigid foam above sheeting. It looks like I must use spray foam (at least 2.5 inch, i.e. R-15 for my zone according to your article) just for the rafter bays in question. Could you please confirm whether it is OK to use this hybrid approach to a roof assembly (make it part vented and part unvented)? I believe your article doesn't explicitly state that. Could you please also confirm that, in case of a leak, the sheeting will be able to adequately dry outside under two layers of shingles and a layer tar paper? Lastly, please excuse my non-pro approach, but would it be at all possible at all to use something as Loctite TiteFoam (which, as the company rep stated in the HD Q&A section, is closed-cell, although I am not sure if that is correct), or any other one-component closed-cell PU spray foam product for that matter, instead of a 2-component kit? It seems that it would make things much easier if I made or bought a flat fan-shaped applicator, considering the relatively small area of application.
Thank you again for your help!
Greg
Greg,
Q. "Is it OK to use this hybrid approach to a roof assembly (make it part vented and part unvented)?"
A. Yes.
Q. "Could you please also confirm that, in case of a leak, the sheathing will be able to adequately dry outside under two layers of shingles and a layer tar paper?"
A. No, I can't confirm that. Asphalt shingles will prevent outward drying. If you have a leak, you have to fix the leak promptly. No one with an asphalt shingle roof can depend on outward drying to handle a leak -- whether the roof is vented or unvented.
Q. "Would it be at all possible at all to use something as Loctite TiteFoam (which, as the company rep stated in the HD Q&A section, is closed-cell, although I am not sure if that is correct), or any other one-component closed-cell PU spray foam product for that matter, instead of a 2-component kit?"
A. No. There just isn't enough foam in the can of a one-component spray can. Go out and buy one or more two-component spray foam kits -- or hire a spray foam contractor.
Martin,
I can't thank you enough for your prompt feedback. Before I can proceed with the hybrid vented/unvented insulation model for my roof, would you mind clarifying a couple of things:
1. Looking at your answer to my second question, I see some contradiction with what I've learned so far about roof assemblies. I thought the sheathing should be able to dry either inside or outside. In case of vented roof, I have some degree of peace of mind knowing that if some small amount of water somehow seeps under the shingles and gets absorbed by the plywood, it can eventually evaporate from its other side before it starts rotting. That seems to be not the case with unvented roof, which makes me wonder whether this design is appropriate for our generally humid climate.
2. Since I am planning to drop the ceiling lower by adding strapping perpendicular to the rafters, do I need to install any air and/or vapor barrier between vented and unvented sections of the assembly?
Thanks!
Greg
Greg,
Q. "I thought the sheathing should be able to dry either inside or outside. In case of vented roof, I have some degree of peace of mind knowing that if some small amount of water somehow seeps under the shingles and gets absorbed by the plywood, it can eventually evaporate from its other side before it starts rotting. That seems to be not the case with unvented roof, which makes me wonder whether this design is appropriate for our generally humid climate."
A. It's true that vented roofs are more forgiving than unvented roofs. If you were building a new house, you could have created a vented unconditioned attic. But you have an old house. If you were thinking ahead, you could have installed rigid foam above your roof sheathing before you installed new shingles. But you didn't think ahead. So you've run out of options.
Q. "Since I am planning to drop the ceiling lower by adding strapping perpendicular to the rafters, do I need to install any air and/or vapor barrier between vented and unvented sections of the assembly?"
A. Your vented section needs two air barriers: one air barrier above the fluffy insulation (you can create this air barrier by installing airtight ventilation baffles) and one air barrier below the fluffy insulation (your drywall). There really isn't any reason, however, to install an air barrier between your vented section and your unvented section.
This is in response to #297.
Martin, thank you again for your comment.
I wonder if you or anybody else has an opinion on using smart vapor retarders for relatively small unvented sections of cathedral ceiling, like those dying at hip ridge in my case. I only have one hip ridge like that, the other three are part of vented attic. Please see this link from the SOLITEX MENTO distributor:
https://foursevenfive.com/blog/cant-vent-at-valleys-and-dormers-use-a-smart-vapor-retarder-not-foam/
Exactly the same setup appears on this site. Please see the picture attached to comment #3 to this article: https://www.greenbuildingadvisor.com/article/smart-vapor-retarders.
This opinion is very important to me as I have certain reservations against installing closed cell foam in general, and particularly now as it is mostly below freezing outside and is chilly in the room in question since there is currently no insulation on the ceiling, with the exposed soffit vents just plugged with fiberglass. The commercially available spray foam kits require at least 60F surface temperature.
I also wanted to reiterate that I am planning to drop the ceiling by 2" by running strapping perpendicular to the rafter beams. That space, being filled with rockwool, can also act as a vapor escape route to the ventilated attic.
BTW when I did not have rigid foam installed above the roof sheathing, it was not because I did not think ahead but because I could not afford more than $10K extra cost associated with it vs. simply adding a second layer of shingles on top of the existing one. I was also "lucky" enough to discover both lots of missing insulation and a minor leak in the end of December. The roofer had to come an the New Year's day as it was the only day with mild weather, so his guys could complete the job in one day.
Thanks!
Greg
Greg,
My reaction to the approach promoted by 475 High-Performance Building Materials is laid out in the following article: "Smart Vapor Retarders for Walls and Roofs."
While 475 tries to sell products for this approach, the approach (a) violates building codes and (b) is judged to be risky by most building scientists.
It's up to you to weigh the evidence and decide how to proceed.
Hi folks, I'm back again having spent quite a bit of time working through the pre-cutting construction phase of my small cabin. I'm nearing the point of assembly on site now and wanted to run my approach by the group for some thoughts before things become permanent. I've attached an illustration of how my roof assembly is designed. I know I am light on the roofing insulation - 5" is not ideal but I'm quite concerned about my ability to hit the 2x8 rafters with screws through everything. I am not concerned about energy performance of this cabin - purely about preventing mold/rot. What are everyone's thoughts on what I'm proposing here with regards to moisture issues?
Secondly, I've been recycling wood from a family friend's cottage demolition and was able to rip a number of 2x8's to use as the 2x4 wall studs. As a result, my exterior walls are 2x4 so I'm looking at mineral wool batts between the studs as well as rockboard 80 installed on the exterior sheathing. I've been reading a lot about vapor barriers/retarders and smart retarders and am leaning much more toward something like Intello Plus on the interior rather than poly. Given my amature status I feel an intentionally "breathable" wall will help with some inevitable errors/misses on my part. I'd be looking at Intello Plus on the interior, wool batts, exterior sheathing, house-wrap, rockboard 80, furring strips, siding. Sound like a plan?
Appreciate everyone's input - this site has been an excellent resource.
Thanks,
Andrew Southam
Andrew,
Q. "What are everyone's thoughts on what I'm proposing here [for the roof assembly] with regards to moisture issues?"
A. My main comment concerns airtightness. Make sure that the Solitex Mento is installed in an airtight manner (with taped seams) -- and/or that the layers of XPS have taped seams.
Q. "I'd be looking [for the walls] at Intello Plus on the interior, wool batts, exterior sheathing, housewrap, rockboard 80, furring strips, siding. Sound like a plan?"
A. Yes -- again, assuming you pay attention to airtightness.
Thanks again Martin.
My intent for the roof is to tape both the solitex and xps. For the walls I'll be taping the housewrap.
Hello my name is Mason and I am hoping someone can help me. After reading the article and all the comments my head is spinning. I live in NW Iowa, zone 6, and I just added an addition to my house. The outside of the addition is done with the siding and shingles on. Nothing on the interior is done yet. It has a cathedral ceiling, and the rafters were built using I Joist. It is just a simple gable roof and I was planning on it being vented. If there is a perfect way to insulate this how would you do it?
Do you vent it and leave an inch air gap and use closed cell spray foam?
I was planning on using recessed can lights? I thought since I used I Joist as the rafters and planning on using closed cell spray foam that there would be plenty of room in the rafters for canned lights? Any help would be greatly appreciated. I think I do not know enough about this subject and have been reading way too much about it and now I am completely lost.
Mason,
If you are planning to have a vented cathedral ceiling, that's still possible. Ideally, your gable roof is not interrupted by roof valleys or skylights.
A vented gable roof needs soffit vents and a ridge vent. So your first order of business is verifying that you have soffit vents and a ridge vent. If you don't have these, a carpenter or roofer can retrofit them for you. If your roofer forgot to install a ridge vent, you'll need to hire someone to remove the cap shingles at the ridge, cut back the roof sheathing a few inches on either side of the ridge, and install a ridge vent and new ridge shingles.
You'll also need ventilation baffles in all of your rafter bays. Here is a link to an article about ventilation baffles: "Site-Built Ventilation Baffles for Roofs."
Once your ventilation baffles are installed, you can insulate the rafter bays with fiberglass batts, mineral wool batts, cellulose, or even the flash-and-batt approach.
I strongly urge you not to install recessed can lights, which are associated with air leaks and moisture problems in cathedral ceilings. If you insist on some type of lighting that resembles recessed can lighting, buy some of the new "pancake" LED fixtures that fit into a shallow electrical box, and make sure you buy a type of electrical box called an airtight electrical box. Install the boxes carefully, and verify ceiling airtigtness with a blower door test.
Martin thank you for the quick feedback. It does have a ridge vent and soffit vents. I will make sure to have ventilation baffles installed in all rafter bays.
I know you do not suggest recessed can lighting, but that is why I was wondering if instead of doing batt insulation if I did closed cell spray foam at 8 inches I would approximately have an R value of 52. I could leave an 1 inch air gap for ventilation and that would leave me 3 inches in space where slim or pancake light recessed light could be installed? And my R value should be high enough that it will not allow the warm air to reach the roof deck? Would that work or am I forgetting something?
Mason,
If you choose to install spray foam insulation, you don't have to worry about air leakage. As long as the recessed cans aren't taking up room required for insulation, they won't cause problems if you have an adequately thick layer of rigid foam above them.
Thank you for the quick response!
Hey Martin,
Well my plans changed. Now the person doing the insulation wants to do an unvented roof and spray closed cell foam 4 in thick directly to the sheathing and then fill the rest with fiberglass batts. I know you said that can be done using the flash and batt approach. By doing so won't that only give me roughly 24 R value in spray foam and 19 in batt insualtion so a total R value of 43. In Iowa I thought you needed a R value of 48?
By doing what they suggested am I asking for trouble?
Mason,
In general, with new construction, it's certainly desirable to (at least) hit minimum code R-values, for two reasons: (1) if you have less than code minimum insulation, your energy bills will be higher than they would be if you met code, and (2) your local building inspector probably wants you to comply with the law.
Of course, complying with the building code requires planning ahead, and it doesn't seem as if you did that.
You have two choices:
1. You can go with your current plan, and accept R-43, as long as your local code inspector, if any, is happy. (Note that there are several code compliance paths that allow lower R-values for cathedral ceilings than specified in the prescriptive table; for more on this issue, see "Three Code-Approved Tricks for Reducing Insulation Thickness.")
2. Increase the thickness of the spray foam layer in your flash-and-batt assembly so that you can achieve R-49.
Mason, I'm not in a position to give expert advice on insulation but just wanted to mention, in case you may not be aware, that some new wafer-thin recessed lights recently became available online and in big box. Many of those are also IC rated and suitable for damp locations. Aside from being 1/2'' thick (flush with drywall underside when installed), they are connected to a low profile electrical box via a low voltage connector wire. This makes the installation and air sealing a breeze. You just connect the box to commercial power, let it rest on top of drywall, plug the fixture into the connector, apply some sealant under its rim and clip it on. I am currently replacing all my old leaky cans with those. Here is just one example:
https://www.amazon.com/Lithonia-Lighting-WF6-LED-30K/dp/B01ND1L263/ref=sr_1_3?ie=UTF8&qid=1547220349&sr=8-3&keywords=lithonia+6+inch+wafer+led
Good luck!
Greg
Thank you! Those should work great. I haven't seen those before. Thanks again!
In response to #308.
Martin, thank you again for quick reply! I will read your article and decide. I am not too concerned about the code, just about the end result.
Martin,
As I mentioned earlier, I also have two skylights taking two 16" o. c. rafter bays each on my cathedral ceiling. In other words, I have two small potentially unvented sections under each skylight (each one is about 2.5' long from the vent soffit to the bottom of the skylight). However each of those sections is adjacent to a fully ventable section. I am becoming increasingly convinced that by cutting, say, a 6" long x 1" deep slot in the 2 x 8 rafter at the top corner of an unvented cavity in question (between the beam and the sheathing), I can provide enough ventilation for that section by creating a full-fledged vent channel with a short "tributary" channel. I have no knowledge of anything like this being implemented elsewhere, but I do not see why this solution should fail for a short section like mine. If anything, the air flow in the neighboring channel should create enough pressure differential to pull the air from the cavity in question. What do you think? Hope you don't accuse me of "heresy".
I do not believe cutting a short 1" strip off the top side of 2 x 8 beam would jeopardize its structural integrity, but I am ready to reinforce it with, say, a wide strip of 3/4" plywood as a sister beam as an extra precaution.
As an extra step to prevent any moisture buildup, I can make the vent baffles for those short cavities out of a vapor-permeable or somewhat permeable material. As you mentioned in your article about site-built vent baffles, that could be an option if there is such concern. Is there any material you would recommend for that? Or would a "smart" retarder be an option? I am asking this because I currently have a roll of Membrain available. I can also refer to the material vapor permeability table from Building Science Corp., in case you might have certain permeability range in mind.
Thank you again! I hope this would be my final inquiry on the topic.
Greg
Greg,
Q. "By cutting ... a slot in the 2 x 8 rafter at the top corner of an unvented cavity in question ... I can provide enough ventilation for that section by creating a full-fledged vent channel with a short 'tributary' channel. I have no knowledge of anything like this being implemented elsewhere."
A. Trust me. Carpenters have been doing that for years, either with drills or Sawzalls. The result is a weakened rafter and ineffective venting. Whether or not your roof will accumulate enough moisture to cause sheathing rot will depend on the indoor relative humidity, the climate, and the leakiness of your ceiling. Whether or not the notches will weaken the rafter enough to cause failure depends on the depth of the notch and your snow load. My advice: don't do it.
Instead, insulate these unvented rafter bays with closed-cell spray foam, installed on the interior side of the roof sheathing.
Martin,
Thank you very much! I may have to wait for warmer weather to apply spray foam.
In response to 335 - It was well planned I just want to make sure it is done right because everyone says to do something different.
They are 12'' I Joist - which were chosen to give me the most room possible for insulation. Builder wanted to go the vented route, which can still be done, it has a ridge vent and eaves vent. He wanted to install baffles leave 1 inch ventinlation gap and then use R 38 batts....
My guy doing the insulation says no don't do that. He said to do it unvented and wants to spay 4 inches of closed cell and then fill the rest of the bay with 6 inch batts....
I can still do either way. Everything has been thought but every person says to do something completely different. So I am trying to ask what would be the best? SInce you are an expert I would love to hear your advice.
I thought you needed an R value of 49, but insulation guy says in cathedral ceilings you only need an R value of 38. I do not anything about building a home but trying to learn as much as I can. From what I understand I have all the options available and since I do have 12'' I joist I have the most room possible for insulation for this type of situation...... I just need to know which is the "best" way. Thanks
Mason,
Codes vary, and your local code may well require only R-38 for a cathedral ceiling. As I noted in my last reply, I wrote an article on this topic ("Three Code-Approved Tricks for Reducing Insulation Thickness") that provides several code-approved approaches for cathedral ceilings that allow less than R-49.
In zone 5, a flash-and-batt ceiling needs to have at least 41% of the total R-value of the roof assembly from the closed-cell spray foam layer; the remaining 59% (or less) of the total R-value can come from fluffy (air-permeable) insulation.
If you have 12 inches, and you want R-54 using the flash-and-batt method, you can get it. Just install 4 inches of closed-cell spray foam (for R-24) and 8 inches of fiberglass, mineral wool, or cellulose (for R-30). This configuration has 44% of the total R-value coming from the spray foam, so it's safe.
Hi, this is Greg again,
Please consider this part question, part friendly suggestion.
While there is a lot of attention paid in this article, and on GBA in general, to protect the roof sheathing from moisture damage, I found very little information on this site regarding anti-fungal treatment of the sheathing material. There are time tested non-toxic borate treatments, both commercially available (e.g. Timbor), and cheap home-made versions. They are based on fungicide and insecticide properties of borates (boric acid salts, and boric acid as well). There is a link to several several homebrew formulas here: https://www.greenbuildingadvisor.com/question/home-brew-wood-preservative. The idea is mixing and cooking a solution of borax (sodium tetraborate decahydrate) and boric acid to yield sodium octaborate tetrahydrate, another borate salt that contains higher % of borate by weight than either borax or boric acid, so it is a stronger fungicide (it is boric acid < borax < Na octaborate by borate content). Is is also suggested to make an octaborate solution in a glycol (e.g. ethylene or propylene glycol) for better wood penetration and glycols' own fungicide and pesticide properties. I personally would use non-toxic propylene glycol instead of highly toxic ethylene glycol that is used in commercially available Boracare. 20 Mule Team Borax and boric acid powders are super cheap and widely available. Propylene glycol is relatively inexpensive on ebay. But even if one is hesitant to use commercial or homebrew formulas, simply making a borax solution in water and painting or spraying it on the sheathing surface and letting it dry should be way better than nothing for preventing any accidental rot. This is when I believe that very little money and effort should go a long way.
In my case, I was advised to apply closed-cell spray foam to the interior side of the roof sheathing of non-ventable rafter bays in my old house cathedral ceiling. Directly on top of the plywood sheathing, there is asphalt felt and two layers of shingles, so it has no adequate drying potential to either side in case of a roof leak. So I see the borate treatment before applying closed-cell foam as a very important step to ensure that the plywood stays intact.
I would love hear from anyone who might have experimented with treating roof sheathing or other structural components with borates and/or glycols. What are your results? I would abstain from copper-based preservatives as they are toxic and potentially corrosive for the nails.
Here is a link to another useful article on the topic: https://www.greenbuildingadvisor.com/article/reconsidering-rot-resistant-framing-material
As I said, there is very little discussion on the topic on this site. I believe it should deserve much more attention.
Thanks!
Greg
Greg,
The only discussion around treatment in the context of roof sheathing I can remember was in this paper about mold in PNW roofs. The conclusion appeared to be that they haven't found an effective product to discourage growth in roof assemblies.
http://rdh.com/wp-content/uploads/2015/03/The-Problem-with-Ventilated-Attics-RCI-March-2015-Nov-5-2014-For-Printing.pdf
Malcolm,
Thank you, it is an interesting article. The authors note that mold growth could be a side effect of better thermal decoupling of ventilated attics, so the roofs get colder as a result. Speaking of treatments they studied, the results vary from bad to pretty good. Here are their findings:
"In regard to the efficacy of the fungal treatments, in general, the bleach and Thompson’s
WaterSeal® have to this point been inadequate in preventing fungal growth. In some cases, it as if the antifungal properties of bleach have primed the surface for a new wave of fungal
colonization by eliminating the established fungi, resulting in more severe fungal growth than the adjacent areas. The Boracol 20-2BD, Kilz® Paint, Copper Napthenate, and Zinc Napthenate seem to provide good resistance to fungal growth at this early stage. It is also obvious that products with mouldicides (e.g., Boracol 20-2BD and Kilz®paint) perform better than wood preservatives primarily designed to stop (Copper and Zinc Napthenate). Nonetheless, longer-term field studies are required to ascertain whether repeated application is required to maintain the level of fungal resistance. "
BTW Boracol 20-2 BD that they mention is 20% solutiuon of disodium octaborate tetrahydrate in propylene glycol with 1% added moldicide, and it shows excellent results, at least for this short-term study. Kilz paint seem to work just as well, but I'm sure it can't penetrate the material nearly as deep, and it probably acts as a vapor retarder as well. So if the moisture is caused by a roof leak, Boracol should be a better bet.
Thanks again!
Greg
Greg,
As I understand it the downside of borate treatment is that it leaches out when the material is wetted. I've had good luck remediating moldy areas with Concrobium, which encapsulates the surface, but don't know if it stops fresh infestation.
The approach I try to take is to specify safe enough assemblies that they don't need to rely on treatment to resist mold - at least that what I hope I do.
Malcolm,
Thanks so much for your feedback. I actually just treated my sheathing surface this morning with a solutiuon of borax in propylene glycol/water (had to heat it on a stove, otherwise it does not dissolve very well). But now that I looked up Concrobium, it might be a good idea to get some at HD and spray a bit right on top. It contains some TSP and Na carbonate. It is a bit more alkaline (pH 11.1 - 11.5 vs. 9.3 for borax), so all in all the two appear to be compatible. Concrobium is being marketed for mold prevention in addition to remediation.
I wonder if it is high pH that makes Concrobium effective. A simple search about mold and pH brought me to this page: http://pacificmoldprevention.com/-raise-the-ph.html. So I wonder if I could just spray some TSP solution instead (pH 12 at 1%; I have it at home). Have you ever tried that?
Thank you again!
Greg
Greg,
No I haven't tried TSP. The two situations where Concrobium worked for me were a table were reoccurring mold on the unfinished underside, and an amazingly over-filled walk-in closet with many vintage clothes, some were showing stains. For the closet I just sprayed it into a fan and let it dissipate in the air. I was sceptical, but it worked.
I wonder if the borate might not be enough? If it only leaches out when wet, how much is going to leach out of damp sheathing? Maybe not much at all?
Malcolm,
I really hope borate will be enough considering the conditions. My only concern originated from the study you originally mentioned. The result table shows that on northern side of the roof, Boracol 20-2 (essentially same treatment I used) performed somewhat worse than Boracol 20-2BD (with 1% added organic ammonium salt - also alkaline by definition - as biocide; I checked the MSDS). I know the evidence is very limited. At the same time, using high pH treatment to kill microorganisms looks like an established technique. I should've thought about it before. I will look closer into it before I decide whether to do anything extra.
I really appreciate your help!
Greg
Dear Martin & Others,
Thanks for the information, I'm wondering if anyone has any input on my roof construction for a house going up this spring (in Ashland OR).
I have a simple gable roof with a shed dormer on one side. My roof construction is 2x12 24 OC which I intend to insulate with loose-fill wool. I may fur out the inside of the rafters to get another 1-2 inches of insulation, especially if I vent the rafter cavities with baffles. On the inside I'm intending to put intello plus as an air barrier and to retain the wool, inside of which I'd have T&G.
Within the rafter cavities I could do 1-2" baffles, I'm certainly swayed by getting the full 2" if it doesn't compromise my R-value too much.
For roof sheathing I was going to simply do 3/4 CDX but your article is making me consider the possibility of a particleboard (Huber Advantech?).
My first question is, if this particle board is taped or sealed at the seams does this constitute an air barrier for the exterior side of the infill insulation, preventing wind washing? Or would I need an air barrier in addition to this, perhaps something vapor permeable such as solitex mento. And would this decision be affected by the choice between plywood or particleboard?
My roofing will be standing seam metal, and I was thinking of venting the underside of the metal for a cold roof, with vertical battens and horizontal skip sheathing nailers. I'm not concerned with ice damming/snow build up on the roof as we get pretty minimal snow here, but more with strategies for a cooler roof in summer.
It's sounding overbuilt and excessive so I thought I'd ask for some input! If you have a wool infill insulation, and you can sheathe it with something that has some vapor permeability (particleboard?) would it be effective just to vent the exterior surface of the sheathing, between the metal roof and the sheathing? And in that scenario, what type of membrane would be required outside the sheathing?
Many thanks for any input, each time I think I've got a handle on the requirements a little detail comes up that makes me reconsider something else...
R. Kirkby,
Q. "For roof sheathing I was going to simply do 3/4 CDX but your article is making me consider the possibility of a particleboard (Huber Advantech?)"
A. Huber Advantech is not particleboard. It is oriented strandboard (OSB). Plywood (for example, CDX plywood) and Huber Advantech OSB are equally good choices.
Q. "If this particle board [I think you mean OSB sheathing] is taped or sealed at the seams does this constitute an air barrier for the exterior side of the infill insulation, preventing wind washing?"
A. Taped OSB is a good air barrier -- many builders use Zip sheathing for this purpose. But the location of the air barrier is wrong for a vented assembly. You need an air barrier directly above the fluffy insulation, which means that your ventilation baffles need to be airtight. For more information, see "Site-Built Ventilation Baffles for Roofs."
Q. "Would I need an air barrier in addition to this, perhaps something vapor-permeable such as Solitex Mento?"
A. Solitex Mento might work, if you can figure out how to use it as a ventilation baffle. However, I think that a cloth membrane fails the "buildability" test.
Q. "Would this decision be affected by the choice between plywood or particleboard?"
A. Again, no one is suggesting the use of particleboard. The choice between plywood and OSB has nothing to do with the need for an air barrier directly above your fluffy insulation.
Q. "If you have a wool infill insulation, and you can sheathe it with something that has some vapor permeability (particleboard?)?"
A. You may be thinking of fiberboard -- not particleboard. Fiberboard might work, as long as it is approved by your engineer.
Q. "Would it be effective just to vent the exterior surface of the sheathing, between the metal roof and the sheathing?"
A. Yes, some builders have done this, using either structural fiberboard (with approval of an engineer), board sheathing (with approval of your code enforcement official), or even Solitex Mento (assuming you can get approval from an engineer and you solve the buildability problems).
Q. "What type of membrane would be required outside the sheathing?"
A. Building codes require the installation of roofing underlayment. A few manufacturers sell vapor-permeable roofing underlayment; for more information, see "Synthetic Roofing Underlayments."
Hi Martin,
Thanks very much for your response, I had reread your article as well and saw I somehow missed the point about venting above the sheathing.
For maximizing insulation and buildability, as far as I can tell, I like the following method based on your suggestions, and would be grateful to hear what you think is the weak point in this setup:
Intello plus air barrier on the inside of 2x12 rafters infilled with loose wool, with no ventilation chutes, for a full 11+ inches of wool, theoretically over R-45. Sheathed with fiberboard (pending engineering approval, if you have any suggestions for the best balance of cost/structure/health I'd be glad to hear it) for the higher vapor perm, and then skinned with Solitex mento. On top of the underlayment, 2x4 vertical furring to create a 1 1/2" ventilation channel, then horizontal skip sheathing for nailers for a metal standing seam roof, for which I'd prioritize high reflectivity for summer cooling in my moderate, probably warming climate. Eave venting would be something like coravent tucked behind the eave flashing, since a continuous soffit vent would have no direct path to the ventilation channels.
Many thanks! Ryan
Ryan,
Your approach will work. You don't need the Solitex Mento -- a vapor-permeable synthetic roof sheathing will work as your air barrier, as long as the seams are taped. Or you could skip the roofing underlayment, if your local building inspector will approve Solitex Mento as a roofing underlayment. (I don't know if the European manufacturer of Solitex Mento has obtained code approval for the use of their product as a roofing underlayment -- but if the manufacturer has, then that's probably all you need.)
Thank you, I was looking at the Advantech Zip System roof panels which have a built in water resistive barrier that has a permeability rating of 12-16 but not much info seems to be available on perm ratings for either of those Huber products themselves - ZIP system or Advantech Sheathing.
Based on your experience would you say those products would be better off being ventilated along the outside (outside of the WRB/air barrier) vs inside the rafter channels with baffles? Since the wool itself does not need or benefit from those ventilation baffles I'm sure leaning towards venting the outside surface of the sheathing, and just want to identify best products for that. I'm still trying to get a grip on how important, in a roof construction like mine, the vapor permeability of that sheathing layer actually is. Does that influence the ability of the sheathing itself to dry out, or only facilitate outward drying of whatever is underneath?
Thanks again - Ryan
Ryan,
Q. "Not much info seems to be available on perm ratings for either of those Huber products themselves - ZIP system or Advantech Sheathing."
A. Zip System sheathing has a permeance of 2 t0 3 perms, and I'm fairly sure that the permeance of Advantech is about the same. It's not that different from other brands of OSB.
Q. "Would you say those products would be better off being ventilated along the outside (outside of the WRB/air barrier) vs inside the rafter channels with baffles?"
A. No. If you plan to install fluffy (air-permeable) insulation, the best location for the ventilation channel is between the top of the insulation layer and the underside of the roof sheathing. That way, the moving air can carry away the moisture that accumulates on the underside of the roof sheathing.
I'm not sure what type of insulation you plan to use. You call it "loose wool." What does that mean? Is this sheep's wool? If so, that's an unusual approach.
Q. "Since the wool itself does not need or benefit from those ventilation baffles I'm sure leaning towards venting the outside surface of the sheathing."
A. If the underside of your roof sheathing gets wet, and the wool insulation gets wet, that's a problem. So a ventilation channel between the top of the insulation and the underside of the roof sheathing is, indeed, a benefit. I'm not sure why you think damp wool is not a problem. It is.
The origin of the problematic moisture is interior air. It enters the roof assembly by tiny, undiscovered leaks, driven by the stack effect, which is a powerful mover of air.
If you choose to install fiberboard sheathing, the moisture can diffuse through the fibeboard and dry to the exterior -- but only if you have a ventilation channel under the roofing to help remove the moisture.
Thanks Martin -
Just to clarify yes I am talking about infilling the rafter cavities with loose fill sheep's wool (treated w/ boric acid). Since it does have some significant hygroscopic capacity I thought it would help protect the sheathing from that side.
I like the idea of ventilating the outside in order to maximize the rafter insulation space without furring it out further, though I can do that, and also to avoid having to air seal the ventilation chutes between rafters. The ZIP system panels with their decent perm rating and air sealing capacity with taping seemed like a nice possible solution to still encourage that outward drying capacity, with the interior well air-sealed.
I also like the exterior venting (outside the roof sheathing) as it circumvents a couple roof geometry problems where rafter channels would be blocked (two skylights, etc.).
It sounds like extra cost aside it would be ideal to vent rafter channels and leave a ventilation space between metal panels and sheathing?
Thanks for your clarifications - admittedly I am not knowledgable about the tradeoffs of these options yet but your articles and responses have been very helpful.
-Ryan
Ryan,
You note that the Zip System panels have a "decent perm rating." I'm not sure what is considered "decent" -- we usually speak about perm ratings being relatively high or relatively low.
Zip System sheathing, like ordinary OSB, isn't very vapor-permeable -- especially when compared to fiberboard or a vapor-permeable European membrane. Drying through OSB or Zip System sheathing is quite slow -- which is why the ventilation channel belongs under the Zip sheathing, or why you need to specify fiberboard (if you want your ventilation channel to be above the roof sheathing).
For more information, see this article: "All About Vapor Diffusion."
Is it possible to construct a vaulted ceiling with exposed beams on a gable roof with rigid foam on top of structural 2x6 T&G decking...sheathing (probably radiant with an air gap) on the foam and a metal roof. I live in coastal SC and heating isn't that big of a concern but moisture is. I'm not having much luck finding info other than faux installation and scissor type truss systems
FourBoles,
The big problem with structural T&G sheathing is it usually extends to the overhangs, and is very difficult (impossible?) to air-seal at the exterior walls.
Four,
Q. "Is it possible to construct a vaulted ceiling with exposed beams on a gable roof with rigid foam on top of structural 2x6 T&G decking...sheathing (probably radiant with an air gap) on the foam and a metal roof?"
A. Yes. If you go this route, the most critical detail is to include a bulletproof air barrier above the tongue-and-groove ceiling boards (the sheathing boards). For more information on this approach, see this article: "How to Install Rigid Foam On Top of Roof Sheathing."
Q. "Heating isn't that big of a concern but moisture is."
A. Moisture is a concern in all climates. Even though you write that "heating isn't that big of a concern," you have to follow code requirements for roof assembly R-value for new construction. You are in Climate Zone 3, where most codes require ceiling or roof insulation to have a minimum R-value of R-38.
Martin - Thanks for the great articles and comments. I'm building an addition that includes a dormer roof with rafters dead-ending in a valley, which I guess can be described as a cathedral ceiling for this discussion. Although there are some products out there which would allow me vent air in above the rafters (Valley Vents or Rafter Vents from DCI/IPS), and then vent that air out through ridge vents, I think I've decided from reading your articles to go the unvented route for this portion of my roof only (the rest of roof will be standard vented via soffit inputs, up through baffles to a ridge vent). I'll probably just buy one of the closed-cell foam DIY kits since it's too small of an area to hire someone. Here's my question, though: The valley rafters are 2x8s and the other roof rafters are 2x6 (architect drew it this way; don't ask me), which means the valley rafters extend below the level of the other roof rafters, which means if I dry-wall the bottom of the 2x6s, I'd then have to go down and around the valley rafters to head up the cathedral ceiling of the dormer, which would be an awful sight. So, one possible solution is to fill the entire cavities of the 2x6 rater bays with closed-cell (5.5"), and then put 1.5-2" of rigid foam boards across the all of the 2x6 rafters to even up with the level of the 2x8 valleys. Aside from the positive effect of adding some R-value, are there any negative side-effects (vapor, drying, etc.)?
I'm in the hot/humid area of zone 3.
Just realized I need to edit this explanation slightly: Only the dormer/cathedral section of roof will be filled with closed-cell foam and then the rigid board. The rest would be fiberglass bats and then the rigid board. So, really two different situations where I need to know if the rigid board is a bad idea.
Brian,
A continuous layer of interior rigid foam is OK. It won't cause any problems -- either with rafter bays filled with closed-cell spray foam, or with rafter bays filled with fiberglass batts with ventilation baffles above the batts.
One note: If your roof has valleys, remember that both sides of the valley are problematic when it comes to ventilating rafter bays. The dormer side of the valley can be unvented -- but how will you introduce ventilation air into the bottoms of the rafter bays on the other side of the valley?
Yes, that's true. I didn't explain that fully enough. Both sides of valleys will need spray foam. Only the rafters with straight shots from soffit to a vent will get fiberglass. Thanks for your input
Martin,
Thanks for your posts- they have been very informative. We are planning to replace a 3/12 through-fastened metal roof in Climate zone 5b with a standing-seam metal roof. The current metal roof was probably installed in the 80’s and, after pulling a panel, it appears to have been installed on top of the original tar-and-gravel built up roof, with 2” of EPS foam in between. To complicate matters, one side of the house has a vented attic, but the other side has an unvented and not particularly well-sealed cathedral ceiling. We don’t have any major concerns on the vented attic side, but we are having a hard time deciding what to do about the cathedral ceiling. At present, the stack-up appears to be the following from the inside-out:
3/8” texture 1-11 plywood, 4” groove (this is the visible ceiling)
3.5” BATT
1/2” plywood decking
built-up roof (or some portion thereof)
2” EPS foam
current through-fastened metal roof
We have gotten numerous re-roofing bids. One roofing contractor wants to remove the foam completely along with the tar and gravel roof and then install the new metal directly onto the decking. We do not like this idea because it would leave us with an R=11 situation and potential condensation issues on the roof deck. The roofer we are working with now proposed to keep the 2” foam in place and install the new standing seam on top using bearing plates. While this is a possibility, it preserves the current R=20 insulation (R-11 under decking and R=9 above deck). Should we be concerned about potential condensation given the fact that the 1-11 plywood ceiling leaks air through several holes where electrical boxes and cords have been (and probably between joints in the plywood as well), keeping in mind that our winter climate is very dry (the current humidity is only 20% in the great-room). The humidity does rise in the summer during monsoon season, but then we are in a situation where it is generally cooler inside than outside due to AC.
We did explore a potential venting solution that would involve sistering 2x8’s up against the current 2x4’s in the ceiling cavity that are parallel to the ridge line, cutting 1” holes for ventilation, replacing the BATT with 6.6” polyiso, and installing soffit and ridge vents, but given that there is not a good air barrier on the interior plywood, it sounds like this might cause more problems than it solves, and would also result in an uneven roof line that requires parapets, etc.
Reading your summaries, I am wondering if the following stack-up would be an acceptable solution:
3/8” texture 1-11 plywood, 4” groove (this is the visible ceiling)
3.5” BATT
1/2” plywood decking
built-up roof (or some portion thereof)
6” EPS to bring outer R-value to 27.6 and total R-value to 38, and to push the dew-point outside of the sheathing.
Several questions:
1) If we leave the old roof in place, the foam will not be in direct contact with the roof sheathing. Is this a problem? There would also be no air barrier immediately above the roof sheathing, unless the old built-up-roof counts as such a barrier. The roofers are concerned that attempting to remove the old built-up roof will destroy the decking as well, but if absolutely necessary, we could have them remove the old roof over the cathedral ceiling and put down all-new sheathing.
2) The roofers have proposed to apply Ice and Water Shield on top of the outer layer of foam over the entire roof. In this “dry-to-the-interior” solution, is this the right place for the underlayment? Like you, I am also nervous about putting a vapor barrier on top of this assembly, but it sounds like the standing seam will serve as a vapor barrier in any case, so perhaps this is not concerning? Furthermore, will the lack of barrier (aside from the original roof) directly over the sheathing cause any condensation within the EPS layers to simply leak downwards into the sheathing?
3) They are also planning to attach the standing seam directly to the foam using bearing plates like those shown on page 12 of https://www.buildsite.com/pdf/owenscorning/Owens-Corning-FOAMULAR-XPS-Roof-Insulation-for-Commercial-Buildings-Summary-Brochure-1235135.pdf. Does this sound reasonable, or would we need to use either nail-base or have another layer of decking and/or purlins installed.
4) If we do add an additional 4” of foam over the cathedral ceiling sections of the house, we will need to do something similar over the remaining roof to keep the roof-line even and avoid parapets/etc. It seems pretty wasteful to do this over vented attic space. Would it be better to push for some kind of framing solution elsewhere? I suspect that would be difficult without removing the built-up roof everywhere. An alternative would be to remove the 2” EPS over the cathedral ceiling and put down 4” total of polyiso or XPS (and and additional 2” EPS elsewhere), but it sounds from your posts like polyiso and XPS are not the best choices in cold climates (and for long-term performance).
Thanks for any advice or recommendations you can give!
Perplexed,
Since you have a very leaky ceiling (the T1-11) topped by a pathetically thin layer of fiberglass insulation (the 3.5-inch-thick batts), and since you don't intend to do any interior improvements, you should simply assume, from a thermal performance perspective, that there is no insulation under your old roofing. For all intents and purposes, the T1-11 and the fiberglass batts are worthless.
(By the way, the word "batt" is a common noun, like "chair" or "table." It doesn't need to be written in all caps -- it isn't an abbreviation or acronym.)
Q. "If we leave the old roof in place, the foam will not be in direct contact with the roof sheathing. Is this a problem?"
A. No.
Q. "There would also be no air barrier immediately above the roof sheathing, unless the old built-up-roof counts as such a barrier."
A. The built-up roofing is an air barrier.
Q. "The roofers have proposed to apply Ice and Water Shield on top of the outer layer of foam over the entire roof. In this 'dry-to-the-interior' solution, is this the right place for the underlayment?"
A. The Ice & Water Shield in this location isn't really underlayment. It is an additional air barrier. There is nothing wrong with installing Ice & Water Shield in this location.
Q. "Like you, I am also nervous about putting a vapor barrier on top of this assembly, but it sounds like the standing seam will serve as a vapor barrier in any case, so perhaps this is not concerning?"
A. The Ice & Water Shield isn't at the top of the assembly -- it is near the bottom of the assembly, since there will be 6 inches of rigid foam on the exterior side of the Ice & Water Shield. You're right that standing-seam metal roofing is a vapor barrier.
Q. "Will the lack of barrier (aside from the original roof) directly over the sheathing cause any condensation within the EPS layers to simply leak downwards into the sheathing?"
A. Condensation happens on cold surfaces. There won't be any cold surfaces under the Ice & Water Shield, so I don't know why you think condensation is possible.
Q. "They are also planning to attach the standing seam directly to the foam using bearing plates like those shown on page 12 of https://www.buildsite.com/pdf/owenscorning/Owens-Corning-FOAMULAR-XPS-Roof-Insulation-for-Commercial-Buildings-Summary-Brochure-1235135.pdf. Does this sound reasonable?"
A. I have reproduced the Owens Corning image below. If the manufacturer of the roofing approves this detail, I have no reason to doubt that it will work.
Q. "If we do add an additional 4 inches of foam over the cathedral ceiling sections of the house, we will need to do something similar over the remaining roof to keep the roof-line even and avoid parapets/etc. It seems pretty wasteful to do this over vented attic space. Would it be better to push for some kind of framing solution elsewhere?"
A. I don't know where "elsewhere" is, and I don't know what you mean when you refer to "some kind of framing solution." Please elaborate.
Q. "An alternative would be to remove the 2 inches of EPS over the cathedral ceiling and put down 4 inches total of polyiso or XPS (and and additional 2 inches of EPS elsewhere), but it sounds from your posts like polyiso and XPS are not the best choices in cold climates (and for long-term performance)."
A. The thermal performance of polyiso and XPS are fine, even in cold climates, as long as you assume the right R-value per inch. Polyiso in cold weather performs at about R-5 per inch. XPS will gradually lose R-value over the next 40 or 50 years, but the degradation in thermal performance isn't huge, and the XPS will never drop below about R-4 per inch. Note, however, that green builders avoid the use of XPS because it it manufactured with a blowing agent that has a high global warming potential.
For more information on these issues, see "Choosing Rigid Foam."
Martin,
Thanks for the quick response. A few clarifications:
- The roofer's current plan includes only the already-present 2" of EPS over the original built-up roof. In this scenario, they are planning to put the ice and water shield on top of the EPS (so on the cold side, directly beneath the new standing-seam roof). The reason for this is that the old built up roof doesn't provide a smooth surface to which ice and water shield could be adhered. I'm concerned that if they do this, any condensation that develops in the thin EPS layer will make it back down through the old built up roof and into the sheathing.
If we go with 6" EPS (or 4" polyiso), they could presumably adhere the ice and water shield onto the exterior surface of the innermost layer of foam, but depending on the amount of foam, it is again possible that the ice and water shield ends up outside the dew point. To adhere ice and water shield below the foam entirely, it sounds like we will need to strip off all of the old built-up roofing and potentially replace all of the sheathing as well, simply to give ourselves a smooth surface to work with underneath the foam layers. Alternatively, we could forego a self-adhering layer and go with a synthetic underlayment attached directly to the old built-up roof underneath all layers of foam.
- By elsewhere, I meant the half of the house with ventilated attic, as well as the unheated garage, which has cathedral ceilings as well with interior drywall. At the moment, there appears to be 2" foam over the entire original roof, presumably to keep the roof line even at the ridge. If we increase the amount of foam over the conditioned cathedral ceiling, we will need to do something to raise the roof level everywhere else as well, even though added insulation will provide no benefit.
- If we can't take advantage of any of the meager insulation under the roof, would we still want to aim for R=20 over the roof, or would we need to increase this to R=38? I'm less concerned about strictly bringing the roof up to current code than I am about ensuring we don't create a moisture situation, albeit in our dry winter climate.
Thanks again!
Perplexed owner,
The best approach from a thermal performance perspective is obviously to cover the entire roof with 6 inches of additional rigid foam.
If your budget won't allow that, you may have to make compromises. But now is your chance to get it right -- the next chance won't come around again for decades. Who wants an R-8 or R-10 roof?
Martin & others,
Can you give any input on what if any technical difference there is in these two scenarios for roof construction on a cathedral ceiling/gable roof:
1) Air barrier, 2x12 rafters (filled with dense pack cellulose or other fibrous insulation) with site-built 3/8" plywood baffles leaving a 1 1/2" ventilation space, 3/4" plywood, synthetic underlayment, standing seam metal roof
vs.
2) Air barrier, 2x12 rafters (filled with dense pack cellulose or other fibrous insulation) w/ NO vent channel, 1/2" plywood, 2" vertical furring strips, 3/4" plywood, synthetic underlayment, standing seam metal roof
Despite the fact that the first option has a vent channel between the rafters, overall they both have fibrous insulation in contact with plywood that is not the exterior sheathing, and a ventilation channel between that plywood and the (most) exterior sheathing. Is there any technical difference in those two constructions, or other reasons to prefer one over the other?
If there was some strong reason to prefer scenario #1 then the inside of the rafters could be furred out for increased insulation.
Thanks for any feedback - Ryan
Ryan,
In the scenario with the conventional ventilation channels under the lowest level of roof sheathing, the rafters have some contact with the ventilation air space. That means that the moving ventilation air can remove moisture from the top of the ventilation baffles as well as the sides of the rafters (at least the upper 1.5 inch of the rafters). This opportunity to remove moisture from the sides of the rafters is missing when the ventilation channels are above the roof sheathing.
Moreover, moisture will migrate through the 3/8-inch plywood ventilation baffles more easily than it will migrate through 1/2-inch plywood roof sheathing.
We are building a home in Salida co (zone 6). The unvented cathedral roof is built as follows: plywood sheathing, ice and water, 4" polyiso/OSB nail base, felt and then standing seam. Rafters are 12" I-joists. We were planing on R-36 batts then T&G for the ceiling which gets us well over the roof code. The inspector now wants 2" of closed cell spray foam to the interior sheathing for moisture control. This will be considerable increased cost. It looks like we are 1 R short of the 25 you mention for the code in zone 6 but that was not brought up by the inspector. I can't seem to find any code for this situation. I'm hoping to change his mind, any ammunition or is he right? Thanks
Rooster,
You're in Climate Zone 6. The code section that applies to your case (in the International Residential Code) is Table R806.5 (see image below).
If you want to read this code section in detail, here is the link: 2015 IRC - Roof and ceiling construction.
The code calls for a minimum of R-25 of exterior rigid foam in your zone (based on the assumption that your total roof assembly R-value will be R-49).
I'm not sure what R-value you are assuming for your 4 inches of polyiso, but some building inspectors might go along with your theory that polyiso has an R-value of R-6.25 per inch, which means that some building inspectors might go along with your plan.
There are two problems, however.
1. Problem number one is that polyiso performs at about R-5 per inch at cold temperatures -- sometimes only R-4 per inch -- so a more conservative analysis would be that your 4 inches of polyiso has an R-value of about R-20, not R-25.
2. Problem number two is that you have too much fluffy insulation, making your roof assembly riskier from a condensation perspective. You are planning a roof assembly with a total R-value of about R-56, with about R-20 of rigid foam -- meaning that you have only 36% of your insulation in the form of exterior rigid foam instead of the needed minimum of 51%. For more information on where this minimum of 51% comes from, see this article: "Combining Exterior Rigid Foam With Fluffy Insulation."
So your building inspector is right.
Is there a general consensus for how to create an underside air barrier on a vented cathedral scissor truss roof? Solitex Mento, taped seams, and strapping for electrical? More affordable option?
Morgan,
By far the most common approach is to use gypsum drywall as the air barrier. For more information, see "Insulating Scissors Trusses."
Martin, thanks for the reply. But ideally you'd have the air barrier on the underside of trusses, then strapping, then your drywall to allow for elec and non-puncturing LED puck lights. In this case I assume it would be a proprietary membrane or taped osb correct?
Morgan,
If you have your heart set on a European air-barrier membrane, go ahead and buy one. But if you are going to install drywall anyway, why not just use the drywall as your interior air barrier?
If you follow my advice and use the drywall as your interior air barrier, you would need to (a) air seal around penetrations like electrical boxes -- one option is to purchase airtight electrical boxes, and (b) come up with a detail to make sure that the ceiling air barrier is continuous with the wall air barrier. (Here is a link to an article showing a typical detail for that: "A Practical Air-Sealing Sequence." Since the detail drawing doesn't show a scissors truss, you'd have to modify the detail by using something like peel-and-stick flashing rather than plywood for this detail.)
Martin, you said in the article, "Builders solve this problem by furring down or scabbing on additional framing below the rafters to deepen the rafter bays. Another technique is to add a layer of cross-hatched 2x4s, 16 inches on center, installed beneath the rafters." Could you give a bit more info. on what you mean by cross-hatched 2x4s?
I'm coming up with a plan to insulate my walk-in attic with a cathedral ceiling (it'll be conditioned and finished into a living space), and I was considering installing 2x4s on the interior side of my 2x10 rafters--flat and perpendicular to the direction of the rafters to create truss bracing as recommended by FEMA for hurricane resistance (https://www.fema.gov/media-library-data/20130726-1505-20490-3483/agstwnd.pdf). Is that the same thing that you meant by cross-hatched, except standing the 2x4s on edge? Then perhaps I can do that and kill 2 birds with 1 stone and create cross-bracing plus more space for insulation?
Matt,
The cross-hatched 2x4s I was talking about are installed either 16 inches on center or 24 inches on center, on the interior side of the rafters. It's similar to the Mooney wall approach, shown below -- but instead of the wall framing, we're talking about the roof framing.
Hi Martin,
I'm a DIYer that has spent the past couple of months reading a good share of the articles and comments on the site. At times, I feel like I understand some best practices, and at others, I feel lost again. I'm preparing to build an unvented vaulted roof assembly in zone 5, and I'm trying to find the best way to get the right ratio of rigid foam above deck to fluffy insulation between the rafters, to meet or exceed code (now and if/when the rigid insulation loses R-value).
In my shed roof design, I will either be going with 2x10 or 2x12 rafters. I would like to install 4" of foam max between two layers of OSB, given my reading of how difficult it can be to install when you get over 4". I'll follow the articles regarding taping seams and underlayment. I'll be finishing with asphalt shingles.
My questions are as follows:
(1) Is it okay to use spray foam beneath the sheathing before adding R30 batts? This would insure the right foam to fluffy ratio for now and once the foam's R-value degrades. I get lost in the articles on here. Is this a problematic setup for my sheathing?
(2) Does it matter whether the R30 batts are faced or unfaced? I'll be adding 1/2" gypsum to the rafters.
(3) If going with 2x12's, which one of the local lumber suppliers advises, should I be concerned about the air gap left in the rafter bays? According to the IRC, it appears that 2x10's in Doug Fir SS would more than handle the 15' span in my design with an even higher snow load, so I'm not too worried, but in the words of the local lumber supplier, "This is one area it's not a bad idea to over-build." It just seems it would be easier to work out all of the details with 2 fewer inches of wood up there.
Any advice you have to offer is greatly appreciated.
Thanks for your patience,
Chris
Chris,
Q. "Is it okay to use spray foam beneath the sheathing before adding R30 batts? This would insure the right foam to fluffy ratio for now and once the foam's R-value degrades."
A. Yes, that's OK -- people do it all the time. However, this approach sandwiches the roof sheathing between two impermeable layers, so you need to make sure that the sheathing is dry on the day that the spray foam is installed. Some builders avoid this approach because of the sandwiching issue. It's your choice -- I think it isn't ideal, but it usually works.
Q. "Does it matter whether the R-30 batts are faced or unfaced? I'll be adding 1/2" gypsum to the rafters."
A. No, it doesn't matter. The kraft facing is unnecessary in this assembly, but the kraft facing won't do any harm.
Q. "If going with 2x12's, which one of the local lumber suppliers advises, should I be concerned about the air gap left in the rafter bays?"
A. The air gap isn't ideal. The best approach is to fill the rafter bays completely with fluffy insulation (assuming that approach doesn't mess up your ratio of foam-to-fluffy). If you do end up with an air gap, you need to find a way to make sure that the fluffy insulation is in direct contact with the cured spray foam -- and that the fluffy insulation doesn't slump away.
Q. "According to the IRC, it appears that 2x10s in Doug Fir SS would more than handle the 15' span in my design with an even higher snow load, so I'm not too worried, but in the words of the local lumber supplier, "This is one area it's not a bad idea to over-build." It just seems it would be easier to work out all of the details with 2 fewer inches of wood up there. "
A. So specify the 2x10s.
Hello Mr. Holladay. Great thread on insulated cathedral ceilings! I live in Portland, OR and am designing a 1500sq ft home addition with a simple gabled roof. The home is singled sided ICF (Nudura One Series) construction to the eaves and rake. The roof will be stick framed 2x10, possibly 2x12 rafters, 24" O.C. I would like to do a 'cold roof' 'over-roof venting' option as crudely depicted below. My plan is to fill the rafter bays with mineral wool batts up to the bottom of the plywood sheathing, then tar paper and sleepers on top of the sheathing eventually being covered with strapping and metal roofing. The skylights as shown in framing pix will probably be jettisoned to further simplify construction.
My problem is I find few references on how to detail a cold roof cathedral ceiling with venting channels on top of the sheathing. According to comments in #191 and #323 postings, venting channels on top of sheathing is fine if building officials approve it. In #323 it is mentioned to use fiberboard as sheathing if you are going to do venting channels on top of sheathing. Using fiberboard for roof sheathing does not sound wise to me and I prefer plywood which according to Joe, can hold up to wetting/drying cycles. Plus the roof sheathing needs to be structural 3/4" plywood according to engineer.
My building officials are very supportive of my project. They suggested treating the roof design as a modified SIP panel construction. Evidently it has been found SIPs have tendency to collect moisture in the ridge areas. They suggest cutting back the plywood sheathing along the ridge to let this moisture escape to the ridge vent. See attached sketch.
My building officials are encouraging me to supplement my building permit application with references on how to properly detail a cold roofed over-vented cathedral roof assembly. From my research, GBA and BSC are the leaders in understanding why roofs work and why they fail. I would deeply grateful to hear your opinion on how my roof design might perform and could be improved.
Thank you,
Roger Ellingson
Roger,
You can't have everything. If you use plywood, you have the advantage of strength (and a grade stamp) -- but you lose vapor-permeance.
There is a chance that moisture will accumulate on the underside of the roof sheathing during the winter. The more airtight your ceiling, the lower the chance. But damp roof sheathing above cathedral ceilings insulated with fluffy insulation is common.
Ideally, you would sheathe your roof with either fiberboard sheathing or ordinary boards (1x6s or 1x8s -- they could be rough-cut boards from a local mill, if your building inspector approves). Top that with a vapor-permeable synthetic roof underlayment -- be careful, because most synthetic roofing underlayments are vapor barriers -- and you'd have a good roof assembly.
I know this isn't the question you asked, so feel free to ignore, but why the vented over-roof?
Why not vent the cathedral ceiling under the sheathing the conventional way?
If you need more depth for insulation, you could extend the depth of your rafters with a strip of rigid insulation sandwiched between the bottom of the rafter and a strip of 3/4" plywood or 1x lumber (aka a Bonfiglioli strip). This has the added bonus of creating a thermal break for your rafters, so may be higher performance than the vented over-roof plan with no thermal break. (You could of course add the Bonfiglioli strips to your vented over-roof if you wanted as well).
Perhaps you have a specific reason why the over-roof is the way to go for you, but if not, consider conventional venting!
Thank you Brendan for asking why would I want to do a vented over roof. I am the homeowner acting as a designer, architect, and general contractor on this project so can use all the help I can get. From the get-go my project is not conventional, including the building materials and building methods!
Here is some of my reasoning on the over-vented roof design:
0. I am not necessarily trying to minimize construction labor costs related to the roof installation. I am the primary labor on the project and am more interested in craftsmanship and doing it right than getting it done quick. A vented over roof just makes more sense to me than a non-vented or under-sheathing-vented cathedral roof assembly.
1. Structural. I am hoping the engineer will approve the 2x4 on the flat sleepers for eave supports so I can have a simple, thin roof in cross section. I am trying to avoid extending the rafter tails to support the eaves as the visible roof sandwich gets too thick and heavy looking. No odd pork chops to deal with on the gable ends of eaves.
2. Insulation and air sealing at the roofline. For the record, my building will be entirely exposed concrete on the interior except for the ceiling, including the floors. The concrete mass is surrounded by the 4-5/8" EPS ICF foam. I am thinking to continue the peel and stick SBS rubberized asphalt membranes to the roofline, primarily for air barrier on the walls. By not have the rafter tails sticking out, it should be easier to seal the area up at the roof line along the two 70' sides. The remaining 45 feet of gable wall/roofline will have outlook rafters to seal around. The over-vented roof can vent at the fascia boards above the gutters. It does not require vents at the top of the wall at each rafter bay.
3. Complexity and installation quality. It appears to me installing baffled ventilation chutes under the sheathing looks difficult and prone to leakage. It looks to me like there are often cracks of considerable width between the baffles and sides of rafters. Some of the baffle types looks very flimsy and subject to pressure from below. Often there are gaps in the baffles. It is my understanding and I could be wrong that there would be less R overall R value to the assembly with baffles instead of filled cavity insulation. It seems you really need two inches of chute space to efficiently I thought I read somewhere.
4. Sheathing penetrations. If one goes conventional, wouldn't there be an array of fasteners protruding into the ventilation space? Might not matter but it would seem better to avoid puncturing the sheathing.
These are at least some of the reasons I am thinking vented over roof design. Thanks for asking and feel free to agree/disagree.
Thank you for the Bonfiglioli strips pointer. Looks interesting. I will check it out and report back.
https://www.finehomebuilding.com/membership/pdf/9750/021250059.pdf
Roger
Hello Martin and Brendan, Thank you for the comments on my roof assembly. They were very helpful. My new roof design includes both under and over sheathing venting. I upsized rafters to 2x12. I plan to line the tops of the vent chutes with 2x2 rigid foam and figure this will help reduce thermal bridging. According to this article, the thermal bridging of a 2x12 rafter is fairly minimal.
https://www.ecologices.com/savings-efficiency/frequently-asked-questions/how-significant-is-thermal-bridging-through-studs-and-rafters/
Under the sheathing: I am planning a 2" vent space under the 3/4" sheathing and 1.5" vent space over the sheathing. So under the sheathing is 2" vent channel, 2" rigid insulation panel, 7.25" mineral wool batt, smart vapor membrane, and ceiling sheathing.
Over the sheathing: roofing underlayment (not exactly sure what to use), 2x4 sleepers aligned with rafters, 1x3 strapping across the sleepers, metal seamed roofing.
Soffit venting via screens behind the fascia at eaves. Rake venting via screens behind the rake boards. Some type of ridge venting and screening to be determined depending on the metal roof material I use.
I plan to wrap the outside of the exterior rigid insulation with peel and stick membrane.
It looks like a great opportunity to vent the wall rainscreen up the rafter ventilation chute. It would simplify soffit and rake venting. Good idea?
Here are some sketches of my updated plans. Thank you for any comments.
Roger,
Your plans seem unnecessarily complicated to me. Why have two different layers of ventilation?
Also note:
1. Using rigid foam to make your ventilation baffles does nothing to address thermal bridging through the 2x12 rafters. The thermal bridge is still there. It is minor, as you point out, but it's still there, unaffected by the rigid foam baffles (which after all are between the rafters, not over or under the rafters).
2. If you go ahead with this plan and end up drilling big holes in your roof sheathing, you had better be meticulous when you air seal around the perimeter of each ventilation baffle. Those ventilation baffles are now the only top-side air barrier you've got.
Hello Martin, Thank you for your prompt reply and maintaining the discussion group. Great work! I appreciate your efforts very much.
I guess the reason I have two layers of ventilation is design creep? Initially, I was reluctant to consider venting under the sheathing, intuitively thinking over venting would be a better solution. I outlined some of my fears of under-sheathing venting above. But the more I study the roof venting science you have reported, I think I beginning to see the daylight! Thanks for your patience. I plan on revising my double venting scheme to simply under-sheathing venting chutes.
1. I figured lining the exposed rafters with above the ventilation chute rigid panels with rigid foam would help reduce thermal bridging through the rafters. less rafter would be exposed to venting channel temps. The rafter might end up with the reduced thermal bridging characteristic of a 2x14 was my thought.
2. If I get rid of the over-sheathing venting, I can dump those big holes. I do not fully understand the 'top-side air barrier' concern but maybe it does not matter now.
I want to thank you and Brendan for helping me get this roof figured out. I will post new design within a few days.
Roger
Roger,
When we talk about thermal bridging through a 2x12, we are talking about heat flow through the wood. The 2x12 measures 11.25 inches deep, so the R-value of a 2x12 rafter is:
11.25 inches * R-1.25/inch [the R-value per inch of softwood lumber] = R-14
If you stuff (for example) 10 inches of insulation between your rafters, that insulation might have the following R-value:
10 inches * R-3.7/inch = R-37
Since the rafters have a lower R-value than the insulation between the rafters, they are a weak link in the assembly. The rafters leak heat at a faster rate than the insulated bays between the rafters. This is the phenomenon called "thermal bridging."
Your ventilation baffles don't help address the thermal bridging. If your ventilation baffles are made (for example) out of R-8 rigid foam, you could add that R-8 to the R-37 (or whatever) calculated for your fluffy insulation. But that raises the R-value of the insulation in the bays -- it doesn't change the R-value of the rafters.
Hi Martin, Thank you once again for your prompt response and detailed explanation of the thermal bridging. You are the best! I think I understand the thermal bridging phenom and understand the difference between the rafter bay insulation and the rafter heat flow. The idea I was trying to explain was by lining the sides of the rafters with insulation underneath the sheathing, there would be a reduction in the amount of overall rafter heat loss due to 2" less exposure of the sides of the rafter. The exposed tops of the rafters would not be radiating heat into the vent channel. According to the reference I cited, "The rafter surface area influences heat transfer in the same manner as radiator fins." Regardless, I am not planning to worry about the thermal bridging problem in my roof assembly unless you think I should.
I simplified my roof assembly as attached below. The sleepers are gone and I plan on attaching the metal roofing directly to the sheathing. I have extended the rafter tails so support the eaves. It would seem I am nearing conventional!
But now I am back to having problems supporting the rake area. If I support the rake edge of the roof with vertical 2x4's in the typical ladder type arrangement, I lose vent channel space underneath the sheathing. Do you have any ideas how to keep the 'ladder filled' rafter bay up to R38 in my assembly when those outlookers are hanging down 3-4" below the sheathing? Vent sideways out the blocking between outlookers? Drill holes in the outlookers inside the vent channel? I plan on the venting screen on the wall side of the rake boards to ventilate under the rake edge of the roof. Maybe one should not worry about ventilating under the sheathing in this area? Again, I am stumped.
Thank you for your ongoing consideration. Roger
Roger,
You can drill some 1-inch-diameter holes in the 2x4 outriggers. That's an imperfect solution, but one that will work.
I'm in the process of having plans drawn for a new home and want to make sure that the roof system will function properly.
I'm in Central Florida. Climate Zone 2a. I plan to have a conditioned attic using open cell spray foam under the roof sheathing. (Unless there is a better option) I plan to use a high temp WIP like Carlisle 300ht with a standing seam metal roof. How do I execute this properly so that I dont have moisture issues in both my attic and sheathing? I've seen assemblies where they run 1x4's on diagonal and vent at both the bottom and top of the roof in order to allow for air flow between the metal roof and WIP. Is this best practice? Is there added benefit of running rigid insulation on top of the sheathing before the WIP and 1x4's?
It seems that most WIP's rated for high heat for metal roofs have very low perm ratings...is this an issue?
Any insite would be much appreciated as I am very new to this and just want to make sure it is executed correctly on my new home.
Thank you for your help,
Miles
Miles,
I wasn't familiar with the abbreviation "WIP," so I Googled it. It seems that it is an abbreviation referring to products in the "Water and Ice Protection" category -- what other people usually call peel-and-stick. (Presumably, you don't have ice dams in Florida, so I assume you are worried about hurricanes.)
We need to know the slope of your roof.
In general, homes don't need peel-and-stick over the entire roof, unless the roof has an unusually low pitch (a flat roof, or an almost flat roof), or unless you are worried about hurricanes.
So many problems have been reported when open-cell spray foam is used on the underside of roof sheathing that I would avoid that approach. Either rigid foam above the roof sheathing, or closed-cell spray foam on the underside of the roof sheathing, is a better approach. For more information, see "Open-Cell Spray Foam and Damp Roof Sheathing."
Martin roof pitch with be either 4:12 or 5:12. Haven't 100% nailed that down. As far as using the peel and stick my understanding is that this would be the most "bullet proof" underlayment for a standing seam metal roof. Obviously ice is not and issue though hurricanes are.
If I were to put rigid foam on top of the sheathing I would then put my roofing membrane over top that followed by purlins or would the membrane go on the deck followed by rigid foam and then purlins.
I am more apt to go with a closed cell under the deck and no rigid on the exterior as most contractors in this area would be inexperienced in the previous scenarior. In this case would I benefits from running 1x4 over the roofing membrane to create an air gap? Also is there any worry with using closed cell as it attains to trapping moisture between the roofing underlayment and closed cell foam? What if your roof were to leak.. how would you detect it with closed cell under the sheathing.
Just trying to wrap my mind around it all. Really appreciate your knowledge.
Miles
Miles,
Q. "If I were to put rigid foam on top of the sheathing I would then put my roofing membrane over top that followed by purlins or would the membrane go on the deck followed by rigid foam and then purlins?"
A. You don't need roofing membrane. You need roofing underlayment. (It's required by code.) If you are worried about high temperatures, you can specify a high-temperature roofing underlayment. If you plan to install your standing-seam metal roofing on purlins, then the underlayment would go above the rigid foam, and the purlins would go above the roofing underlayment.
Q. "I am more apt to go with a closed-cell [foam] under the deck and no rigid on the exterior as most contractors in this area would be inexperienced in the previous scenario. In this case would I benefit from running 1x4 over the roofing membrane to create an air gap?"
A. Again, I would refer to the layer above the sheathing as "roofing underlayment," not "membrane." There is some possible benefit to using 1x4 purlins -- especially if you specify vapor-permeable roofing underlayment (in which case you would be providing a possible mechanism to allow your roof sheathing to dry to the exterior).
Q. "Is there any worry with using closed-cell [foam] as it attains to trapping moisture between the roofing underlayment and closed cell foam?"
A. Some people worry about that -- but as long as the roof sheathing is dry on the day you install the spray foam, everything should be OK.
Q. "What if your roof were to leak? How would you detect it with closed-cell [foam] under the sheathing?"
A. All roofs leak eventually. Trust me -- when your roof leaks, you'll notice. The first clue is usually a ceiling stain or ceiling drips.
Hi Martin,
I have an 18'x24' post and beam home in NH. There are 3 common rafters 8"x8" on each side and 5 5"x7" purlins between each set. Also a 5"x5" ridge beam. This is sheathed with 1" boards of varying widths mainly around 9". On top of the 1" boards I adhered a layer of 2" xps, then a layer of 1.5" polyiso, then 1/2" ply, then a layer of owens corning weatherlock and then 3 tab shingles.
My plan from there was to picture frame each set of purlins with spray foam then fill the cavity with unfaced r19 then strap and finish with pine v-groove. Leaving about 3/4 inch of the purlins exposed and 1 3/4 of the center common rafter on each side.
Also while replacing rot in my wall from someones bad siding mistake, which is a whole other story....I added an 8" strip of iso on the exterior wall board to cover the common rafter hoping to eliminate thermal transfer into my ceiling.
Does this sound right or should I be putting gypsum on before the v-groove? That part of the article confused me a bit. I figured just having the v-groove would make it much easier to dry to the interior. Also the xps should work fine as an air barrier right? I'm really hoping that part isn't where I really messed up.
That would be unfortunate for me because it would mean to achieve my r38 requirement I wouldn't be able to expose my purlins
Any help is greatly appreciated.
Preisendorfer,
There are a couple of worrisome issues you haven't addressed. Ideally, this type of assembly has a very good air barrier as close as possible to the interior. Your interior air barrier needs to be continuous. Typically, examples of a good air barrier would be interior gypsum drywall -- which only works if it is continuous (it can't be interrupted by purlins or rafters) -- or peel-and-stick (like the Weatherlock product you plan to use). But the peel-and-stick needs to go as close to the interior as possible -- in your case, directly above the sheathing boards (not on top of the rigid foam).
Your assembly provides lots of hidden air channels where interior air can move around. Eventually, the interior air might hit a cold spot, leading to condensation.
By the way, your proposed ceiling boards aren't an air barrier. They will leak like a sieve.
So considering everything is already installed on the roof but interior insulation and sheathing hasn’t been installed what would your suggestion be for finishing?
Preisendorfer,
I guess the ideal solution to your dilemma would be to add new interior framing that would allow for the installation of a continuous, uninterrupted ceiling of gypsum drywall.
Hello Martin,
I am working on getting new roofing for my church and considering steel roofing to replace the current asphalt shingles. Current issues with the roof are as follows:
- no insulation
- frequent ice dams in winter and large icicles from melting snow
- curling and peeling shingles
Location is Hamilton, Ontario, which I believe is climate zone 6.
A structural engineer has examined the roof and recommended that a dead load of 250 lbs per square is the maximum that should be put on the decking (not including existing fiberboard).
Current construction per the building blueprints is (from inside out):
- for main auditorium, 4" tongue and groove v-joint western red cedar roof decking supported by laminated arch beams on 16 ft. centers (roof pitch 7/12)
- foyer area has 3" t-g decking and 4/12 pitch in outer sections and 13/12 pitch at peak
- aluminum foil
- 1/2" fiberboard
- 15# felt
- asphalt shingles
The current plan based on our preferred roofing contractor is to strip the shingles down to the fiberboard, then do the following:
- install roofing paper over whole roofing area
- install horizontal strapping (2x3's) on 24" centers
- fill space between strapping with 2" Isoboard rigid insulation
- install 2x3 strapping vertically to create a venting channel (1/4" gap at bottom for air inlet and ridge cap for outlet) - see photo
- install 1x4 strapping horizontally to support steel roofing
- install steel roofing (stamped strips 3' wide by 20+' long)
We (the church board) have a consensus on the steel roofing but are at a quandary regarding the option to add the 2" of rigid insulation. Other options were considered but either were out of our budget or added too much weight to the roof. I realize the 2" of insulation will not make much difference in energy savings since the building is only used for services 2 days of the week and estimated savings are only ~$500 per year. But the feeling of many church members is that any insulation is better than no insulation and that it may also help reduce the ice dam issues. Adding insulation on the interior is not an option because people want to preserve the appearance of the wood decking and also the additional cost.
I also realize that the insulation is not enough to prevent condensation of interior moisture in the roof deck, so this is a concern. I would like to add more insulation but the current weight estimate is 206 lbs per square and adding more would increase weight too much if another layer of strapping is used. The contractor is not interested in adding more insulation or in doing it without strapping. Weight estimates from the roofer are: 130 lbs/sq for steel roofing including strapping, 62.2 lbs/sq for insulation strapping and 13.8 lb/sq for insulation = 206 lbs/sq total.
So my questions are:
- is the planned roofing system okay in terms of helping to solve ice dams?
- will the addition of rigid insulation cause issues with trapped moisture in the roof decking or are we better off leaving it out?
- should impermeable underlayment be used over the sheathing rather than roofing paper?
- any other suggestions?
Thanks!
David,
Q. "Is the planned roofing system okay in terms of helping to solve ice dams?"
A. Yes, adding 2 inches of XPS insulation, ventilation, and steel roofing will reduce ice dams.
Q. "Will the addition of rigid insulation cause issues with trapped moisture in the roof decking or are we better off leaving it out?"
A. No, the rigid insulation won't trap moisture. I'm not sure why you wrote that "the insulation is not enough to prevent condensation of interior moisture in the roof deck." The underside of the roof deck is at room temperature -- and therefore it won't be cold, and won't be a condensing surface.
Q. "Should impermeable underlayment be used over the sheathing rather than roofing paper?"
A. Either type of underlayment will work, since your roof sheathing won't be able to dry to the exterior in any case.
Q. "Any other suggestions?"
A. Yes:
(1) Either EPS or polyiso is more environmentally friendly than XPS. For more information, see "Choosing Rigid Foam."
(2) Instead of cutting up your rigid foam into narrow rectangles and inserting it between 2x3s, you should install a continuous (uninterrupted) layer of rigid foam above the roofing underlayment, and then install the 2x3s (if desired) on the exterior side of the continuous layer of rigid foam. For more information, see "How to Install Rigid Foam On Top of Roof Sheathing."
> (1/4" gap at bottom for air inlet and ridge cap for outlet)
A 3" high eave to ridge vent is good for ice dam reduction with little insulation. Blocking airflow through it with a 1/4" inlet and/or outlet isn't.
Yeah - volume of air aside, you can't rely on a 1/4" gap not being blocked or maintaining its dimensions over time.
That was my concern as well. I calculated the minimum area per the Tobiasson article and it should be at least 0.8" high gap all around. I'll take that to the roofing contractor.
Thank you Martin for your quick reply! That is most helpful.
Re question 2, I was thinking of the top side of the roof decking and or the fiberboard. But then I guess it will still be fairly warm due to heat transfer from the interior.
Thanks for the links and advice also.
Hi Martin,
I have an octagon shaped home with a metal roof that is approximately 40 years old. I have owned it for 6 years. The cottage is located in climate zone 5/6. The first floor has cathedral ceilings and there is no attic space. The roof pitch is 2:12. The ceiling joists are 2" by 12", with the addition of 2" by 4"'s to make for a total space of 15" above the drywall. This space is insulated right up to the plywood roof sheathing with no air space and no venting. The insulation is pink fiberglass with paper backing as well as a second layer of pink insulation (no poly vapor barrier). I believe that the 2" by 4" layer was installed when the second story was added not exactly sure why ( maybe to add extra insulation). I should add that the walls are well insulated too.
The existing metal roof sits on top of the sheathing. It predates ice water shield and I do not know what is between the sheathing and steel. There are no caps where it meets at the hips of each the panels of the octagon. The previous owner covered these joints with some sort of sealant and then eventually covered the whole roof in an elastomeric paint. This system is starting to leak in spots. The other issue is the flashing of the second story addition over the first story metal roof. This flashing only extends 5" on to the roof and rain can be driven up underneath.
I am in the process of getting quotes to remove and replace with steel panels. I have received conflicting information from contractors and was hoping you could clear things up for me. Some say that they would strap(batten) the roof others would install roof right on sheathing. Some have recommended installing ice water shield over all sheathing. They have all recommend a synthetic underlay. Although one contractor would put underlay on top of battens the other below. I'm wondering if I need battens at all.
As there is no attic space I was thinking that battens would provide some air flow and allow any moisture that may come up through roof to escape. After reading the comments above I am not sure that this is a good idea. I would appreciate your advice. Thanks for your time.
Max,
In your climate zone, it's not a good idea to install fiberglass batts between the rafters unless you have a ventilation space between the top of the insulation and the underside of the roof sheathing. Octagon-shaped roofs are very difficult to vent, so solving this problem can't be done with ventilation.
To make the roof assembly safe in your climate zone, you need to install a significant amount of rigid foam on the exterior side of the roof sheathing before you install new roofing.
It's possible that your roof assembly already has moisture problems. Have you investigated to see if the existing roof sheathing is damp or spongy?
Ideally, you would install between R-20 and R-25 of rigid foam above your roof sheathing before installing a new roof. More information in these two articles:
"Combining Exterior Rigid Foam With Fluffy Insulation"
"How to Install Rigid Foam On Top of Roof Sheathing"
I would like to advise my sister on how to insulate there cottage cathedral ceiling , climate zone 6, on Christian Island, Great Georgian Bay, Canada, The cottage is only used from April until October.
The problem is overheating on the south facing roof, one pitch is 3/12 and the other is about 6/12. Currently, from the interior, you look up at the rafter bays and see the plywood roof deck and the roofing nails coming through, used to attach the composition shingles. You can feel on your face, the heat radiating from the underside of the roof. The loft area on a sunny day becomes to hot to use.
I was thinking they could press fit and glue with construction adhesive 2" or 3" thick cork to the under side of the plywood, on the south face only, and call it done. I think that would work for the aesthetic of the cottage.
I am not that confident regarding the craftsmanship of the comp roof, (however, there are no visible signs of leaks), so I think allowing the plywood to dry is important. My thought was that the cork would still allow that to happen.
Your thoughts?
Martin,
In the section "Can I use dense-packed cellulose as the only insulation for an unvented roof assembly?" you close with the following
"If you’re building a new house, however, here’s my advice: if you want to insulate with cellulose, make it a ventilated roof by including ventilation channels under your roof sheathing. "
Am I correct that this advice only applies when cellulose is the only insulation and does not apply when rigid foam is installed above the roof sheathing?
Just trying to get it straight in my head,
Phillip
Philip,
Yes. As soon as you choose to put insulation over the sheathing you have to go to an un-vented roof assembly.
Hi Martin, thank you very much for this very informative article. I have a situation that I'm not sure how to address, and was hoping to get some insight from you here. I'm remodeling my quirky old house. The house is a perfect rectangle, with a double gabled roof (not sure if that's a term or not). Basically, gables on all 4 sides, with the taller ridge running front to back. I'm in climate zone 3, I think. In California it's called climate zone 6, but I think that's a different zoning numbering system (zip code 92627, temperate SoCal coastal city).
The 4 corners of the house has very low walls with an angled ceiling where the front and back roof rafters slope, and there unfortunately no soffit vents added when the house was re-roofed and re-cladded. The only vents in the attic are 6 Ohagin vents and the two gable vents on the front and back. When they re-roofed, I put Roxul mineral wool batts between the skip sheeting in the areas I knew I would not be able to reach later from the attic area. Now, in reading this and other articles on how these areas need to breathe, I'm wondering if I caused an issue and should have left that area without insulation even though it is inside the building envelope.
The interior of the home is about to get gutted for an interior remodel, and the plan was to vault certain areas of the inside of the house to open it up in the kitchen and gathering area.
Questions:
*Should I not vault the areas I planned to vault because there is no good way to ventilate the backside of those areas in between the rafters? Or, can insulating the back of the roof sheathing with closed cell spray foam or using polyiso foam board in between or over the rafters do the job?
*For the 4 low sloped ceiling joist areas with Roxul insulation, should I try to remove that insulation from the inside when removing the drywall/lath and plaster inside to allow for proper breathing, or leave the batts in place? They fill the entire void fairly tightly between the drywall and skip sheeting. The rest of the house has not received insulation yet, either in the crawl space or the attic, because I wanted to get everything done with the remodel before figuring out the insulation plan, which I'm also not sure about how to best address given this house's weird setup.
User-7521954,
Several issues here:
1. If you tell us your name, this dialogue will be friendlier. (I'm Martin.)
2. Since I'm retired, I don't really have the time to answer this type of question in detail. I suggest that you post your question on GBA's Q&A page.
3. Briefly, your house has a type of roof called a cross-gable roof. Since this type of roof has 4 valleys, you can't use a vented approach. The only way to create a cathedral ceiling with this type of roof is by using an unvented approach. If you're working from the interior side of the roofing, that means you'll need closed-cell spray foam.
Hi Martin,
Apologies on the name not appearing. I just fixed that. I'm Luke, it's a pleasure to meet you and thank you for your blog and book. I've tried to pull what I can from that information, but it seems my situating is not a perfect fit for examples. I can reach out on the Q&A page. I'd be willing to pay you for your time if you wanted to consult on the phone for a bit. Having a knowledgeable answer from someone who knows what they are doing would mean a lot. Thanks again.
ZIP code 92627 would be DOE climate zone 3B.
As little as an inch of closed cell polyurethane (R6-R7) on the underside of the roof deck would be enough dew point control to allow R33 or more of fiber insulation tight to the closed cell foam to bring it up to IRC 2018 code minimum. I'd have to look it up, but I believe CA Title 24 calls out R30.
How deep are the rafters?
If yours are milled 2x8 rafters (7.25") an inch of HFO blown polyurethane (R7) on the underside of the roof deck and 6.25" of blown cellulose (or compressed R25 fiberglass batts) would pretty much get you the R30 with very little moisture risk.
It looks like you're re-roofing over skip sheathing(?), with possibly full-dimension 2x4 rafters in some sections, or maybe it's all 4x6 or 2x8??
Measure the rafter depths and spacings- it matters.
Laying down a structural layer of OSB sheathing over the skip sheathing and intalling a fully adhered membrane type weather resistant barrier (vapor permeance not important) followed by 2.5" of fiber faced roofing polyiso (R14) held down with a 5/8" plywood or OSB nailer deck with a felt & shingle layup works. With 4" of rafter bay cavity you'd be able to get another R15 of blown cellulose or R17 of 1.8lbs blown fiberglass to hit the R30 mark, coming close to hitting IRC 2018 compliance on a U-factor basis (U0.030, or R33 "whole assembly").
Hi Dana, thanks for the well-written response. The existing rafters were full dimension 2x4 rafters spaced around 32" apart. The newly installed rafters in the vaulted areas are milled 2x10 rafters on the 20' spans spaced 16" on center, and on the shorter span they are milled 2x8 spaced 16" on center. 16" OC is a lot of thermal bridging with lumber from the roof assembly to the inside of the home, but I would like to get to the effective R-value up to a decent level, if possible, while being mindful of cost. The minimum amount of closed-cell followed by less expensive insulation does sound like a nice way to go, especially given how expensive closed cell spray foam is here in coastal California where it's still a rarely used insulation type.
I suppose to get to R-30, I would need 1.5" of closed cell (R-9.75) plus 5.5" of open cell (R-20.35), getting me just over the required insulation value. That said, it seems like an unvented attic only requires R-22? https://www.jm.com/content/dam/jm/global/en/building-insulation/Files/BI%20Toolbox/BID_285_CA_Title24_Flyer.pdf
It would be nice for budget reasons to find a way to get the insulation costs down to 1" of closed cell and batt insulation.
"As little as an inch of closed cell polyurethane (R6-R7) on the underside of the roof deck would be enough dew point control.."
Can you confirm that 1 inch is sufficient? I'm being told by my spray foam contractor that 1.5 inch is the minimum for closed cell spray foam. It's possible it varies based on the type used. This is Demelic HFO closed cell spray foam he is quoting as having an R-7 per inch value.
I'm in 92627 zip code, which I believe is a marine climate zone 3. I think California has its own climate zone classification in which I would be California's climate zone 6 under that scale.
1) you mentioned no can lights... as they take up insulation space, generate heat, etc. what about the new slim led recessed lights: https://www.homedepot.com/p/Commercial-Electric-4-in-Selectable-New-Construction-and-Remodel-Canless-Recessed-Integrated-LED-Kit-for-Shallow-Ceiling-4-Pack-91364/306079859
2) what about a fan, that wouldnt give off the same sort of heat, but would take up some space. Is the only drawback on a 1.5" fan box diminished r value?
if everything is good to go, would fire-rated be the way to go for that last layer of insulation?
(if it matters for this question, ill be doing cut and cobble polyiso or rockwool in between rafters, then a 2" polyiso screwed to underside of rafters w/ a 1" air gap between sheathing and insulation.)
@kevin I'm in a similar position looking for slim recessed lighting options for my 7/12 and 8/12 pitch vaulted ceilings that are okay being right up to spray foam. The issue I see with the lights you shared is that they are not adjustable and therefore could not be directed to point down. You'll want to look at gimbal options if you want to avoid the lights playing lightsabers across the room.
Luke,
I've used similar lights on cathedral ceilings without a spot-light effect. They are more like a surface-mount than a recessed fixture in the way they diffuse light.
I'd be using the type of lights youre talking about Malcolm. Martin says no recessed lights... but WHAT ABOUT the slim style? Is the only drawback in this case diminished r value with potential air leaks?
And I also called my inspector, he said theres no code for air gap between housing and insulation, but said to be safe, leave 1" all the way around. thoughts?
I am looking for some advice on re-insulating a cathedral ceiling. The house is early 1990s, 2x10 rafters, no vapor barrier, R30 fiberglass rolls with kraft facing, drywall below the insulation, asphalt roof above the sheathing above. There is a knee wall on both sides of the room with no drywall (kraft facing of R30 is exposed). There are soffit vents, but they open into the fiberglass roll and then further up the roof a small, inadequate ventilation chute starts. There are ice dam problems, not surprisingly, and in the summer he peak of the room is well over 100F. The main room covered is a bedroom, but there is an attached bath (also cathedral ceiling) with a skylight.
We are in the middle of zone 5 (SE Michigan).
We are getting a new (metal) roof, and I plan to insulate and air seal the roof much better. The question is how. We’ve thought about adding rigid foam above the sheathing (R24 outside, new R 30 in the rafter bays), but the aesthetics are problematic as this section of roof butts up against another section of roof at an angle.
We are considering two options. Both involve installing the new roof without exterior insulation. Instead we’ll pull the ceiling down and work from the inside. I’d like to hear thoughts on the following two options, particularly as they relate to moisture management and air flow. I’ll describe the assemble from the top (by the sheathing) down.
Option 1:
Sheathing
Air gap (1.75”)
4” fiberglass-faced polyiso, sealed with foam on edges and seams (probably 1.75” slats above it for spacing)
3.5” rockwool (note that below this layer we’re now at the bottom of the rafter)
3” of foil-faced polyiso (1” layer and 2” layer with offset and taped seams)
Drywall (but not in the knee wall area)
Option 2:
Sheathing
1” air gap
4” polyiso (fiberglass-faced)
Fur the bottom of the rafters out 3.75”
8” Rockwool
[Would I want a vapor barrier beneath the Rockwool?]
Drywall (also in the knee wall area with this option)
Both should get R50 or slightly higher depending on how you count polyiso. Vapor management is different with the two approaches.
What changes would you suggest?
Seth,
A vented approach is only possible if your rafter bays are clear of obstructions from soffit to ridge, and if your roof has no valleys, hips, dormers, or skylights. Does that describe your roof?
If that describes your roof, you can have a vented roof assembly. That said, I'm not sure why you want to use 4 inch-thick polyiso for your ventilation baffle. In general, you only need your ventilation baffle be thick enough to resist breakage. Usually 1 inch thick is plenty.
In most of the rafter bays, yes, obstruction free. While I don’t need 4” for the baffle, I’m trying to increase the r value substantially with limited rafter space to work with. 4” of polyiso has good r value per inch. I. Could do a 1” baffle and fill with Rockwool or cellulose, it ether I would need to fur out further to Ge the same r value. Is there a performance reason not to use thick polyiso?
Seeking to create 100% closed-cell assembly that is future proof.
thanks for bringing all this information together into one place. super helpful. I went through most of the comments and did not see this question posed so here goes...
We have a 700 sqft partially vented attic in Zone 4/5. We’re planning on turning this simple gable roof into an unvented attic using 100% closed-cell spray foam. We intend to seal from top plate to the ridge board of the 2” x 6” rafters to get ~ 5” of foam and 100% airtight. My only reservation is regarding the serviceability of the roof deck down the road. Worried that the bond of the deck to the foam will inhibit any ability to service the sheathing alone. We will also be installing solar panels, anchored to the rafters, but may introduce other conditions that we haven't anticipated.
Would there be any penalty if we installed 1/2” rigid foam boards – attached directly under the roof deck in the rafter bays and gable walls before filling the rafter and stud bays with several inches of closed-cell spray foam? Sort of a hybrid to cut and cobble? What type of foam boards would be best in this application?
It seems like this approach would allow us to remove the sheathing from the outside if we ever needed to. Thanks in advance for your views on this and keep up the great work on GBA! - Jim.
Jim,
Q. "Would there be any penalty if we installed 1/2 inch rigid foam boards – attached directly under the roof deck in the rafter bays and gable walls before filling the rafter and stud bays with several inches of closed-cell spray foam?"
A. No penalty -- in fact, it's a good idea. Other materials you can use include strips of asphalt felt installed with staples, kraft paper installed with staples, or cardboard rectangles installed with staples. Almost anything will work as a bond break.
thank you Martin! the underside of the roof deck isn’t “clean” in that there are certainly nails that were intended for a rafter that were placed directly through the sheathing. is that something to be concerned with when creating the bond break? what happens when water finds its way into the foam via these nails?
Jim,
Q. "The underside of the roof deck isn’t 'clean' in that there are certainly nails that were intended for a rafter that were placed directly through the sheathing. Is that something to be concerned with when creating the bond break?"
A. No.
Q. "What happens when water finds its way into the foam via these nails?"
A. Then you have a roof leak. No matter what insulation method you choose, you can't expect your insulation to prevent roof leaks. To prevent leaks, inspect your roofing regularly and replace it when necessary. Left in place long enough, all types of roofing will eventually leak.
A couple of us asked this question above and there have been various ideas proposed, but Martin's reply summarizes the main options presented for people who have a clean roof deck between evenly spaced rafters - which is sounds like you have.
Unfortunately for people like me who have skip sheeting between the deck and the joists, and old 2x4 joists sprinkled in between the new joists (and several nails sticking through from the nail-happy roofers), there isn't a clear answer for how to create a break.
Martin or Dana, can I create a bond break at the skip sheathing, which would inevitably leave a 1" air gap where there isn't skip sheathing? I'm in climate zone 3, so I'm not sure if moisture in the deck is really even going to be an issue with or without spray foam.
Luke,
Q. "Can I create a bond break at the skip sheathing, which would inevitably leave a 1 inch air gap where there isn't skip sheathing?"
A. Yes.
Hello Martin,
Thank you so much for this great site. I'm trying to put together the information in all of these articles:
https://www.greenbuildingadvisor.com/article/how-to-install-rigid-foam-on-top-of-roof-sheathing https://www.greenbuildingadvisor.com/article/insulating-low-slope-residential-roofs
https://www.greenbuildingadvisor.com/article/how-to-build-an-insulated-cathedral-ceiling
I am in Climate Zone 3C and currently have an uninsulated, 2/12 low slope, tongue and groove cathedral ceiling. I want to add insulation during an re-roof so I am only adding polyiso rigid foam above the roof deck. I would prefer not to do anything to the T&G from below to keep the wood finish and not need a second contractor.
I'm trying to wade through the several different options various roofing companies have given me.
One roofer is suggesting a 2" vented deck above the rigid foam, but it sounds like that isn't adequate on a low slope roof like mine. No roofer has offered more than 4" of foam. None of them have talked about adding an air barrier layer above the T&G.
Trying to put together all these articles together, given my requirements/restrictions, is the best option to create an unvented roof by doing one of:
1. vapor permeable air barrier above the T&G (such as Blue Skin VP100 or Solitex Mento)
2. R38 insulation (2 layers of 3.5" of polyiso rigid foam board, with staggered seams)
3. OSB
4. two layers of 30lb felt
5. asphalt tiles
or
1. OSB above the T&G
2. R38 insulation (2 layers of 3.5" of polyiso rigid foam board, with staggered seams) with taped seams
3. OSB
4. two layers of 30lb felt
5. asphalt tiles
Besides not meeting code, will I have any issues (such as moisture) if I put up less insulation, say 2 layers of 2" polyiso?
Thank you so much!
User 7574668,
It would be nice if you would tell us your name.
Of the two options listed, the first is the best, because it includes an air barrier between the T&G boards and the rigid foam. Note that this air barrier doesn't have to be vapor-permeable.
The second option lacks an air barrier, although you could install the OSB in an airtight manner if you wanted, by including a high-quality tape like Zip System tape at the OSB seams.
Q. "Besides not meeting code, will I have any issues (such as moisture) if I put up less insulation, say 2 layers of 2 inches polyiso?"
A. No moisture issues -- just increased heat loss (and somewhat higher energy bills) during the winter.
Thank you for your reply!
Is my understanding correct that a vented deck won't help much with a 2/12 low slope roof? And that it could actually make things worse?
Mark,
It is true that you cannot use a vented approach for a roof with a 2/12 slope. If your insulation consists entirely of rigid foam, there is no need for a vent channel.
I was looking at GAF's shingle warranty:
http://apps.gaf.com/content/documents/23303.pdf
"GAF will NOT be liable for and this warranty does NOT apply to:
1) Damage resulting from anything other than an inherent manufacturing defect in the GAF Products, such as:
c) inadequate ventilation."
It sounds like they won't warranty an unvented roof?
I may be reading it wrong, but Inspectapedia shows a diagram from Carson Dunlop Associates which as far as I can tell indicates that the recommended venting for a 2/12 cathedral roof has 1" between the roof and the insulation? That doesn't seem like it would work?
https://inspectapedia.com/insulation/Insulate_Cathedral_Ceilings.php
https://inspectapedia.com/interiors/1382s.jpg
Mark,
You raise several issues. The first issue is whether asphalt shingles are an appropriate roofing material for a low-slope (2-in-12) roof. GAF may or may not allow their shingles to be used for such a low-slope roof -- I haven't checked -- and may specify certain extra details when their shingles are installed at such a low slope. Whether or not GAF allows it, many roofers advise against using asphalt shingles for such a low-slope roof.
The second issue, which Malcolm Taylor addresses, is whether (a) GAF's warranty is worth very much, and (b) whether you should care if your installation violates the shingle warranty. Many roofers who have tried to make a claim on a roofing shingle warranty have discovered that most such warranties are worthless, since they don't cover labor costs and because it's hard to convince a shingle manufacturer that their product was defective. That's why builders who install asphalt shingles on unvented roof assemblies don't worry much if such installations violate the manufacturer's warranty provisions.
The third issue is whether Carson Dunlop Associates is correct concerning the effectiveness of a 1-inch high vent channel in a 2-in-12 low-slope roof. In fact, research shows that you won't get significant air flow through a 1 inch vent channel on such a low slope. In other words, the vent channel won't work, regardless of what Carson Dunlop Associates recommends.
Mark,
I read that slightly differently. GAF doesn't care what causes your roof to fail. It can be inadequate venting, or damage done when your pet monkey escaped. Was long as it isn't a manufacturing defect that causes the problem, you are out of luck.
Is there any harm with adding a 2" vented roof deck and a GAF Cobra Exhaust Vent? My roofer is very, very insistent that it is the way to go. I'm worried that the insufficient venting (and the Cobra Exhaust Vent doesn't seem like it'll allow a ton of airflow either) might create a moisture problem. But if there's no harm, I may just go ahead with it.
The reason I still want to work with him is that even with the vented deck, he'll still be cheaper than going with other roofers who don't even think moisture is something that needs to be considered in the project. (Most people I've told my concerns about the insulation creating a due point have looked at me like I'm crazy.)
He also said that the air barrier is a waste of money for my house because the entire house is so leaky and won't be fixed (which is probably true).
I'm starting to wonder if going with a TPO roof would simplify things.
Mark,
"He also said that the air barrier is a waste of money for my house because the entire house is so leaky and won't be fixed"
If your roofer said that he has no idea what he is talking about and is just as worrying as the other ones you consulted. The main thing that stands between your new roof working or not is a good air-barrier. My advice would be to get a roofer to put y0ur roof on, and get an architect, engineer, or other building scientist to design the roof assembly.
Mark,
To amplify Malcolm's comment: While an air barrier might save you some money on your energy bills, that's not the main reason you need one here. You need an air barrier to keep your sheathing from rotting.
"You need an air barrier to keep your sheathing from rotting."
If I understand correctly, the reasoning is that even though I'm in a hot climate, during cooler outside temps, the hot interior air will move through my T&G ceiling, hit cooler air leaking through the untaped rigid foam insulation, causing the moisture from the interior air to condense and eventually rot the T&G - the air barrier above the T&G (under the insulation) is there to limit the air flow through the T&G and allowing any condensing moisture to dry to the interior. Is that correct?
The air barrier would be created by using any of the following:
- Solitex Mento 1000, Delta-Vent-S, or Titanium UDL 30 with taped seams
- a layer of OSB with taped seams
- taping the seams of the rigid foam
Taping with some sort of air barrier tape I presume?
Since the rigid insulation is being screwed in, I wonder how solar gets installed above that without going through the air barrier?
If the T&G extends beyond my exterior walls, how would I air seal that?
And just to verify, the 2" vented deck, while unlikely to be useful, shouldn't be harmful?
Thank you so much!
Mark
Mark,
In winter, your OSB roof sheathing may be cold enough to be a condensing surface for the moisture carried by your interior air. That's why you absolutely need an interior air barrier when your ceiling consists of (leaky) tongue-and-groove boards. (Interior air can move through small air channels between your rigid foam and thereby reach the underside of the cold sheathing.)
Q. "If the T&G extends beyond my exterior walls, how would I air seal that?"
A. You wouldn't. If you build your ceiling that way, you will be plagued by air leaks for the life of the house. That's why the tongue-and-groove ceiling boards must stop at the exterior walls -- you certainly don't want to extend those boards to the exterior.
So given that's the way my house is already built, short of pulling off all the roof sheathing is there any solution for me?
Would it be better to just leave it alone (ie. don't add insulation) and live with the uncomfortable temperature? The current roof has never dripped or leaked which I would have assumed would happen if there was condensation problems. The last time the house was re-roofed the roofer didn't find any mold/rot issues. There are a lot of uninsulated T&G houses around here.
Mark,
Owners of older homes make compromises all the time. If you have an existing house with air leaks at the perimeter of the ceiling, you may, indeed, need to "just leave it alone and live with the uncomfortable temperature." Your house won't necessarily be uncomfortable -- but your utility bills for heating and cooling may be higher than they would be in a house with fewer air leaks.
With no insulation, like I have now, I would assume that interior moisture would still be condensing in the roof sheathing as it hits the cold roof shingles. What makes adding insulation to the roof worse? Is it because the roof can no longer expel that moisture from the roof sheathing to the exterior?
Can I fix (most of) the air leak issue by just drywalling under the T&G?
Thanks Malcolm.
We have a new construction project, 1400 sq ft residential in climate 4c marine (olympia wa). We are at the dry-in stage. The 7:12 pitch roof is sheathed with 15/16 cdx and covered with GAF tiger paw. The rafters We have the 26 gauge standing seam material but we are waiting for clear weather to install. Originally we planned to install R10 rigid above the sheathing (along with another layer of sheathing to support the standing seam panels), but due to dangerous conditions (steep roof, constant rain / wet / slippery) we would prefer to save the budget and skip the additional work on top.
New plan is to spray closed cell foam directly to the underside of the sheathing. Rafters are 2x8 so there is just enough space to meet R49.
In my (limited) experience if your roof leaks then no amount of ventilation will save it. I've seen traditionally vented roofs rot away after a few years with a leak. Snow load here is 30 lbs., and rarely lasts more than a few days, so I don't think condensation will be a problem (Joseph Lstiburek points out that > 50 LB snow loads must be ventilated due to the R value of the snow!).
Questions:
Is it really useful to vent the underside of the sheathing? Channel vents have several drawbacks: cost of labor, added cost of material, lost R value. Am I making a mistake by not venting?
The tiger paw was installed assuming that the interior insulation would be vapor permeable (with exterior R10 rigid insulation). Assuming that we do not vent, does it matter that we use a non-permeable underlayment with a non-permeable metal roof? Or do i really need to rip it up and install felt? We chose standing seam to minimize the risk of any leaks, and we plan to focus intently on getting all of the flashing details right. This is a simple doghouse roof, gables at both ends, super simple.
If we had gone with the intended plan, using exterior R10 rigid above, then how would you deal with the top layer of sheathing? Seems like the same problem - you have a layer of cdx or OSB sandwiched between two impermeable layers. It seems to me the only solution is to get the flashing details right.
Would it be useful to install a layer of peel and stick? I'm thinking this would be "belt and suspenders" should the standing seam have leaks.
Hope this makes sense. Yes, I am a DIY'er, but trying to get it right. Any advice would be greatly appreciated.
>"New plan is to spray closed cell foam directly to the underside of the sheathing. Rafters are 2x8 so there is just enough space to meet R49."
Really?
With the thermal bridging of the rafters it's going to underperform R49 of blown fluff on an attic floor by quite a bit, and even HFO blown closed cell foam has a substantial carbon footprint:
https://materialspalette.org/wp-content/uploads/2018/08/CSMP-Insulation_090919-01.png
At 7" the vapor permeance is going to run about 0.15-2 perms, almost a true vapor barrier, with no drying toward the interior.
As an alternative, 2" of HFO blown foam would run about R14 and 0.5-0.7 perms (enough to actually dry during the relatively short warm season in zone 4C) , and compressing R21 fiberglass or R23 rock wool batts (or 1.8lbs blown fiberglass) into the remaining 5.25" would yield R20 or R22 respectively for a center-cavity R of R34-R36, and with ~40% of the total R exterior to the fiber insulation it would have substantial dew point control at the foam/fiber boundary.
Yes there would be a modest increase in energy use, but it's a much smaller hit than you would think when comparing center-cavity R.34-36 compared to R49, since the much more conductive framing fraction hit is about the same either way.
If there is sufficient headroom (and you have the patience) to add 1.5" Bonfiglioli strips (1x furring with 3/4"/R5 polyiso) to the bottom edges iof the rafters with 2" of HFO blown foam (R14) there would then be 7" of remaining cavity, deep enough for R30 rock wool batts, which would then perform at about R39 for R43 total. The R5 thermal break on the rafters would improve the framing fraction performance to something comparable to (a bit better than, actually) a 2 x 12 rafter bringing it close enough to code on a U-factor basis (which is anything under U0.026, or R38.5 "whole assembly) and there would still be adequate dew point control at the foam/fiber boundary to be able to use interior latex on ceiling gypsum as the interior side vapor retarder. See:
https://www.finehomebuilding.com/membership/pdf/9750/021250059.pdf
Thanks Dana, this (with the Bonfiglioli strips) is a much better approach. Not only is it greener but according to our insulation subcontractor it is about 1/3 the cost. And there is a local supply of recycled polyiso that we can use for the Bonfiglioli strips.
I'd like to find a way to monitor moisture content of the sheathing - even if it is a few localized spots. Maybe embed a few moisture sensors at strategic locations.
Chicago zone 5. We moved into 1910 balloon frame gable home with 2x4 roof rafters in a walk up unvented attic. Right now rafter bays are insulated with kraft faced r-11 fiberglass batts. This was only insulation in whole house when we moved in and we've slowly been doing retrofits. Obviously way under insulated for zone. Shingle roof, no exterior insulation. Roof replaced in 2013 by previous owners and by all accounts great shape (Had a roofer up there to add bathroom fan vent). Sheathing appears like some sort of skip sheathing? I can feel roofing paper between gaps in boards. Roof very steep, not sure angle. We added a second zone HVAC into attic and hope to convert into office space. We have been doing work ourselves. Initially looked into close cell however extremely put off by negative reports of off gassing and bad applications.
It seems my options are very limited. I initially thought to cut/cobble 4inch foam boards between rafters and then layer another layer of 4 inch foam board to achieve r40. Sounds like this would not be smart after reading article. Feel very stuck between a rock and a hard place.
Thinking possibly 2 inch polyviso in bays to create 1.5in vented space then another layer of 4inch xps across rafters. Bring to R33. Still shy of R38. Do I need ridge vent if entire roof has gaps? Sorry if that is dumb to ask.
No idea to to correctly attach all this and still put up drywall. 1x3 furring cross top of 4 inch boards I'm guessing over rafters.
Added photo of roof sheathing where some batting fell away. Photo is sideways FYI.
Ashley
>"Thinking possibly 2 inch polyviso in bays to create 1.5in vented space then another layer of 4inch xps across rafters. Bring to R33. Still shy of R38. Do I need ridge vent if entire roof has gaps? Sorry if that is dumb to ask."
Skip sheathing isn't really "vented" if there is a continuous layer of tar paper/rosin paper between the sheathing and shingles, and the shingles would have to be cedar or something similar to allow some amount of free air movement. If it's possible to get full soffit to ridge ventilation in every stud bay (often possible with simpler roof lines) that's the preferred method, with a 60/40 split in the free air area of soffit/ridge.
Why the shift to XPS for the 4" continuous layer? If it were polyiso on the interior it would be a continuous R24. (R22.5-R23 if recliamed roofing polyiso- highly recommended), and with 2" of foil-faced cut'n'cobble the center cavity R would be R35- R36. When the R1.5- ish value of the air films (both in the vent gap the interior & exterior films), the R0.5 interior side gypsum ceiling, the R1 sheathing and the R0.25 roofing are all added in, along with the thermal bridging of 2" of rafter through the cut'n'cobble it comes in a just about R38.5 "whole assembly" (or a hair higher), which is U0.026, exactly hitting code minimum performance on a U-factor basis.
You're right, we'll do continuous polyviso. That makes more sense.
Potentially found some used sheets. If we cut and cobble and fill 2x4 rafters with 3.5 inch board without air gap and then another layer of continuous polyviso underneath and took care to tape seams and airseal well, do you think this is inferior to vented attic?
Is it better to do thinner continuous rigid board sheets with seams staggered than 1 thicker sheet? Could create a lot of extra work though.
This would be the much easier route since right now the attic is already unvented.
Thanks so much for help, it has been so helpful.
Ashley,
Yes, if you want a vented roof assembly, you need all the usual components of a vented roof assembly -- soffit vents, a continuous vent channel from soffit to ridge, and a ridge vent. This approach won't work if your roof has valleys or hips.
Achieving code minimum levels of insulation in an older roof assembly is often difficult unless you are willing to lower the ceiling. You have to face facts, and facing facts sometimes results in a compromise. You may have to choose between a lower ceiling or a roof assembly with an R-value that is less than code minimum requirements.
“[Deleted]”
Hi, Martin and everybody.
I’m an owner-builder restoring a 19th century log house, and have a question about venting the cathedral ceiling. We’re in Zone 4 (southern Wisconsin).
My roof, from top to bottom, is this:
- standing seam metal roof, with soffit vents and ridge vent
- roof underlayment
- rough sawn 1x12 sheathing
-2x12 rafters and ridgeboard
- ventilation baffles from soffit to ridge
- dense-packed blown cellulose
- Reflectix vapor barrier (on bottom of rafters)
- ship-lapped 1x12s for ceiling
I’m at the stage of making my vent baffles on-site, and was planning to tack OSB board to ¾-inch by 1.5-inch furring strips. But a friend advised against the OSB, and suggested instead stretching Tyvek tightly between the furring strips to create a vapor permeable vent. Because of the log house structure, I don’t have that perfect building envelope from walls to ceiling. With that, and my ship-lapped ceiling, I’m thinking the Tyvek might be a good idea, in case any house moisture does get into the rafter bays. But it’s a time-consuming process (I tried it out today), I’m still working out how to get all of the seams (like at both ends of the rafter bay) air tight, and I’m wondering whether to just do the OSB boards.
I’ve read your article on site-built baffles, but as I’m new to all this, I still keep going back and forth. OSB? Tyvek? Something else? Any other detailing I should be aware of?
Thanks for any advice anybody has.
Peace,
Joe
Joe,
I think OSB is preferable to Tyvek, for a variety of reasons. The OSB is easier to install and easier to make airtight.
Your proposed roof assembly has an interior finish material (1x12 boards) that isn't airtight. You really need an airtight interior layer. Your "Reflectix vapor barrier" isn't designed to be airtight. The preferred method in your case would be to install a drywall ceiling with taped seams -- this would be your interior air barrier -- on the interior side of the rafters, followed by your 1x12 boards (which are decorative, not functional) on the interior side of the drywall.
Thanks, Martin. I appreciate it! It's a relief to get a professional's opinion. A couple follow-ups.
1) Before drywalling, would you still install a plastic vapor barrier onto the bottom of the rafters?
2) I'll be putting an 8-inch (outer dimension) stovepipe through one of the bays in the cathedral ceiling. Seems like a lot of possibility for problems here. Any advice on getting this detail right? (The bays are 22.5 inches wide.)
Thanks again,
Joe
Joe,
Q. "Before drywalling, would you still install a plastic vapor barrier onto the bottom of the rafters?"
A. I never recommended the installation of a plastic vapor barrier. You are in southern Wisconsin (Climate Zone 6). Apparently, you are under the mistaken impression that you are in Zone 4. For more information, see the climate zone map.
There is no code requirement for a vapor barrier in this assembly. What you need is an air barrier, not a vapor barrier. For more information, see "Do I Need a Vapor Retarder?"
Q. "I'll be putting an 8-inch (outer dimension) stovepipe through one of the bays in the cathedral ceiling."
A. I hope you don't mean a stovepipe -- I hope you are really talking about a metal chimney. (Unlike a stovepipe, a metal chimney consists of at least two pipes -- a pipe within a pipe, along with an air space or some type of insulation between the two pipes.) If you want your metal chimney to penetrate your ceiling, you need to contact the manufacturer of the metal chimney and order a kit designed for ceiling penetrations or roof assembly penetrations, and you need to install the kit according to the manufacturer's instructions.
Thanks, Martin.
Yes, metal chimney with an air space between two pipes, and we're getting that box that goes through the ceiling. And thanks for the clarification. I was assuming growing zones are the same as building climate zones, but I guess not!
~Joe
>"With no insulation, like I have now, I would assume that interior moisture would still be condensing in the roof sheathing as it hits the cold roof shingles. What makes adding insulation to the roof worse? Is it because the roof can no longer expel that moisture from the roof sheathing to the exterior?"
The interior side of the roof sheathing is much warmer now, so moisture only accumulates (as adsorb, not condensation) on the exterior-most portion of the sheathing, so a much smaller amount of wood is affected. The exterior of the sheathing is also much warmer than after the roof is insulated from the interior, so it's moisture content is less likely to rise to rot-inducing levels when it's finally warm enough for mold and fungal growth to really take off.
When insulated from the interior the entire thickness of the roof sheathing dwells are much lower temperatures, temperatures at which quite a bit of moisture can accumulate over a full winter, which is why it needs at least a Class-II vapor retarder for managing interior moisture drives. An inch or two of closed cell polyurethane at the roof deck is a Class II vapor retarder and air-tight, making it sufficiently protective of the roof deck from winter moisture drives in most climates, yet sufficiently vapor open for the roof deck to dry toward the interior.
But the R-value of just an inch or two of closed cell foam may not always be sufficient to prevent excessive condensation at the foam/fiber boundary if fiber insulation is used in combination with the closed cell foam. The ratio of foam-R to total-R matters, and the minimum ratio needed is climate-dependent.
Hi Martin, Dana, et al
I realize this article is pretty old, but comments seem to be going strong, so I figured I'd sign up and ask my question. (probably been heard a thousand times already).
We are currently refinishing the attic in our 120 year old 2.5 story house in coastal MA. Stripped all plaster and lathe off rafters and what seem to be mid span collar- or rafter ties, depending on whom you ask. The attic space is 24x32 with 3' kneewalls, which are actually part of the exterior wall. The rafters are 2x6 16' long and 24" on center. Roof is plain gable with 12/12 pitch.
I've already insulated the knee walls with roxul batts, put leftover batt pieces in plastic bags and stuffed them into the stud bays at right below floor level. (the spray foam guy told me to do that)
So, speaking of the spray foam guy: We got quotes for either 4" or 5" of closed cell spray foam. But when I mentioned thermal bridging through the rafters, (thanks, guys. I only knew about that from doing research) the sales person told me that I could either live with it or put up a continuous layer of 1" polyiso against the bottom of the rafters, then strapping, then the drywall.
Now here are my questions:
1. with 5" of foam, wouldn't there be an air gap of one inch or so between foam and polyiso, and would that be okay?
2. Would I also have to do the polyiso against the knee wall?
3. And are there alternatives in our scenario to avoid thermal bridging?
Thanks in advance for any help here. This stuff is keeping me awake at night!
Kerstin
Kerstin,
Q. "With 5 inches of foam, wouldn't there be an air gap of one inch or so between foam and polyiso?"
A. Yes.
Q. "And would that be okay?"
A. It wouldn't cause any problems.
Q. "Would I also have to do the polyiso against the kneewall?"
A. A continuous layer of interior rigid foam on the walls is certainly possible, but not mandatory. For more information, see "Walls With Interior Rigid Foam."
Q. "Are there alternatives in our scenario to avoid thermal bridging?"
A. Thermal bridging can be reduced, but it cannot be eliminated. There are lots of alternative approaches, and they are explained in my article. For example, you can install a continuous layer of rigid foam on the exterior side of the roof sheathing, or you can install framing members at 90 degrees to the rafters, on the interior side of the rafters, to deepen the rafter cavities.
Thanks, Martin!
"A. Thermal bridging can be reduced, but it cannot be eliminated. There are lots of alternative approaches, and they are explained in my article. For example, you can install a continuous layer of rigid foam on the exterior side of the roof sheathing, or you can install framing members at 90 degrees to the rafters, on the interior side of the rafters, to deepen the rafter cavities."
So, if I understand correctly, I could screw (?) 2x3s perpendicular to the bottom of the rafters, sort of like strapping, and fill those cavities with roxul, for example?
Which would be the better approach? Continuous polyiso or the 90 degree framing members?
I'll go digging through the site articles, too. It's frustrating sometimes because as common as our type of house is around here, there is precious little info on how to approach a renovation to meet code, etc etc. This site is the only one where I come even close to getting any help, so thank you again!
Kerstin,
Q. "Which would be the better approach? Continuous polyiso or the 90 degree framing members?"
A. Either way would work. Neither approach is "better." Your method of insulation depends on who is doing the work, the preferences of the workers who are doing the installation, your philosophical opinions on rigid foam, and the availability of different materials in your area.
Hi Martin.
With very recent studies showing that poly perform worse and worse as the temperature drops below 50F, it appears XPS should be the go to foam board in zone 5 and above - yes? I understand the global warming implications of the gas in XPS, but is there a choice when R value is the priority?
Eli
Eli,
Q. "It appears XPS should be the go-to foam board in zone 5 and above - yes?"
A. No. Green builders avoid the use of XPS because XPS is manufactured with a blowing agent that has a high global warming potential. Instead of XPS, choose either polyisocyanurate or EPS. For more information, see "Choosing Rigid Foam."
Q. "Is there a choice when R-value is the priority?"
A. Sure there is a choice. The choice is between EPS and polyiso. As with any R-value calculation, you simply need to choose rigid foam that is thick enough to meet your R-value target. In most cases, you can assume R-4 per inch for EPS, and either R-4.5 or R-5 per inch for the cold-weather performance of polyiso.
Eli,
Don't let the stated R value of XPS fool you. XPS has its own issues. Its R Value degrades within a couple years to R 4ish.
Graphite EPS (Neopar) has a true, stable R Value of 5. Type II EPS is around R 4.2 but it increases to around R 5 when you need it most.
The US version of Extruded Polysterene should be banned at once as it's environmental impact is staggeringly high. One 4x8x2" sheet of XPS probably carries the same embodied energy of 100,000 pounds of cellulose. (I completely made that up but you get the idea)
Thanks guys - I was forgetting about EPS. Not interested in Polyiso due to the poor performance in frigid temperatures.
Hi, I'm planning on building my first home (I'm not a builder, I'm a customer) and I would like to know what would be the most cost conscious way of building an airtight home? My home will be in zone 2 and because of my tight budget I plan on doing some of the building/labor myself with my dad (who grew up building houses). I've been looking at using a zip system and rockwool combination (from what I understand this approach would be cheaper than spray form insulation since we would be able to save money by installing both Zip and Rockwool ourselves), and am unsure of going with vented and unvented. I believe unvented would be better because I can seal from the outside with zip system (also because the attic will contain the air handler and ducts), but I read I'd need exterior ridgid insulation so would Zip R6 be sufficient? Underneath I'd have Rockwool in the rafter bays. Thank you for your help and sharing your knowledge! I've been able to learn alot from yall! -Roel
Roel,
Q. "I believe [an] unvented [roof assembly] would be better because I can seal from the outside with Zip System (also because the attic will contain the air handler and ducts), but I read I'd need exterior rigid insulation so would Zip R6 be sufficient?"
A. With this approach, R-6 exterior insulation would be sufficient in Climate Zones 1 through 3. But if you live anywhere colder than Zone 3, you would need more rigid foam. All of this is explained in the following article: "Combining Exterior Rigid Foam With Fluffy Insulation."
Hi, We greatly appreciate the information that you are providing on this site. We live in zone 4c marine on the coast of Oregon. We are owner/building a new house with a shed roof with a slightly more than 2:12 pitch. We are planning on asphalt shingles. On such a low slope roof it is our understanding that we will need to add ice & water shield underlayment to the entire roof surface under the shingles.
We are using 2x12 rafters which serve as the ceiling below. After reading this blog it seems like a good option would be to use a non-vented roof style using closed cell foam spray insulation under the sheeting between the rafters to achieve my required 38 r value in this mild, but wet climate.
Our question is: Will covering the entire roof with ice & water shield conflict with the spray foam non-ventilated rafter bays since the sheeting will be essentially sandwiched between 2 non-permeable materials? Thanks (Greg & Joannie Miller)
Joannie,
Q. "Will covering the entire roof with Ice & Water shield conflict with the spray foam non-ventilated rafter bays since the sheeting will be essentially sandwiched between 2 non-permeable materials?"
A. Here is a link to an article that answers your question: "Sandwiching Roof Sheathing Between Two Impermeable Layers."
Hello Martin,
I appreciate all of the knowledge I have gained from you.
We are in Central Texas. I see the above sheathing ventilation for metal roofs picking up here, and installation techniques vary greatly.
Enter my current project. I am doing a cathedral that is ventilated above the roof deck; the choices are limited due to the historical nature, roof profile etc.
We are planning for R38 mineral wool in 2x10 24”OC rafters, 5/8” cdx deck with permeable underlayment (SlopeshieldPlus), 1x4 diagonal and spaced battens, continuous coravent/fascia vents to the vented ridge, air barrier (Tyvek or Drywall) on the interior under the rafters and with tongue and groove interior. Slopes are 7/12 with small shed roofs at 3/12; easy gable roof, mostly.
If I cannot get the Slopeshield or other for dry in, I may go with asphalt felt underlayment; however the "advice" on that with the venting/battens is conflicting.
What are your thoughts on this plan?
Thanks, Earl
Earl,
You should really choose a vapor-permeable roofing underlayment. Number 15 asphalt felt is somewhat vapor permeable, especially when damp, but not as vapor-permeable as some of the synthetic underlayments that are marketed as high-perm underlayments.
If you can't find SlopeShield, consider one of the other available vapor-permeable products:
Permafelt from Perma R Products P
Deck-Armor from GAF Materials
Delta-Maxx Titan from Cosella-Dörken
Delta-Foxx from Cosella-Dörken
Vent S from Cosella-Dörken
RoofAquaGuard BREA from Nemco Industries
Great, thank you!
As far as the 1x4 diagonal battens for the vented air space goes... are there any references for the performance of that system compared to the larger airspace like 2"? I know you are an advocate of the larger airspace. There are a lot of roofs going up that are spaced with 1x4. Just curious about the return vs. cost if the airspace is this small.
Earl,
In central Texas, your winters are mild -- so you have fewer reasons to worry about condensation, moisture accumulation, or frost on the underside of your sheathing than homeowners in Minnesota or Maine. I think you'll be fine.
Makes sense, thank you!
I am on a ridiculously small budget to even consider foam panels to the exterior of a new roof. But that is what I want! And I came across a resource of paper-back 4" poly iso (damaged) for $16 per panel. That's just 50 cents per square foot and getting darn close to price of fiberglass batt. But I am concerned about paper being food for mold. How hard is it to tear the paper off? Does the poly iso have to have a face or was it just something they need during the manufacturing process?
Mary Ann,
All polyiso insulation has some type of facing. Many kinds of construction products include paper, so I wouldn't worry. Kraft facing is a type of paper. Asphalt felt is a type of paper. Cellulose insulation is a type of paper. Paper is your friend, not your enemy. Just make sure you follow the requirements to keep everything dry. For more information, see "How to Install Rigid Foam On Top of Roof Sheathing."
This is a great article but I am unfortunately still confused and I am hoping someone can answer a question about if I need an interior vapor barrier with my particular roof assembly before installing a shiplap wood ceiling?
I'm in climate Zone 6 and this is a new shop building that is fully complete and signed off on by the building inspector except for the final inspection when I complete the interior work that I'm doing myself. I suspect because this is a shop and not a home, the inspector didn't go over everything as thoroughly as he might have otherwise.
The building does have a cathedral ceiling and the roof assembly currently from inside out is:
2x12 rafters with R38 fiberglass (no vent space) - > 5/8" plywood -> 2" R-10 rigid insulation -> 5/8" plywood -> 1x3 furring strips run vertically creating a ventilation channel -> ANOTHER later of 5/8" plywood as a substrate for a metal roof -> Ice and Water (full roof) -> Screw down metal roof.
There are continuous soffit and ridge vents that align with the furring strips in the vent zone. As I understand it, this IS a vented roof, it is just vented to the outside above the roof deck rather than below but it seems like I may not have enough rigid insulation on top of the roof deck to keep that inner most layer of plywood from getting some condensation. I've installed the R38 fiberglass bats but they currently just being held in place by those thin metal rods and there is no ceiling installed yet so I do still have full access from below.
My plan was to install a ship lap wood ceiling so I didn't have to handle large sheets of drywall overhead and there are rafter ties every 4' (doubled-up) 1/3 of the way up the roof which would make hanging large sheets a nightmare.
My question is, based on this assembly, do I need a vapor barrier at the ceiling or does this roof assembly need to breath to the inside? If so, can I go with 6 mil plastic if I figure out out a way to install it so it isn't punctured by my finish nailer installing the shiplap? Sealing around the rafter ties will be a challenge regardless of the method used if this roof assembly does need to be air tight. Thanks for reading if you made it this far :)
Brandon,
Q. "As I understand it, this IS a vented roof."
A. No. It is an unvented roof, since there is no vent channel between the fluffy insulation and the lowest level of roof sheathing. The vent channel above the rigid insulation may reduce the chance of ice dams, but that vent channel doesn't make your roof assembly vented.
Q. "It seems like I may not have enough rigid insulation on top of the roof deck to keep that inner most layer of plywood from getting some condensation."
A. That's right. In Climate Zone 6, with your type of roof assembly (an assembly that combines fluffy insulation on the interior side of the lowest level of roof sheathing with rigid foam on the exterior side of the lowest level of roof sheathing), at least 51% of the total R-value of the roof assembly must come from the rigid foam layer. (For more information on this issue, see "Combining Exterior Rigid Foam With Fluffy Insulation.") In your case, the rigid foam provides only 21% of the total R-value of the roof assembly. So you screwed up.
You'll need to either (a) add more rigid foam on the exterior, or (b) decrease the thickness of the fluffy insulation.
Q. "Do I need a vapor barrier at the ceiling or does this roof assembly need to breath to the inside?"
A. You don't need an interior vapor barrier, but you definitely need an interior air barrier -- preferably, a layer of taped gypsum drywall on the interior side of the fluffy insulation. After the drywall is installed and taped, you can add a layer of boards on the interior side of the drywall if you prefer the look of boards.
Thanks for the reply Marin and I appreciate you taking the time to answer these questions. The roof is finished and the contractor is no longer on the job so I'm stuck with what is built from the deck up so adding more rigid up there is not really an option at this point. If I'm going to rip the roof off, I might as well wait until there is a failure. Total insulation below R49 isn't really a viable option either so I'm trying to sort out the best path forward with what I have and I'm open to suggestions.
Would adding ventilation baffles below the deck help? I could pad out the bottom of the rafters to get back the 12" of space I need for the fiberglass bats. We're in a very rural area so I don't really know if there are options for spraying closed cell foam or anything but if that is the only option at this point, I could look into it. I already have the R38 batts but I could always add them to the attic of our house if I need to go another way so they wouldn't be wasted if that is the only option.
Is there anything specific about drywall or would 1/2" plywood or OSB work as long as I taped the joints with zip or tyvek tape or something similar? At least that would accept fasteners for for the ship lap if we decide to go that way. Thanks again. and although I wished I would have found this before the building was built, I'm glad that at least the ceiling isn't closed up already so I do still have some options.
Thanks for the reply Martin and I appreciate you taking the time to answer these questions. The roof is finished and the contractor is no longer on the job so I'm stuck with what is built from the deck up so adding more rigid up there is not really an option at this point. If I'm going to rip the roof off, I might as well wait until there is a failure. Total insulation below R49 isn't really a viable option either so I'm trying to sort out the best path forward with what I have and I'm open to suggestions.
Would adding ventilation baffles below the deck help? I could pad out the bottom of the rafters to get back the 12" of space I need for the fiberglass bats. We're in a very rural area so I don't really know if there are options for spraying closed cell foam or anything but if that is the only option at this point, I could look into it. I already have the R38 batts but I could always add them to the attic of our house if I need to go another way so they wouldn't be wasted if that is the only option.
Is there anything specific about drywall or would 1/2" plywood or OSB work as long as I taped the joints with zip or tyvek tape or something similar? At least that would accept fasteners for for the ship lap if we decide to go that way. Thanks again. and although I wished I would have found this before the building was built, I'm glad that at least the ceiling isn't closed up already so I do still have some options.
Brandon,
Q. "Would adding ventilation baffles below the deck help?"
A. Yes, as long as the ventilation channel was connected to soffit vents at the bottom and a ridge vent at the top. That would turn your unvented roof assembly into a vented roof assembly. You would lose the insulating value of the rigid foam, unfortunately, but that approach would work.
Q. "I don't really know if there are options for spraying closed cell foam or anything but if that is the only option at this point, I could look into it."
A. That would work. If you are aiming for a total assembly R-value of R-49, you would need to install R-15 of closed-cell spray foam (about 2 .5 inches) on the underside of your roof sheathing, followed by no more than R-24 of fluffy insulation on the interior side of the cured spray foam.
Q. "Is there anything specific about drywall or would 1/2" plywood or OSB work as long as I taped the joints with zip or tyvek tape or something similar?"
A. Plywood or OSB would work. It's also possible to use one of the vapor-permeable European air barrier membranes, as long as you are very conscientious about sealing the seams with a high-quality tape. (I wouldn't use polyethylene, because you want the assembly to be able to dry to the interior, and because polyethylene is somewhat fragile.)
Thanks again. I think the easiest/cheapest option at this point is to try and locate an insulation contractor to spray closed cell foam. Tying into the vents seems difficult to impossible as that would require cutting or drilling through 2 layers of 5/8” plywood and 2” of rigid insulation. Now that I understand this is an unvented roof and not some weird hybrid, these articles make a lot more sense.
“[Deleted]”
An update: After calling around all morning, I was able to locate a very reputable spray foam contractor (referred by several other contractors As best spray outfit around) that will service my area and quoted me $1 per sq ft per inch for closed cell and suggested I go ahead and do a full 3 inches based on my assembly and fill in the rest with batts. Sounds reasonable so that’s the way we are going to proceed. I sincerely appreciate the advise I received here and feel like it probably saved my roof from a premature failure.
Last question if I may? Since we will now have a proper unvented roof that dries to the interior, how important is that taped drywall as an air barrier now that I’ll have an air impermeable layer of foam below the deck? Is it safe to install the shiplap directly to the underside of the rafters in this scenario given I’ll have approximately R30 of CC & rigid before I get to the paper-faced fuzzy stuff?
Brandon,
With all that spray foam, I agree that you'll be safe without an interior air barrier. However, check with your local code inspector to make sure that your shiplap boards qualify as a thermal barrier (to limit the chance that the flammable spray foam catches fire). Half-inch drywall is a thermal barrier, but it's up to your code official to determine whether your shiplap boards will work.
“[Deleted]”
I am planning an unvented, asphalt shingle roof/cathedral ceiling, using 2x12' rafters with 4" closed cell spray foam + R-19 Batts. We are then planning on installing BORAL Nickel Gap Siding directly to the underside of the rafters. Any issues with this assembly? Also, is there a GBA Drawing in the Library for this ....or something similar? I could not find one.
Jonathan,
You are describing the flash-and-batt approach. For more information on this method of insulation, see "Flash-and-Batt Insulation."
Four inches of closed-cell spray foam -- the thickness you plan to use -- will work for Climate Zone 6 (or anywhere warmer), but you will need thicker spray foam if you are located in Zone 7 or 8.
A drawing of this method (see image below) can be found in my Fine Homebuilding article, "Insulating a Cathedral Ceiling."
If you nail siding directly to the underside of the rafters, your assembly will lack an interior air barrier. (The siding leaks air like a sieve.) While it is true that the spray foam layer is an excellent air barrier, there is always a chance that defects in the spray foam job might allow a few air leakage paths, and you may live to regret the lack of an interior air barrier.
Thanks for the REPLY Martin. So would a simple 6mil plastic sheet stapled to the underside of the rafters before installing the lap siding be sufficient as an air barrier? Or would you recommend 1/2" drywall taped be the better way to go? 6mil plastic would certainly be less expensive but I would worry about getting it installed successfully with just staples....perhaps cap nails would be better?...but will they cause me headaches when I install the siding on top of them? Some other inexpensive air barrier besides drywall? Is the paper facing of the fiberglass insulation not sufficient?
Jonathan,
It's a judgment call. I think taped drywall is best -- polyethylene is flimsy, easily damaged during installation, and is more likely to leak through fastener holes. Some people will think that these details are overkill -- but I hear a lot of complaints about failing cathedral ceilings, and you might as well do it right the first time.
Martin:
I recently bought a home near Sacramento, CA. A portion of the home has cathedral ceilings with a vented, shed style roof assembly. Built in 1978, I assume they stuffed the rafter bays with fiberglass batts. The roof was recently replaced and the interior ceilings are likely pine T&G that’s been painted. This area of the home is always cold. What are my options for addressing insulation and air sealing from inside the envelope?
Best,
Eric
Eric,
Q. "What are my options for addressing insulation and air sealing from inside the envelope?"
A. Step one: Assess the current situation to determine whether the rafter bays have any insulation. Perhaps you can drill an inspection hole in an inconspicuous part of the ceiling, or perhaps you can carefully remove one ceiling board.
If there is no insulation, you'll probably have to remove the existing ceiling for full access to the rafter bays. Once you do that, you can proceed with a variety of options, as described in my article, depending on whether you want a vented assembly or an unvented assembly.
If you choose a vented assembly with fiberglass batts, you'll definitely need an interior air barrier -- something like taped drywall. If you want to look at a tongue-and-groove board ceiling instead of drywall, you can install the boards on the interior side of the taped drywall.
Hi Martin,
Thanks for the great article and discussions! I am new to construction and have learned quite a lot. We are in Boston area and are adding a family room and master suite with cathedral ceilings, though the bathroom and walk-in closet will have an attic where HVAC is installed.. Ceilings (including ceiling above the attic) will be insulated with R-49 faced fiberglass and will be vented. Attic floor is not insulated. Cathedral ceiling part will be sheetrock, no sheetrock on the ceiling above the attic. How to make sure there's no leakage between the cathedral ceiling and the attic area? Anything else we should look out? I appreciate your help!
Best regards,
Wei
Wei,
If you are installing faced fiberglass batts between the rafters, and there will be "no Sheetrock on the ceiling above the attic," what will you install for your air barrier on the underside of the fiberglass batts? Drywall is a good air barrier, so I advise you to install drywall under all of the fiberglass batts.
Q. "How to make sure there's no leakage between the cathedral ceiling and the attic area?"
A. Use blower-door-directed air sealing. (Blower door testing is mandatory for new construction in most states.) For more information on this method, see "Blower-Door-Directed Air Sealing."
Hi Martin,
Thanks for your helpful reply. I did ask my contractor about install drywall under all fiberglass batts, but he said that since the attic and walk-in closet ceiling will be air tight and batts have paper vapor retarder, there's no need to install drywall under those fiberglass batts. But I thought a drywall would perform better though it might not be easy to install. And thanks for suggesting blower door testing!
Hello Martin,
Thanks for a great article! I wanted to clarify one thing with you - currently working on a 2:12 pitch shed roof. The plan is a to cover the whole deck with ice and water shield, then install 8-9" of polyiso rigid insulation (R49), then furring strips for vent channels and metal roofing on top. On the interior I have 2x8 exposed joists for the cathedral ceiling with no insulation between them. T&G pine for the ceiling. The question is, should I be installing an air barrier like SIGA Majrex 200 below the joists/above T&G? Also would recessed led lights be ok in this assembly, since the sheathing is fully insulated above and is drying to the inside? Thank you for any suggestions on this matter!
Hamerton,
Your description is a bit confusing. If your joists are exposed below a T&G ceiling, how could you install either a membrane or pot lights?
Hamerton,
In your case, the air barrier is your Ice & Water Shield, and all of your insulation is on the exterior side of this air barrier. Everything on the interior side of the Ice & Water Shield is inside your home's thermal envelope, so no further air barriers like Siga Majrex are needed below the Ice & Water Shield. Recessed can lights are OK, because they don't penetrate your air barrier or your insulation layer.
Hi Martin, thank you for a quick reply. Sorry about the confusing description, but I think you nailed it with your reply. That's exactly what I was wondering about. Thanks for your help!
Hamerton,
If the T&G ceiling is below the rafters you might consider reducing the amount of exterior foam and adding some batt insulation to the bays. This will make the roof a lot easier and cheaper to build.
An example can be found in Assembly #3 of this article: https://www.greenbuildingadvisor.com/article/five-cathedral-ceilings-that-work
So how do you install lighting in the ceiling of an unvented low slope roof?
M. Hunt,
Q. "How do you install lighting in the ceiling of an unvented low slope roof?"
A. There are lots of answers to this question.
First of all, not every ceiling needs lighting fixtures. Consider cove lighting installed high on the wall, wall sconces, and floor lamps before concluding that you need ceiling-mounted fixtures.
Second, if you absolutely must have ceiling fixtures, consider installing track lighting, surface-mounted ceiling fixtures, pancake LED fixtures, or pendant fixtures installed in shallow electrical boxes. Don't install recessed can fixtures.
Third, make sure that your shallow electrical boxes are airtight. Either purchase airtight electrical boxes, or do a perfect job of air sealing with caulk. Remember, it's a code violation to fill an electrical box with canned spray foam.
More information here: "Martin’s 10 Rules of Lighting."
https://www.greenbuildingadvisor.com/article/martins-10-rules-of-lighting
Makes sense. If you go with an unvented roof with closed cell spray foam on the underside of the roof sheathing, does the issue of air leakiness around lighting fixtures in the ceiling still matter?
M. Hunt,
No, air leaks wouldn't be an issue in that case -- but displacing useful insulation thickness with deep electrical boxes would be an issue.
I am posting because I didn't see a comment with my particular configuration. I am starting a project in Zone 6 (Vermont) to insulate the second story above my garage that would entail a vented cathedral ceiling with a 12/12 pitch, totally uniform roof (no dormers etc) and gable vents. I am not planning to remove/redo the roof as a part of this project (so adding exterior foam is out of the question), and as the rafters are 2x10, getting anywhere near R49 will be tricky. Therefore I plan to use 2" of rigid foam on the interior to introduce a thermal break as well as increase the R value above the R30-35 I will get from filling the cavities with room for venting. Ideally I am minimizing the loss of interior space after the 2" of foam, and also ideally would not do drywall.
I have been shying away from spray foam due to cost, and because I believe I would need to wait until warmer weather. But I still need to do a big picture cost comparison to understand if my assumptions around cost are correct.
After re-reading this article and many others on GBA (including "Walls with Interior Rigid Foam", "Site built ventilation baffles for roofs", "Do I need a vapor retarder), I think I've finally landed on an insulation approach. However, I still have some uncertainty related to whether the interior rigid foam should be vapor closed or vapor open. I have determined that a high density foil faced EPS (Like SilveRboard 35 from AMVIC, SB35) is likely the best choice because it retains a better R value than polyiso in cold temperatures, the density brings the R value to 5 per inch, and the foil facing adds R value with an air gap, and that the foil facing allows me to leave it exposed to the interior without a thermal barrier (I need to confirm that one). That product also comes in a perforated version (SB35XS) that bumps the vapor perms from 0.08 to 3.79. I realize this is still a Class III vapor retarder, but (I think) permeable enough to allow for some drying.
After much reading on GBA my vapor management understanding is:
- Air sealing is of the utmost importance
- Vapor barriers likely aren't necessary except in zones 7+ or due to code
- Don't sandwich your assembly in vapor closed materials
- Plan for the assembly to dry to the exterior, interior, or both. Exterior is most common with a vented cathedral ceiling in zone 6, as I understand it.
Therefore my proposed assembly is:
- 1" air via venting channel
- 1" perforated, dense, foil faced EPS (SB35XS, R5), taped/calked/air sealed
- 7.25" Mineral wool (Rockwool Comfortbatt, R30)
- 2" perforated, dense, foil faced EPS (SB35XS, R10), taped/calked/air sealed
This would likely later be finished later onwith:
- 1 x 3 furring strips
- Tongue and groove pine
- slim pancake LED lights
This would result in two air barriers (and the mineral wool being airtight) as well as vapor open to both sides to dry in either direction. My goal is that the taped/sealed interior EPS can eliminate the need for a drywall layer. The combination of mineral wool and a DIY EPS vent baffle added an extra R5 over R30C fiberglass batts which are typically an inch thicker than the mineral wool.
My questions, for any that have an opinion/perspective:
1) Should I chose a vapor closed EPS for the interior foam layer? This would mimic what I generally have seen in vented, insulated cathedral ceiling assemblies with interior foam, including many of the Detail pages on this site.
2) Is there any advantage to fully vapor open design?
3) I can also see the advantage to an additional smart retarder layer between the rafters and the EPS as an additional air barrier in case the EPS sealing isn't perfect. This still might make sense to me when using perforated silverboard because as I understand it, the smart barrier in a high humidity environment will actually outpace the perforated silverboard in total perms.
4) Any other reactions to my proposed project, and assembly?
Many thanks,
Sean
Hi, I have a very similar situation to Sean's, as he described above, and I have the same question about the need for a vapor barrier/retarder in a vented, insulated cathedral ceiling scenario.
I'm also looking at an over-the-garage attic conversion, 12-12 pitch roof, straight rafter bays. I'm in Zone 4A.
I was thinking:
-1.5" ventilation channel
-.25" fiberboard baffle (caulked and taped)
-9.5" fiberglass insulation (probably a 10" R-30 batt squished down a little)
-2" EPS (taped)
-1x3 furring strips
-T&G pine
Should there be a vapor barrier/retarder in that assembly?
Thanks,
Nate
Nate,
You already have one. The 2" of EPS is between 1 and 3 perms.
Hi Martin & Community! I am not a builder and this is my first post, I hope my terminology is correct! I have read your materials extensively on this topic and would like to ask your advice on the “cut & cobble” technique for our cathedral ceiling since my Wife was severely ill for many years (thank goodness better now), but I am concerned about the potential of off-gassing with spray foam which might tax her immune system.
To set the stage, we recently bought a great home in Nevada City CA (95959) that we knew had mold issues from a water intrusion/failed wall. During remediation, we also learned that there was mold in the cathedral ceiling from condensation. The cathedral ceiling is complicated by the fact that it has vertical rafters on one side and horizontal purlins on the others. Both rafters and purlins are 2x12’s. See pics. Before the remediation there was only fiberglass batts between the roof sheathing and the drywall. There were no baffles for air flow. On both sides (rafters and purlins) there are soffit vents at the bottom and a ridge vent at the top. Based on all your materials it sounds like for the rafter side we could put baffles against the sheathing to allow airflow above the rigid foam, but on the Purlin side we need some help on the best way to allow airflow without damaging the structural integrity of the roof/purlins. I welcome your general advice as well as I am hoping you can answer my specific questions below. Please feel free to ask me any questions for clarification (Yes, we are removing the can lights), thanks so much in advance!
1.) You cannot tell from the pics, but there are very small triangles cut out of the edge of the purlins where they meet the glulams. I assume this was for airflow, but they are tiny and only at the edges and I doubt they suffice. Our insulation contractor has recommended cutting triangular or trapezoidal holes in the tops of the purlins where they touch the roof sheathing. See other pics for the cuts he is referencing. First question is if you think this will provide enough ventilation to solve the problem, and 2nd question is if you think this will meaningfully weaken the structural integrity of the roof. Lastly on this, do you have any other alternate suggestions on how to make this work?
2.) Can you please recommend (with a link to buy if possible) which pre made baffles you recommend installing in our situation?
3.) It appears you recommend EPS board in our situation. If there is a max 1.5 inch baffle, that leaves I believe 9.75 inches for insulation. Can you please recommend (with a link to buy if possible) which foam board you recommend buying? Also, the insulation contractor recommended doing some rigid board and filling the rest with fiberglass. Do you agree with this? If we went with more foam, would they simply layer the board on top of each other? I assume (but hope I am wrong) that there is not like a very thick (6”+) eps foam board, is there? If the difference in price of more foam board and less fiberglass did not matter to me, what ratio would you suggest?
4.) I have seen you talk about canned spray foam to seal the board, as well as European tape. What do you specifically recommend? Any links to buy would be great. Also, is it dumb for me to think we should tape it and then put a layer of canned foam over the tape?
5.) I have seen you reference moisture retarders and moisture barriers. If we do have drywall on the ceiling, would we need any other layers? Meaning the layer touching the roof sheathing would be the baffle, then rigid foam, then fiberglass, then the drywall. Anything else that should be sandwiched in there, and if so where? I have also seen you talk about certain paints that retard moisture and others that don’t. should this be factored in, and if so how?
6.) I have also seen you talk about adding a layer of continuous rigid foam underneath the rafters/purlins. I am not opposed to ALSO doing this if you think it would be helpful, in addition to the rigid foam between rafters/purlins. If so, how would the foam be attached so as not to have nail penetrations in the foam which I assume would allow air to get in? Also, how would you then attach drywall underneath it so that it could be affixed while also not creating air punctures due to nails etc.?
7.) You also have talked about an air barrier under the insulation. Does drywall suffice or do you recommend something else? This I suppose is a similar question as number 5 above in regards to what the layering should be.
8.) Can you give any other feedback on how to make sure the contractor creates as you described “make sure the roof assembly is as close to airtight as you can make it”
9.) Any last additional thoughts on how we can really do this “right” considering I don’t want to use spray foam, and ripping off the entire roof to do rigid foam on the outside seems like a nightmare?
Ok, thank you SO much for your feedback, I have rally enjoyed getting to know your website and you work!
David,
Without a pathway for airflow from the soffit to the ridge, there is no possibility of having a vented assembly. Your roof is not suitable for the vented approach, because the purlins block airflow.
You have only two choices: either closed-cell spray foam installed on the interior side of the roof sheathing, or a thick layer of rigid foam installed on the exterior side of the roof sheathing. The latter choice will require new roofing.
Hi Martin! Thanks for your quick response. What do you think about cutting the triangular or trapezoidal holes in the purlins to allow airflow? Please see the pics 3 and 4 as examples.
Hi there,
I hope this isn't a silly question, but I have been searching and searching for that answer. In this article, is says, "Yes, of course [you should have an air barrier on the underside of your insulation] — especially if you are using fluffy insulation like fiberglass batts, blown-in fiberglass, or dense-packed cellulose. (If you insulate your ceiling with spray foam, the spray foam should create an air barrier, as long as the installer does a good job.)"
I have an unvented insulated cathedral ceiling attic with HVAC equipment up there. I have 5 inches of closed-cell spray foam applied directly under the sheathing and then blown fiberglass insulation installed right under that (held up by fabric/netting). I live in climate zone 5 if that matters.
My contactor did not install anything under the insulation, and I live in a place where code is not enforced (which I did not know when starting the project). Recently, I suspected this was wrong/not safe (I moved in 2 months ago). I want to ask the contractor to come back to install drywall under the blown insulation, and I want to be able to explain my reasoning.
I can't find anything in our residential code that addresses this directly (may have missed it). Can you please explain the following?
1. Do I need drywall (air barrier) because there is fluffy insulation and it can get into the air? (I am afraid the dust from it has already gotten into the HVAC system up there.) Or is it for some other reason? Or do I need drywall because I need a thermal barrier (and the spray foam technically isn't covered, even though it's hidden by the blown insulation)? Or both?
2. Is there anything wrong with having the spray foam installed as an air barrier, having a layer of blown fiberglass, and having another air barrier in the dry wall?
Thank you so much in advance. As a homeowner, I was not anticipating having problems like these and it's really hard for me to find trustworthy answers.
Hello everyone,
Sorry in advance for the long winded post but if anyone has the time for input, I would greatly appreciate. I have tried to do as much due diligence and read as many of (mostly) Martin's posts on the subject as possible.
Here it is:
• Climate zone 5B, ¾ Detached, unfinished, single car garage that measures approx. 10ft by 20ft.
• Gable/shed style roof, which originally had an unvented ceiling with 2x6 rafters and a couple 2x6 joists with electrical/lighting/garage door attachments.
• I had a square top roof vent installed when the shingles were replaced 2 years ago, so there is approximately 1 sq.ft of roof ventilation for the ~200 Sq.Ft. of ceiling space, in addition to soffit venting all around.
• The goal is to create a 4 season workshop space that can be heated with something like a 5000W 240V ceiling mounted heater.
• Walls are 2x4 16" OC, which I am intending to insulate with R-14 fibreglass batts, vapor barrier etc.
The walls are the easy part, which brings me to the ceiling. I've gone full circle, so I am hoping to get some more experienced input.
I was originally hoping to install 2x6 joists and hang an attic ceiling with unconditioned space above. Installing and hanging the ~10' joists felt like I was making this a bigger project than it needed to be given the goal.
There is no ridge vent, so I don't believe a full on cathedral ceiling is possible/practical unless I hire a spray foam contractor. I was recently quoted $1500-1700 CAD + tax for 3in R18 foam. It's tempting as the easy fix..but, pricey.
The alternative plan is to air seal (with tack tape) the proVent 14"x48" baffles with tucktape, to create an air tight vent from the side soffits, 4ft up the roof sheathing.
The square top roof vent I had installed, is 2" higher than the end of the baffles.
So the current thought is to install the air tight baffles, install fibreglass batts between the rafters for the length of the baffles (minus an inch or two), and vapor barrier it air tight. This would create a ~4' long cathedral ceiling with an open air vent into the upper portion of the attic.
From where the insulation ends, install 'joists' spanning 3 ft between the rafters on both sides of the roof, to create a flat ceiling with unconditioned attic space above it. The new 3' joists would be insulated with the same R-14 batts (possibly double stacked), air sealed with vapor barrier, and dry walled over.
The space above this new ceiling is between 1-2', and the attic ventilation would be the square vent I had previously mentioned.
Before getting into the corner venting details/issues, is this plan asking for trouble?
The final alternative plan is the "flash and batt" method, 1" of spray foam against the sheathing to serve as an air sealer, and install batts over the 1"spray foam.
Open to any other suggestions!
Thanks,
Kyle
Kyle,
The posts in this area disappear quickly. For a better response I would re-post this in the Q&A section.
Thanks Malcom, I just posted over in the Q&A.
Kyle,
Your plan will work, although you should remember that you may not get code-minimum levels of insulation unless your fiberglass batts are thick enough.
One other point: You seem to have a mistaken impression about the need for a vapor barrier. In this situation, an air barrier is far more important than a vapor barrier. For more information, see "Do I Need a Vapor Retarder?"
hello everyone, Can you please point me in the right direction so I can learn more about the skylight installation in the cathedral ceiling? Would it even be a good idea to install a skylight if I use exterior insulation (4'' EPS/XPS in zone 5). I would appreciate any feedback.
Or am I better off having no exterior insulation if I plan to install skylights?
SSHabel,
Skylights are a lot easier to install, air-seal and insulate on a cathedral ceiling than on a trussed roof. Having exterior insulation makes no difference as long as you are planning a layer of sheathing above the exterior foam.
Thanks for your response, Malcolm. Yes, that seems to be the caveat; I assumed only 2x4 over 3'' of foam boards and standing seam roof.
What happens IMHO is with a skylight I have not a continuous air barrier and need to sheet the sides of the opening. So it's basically 3'' plywood with a membrane on top of it connecting two layers of sheathing and creating a skylight opening?
SSHabal,
It's a bit dependent on what type of skylight you use. Some like Velux mount right to the roof deck, some are curb mounted. You don't necessarily need sheathing on top of the foam, but if you are using 2"x strapping you need to fill in the area around where the skylight will sit to provide a base for flashing.
You are right though - you need a continuous air barrier from the ceiling to the skylight. That can be plywood, poly, drywall, or a peel & stick membrane.
“[Deleted]”
Hi all,
I’m so thankful to the author of that article and to all you knowledgeable folks! My name is Peter and I live in Southern California within 5 miles of the coast (Climate Zone 3B).
My roof above an unvented cathedral ceiling is being replaced this week, and I would greatly appreciate any feedback you have on the proposed approach, below.
Background: The original roof is cedar shake, and the new roof will be asphalt shingles. The rafters are 2×6″ with 1/4″ skip sheathing spaced every 4″ from roof edge to ridge. The rafter bays are continuous with no blocking or penetrations from roof edge to ridge. I am mostly concerned with preventing moisture issues – the addition of insulation is mainly to prevent condensation.
Here is the proposed construction from interior to exterior:
1) drywall + plaster + drywall, about 1.5″ thick (existing)
2) Unfaced fiberglass insulation inside 2×6″ rafter cavity filled all the way from drywall to skip sheathing (new)
3) skip sheathing made of 1×4″ strips, spaced every 4″ (existing)
4) 1.5″ of EPS rigid foam sheets, R-6 (new)
5) 1/2″ OSB sheathing (new)
6) roofing paper
7) asphalt shingles
Some specific questions/concerns:
A) Do you see any potential issues with this roof construction above the unvented cathedral ceiling?
B) Does the 1.5″ of EPS foam need any special treatment? taping or caulking at the seams?
C) The skip sheathing creates many non-continuous, small air gaps between the fiberglass insulation and the EPS foam. Is this an issue?
D) If preventing moisture issues is my main concern, would I be better served by either 1) ventilating the ceiling with new soffit/ridge vents or 2) adding vapor diffusion ports?
Thank you so much for your help and wisdom in advance.
Be well,
Peter
Peter,
You raise a lot of questions -- more than can be easily answered here. I'll answer one of them.
Q. "The skip sheathing creates many non-continuous, small air gaps between the fiberglass insulation and the EPS foam. Is this an issue?"
A. Yes, especially if the gaps between the skip sheathing aren't air-sealed at the perimeter of the roof plane. You don't want any outside air flowing through these gaps. Your plan won't work well unless you come up with a method of preventing entry or exit of exterior air into these gaps. It's a big challenge.
I have cathedral ceilings with T&G interior fastened (I believe) directly to 2x12 rafters. A number of years ago we had a home energy audit and the tech show us the thermal pictures of our heat escaping through the slats. The tech suggested if we were to replace the roof, we could remove the roof sheathing and insulation batts and then spray some closed cell foam in from the top to air seal everything.
I'm at the point where we're going to be replacing the roof soon, and I trying to figure out if this is a good idea, and if so, do I insulate with just foam or go with a flash-and-batt approach. For the latter, all of the information I see assumes the foam is sprayed on the underside of the sheathing, and this article makes it clear that is required in an unvented space. But I'm guessing because the current space is vented, this could work? And what about the dew-point considerations? I'm in zone 6, which normally requires 50% of the insulation to come from the foam. Does that issue also go away in my inverted, vented scenario so that I could get by with less foam?
Thanks for any insights you can provide.
- David
David,
First of all, the suggested approach -- installing closed-cell spray foam on the exterior side of the tongue-and-groove ceiling from above -- is a good one. I have known this approach to work and be effective. In most cases, the easiest approach is to install as thick a layer of spray foam as you can afford (or as thick as the rafters allow).
If you decide to use a "reverse flash-and-batt" approach, you can. There is no technical reason why a reverse flash-and-batt installation would result in moisture problems.
The article details four ways to insulate an unvented assembly, but among those was not thick foamboard above the roof sheathing and nothing in the rafter bays. I know for practical purposes you’d normally want something in the rafter bays to help meet R-value, rather than needing even thicker insulation above the sheathing, but if you were willing to put 109% of the insulation above the sheathing, would it be acceptable?
michaelbluejay,
Here is a house which takes that approach to both walls and the roof:
https://architizer.com/projects/perfect-wall-house/
https://www.youtube.com/watch?v=hTwq-qUnr9I
Michael,
Here is an article that discusses the approach you suggest: "Getting Insulation Out of Your Walls and Ceilings."
Thank you. Okay, so all-insulation-above-the-sheathing isn't listed among the four methods in this article because in that approach it's actually vented?
Michael, I'd say that it wasn't included because it rarely makes practical sense. If you have framing cavities, it's usually cost-effective to insulate them. Adding insulation above the sheathing improves the performance. Foam insulation above the sheathing does not have to be vented; fibrous insulation installed above the sheathing does need to be vented.
...my cathedral ceiling was constructed long ago from 2x6 rafters. So, 5.5" of space to work with.
I used S 400 strip vents at the soffit, mesh ridge vent, planning to use a 1.5" vent full width between rafters leaving 4" for insulation. I plan to use closed cell for the full 4", then 1" high density XPS under the rafters, then 1/2" shiplap. Does this read as a good approach?
If my foam installer uses the higher density closed cell, which is reportedly R8/1" and I add 1" high density XPS under the rafters, the total R is in the 38 neighborhood. Currently the 1953 insulation has collapsed...so much better than what we have now.
Your approach would work, but if you're using spray foam insulation there is no need to vent the space. All closed-cell foam loses R-value over time and will eventually end up around R-5.6/in. Conventional XPS is one of the most climate-damaging materials used in construction. Newer, "low-GWP" XPS is better, but still has twice the impact of other common foams such as polyiso, EPS or GPS.
Hello Martin,
We've managed to begin our project...top floor, Cape...
We have decided to spray the entire 2x6 cavities - unvented from ridge vent down to the top plates so that the areas behind the knee walls will be "conditioned" spaces. All of the rafters will be encapsulated behind the knee walls and above the collar ties.
I plan to install 1" GPS rigid insulation the under the angled portions of the rafters, but not under the collar ties (which may be a problem?)...which will leave a void space that I can fill with fiberglass or rock wool. Then we will install 5/8" sheet rock. Does this feel like a decent way to prevent bridging? Obviously I must be very careful with joining and sealing the GPS.
Your thoughts?
Thank you!
Meboice,
Your plan should work. Good luck.
Thank you Michael,
I have a couple of questions based upon your reply...also, we live about 70 miles north of NYC, zone 5.
I am happy to spray closed cell up to the bottom of the roof deck...but, with no vent, will the shingles heat up beyond their design limit? I installed GAF Lifetime Architectural shingles about 10 years ago.
Polyiso...I've never used this material...it is foil faced? Which side does the foil face if I am fastening this to the bottom of the rafters to limit bridging?
Thank you again! Very helpful
Michael
The shingles will be slightly warmer than they would without a vent but Building Science Corp research has shown that it doesn't make enough difference to matter much--it might take a few years off the total life of the shingles at most.
Polyiso is usually foil-faced when used on residential projects, but it's also available with a glass fiber facing that is vapor-permeable. The foam is extruded between two facers so it always has something on both sides.
...this is a drawing that I prepared for the town.
I included 1" Polystyrene on the inside of the ceiling and knee walls...but wonder of mineral Wool or Rock Wool boards might be better...this material will not burn like the others if a fire should start for example...but it's not a vapor barrier...
...I changed the drawings to include 1" GPS under the rafters. Thank you for this suggestion Michael!
Looks good!
marine climate 4C--
existing condition by previous homeowners from in to out: drywall, 2x4 rafters furred down 1.5" with 4" polyiso flush with inside of rafters/furring so there is an airspace above the polyiso, original skip sheathing, 1/2" plywood
question 1: add ice & water shield above existing plywood, plus R10 eps, plus new plywood, roofing felt & comp shingles. Continue to vent original roof by leaving air holes at eaves and keeping a ridge vent--does it create a moisture problem?
question 2: seal up eave holes and no ridge venting, however leave original airspace, does it create a moisture problem?
question 3: which one would be preferred if removing the airspace is not possible?
Thanks
I am an architect and renovating a townhouse in Massachusetts (Zone 5). We want to insulate the cathedral ceiling. Built in the mid-70s, it has exposed 2x10 rafters with what is likely Tectum panels above. So, continuous open cell foam insulation (maybe 3" or 4" thick) that has an exposed finish to the interior, topped with a cellulose board (think Homasote). This summer the condo HOA re-roofed leaving the Tectum panels in place, then using ZIP boards with tape and no house wrap on top of the Tectum.
So, we have a water barrier (ZIP) which may have random nail holes that may or may not have been properly sealed. ZIP has a low perm rate so some drying to the exterior can happen on top of a permeable continuous insulation layer.
To meet R-49 I would like to add batt insulation in the cavity, then span the interior side of the rafters with continuous rigid insulation.
The questions are:
1. Should I make a vented or un-vented roof?
2. If I add ventilation, it has to be under the Tectum panels. Does it make sense to ventilate under insulation? Not that it has great R-value (maybe R-5). And is permeable.
3. If I do unvented, and I add continuous foil faced Polyiso boards under the rafters, creating a vapor barrier from the interior of the home, do I have a risk of having vapor penetration through the ZIP boards into the permeable Tectum and batt insulation below?
4. If I make the roof unvented, should I add polyiso under the Tectum first, fill the rest of the cavity with batt to meet my R-49? A modification of the flash-and-batt method.
5. Vented, or unvented, should I have a vapor barrier to the inside of the space, under the rafters, or should it all breathe because the ZIP boards are there.
My issue is dealing with rigid, permeable insulation BELOW the sheathing. And any ventilation would have to be BELOW the rigid insulation.
Thanks for any guidance. Chris
Log in or become a member to post a comment.
Sign up Log in